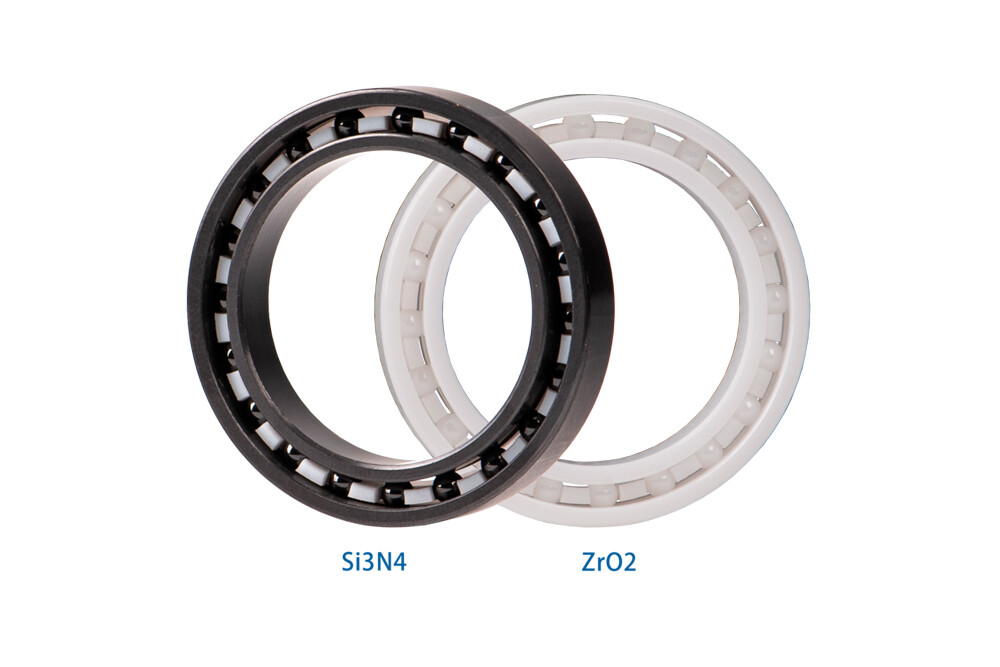
Bearing Manufacturer & Supplier
Specialize in ball bearings, roller bearings, thrust bearings, thin section bearings etc.
Zirconia Bearings vs Silicon Nitride Bearings, Which One?
With the continuous advancement and development of science and technology at this stage, many equipment such as high-speed machine tools and precision testing instruments have increasingly higher requirements for the working environment and work. People also require that these mechanical equipment must have various performances such as high speed, high precision and high reliability. In order to meet the development needs of many fields such as high-precision machinery, petrochemical industry, aerospace, military and national defense, mechanical parts must have good heat resistance, corrosion resistance, low magnetic properties, etc., and must also be able to withstand greater pressure. . As one of the key components, rolling bearings have higher performance requirements.
However, traditional metal bearings are no longer able to meet the current requirements for long-term stable operation under extremely harsh working conditions. Compared with traditional bearings, ceramic bearings have excellent comprehensive properties such as long service life, high overall precision and stiffness, high rotation speed, good thermal stability, insulation and non-magnetic properties. They are suitable for use in high temperatures, high speeds, high precision, strong corrosion and strong magnetic fields. It has very broad application prospects under working conditions such as and without lubrication. There are several commercially available ceramic bearing types, all of which offer many advantages over traditional bearing elements. Typical ceramics commonly used as bearing materials are silicon nitride (Si3N4) and zirconium oxide (ZrO2). This blog will explain in detail the advantages and disadvantages of silicon nitride (Si3N4) and zirconium oxide (ZrO2) ceramic bearings, and provide constructive suggestions for you to choose a suitable bearing.
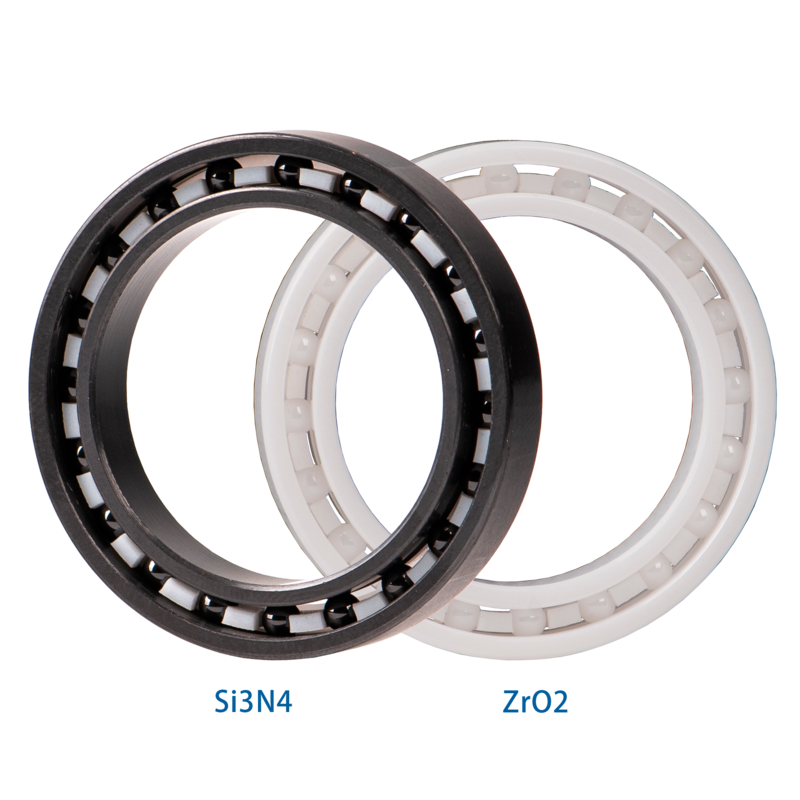
Table of Contents
ToggleWhat are silicon nitride bearings?
Silicon nitride is a very hard but also very light material. It has excellent resistance to water, salt water and a variety of acids and alkalis. It also has a very wide operating temperature range and is suitable for use in high vacuum applications. The extremely high hardness of silicon nitride bearings also means greater brittleness, so impact or impact loading should be minimized to avoid the risk of cracking. Silicon nitride ceramic bearings are black. Generally, the inner and outer rings and balls are made of silicon nitride, and the cage is made of PTFE or nylon. In this combination, the temperature resistance does not exceed 240 degrees (because PTFE itself is also a type of nylon, so the product If there is this material in it, the temperature resistance will not exceed 240 degrees.
Silicon nitride bearings have been used as the primary bearing type for a variety of aerospace applications. It’s worth noting that NASA’s space shuttles were originally built using steel bearings in the turbine pumps, which proved not to be the right thing when the space shuttles, and particularly its engines, experienced tremendous loads and temperatures. Because of these extreme loads, NASA engineers upgraded the bearings to silicon nitride bearings because of its superiority in vacuum environments. Impressively, according to NASA analysis, Si3N4 bearings offer a 40% improvement in operating time compared to steel bearings.
Advantages of silicon nitride bearings
Explore the benefits, applications, and key considerations for silicon nitride (Si3N4) ceramic bearings. Silicon nitride bearings are rapidly finding their way into various industries due to their unique combination of strength, lightweight properties and environmental resistance.
Lightweight characteristics: Si3N4 ceramic bearings are about 40% lighter than steel bearings. The significant reduction in weight means lower inertia and less energy required for mechanical acceleration and deceleration, increasing efficiency in high-speed applications.
Exceptional hardness and wear resistance: Silicon nitride is known for its extremely high hardness, exceeding that of most metals. This hardness helps improve wear resistance, thereby extending bearing life even under severe operating conditions.
Low coefficient of friction: The smooth surface finish of Si3N4 ceramic bearings combined with its material composition results in a very low coefficient of friction. This low friction minimizes heat generation and energy loss, thereby increasing the overall efficiency of the equipment.
High Temperature Capability: Si3N4 ceramic bearings maintain their mechanical properties at high temperatures where traditional materials may degrade. This makes them suitable for applications involving high operating temperatures, extending their usability in environments unsuitable for metallic bearings.
Corrosion and chemical resistance: Silicon nitride is inherently resistant to a wide range of corrosive substances, including water, salt water, and many acids and alkalis. This resistance ensures their reliability in corrosive environments such as chemical processing or marine applications.
Electrical insulation properties: Silicon nitride ceramic bearings are electrically insulating. This property is critical in electrical and electronic applications, as insulation is essential to prevent galvanic corrosion and related damage.
Compatibility with high vacuum environments: Silicon nitride bearings can operate effectively in high vacuum environments without the risk of outgassing, a common problem with certain materials under vacuum.
Reduced thermal expansion: Silicon nitride has a lower rate of thermal expansion, providing dimensional stability over a range of temperatures and reducing gaps that can affect accuracy.
Non-magnetic: The non-magnetic properties of silicon nitride make it suitable for applications where magnetic interference must be avoided, such as certain medical or electronic devices.
Potential for lubrication-free operation: Due to their inherent characteristics, silicon nitride ceramic bearings can operate without lubrication in certain applications, reducing maintenance requirements and eliminating
Disadvantages of silicon nitride bearings
Expensive: Due to its complicated preparation process, the price is relatively high.
Sensitive to impact: Silicon nitride bearings are susceptible to impact damage than zirconia bearings.
Silicon nitride bearing cage
Si3N4 ceramic bearings are available in a range of cage options, each tailored to specific requirements:
PEEK Cage: Known for its high strength and chemical resistance, PEEK cages are ideal for a variety of harsh environments.
PTFE cages: These cages have excellent chemical inertness and low friction, making them ideal for applications requiring minimal resistance.
316 Stainless Steel Cage: Best suited for applications requiring strength and moderate heat and corrosion resistance.
Enhanced load capacity: Full complement silicon nitride ceramic bearings feature extra balls and no cage, which has a load capacity approximately 20% higher than cage bearings.
Speed considerations: However, due to the increased number of rolling elements and the resulting friction, the maximum operating speed of these bearings is 70% lower than comparable bearings with cages.
Feature | Zirconia ceramic bearings | Silicon nitride ceramic bearings | Silicon carbide ceramic bearings |
Material hardness | High | very high | extremely high |
Weight | lighter than steel | About. 40% lighter than steel | lighter than steel |
Friction coefficient | low to medium | very low | low |
Highest temperature resistance | up to 400°C | up to 1200°C | up to 1600°C |
Corrosion resistance | very good | Excellent | Excellent performance in acidic and saline environments |
electrical insulation | High | High | Changing |
thermal expansion | ease | low | low |
Impact Resistance/Shock Resistance | Good | Good | High |
To maximize silicon nitride bearing life and performance, operation below maximum load and rated speed is recommended. This approach is particularly important because they are brittle than less hard materials.
Application of silicon nitride bearings
Si3N4 ceramic bearings are widely used in various industries due to their unique characteristics. Main applications include:
Marine Applications: Their resistance to complete and permanent submersion makes them ideal for marine applications.
High vacuum environment: The material properties of silicon nitride are beneficial for high vacuum applications.
Precision applications: Low friction and high load-bearing capacity make it suitable for precision machinery.
Electric vehicles: In the electric vehicle industry, their lightweight nature and electrical insulation properties increase motor efficiency and reliability.
Zirconia ceramic bearings are white. Generally, the inner and outer rings and balls are made of zirconia, and the cage is made of PTFE (that is, Teflon). This combination can withstand temperatures up to 240 degrees Celsius, but if the temperature resistance is required to exceed 240 degrees Celsius to 400 degrees Celsius, the ball must be filled with zirconia (that is, the cage is not used, and the entire ball is made of zirconia), so It can withstand temperatures of about 400 degrees.
Zirconia bearings are mainly ceramic bearings made of zirconia (ZrO2) as the main raw material. It has outstanding high toughness, high flexural strength and high wear resistance, which make it excellent in many fields. In addition, the thermal expansion coefficient of zirconia ceramics is close to that of metals, allowing it to be perfectly combined with metals. Another important feature of zirconia bearings is its thermal insulation properties, which allow it to work in high temperature environments and withstand rapid temperature changes. Ceramic bearings made of ZrO2 or zirconium dioxide are a tough ceramic material with expansion properties very similar to steel, but are 30% lighter. This is an advantage when considering the fit of the shaft and housing in high-temperature applications, where bearing expansion may mean the shaft no longer fits. Although they are often referred to as ZrO2 bearings, they are actually made from yttria-stabilized ZrO2, which gives the material greater strength and resistance to fracture at room temperature. They are also extremely waterproof, which means they are often used in marine applications, particularly where equipment is completely submerged, or where traditional steel bearings cannot cope with the load or speed.
Zirconia ceramic ball bearings VS silicon nitride ceramic ball bearings
Zirconia ceramic bearings (ZrO2) and silicon nitride ceramic bearings (Si3N4) are both types of ceramic bearings. They are usually widely used in the field of high-precision machinery industry or in the field of abrasive materials. The main differences between zirconia ceramic ball bearings and silicon nitride ceramic ball bearings are:
Color
than 80% of zirconia ceramic balls are mainly white, and white zirconia ceramic balls are their true color. But sometimes you see that ceramic balls appear light yellow or gray, because the zirconia material contains a small amount of impurities. Zirconia ceramic balls have the advantages of high toughness, high flexural strength and wear resistance, excellent thermal insulation properties, and a thermal expansion coefficient close to that of steel balls. Silicon nitride ceramic balls are mainly carbon black. They are extremely resistant to high temperatures and their strength can be maintained up to 1,200 degrees without decreasing. They are one of the hardest materials in the world.
Physical performance comparison
In terms of physical properties, zirconia ceramic balls have excellent wear resistance and corrosion resistance, while silicon nitride ceramic balls also have equally excellent performance. At the same time, silicon nitride ceramic balls also perform well in terms of processing accuracy. Therefore, in the application fields of high-precision machinery industry, such as ultra-precision bearings, in addition to the widespread use of steel balls, ceramic balls have also begun to become popular in precision bearings. Because ceramic balls have anti-corrosion and anti-rust characteristics compared to bearing steel balls, and the processing accuracy is even higher than steel balls.
At the same time, it can play the role of high temperature resistance in high temperature environments. Therefore, ceramic balls appear in bearings and other ultra-precision machinery fields, such as guide rails, linear sliding accessories, etc., and have a tendency to replace steel balls.
Material properties | Zirconia Bearing | Silicon Nitride Bearing |
Density (kg·m-3) | 5900 | 3250 |
Modulus of elasticity (GPa) | 205 | 310 |
Compressive strength (MPa) | 2000 | >3500 |
Modulus of rupture (MPa) | 600-900 | 700-1000 |
Vickers hardness (GPa) | 10-13 | 14-18 |
Toughness (MPa·m1/2) | 8-12 | 5-8 |
Thermal expansion coefficient (K-3·10-6) | 12 | 3.4 |
Specific heat (J·kg-1·K-1) | 400 | 800 |
Upper limit of use temperature (℃) | 750 | 1050 |
Impact resistance | medium | High |
Rolling contact fatigue failure mode | Peel off | Peel off |
From the table, we can know that the density of silicon nitride is 55.09% of that of zirconia ceramics. Ceramic bearings made from silicon nitride are lightweight, allowing them to be used in medical devices, home appliances, aerospace equipment engines and racing car crankshafts. At the same time, due to its low density, when silicon nitride is used as a rolling element, the centrifugal force generated by the rotating body when the bearing rotates is reduced, which is conducive to high-speed rotation. This allows it to be used in gas turbine engines, machine tool spindles, and centrifugal separation. equipment and other fields.
The elastic modulus and compressive strength of silicon nitride are also higher than those of zirconium oxide, which is beneficial to the bearing’s ability to withstand stress; the thermal expansion coefficient of silicon nitride is smaller than that of zirconium oxide, which is beneficial to reducing the bearing’s response to temperature. The changing sensitivity makes the bearing operating speed range wider; silicon nitride’s high temperature resistance, corrosion resistance and excellent chemical stability allow silicon nitride ceramics to be used in higher temperatures and in places where zirconium oxide such as sodium hydroxide sulfate cannot be used. Strong acid-base scenes.
Although silicon nitride ceramics have the characteristics of strong adaptability and superior performance, the cost of silicon nitride ceramic bearings is relatively high. Compared with other ceramic materials (silicon nitride, etc.), the preparation process of zirconia materials is relatively simple, the cost of the green body is low, and it is easy to be marketed. Therefore, zirconia ceramic bearings can be used in applications that have relatively low performance requirements and low cost requirements. Lower scene. At the same time, the toughness of zirconia is higher than that of silicon nitride, which is beneficial to the stable use of bearings.
Is the added cost worth it?
All-ceramic bearings are generally rounder, smoother and harder than steel, with excellent corrosion and heat resistance, higher dimensional stability and lower density. However, this comes at a cost. Ceramic bearings are much expensive than steel bearings. So, when is it worth investing in ceramic bearings?
High-value applications, such as laboratory equipment, have exact requirements that need to be met every time the application is used. Using the wrong components in such equipment can contaminate research conditions or cause the study to stop altogether. This is the same as in medical equipment, where the contamination-free and non-magnetic properties of ceramic bearings are critical.
Take magnetic resonance imaging (MRI), an imaging technique primarily associated with hospital MRI scanners. The technology uses strong magnetic fields to generate two- or three-dimensional images of any living object. Standard steel bearings cannot be used in these scanners due to magnetism, so ceramic bearings are the best choice for these high-value applications.
Likewise, as integrated circuit manufacturers strive to make their chips faster, smaller, and cheaper, semiconductor manufacturing equipment companies have become reliant on advanced ceramic components to achieve the required performance. Bearings made from silicon nitride instead of standard aluminum oxide (aluminum oxide) provide electrical insulation and good corrosion resistance.
In modern industrial fields, bearings are widely used, and zirconia bearings and silicon nitride bearings, as two high-performance ceramic bearings, have become the first choice in many high-demand situations due to their unique physical and chemical properties. So what is the difference between the two and how should we choose?
Silicon nitride has a similar resistivity and dielectric constant to aluminum oxide, but due to its microstructure, the material is much stronger. All-ceramic bearings can accommodate the many challenging conditions present in the semiconductor production phase; from oven temperatures approaching 1400 degrees Celsius, to the air quality of Class 1 clean rooms. Suddenly, the added cost is clearly justified.
In general, zirconia bearings and silicon nitride bearings each have their own advantages and disadvantages. When selecting, you need to consider the actual needs and application conditions to select the most suitable material. For example, zirconia bearings are a good choice for applications that require high wear resistance and heat insulation; while silicon nitride bearings are suitable for applications that require high strength and corrosion resistance.
Full ceramic vs hybrid ceramic bearings?
When most people think of ceramic bearings, they are usually referring to hybrid versions. Hybrid bearings sit somewhere in the middle between ceramic and steel and typically include stainless steel races or rings and ceramic balls. The steel inner and outer rings of hybrid bearings can be machined to very tight tolerances, meaning they are best suited for applications such as electric motors, laboratory equipment and machine tools.
For example, on a grinder, friction can be reduced by adding ceramic hybrid bearings and a synthetic grease lubricant, thereby increasing revolutions per minute (RPM) by 25%. A grinding spindle with hybrid ceramics can run for 4,000 hours without any problems, while a grinding spindle with steel bearings can run for 3,000 hours. Hybrid bearings also reduce temperatures by nearly 50%. In horizontal machining centers, switching from conventional to hybrid bearings has been shown to reduce bearing temperatures from 60 degrees Celsius to 36 degrees Celsius at 12,000 RPM.
Higher speeds can be achieved using hybrid bearing combinations than fully ceramic bearings because the less brittle metal rings are less prone to sudden catastrophic failure at high speeds or under load. That said, the corrosion resistance of hybrid bearings pales in comparison to that of fully ceramic bearings. Specifying the right bearings for extreme environments has always been a complex issue. But just as zirconia clarified the origins of life, asking these three questions will aid the decision-making process.