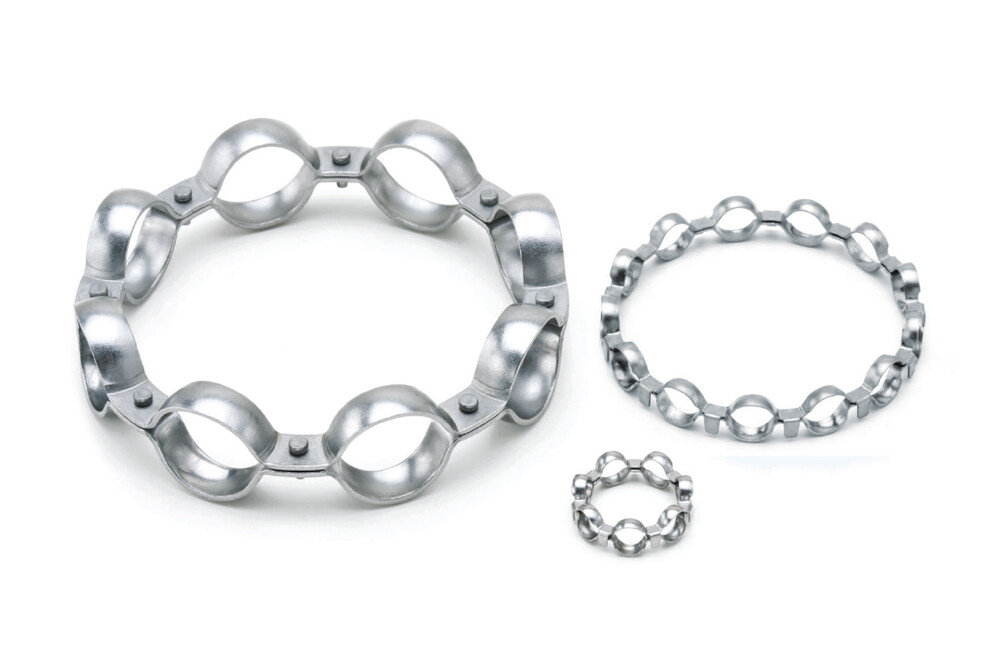
Bearing Manufacturer & Supplier
Specialize in ball bearings, roller bearings, thrust bearings, thin section bearings etc.
You Should Know About Bearing Cages
Although the bearing is composed of many parts, the cage can also be said to be the “blood vessel” of the bearing. Therefore, in the performance of the bearing, the material of the cage is directly related to the efficiency of the bearing. Bearing cage is a bearing part that wraps all or part of the rolling elements and moves with them to isolate the rolling elements. It usually also guides the rolling elements and keeps them within the bearing.
When a rolling bearing is working, especially when the load is complex and rotates at high speed, the cage must withstand large centrifugal force, impact and vibration. There is large sliding friction between the cage and the rolling elements, and a large amount of heat is generated. The combined effect of force and heat can lead to cage failure, and in severe cases, the cage can be burned and broken. Therefore, the cage material is required to have good thermal conductivity, good wear resistance, small friction coefficient, small density, a certain combination of strength and toughness, and good elasticity and stiffness. An expansion coefficient similar to that of rolling elements. And good processing performance. In addition, the cage is also affected by chemical media, such as lubricants, lubricant additives, organic solvents and coolants.
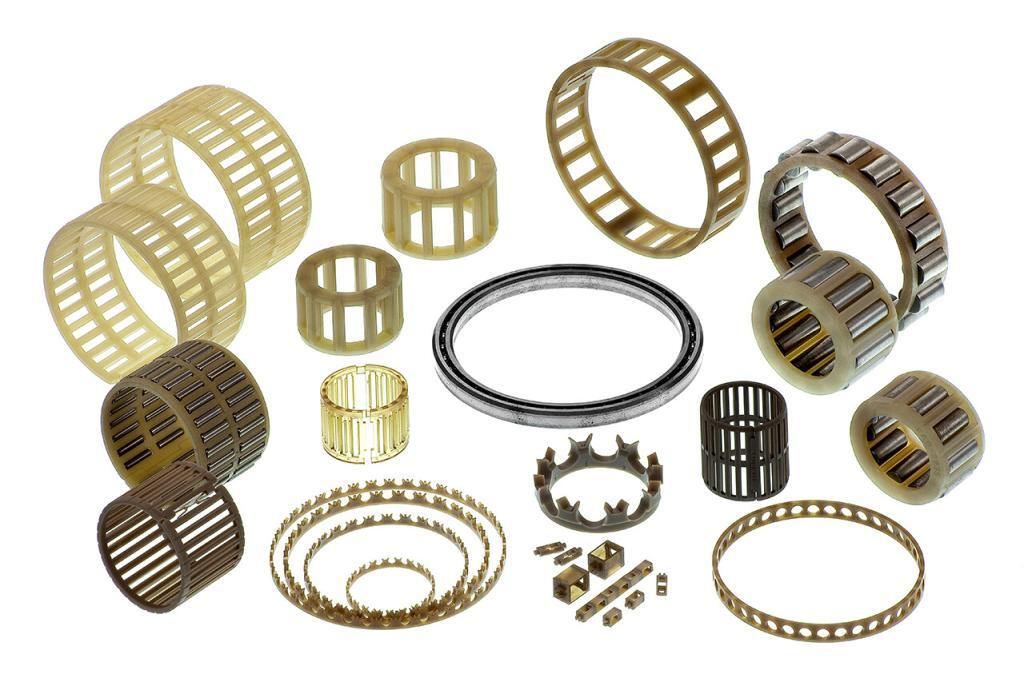
Table of Contents
ToggleThe role of bearing cage
The main purpose of the bearing cage is to maintain a suitable distance between the rolling elements and avoid direct contact between adjacent rolling elements to maintain friction and the resulting heat at a minimum level; to keep the rolling elements evenly distributed In all bearings, the load can be distributed evenly in all bearings, so that the load can be distributed evenly and reduce noise. The rolling elements can be correctly guided in the no-load zone to improve the rolling conditions in the bearing and avoid destructive accidents. drag.
Classification of bearing cages
Commonly used cages are mainly divided into metal cages and non-metallic cages according to material types. There are also composite cages, etc. Special-purpose bearing cages should also meet the requirements of special working conditions. Such as high temperature resistance, corrosion resistance, self-lubricating (used in vacuum) or non-magnetic, etc.
Steel cage material
Due to its high strength, good toughness, and ease of processing, steel cage materials are commonly used in rolling bearings. Usually steel retainers are cold stamped from high-quality carbon steel sheets. In addition, other mechanical processing methods can also be used as needed. Commonly used steel cage materials include 20, 30, 45, 0Cr18Ni9, 1Cr18Ni9Ti, 40CrNiMo, ML15, ML20, etc. Steel cages are generally heat treated to eliminate stress and restore plasticity. Including high temperature tempering, recrystallization annealing, etc. In order to reduce the friction coefficient of the steel cage, the finished cage must be surface treated if necessary.
Nonferrous metal cage materials
Different from steel, non-ferrous metals have their own special properties. For example, aluminum alloy has the characteristics of low density, good thermal conductivity, and good corrosion resistance; copper alloy has the characteristics of good thermal conductivity, small friction coefficient, good formability, and high operating temperature; Zinc-aluminum alloy has the advantages of low cost, low density and excellent performance.
Non-metallic cage materials
Non-metallic cage materials mainly include polymers and composite materials, including nylon, phenolic tape, polytetrafluoroethylene, etc. Polymer materials have a good match of strength and elasticity. The good sliding properties allow the polymer cage to generate only a small amount of friction when it moves relative to the lubricated rolling element surface, thus minimizing the heat generation and wear of the bearing. Under the condition of lack of lubricant, the polymer cage still has excellent movement characteristics. It can ensure that the bearings continue to operate for a period of time without damage. Due to the lower density of polymers, cages made from them have less inertia.
In addition to being made of pure materials, the cage also uses modified polymer materials. Use other materials for filling or reinforcement.
After the cage is installed into the bearing. Due to the gap between the cage and the rolling elements, the cage can be offset in the radial direction, which is called the radial offset. Its offset can be expressed by the following formula:
It should be ensured that when the cage reaches the maximum radial offset, the cage does not contact the bearing ring.
Bearing cage manufacturing process
Die cast cage
The raw materials of the die-cast cage are aluminum alloy and brass. The raw materials are melted and poured into the die-casting mold of the die-casting machine, and the cage is die-cast in one go. The casting gate is turned on a lathe.
(1) The cage is directly die-cast, which can obtain good geometric shape and dimensional accuracy without mechanical processing, and has high production efficiency.
(2) After die-casting, the metal crystallizes and solidifies, with precise structure, good surface quality and wear resistance.
(3) High material utilization rate and reduced cost.
However, when die-casting an aluminum alloy cage, large-tonnage equipment is required, and the mold design and manufacturing are complicated. The cage pockets are easily strained during die-casting. Under the conditions where the bearing is subjected to impact, vibration and variable speed, the quality of the die-cast cage needs to be further improved.
Plastic cast cage
Vacuum-dried granular engineering plastics are placed in a barrel, heated by resistance wires and melted into a semi-liquid state. Pressurized by a plunger or moving screw, the semi-liquid raw materials are injected from the nozzle into the forming mold of the injection molding machine. After being insulated, , obtain the required cage after cooling.
(1) The cage is molded in one injection molding, which can obtain precise geometric shape and dimensional accuracy and low surface roughness value without the need for mechanical processing, and the production efficiency is high.
(2) The mold and plastic casting are simple to form, the bearing is easy to assemble, and it is easy to realize automatic control.
(3) The plastic cage has good properties such as wear resistance, antimagnetic and low friction.
However, due to the shortcomings of thermal deformation, aging and brittleness of the plastic itself, as well as some problems in the cage structure and plastic injection process, the application of the plastic cast cage is limited.
For engineering plastic cages, the performance of each manufacturer is slightly different, but they are generally similar. This kind of cage is light in weight and suitable for high-speed applications. over, the failure mode of this kind of cage is not sudden bursting, so it is suitable for some occasions where sudden shutdown is not allowed. However, for mining machinery, this kind of cage is not suitable for use due to safety considerations, because its damage does not occur suddenly, but as the temperature gradually rises to a certain level, it is completely damaged, which will be very dangerous in explosive situations. . At the same time, this kind of cage has a temperature limit, usually -40~120℃: There is basically no obstacle to the brass cage, but it is not suitable for environments with ammonia. Generally, small bearings do not use copper cages. There are no restrictions on steel cages, but large-size bearings do not use steel cages.
How to choose a bearing cage
The materials of bearing cages can be classified according to their manufacturing materials and application scenarios. The following are some common bearing cage materials:
Steel cage: Usually made of high-quality carbon steel or alloy steel, it has the characteristics of high strength, wear resistance and corrosion resistance. Suitable for high-speed, heavy-load and high-temperature applications, such as bearings in aerospace engines and automobile gearboxes.
Advantages and performance: This kind of cage has high strength and light material. It is mostly used in deep groove ball bearings, spherical roller bearings and tapered roller bearings, and is generally not affected by mineral oil-based or alkali-containing oil-based lubricants in rolling bearings.
Usage limitations: susceptible to rust due to the influence of water and water vapor;
Operating temperature: The operating temperature of the cage can reach 300°C.
Brass cage: Usually made of brass or bronze, it has excellent wear resistance, corrosion resistance and low friction coefficient. Suitable for medium speed and light load applications, such as bearings in household appliances, instruments and office equipment.
Brass has high tensile strength and is not affected by common bearing lubricants. It is often used in small and medium-sized bearings. However, due to the high price of copper, the price of brass cages is also high. The main features are as follows:
Cage type: stamping and solid, stamping is only suitable for small and medium sizes;
Material: Brass plate, brass casting or brass forging. Brass has high tensile strength, and its mechanical strength is equivalent to that of steel plate stamping cage, but its density is relatively small, its limit speed is high, and its price is higher.
Advantages: Not affected by lubricants, including synthetic oils and greases;
Restrictions on use: Brass cages cannot be used in situations above 300°C, and are not suitable for ammonia (such as cooling), because ammonia will cause seasonal breakage of brass;
Operating temperature: The operating temperature is below 300°C.
Nylon cage: Usually made of polyamide (PA66) and other engineering plastics for injection molding, it has the characteristics of light weight, corrosion resistance, good insulation and easy processing. Suitable for light load, low speed and high temperature applications, such as bearings in power tools, sewing machines and food processing machinery.Polyamide nylon material has the advantages of high elasticity and light weight. This cage has very good sliding and self-lubricating properties. It is a new generation product that currently replaces iron cages.
Advantages and performance: Polyamide nylon material has the advantages of high elasticity and light weight.
This cage has very good sliding and self-lubricating properties. Especially suitable for situations where there is vibration impact stress or high acceleration and deceleration, or the inner and outer rings of the bearing are tilted to each other;
Limitations of use: The polyamide nylon cage may be affected by special lubrication (corrosive additives in the lubricant) and cannot be used in vacuum as it will become brittle due to dehydration;
Working temperature: The working temperature is lower than 120°C and greater than -40°C. If the temperature is too low, the nylon will lose its elasticity.
Phenolic cage: composed of phenolic resin, glass fiber cloth and other materials, it has the characteristics of high strength, high temperature resistance and good insulation properties. Suitable for high temperature and high speed applications, such as bearings in aircraft engines and gas turbines.
Other materials: In addition to the common materials mentioned above, there are also other materials used in the manufacture of bearing cages, such as aluminum, magnesium and other light metal materials, as well as some composite materials. These materials are typically selected based on the requirements of the specific application.
Factors to consider when choosing a bearing cage
Working environment: The working environment of the bearing has a great influence on the material of the cage. For example, in high-temperature environments, high-temperature-resistant materials should be selected, such as steel or phenolic tape cages; in corrosive environments, corrosion-resistant materials should be selected, such as copper or nylon cages.
Bearing type: Different types of bearings have different cage materials. For example, deep groove ball bearings, spherical roller bearings and tapered roller bearings usually use steel cages; while cylindrical roller bearings can use copper or nylon cages.
Speed and load: The speed and load are also important factors in selecting the cage material. Under conditions of high speed and heavy load, it is necessary to choose materials with high strength, wear resistance and corrosion resistance, such as steel or copper cages.
Economy: On the premise of meeting performance requirements, economic factors should be considered. Some lightweight, low-cost materials such as engineering plastics are suitable for light loads, low speeds and high temperatures.
Other factors: In addition, factors such as the size, shape, processing method and installation requirements of the cage need to be considered.
Several factors need to be considered when selecting a bearing cage, including working environment, bearing type, speed and load, economics and other related factors. In actual applications, selection should be based on specific requirements and conditions to ensure the normal operation and service life of the bearing.