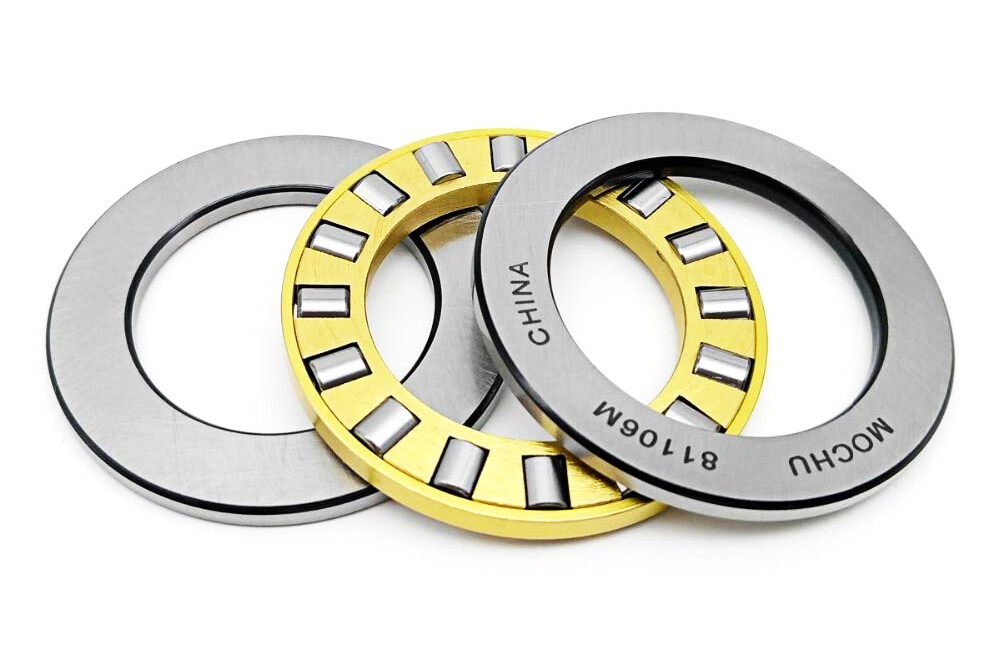
Bearing Manufacturer & Supplier
Specialize in ball bearings, roller bearings, thrust bearings, thin section bearings etc.
What You Should Know About Thrust Bearings
When purchasing a thrust bearing, we all dream of its long-term smooth operation. The trick is to select the correct thrust bearing, install it correctly and perform proper maintenance and lubrication. In this blog, Aubearing will discuss thrust bearing information for you and provide constructive advice for you to purchase the correct thrust bearing.
Table of Contents
ToggleWhat is a thrust bearing?
Thrust bearings are a common type of bearings. They are mainly composed of seat rings, shaft rings, rolling elements, and cage components. They are specially designed to bear axial loads (i.e., forces applied parallel to the shaft). Thrust bearing is a kind of separated bearing. The shaft ring, seat ring, cage and rolling elements are separated from each other. The shaft ring is a ferrule that matches the shaft, and the seat ring is a ferrule that matches the bearing seat hole, with a gap between it and the shaft. The main function of thrust bearings is to reduce friction and support axial loads on rotating shafts. The structure of thrust bearings enables them to provide high stiffness and maintain the rotation of the components they support. For mechanical systems, precision and stiffness are crucial. This makes thrust bearings one of the key components in various industries, such as automotive, aerospace and industrial fields.
Thrust bearing materials
Chromium steel: The main material used in thrust ball bearings is chromium steel. Chromium steel is a hardened alloy steel with very strict requirements on the uniformity of chemical composition, the content and distribution of non-metallic inclusions, and the distribution of carbides. It is one of the most stringent steel types in all steel production. , is also a material commonly used in thrust bearings. Chromium steel has high wear resistance and load-bearing capacity, and is suitable for working environments under medium load, high speed and high heat conditions. Disadvantages: susceptible to corrosion.
Stainless steel: Stainless steel has good corrosion resistance and high strength, and is suitable for use in harsh environments such as high temperatures, strong acids and alkalis. Disadvantages: Stainless steel has high density and relatively high price.
Ceramics: Ceramics have the advantages of light weight, wear resistance, corrosion resistance, high hardness, etc., and are suitable for high-speed, high-temperature, and high-load applications. Disadvantages: The price is relatively high.
Polytetrafluoroethylene: Polytetrafluoroethylene is a colorless, odorless, non-toxic, non-polluting polymer material with excellent wear resistance, chemical corrosion resistance and low friction coefficient. However, PTFE has low density and low strength, so it is not suitable for heavy load applications.
According to the direction of rotation, it can be divided into one-way and two-way thrust bearings. One-way thrust ball bearings can only bear axial load in one direction, cannot limit the radial displacement of the shaft, and have a very low limit speed. Bidirectional thrust ball bearings can bear axial loads in both directions and limit axial displacement in both directions.
According to the application classification, they can be divided into thrust ball bearings and thrust roller bearings. Thrust bearings are divided into thrust ball bearings and thrust roller bearings.
Thrust ball bearings
Thrust ball bearings are divided into thrust ball bearings and thrust angular contact ball bearings. They are composed of washers with raceways, balls, and cage components. The raceway ring that matches the shaft is called the shaft ring, and the raceway ring that matches the shell is called the seat ring. The two-way thrust ball bearing matches the middle ring with the shaft. One-way bearings can withstand one-way axial load, and two-way bearings can Bearings can withstand bidirectional axial loads. Bearings with a spherical mounting surface of the seat ring have self-aligning properties, which can reduce the impact of installation errors. Such bearings are mainly used in automobile steering mechanisms and machine tool spindles. The following are commonly used thrust ball bearing specifications:
One-way thrust ball bearings: 51100, 51200, 51300, 51400 series.
Bidirectional thrust ball bearings: 52200, 52300, 52400 series.
Angular contact thrust ball bearings: 234400, 234700, 562000, 562900 series.
Thrust roller bearings
Thrust roller bearings are used to bear combined shaft and radial loads where axial load is the main component, but the radial load shall not exceed 55% of the axial load. Compared with other thrust roller bearings, this kind of bearing has a lower friction factor, higher rotation speed, and has self-aligning performance. Thrust roller bearings are divided into thrust cylindrical roller bearings, thrust spherical roller bearings, thrust tapered roller bearings, and thrust needle roller bearings. Thrust cylindrical roller bearings are mainly used in oil drilling rigs, iron and steel making machinery. Thrust self-aligning Roller bearings are mainly used in hydraulic generators, vertical motors, propeller shafts for ships, tower cranes, extruders, etc. Main uses of thrust tapered roller bearings: One-way: crane hooks, oil drilling rig swivels. Two-way: steel rolling mills Roller neck.
Type 80000 thrust cylindrical roller bearings, type 90000 thrust tapered roller bearings and type AXK thrust needle roller bearings can bear one-way axial load. They have much greater axial load capacity than thrust ball bearings, and are rigid and Occupies little axial space. Thrust cylindrical roller bearings and thrust needle roller bearings are suitable for low-speed applications. The speed of thrust tapered roller bearings is slightly higher than that of thrust cylindrical roller bearings.
How do thrust bearings work?
The working principle of thrust bearings is based on the loading of thrust (axial) loads and the reduction of friction between the moving parts of a mechanical clock. Let’s take a typical thrust bearing as an example, model number F10-18M.
The F10-18M consists of a fixed washer, a rotating washer, ball and cage. Between the two washers are the rolling elements – balls, in this case balls. When an axial load is applied, the bearing F10-18M remains stationary, is connected to the housing, fixed on the shaft and rotates. Rolling elements located between these washers facilitate this rotation. Their main task is to reduce the friction that occurs during this rotation. The material composition of the F10-18M is a key factor. F10-18M washers and rolling elements are typically constructed from hardened chromium steel for durability and wear resistance under high pressure conditions. This design minimizes friction and helps extend the life and efficiency of the installed mechanical system. In addition, F10-18M thrust bearings are designed to achieve smooth and consistent rotational motion, which is critical in everything from simple machines to complex automotive transmissions. When selecting thrust bearings such as F10-18M, factors such as the size of the axial load, the rotational speed of the shaft and environmental conditions need to be considered. Engineers and designers must carefully consider these parameters to ensure optimal performance and service life of the thrust bearing in the intended application.
Install thrust bearing
Although the installation operation of thrust bearings is relatively simple, errors often occur during actual maintenance, that is, the tight ring and loose ring of the bearing are installed in incorrect positions. As a result, the bearing loses its function and the journal is quickly worn. The tight ring is installed on the end face of the stationary part, that is, it is incorrectly assembled. The inner ring of the tight ring has a transitional fit with the journal. When the shaft rotates, the tight ring is driven and friction occurs with the end face of the stationary part. When an axial force (Fx) is applied, the friction torque will be greater than the inner diameter fit resistance torque, resulting in the tightening ring. The mating surfaces of the ring and the shaft are forced to rotate, aggravating journal wear.
When installing a thrust bearing, the verticality of the shaft ring and the shaft centerline should be checked. The method is to fix the dial indicator on the end face of the box shell, so that the contact head of the dial is on the raceway of the bearing shaft ring while rotating the bearing, while observing the dial indicator pointer. If the pointer is deflected, it means that the shaft ring and the center line of the shaft are not perpendicular. When the hole in the box shell is deep, an extended dial indicator can also be used for inspection. When a thrust bearing is installed correctly, its seat ring can automatically adapt to the rolling of the rolling elements to ensure that the rolling elements are located in the upper and lower raceways. If installed upside down, not only will the bearing not work properly, but also the mating surfaces will be severely worn. Since the difference between the shaft ring and the seat ring is not very obvious, extra care should be taken during assembly to avoid making mistakes. In addition, a gap of 0.2-0.5mm should be left between the thrust bearing seat ring and the bearing seat hole to compensate for errors caused by inaccurate parts processing and installation. When the center of the bearing ring deviates during operation, this gap will This ensures that it adjusts automatically to avoid contact and friction, allowing it to operate normally. Otherwise, severe damage to the bearing will occur.
What is the lubricant for thrust bearings?
Lubrication of thrust bearings is critical to their efficient operation and service life. Lubricant selection depends on several factors, including bearing operating conditions, load, speed, temperature and service environment. Generally, there are two main types of lubricants used in thrust bearings:
1 – Oil Lubrication: Oil is typically used in normal to high speed applications. It can be applied in a variety of ways, including direct methods (such as oil baths, oil mist and oil sprays) or indirect methods (such as oil circulation systems). Oil not only reduces friction and wear, it also helps cool the bearings by removing heat. The specific type of oil (such as mineral, synthetic or blended oils) is selected based on operating temperature, speed and load conditions.
2 – Grease Lubrication: Grease is a commonly used thrust bearing lubricant for applications where high speed is not a critical factor. It is a mixture of oil and thickeners, often with additives added to improve performance characteristics such as resistance to oxidation, corrosion and high temperature resistance. Where minimal maintenance is required, grease is preferred as it tends to last longer and acts as a seal to prevent contaminants from entering. The specific type of grease is selected based on the application requirements of the bearing.
Thrust Bearing Selection Guide
Loading capacity
Bearing load is a very important parameter in the selection of one-way thrust bearings. First, determine the radial force and axial force that the bearing bears, and then select the corresponding bearing model and size according to the bearing load capacity table. The carrying capacity of the thrust bearing must match the actual load, and generally a specification larger than the actual load should be selected.
Rotation speed
When selecting a one-way thrust ball bearing, the rotation speed also needs to be considered. According to the related properties of the bearing speed and the bearing structure and material, the rated speed of the bearing and the size of the bearing ball diameter need to be determined during selection to ensure that the bearing can operate normally at the specified speed. Generally speaking, the allowable speed of thrust ball bearings should not be greater than the rated value.
Roundness error and eccentricity
In the selection of one-way thrust ball bearings, the roundness error and eccentricity of the bearing should also be considered. If the roundness error and eccentricity of the bearing are too large, it will cause the bearing to produce vibration and noise during operation, and even cause damage to the bearing. Therefore, it is necessary to pay attention to the roundness error and eccentricity of the bearing during the selection process, and select bearings with the lowest possible error and eccentricity.
Environmental conditions:
Thrust bearings should be selected that are suitable for environmental conditions. For example, under environmental conditions such as high temperature, high speed, and high load, thrust bearings that are resistant to high temperature, high speed, and high load should be selected. Bearings will generate heat during operation. If the temperature is too high or the humidity is too high, it will affect the service life of the bearings and even cause damage to the bearings.
Installation and maintenance:
When installing and maintaining thrust ball bearings, care should be taken to keep the bearings clean, smooth and correctly installed.
Matching issues: The matching of thrust ball bearings and matching parts is also very important, such as matching shafts, matching holes, etc., so that the bearings and parts have good fit.
Conclusion
When selecting thrust ball bearings, you must fully consider the actual needs, select appropriate specifications according to the needs, and pay attention to installation and maintenance issues, so as to ensure the normal use and life of the bearings.