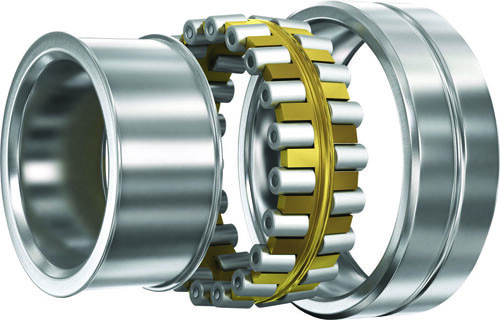
Bearing Manufacturer & Supplier
Specialize in ball bearings, roller bearings, thrust bearings, thin section bearings etc.
What You Should Know About Cylindrical Roller Bearings
Cylindrical roller bearings have high radial load capacity and moderate thrust loads. They contain cylindrical rollers, but are not true cylinders. Instead, these rollers are crowned or end relieved to reduce stress concentrations. This geometry results in low friction and allows high speed applications.
Cylindrical roller bearings are usually available in precision classes such as RBEC-5, which is a Roller Bearing Engineers Council (RBEC) classification. RBEC classes describe the range of precision and tolerances for different types of bearings. Generally, the higher the RBEC number, the tighter the bearing tolerances. Typically, cylindrical roller bearings are lubricated with oil, which is also used as a coolant.
Table of Contents
ToggleCylindrical Roller Bearing Assemblies
Cylindrical roller bearings are radial roller bearings. All cylindrical roller bearings have four basic components: inner ring, outer ring, rollers and cage. The bearing rings and rollers carry the load, and the cage holds the rollers in place.
Cylindrical roller bearings vary in clearance and lubrication options, depending on the manufacturer. They can be crafted together with the cage or as a complete supplementary part. Some have no ribs on both rings, allowing the rings to move axially and can be used as free end bearings.
Stamped steel or machined brass are the most common materials used to construct cylindrical roller bearing cages. Still, some use molded polyamide, which makes the bearing run smoother and quieter. When necessary, hardened high carbon steel or carburized low carbon steel enhances bending fatigue and withstands heavy impact loads.
Materials for cylindrical roller bearings
Most cylindrical roller bearings are made of alloy steel or mild steel. Some applications require the use of case hardened or through hardened high carbon bearing steels. High carbon grades of steel do not require cylindrical roller bearing carburization and can be case hardened by induction heating or through hardened by conventional heating methods. When using low carbon, carburized grades of steel, the carbon is introduced after the cylindrical roller bearing has been machined to a depth sufficient to produce a hardened shell that can carry the bearing loads. The addition of carbon and alloys ensures the proper combination of a hard, fatigue-resistant case with a tough, malleable core.
Cylindrical Roller Bearing Specifications
Bore and outside diameter (OD) are important specifications to consider when selecting a cylindrical roller bearing. The bearing industry uses a standard numbering system for roller bearings with metric diameter bores. For bore size 04 and above, multiply the bore diameter by 5 to determine the bore diameter in millimeters (mm). The outside diameter of cylindrical roller bearings includes the housing, if present, but excludes the flange.
Other important specifications for cylindrical roller bearings include overall width, rated speed (oil), static axial load, static radial load, dynamic axial load, and dynamic radial load.
Axial static load and radial static load are respectively the maximum axial load and radial load that the bearing can bear without permanent deformation.
Axial dynamic load and radial dynamic load are the calculated values of the axial and radial loads that a group of bearings with the same outer ring and stationary inner ring can bear respectively when the rated life of the inner ring is 1 million revolutions.
Types of cylindrical roller bearings
While single row cylindrical roller bearings are the most common type, there are also multi-row cylindrical roller options.
Single row cylindrical rollers are popular because they are separable, making them easier to install and remove. However, they cannot support heavy or oversized radial loads because they only allow axial loads in one direction.
Double row cylindrical roller bearings can often solve load capacity challenges. Double row bearings spread the load over a wider area and handle unstable loads or vibrations. Additionally, a double row bearing takes up less space within the housing than two single row bearings placed back to back. It also optimizes load transfer between the two rows.
Multi-row or four-row cylindrical roller bearings are usually used as roll neck bearings. Four rows of rollers can withstand greater radial loads. Tight diameter tolerances on the contoured rollers allow the bearing to distribute loads evenly. Cages for multiple rows of rollers typically use machined brass finger cages or mild steel finger cages. Still, larger sizes use steel cages with hollow rollers.
Depending on the design or without side ribs, single row bearings have different type designations NU, NJ, NUP, N, NF and double row bearings NNU, NN. AST’s cylindrical roller bearings are available in the following series with various cage designs and metric sizes:
N Series – Bearings of N design are single row cylindrical roller bearing and have two fixed ribs on the inner ring that retain the rollers and cage and one smooth outer ring. This design allows an axial displacement in certain limits, of the shaft in relation to the housing. Therefore, N Series rolling bearings are used in non-locating bearing units. Also, the N Series bearings have virtually no thrust capacity.
NU Series – Are single row cylindrical roller bearings and have two fixed ribs on the outer ring and one smooth inner ring. This design allows an axial displacement in certain limits, of the shaft in relation to the housing. Therefore, NU Series rolling bearings are used in non-locating bearing units. Also, the NU Series bearings have no virtually thrust capacity.
NJ Series – Are single row cylindrical roller bearings and have two fixed ribs on the outer ring and a fixed rib on the inner ring which can guide the shaft in a single direction (axially).
NUP Series – Are single row cylindrical roller bearings and have two fixed ribs on the outer ring and, on the inner ring, a fixed rib and a support washer. This way they can be used as locating bearings, guiding the shaft axially in both directions. Are single row cylindrical roller bearings and have two fixed ribs on the outer ring and has no inner ring. Instead, it uses the shaft as the opposing raceway.
NF Series – Also able to carry incidental thrust loads, this bearing type features two integral ribs on the inner ring and a single rib on the outer ring.
RNU Series – Are single row cylindrical roller bearings and have two fixed ribs on the outer ring and has no inner ring. Instead, it uses the shaft as the opposing raceway.
NN Series – Bearings of NN design are double row cylindrical roller bearing and have three fixed ribs on the inner ring that retain the rollers and cage and one smooth outer ring. This design allows an axial displacement in certain limits, of the shaft in relation to the housing. Therefore, N Series rolling bearings are used in non-locating bearing units. Also, the NN Series bearings have no virtually thrust capacity.
NNU Series – Are double row cylindrical roller bearings and have three fixed ribs on the outer ring and one smooth inner ring. This design allows an axial displacement in certain limits, of the shaft in relation to the housing. Therefore, NU Series rolling bearings are used in non-locating bearing units. Also, the NNU Series bearings have no virtually thrust capacity.
Why Choose Cylindrical Roller Bearings?
When selecting a bearing, several basic factors must be considered. The first factor to consider is the load the bearing can carry – the load carrying capacity. There are two types of bearing loads:
– Radial load: perpendicular to the shaft, at right angles to the shaft (axis of rotation of the bearing).
– Axial (thrust) loads: parallel to the axis of rotation and acting in the same direction as the axis. Consider when the load is parallel to the column.
Each type is designed to support radial or axial loads. If you need bearings that require high radial loads, cylindrical roller bearings are recommended.
Cylindrical roller bearings have high radial load capacity and are suitable for high speeds. They are in linear contact with the raceways. They are designed to be reliable and ideal for the environment. The bearings are versatile and can be used in a variety of applications. They vary by the number of rows of rollers (usually one, two, or four) and whether they have cages. The absence of a cage allows the bearing to have columns, which helps support heavier radial loads.
Why Choose Cylindrical Roller Bearings Over Radial Ball Bearings?
Cylindrical roller bearings are similar to radial ball bearings in that they are designed to accommodate radial loads while minimizing friction. Depending on the application and internal design of the bearing, cylindrical roller bearings and radial ball bearings can also accommodate small amounts of axial load.
In general, roller bearings provide higher load capacity than ball bearings of the same size. Another significant difference between the two types of bearings is their contact area. With ball bearings, the contact area is a single point, while roller bearings touch a larger area.
What are the significant advantages of cylindrical roller bearings?
Higher radial load capacity compared to ball bearings
Roller design accepts faster speeds than other types of roller bearings
Resists damage caused by fatigue
Has a straight outer and inner diameter (can also be tapered)
Flush the inside of the housing
Easy to install, reducing potential installation damage
Slim, saving space and weight
Available in a variety of sizes and materials
Cylindrical Roller Bearing Applications
Cylindrical roller bearings have many applications. Examples include mining, oil production, power generation, power transmission, cement processing, aggregate crushing and metal recycling. Some cylindrical roller bearings are used in briquetting machines, rubber mixing equipment, rolling mills, rotary dryers or pulp and paper machinery. Others are used in construction equipment, crushers, electric motors, blowers and fans, gears and drives, plastic machinery, machine tools and traction motors and pumps.
FAQ
Do cylindrical roller bearings have low friction?
Yes. The design of the rollers and surfaces enables cylindrical roller bearings to carry heavy loads with low friction.
What are the reasons for the failure of cylindrical roller bearings?
Improper mounting and sealing, lubricant failure, and the presence of debris and contamination are the most common causes of bearing failure. Additionally, overloading can cause overheating and failure.
What maintenance procedures should I follow?
Like all bearings, cylindrical roller bearings are subject to rust, pitting, scoring and chipping. Surface-coated bearings help prevent these conditions, extending bearing life.
What surface treatment should I apply to cylindrical roller bearings?
Zinc-nickel plating, zinc, and phosphate coatings help resist rust, pitting, scratching, and chipping.