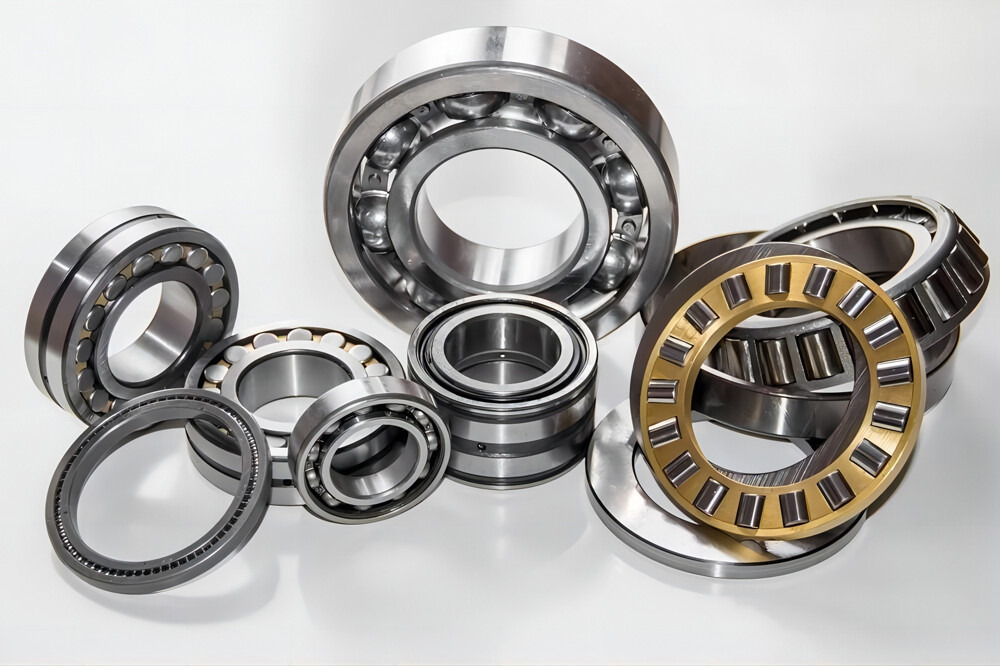
Bearing Manufacturer & Supplier
Specialize in ball bearings, roller bearings, thrust bearings, thin section bearings etc.
What should you consider when selecting bearings?
Bearings are one of the most critical components of any industrial machinery. These high-precision components are essential to reduce friction and carry loads during rotational motion. You will find that many industrial applications feature at least one bearing. There are thousands of bearings on the market, including ball bearings, thin-section bearings, cylindrical roller bearings, tapered roller bearings, needle roller bearings and other types of bearings. Although ball bearings are the most common bearing type, each type has its own characteristics and advantages that make it suitable for certain uses and applications and not suitable for other operating environments.
Selecting and installing the correct bearings is critical to ensuring optimal machine performance. The right bearings not only improve the performance of your machine, but also extend its service life while reducing downtime and maintenance costs. Conversely, choosing the wrong bearing can reduce efficiency, increase maintenance requirements, and possibly even lead to costly downtime. However, choosing the right bearing for your application is not always easy. There are many different factors to consider when selecting a bearing, such as speed, load and operating conditions. If you are unsure, it is best to consult a bearing expert for advice on the best bearing for your application. Aubearing is a leading bearing manufacturer in China. Based on many years of bearing manufacturing experience, here are some factors that should be considered when choosing the right bearing for your application.
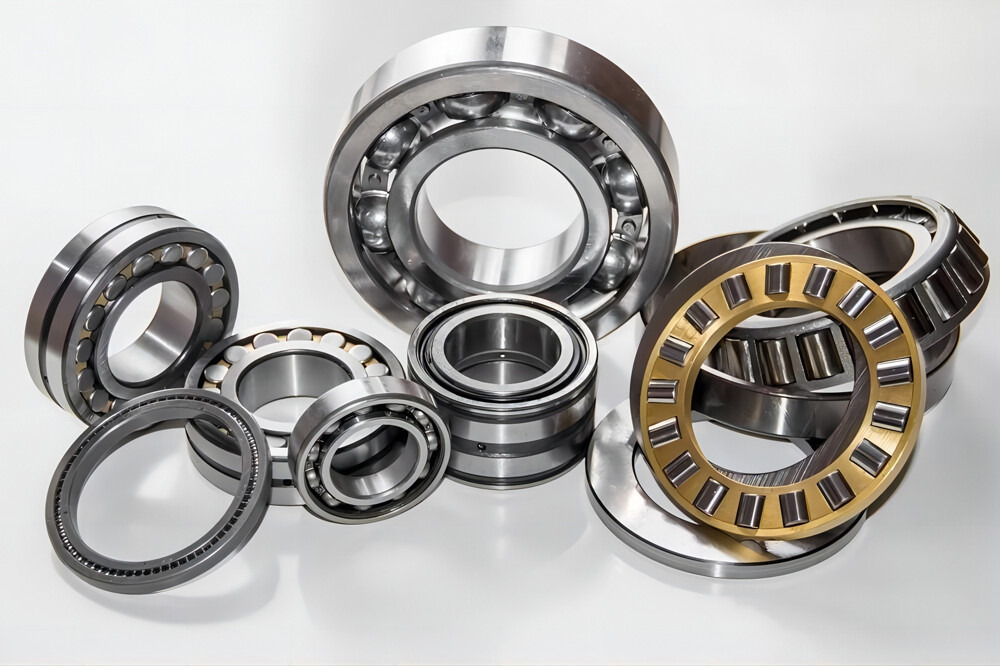
Table of Contents
ToggleBearing working space
The first thing to consider when selecting a bearing is the available mounting space. No matter how well a bearing fits your application requirements, if there is no available space, it cannot be installed. Some types of bearings take up axial space than others, so if the most suitable bearing is too large for your application, there are always alternatives. The available space will determine the bore and outside diameter of the bearing you choose, so it is important to know this information before selecting a bearing. In mechanical design, the size of the shaft is generally determined first, and then the rolling bearing is selected based on the size of the shaft. Usually ball bearings are used for small shafts and roller bearings are used for large shafts. However, when the bearing is limited in the diameter direction of the machine, needle roller bearings, extra light and ultra light series ball or roller bearings can be used; when the bearing is limited in the axial position of the machine, narrow or special bearings can be used. Narrow series of ball or roller bearings.
Bearing Specified load
When we look at bearing specifications, we talk about two different types of loads: radial loads and axial loads. Radial loads are perpendicular to the axis, while axial loads (also called thrust loads) are parallel to the axis. Different bearings can support different types, directions and magnitudes of loads. When a bearing bears both radial load and axial load, it is called combined load. Bearings, such as tapered roller bearings, are specifically designed to withstand combined loads. In some applications, paired bearings may be required to balance variable load conditions, or to account for complex load conditions. In this case, it is best to consult a bearing specialist for expert advice on the best bearing arrangement for your application.
a) Radial load. All types of radial bearings can withstand radial loads. Needle roller bearings and cylindrical roller bearings (NU type and N type) with no ribs on the inner or outer ring can only bear pure radial load.
b) Axial load. Thrust ball bearings and four-point contact ball bearings are most suitable for bearing light or medium pure axial loads; thrust cylindrical roller bearings and thrust needle roller bearings are generally used to bear heavier pure axial loads. One-way thrust bearings can only bear axial loads in one direction, while two-way thrust bearings can bear axial loads in different directions. To bear heavy axial loads in alternating directions, thrust cylindrical roller bearings or thrust spherical roller bearings configured in pairs must be used.
c) Combined load. When radial loads and axial loads act on the bearing at the same time (called combined loads), angular contact ball bearings or tapered roller bearings are generally used. If the radial load is large and the axial load is small, deep groove ball bearings and cylindrical roller bearings with ribs on the inner and outer rings can also be used. Single row angular contact ball bearings, tapered roller bearings, NJ-type cylindrical roller bearings and thrust spherical roller bearings can only bear axial load in a single direction. If there are alternating directional loads, these bearings need to be combined with another bearing to work.
If the axial load is large and the radial load is small, thrust angular contact ball bearings, four-point contact ball bearings, thrust spherical roller bearings, crossed roller bearings, etc. can be used.
Bearing Rotating speed
Each bearing has an optimal operating speed as well as a maximum operating speed. Applications running at high speeds use different types of bearings than applications running at low speeds. Certain bearings, such as deep groove ball bearings and angular contact bearings, are designed to withstand high speeds. However, this usually comes at the expense of some carrying capacity. Cylindrical roller bearings and needle roller bearings often have cages to allow higher operating speeds. Again, this usually reduces the load-carrying capacity of the bearing. If you choose a bearing with a speed rating that is not high enough, your bearing will likely fail quickly due to fatigue, resulting in expensive downtime and the need for replacement. Each bearing model has its own limit speed, which is determined by physical characteristics such as size, type and structure. Exceeding this limit will cause the bearing temperature to rise, the lubricant to dry up, and even the bearing to become stuck. Practice has proved that it is better to work at a speed lower than 90% of the limit speed. The limit speed of grease-lubricated bearings is lower than that of oil-lubricated bearings, and the oil supply method of the bearing has an impact on the achievable limit speed. It must be noted that for grease-lubricated bearings, the limit speed is generally only 80% of the limit speed when the bearing uses a high-quality recirculating oil system, but for oil mist lubrication systems, the limit speed is generally higher than the same basic lubrication system. 50% higher. The design and structure of the cage also affect the limiting speed of the bearing.
Under certain load and lubrication conditions, the maximum speed allowed by a bearing is called the limit speed of the bearing. It is related to many factors such as the type, size, accuracy, clearance of the bearing, the material and structure of the cage, the lubrication method, the nature and amount of lubricant, the size and direction of the load, and the heat dissipation conditions. If the actual working speed of the bearing exceeds the maximum allowable working speed, certain improvement measures need to be taken, such as improving the lubrication method, setting up an effective cooling system, improving the bearing accuracy, appropriately increasing the bearing clearance, switching to special bearing materials and Specially structured cages, etc. When selecting bearing types based on bearing speed, you can refer to the following points:
(1) Ball bearings have higher limit speed and rotation accuracy than roller bearings. Ball bearings should be preferred at high speeds.
(2) The smaller the contact angle of the bearing, the better the conditions for its ring to withstand the inertial centrifugal force of the rolling elements. Therefore, the limit speed of thrust bearings is lower than that of radial bearings, and single-row radial bearings are better than double-row spherical bearings. When the operating speed is high and the axial load is not very large, angular contact ball bearings can be used to bear the pure axial load.
(3) At high speed, bearings with the same inner diameter and smaller outer diameter should be selected. When its load-carrying capacity is insufficient, a wide series of bearings can be used or two bearings can be installed together.
(4) The solid cage allows a higher speed than the stamped cage.
Bearing rigidity
Applying loads to bearings causes elastic deformation. This starts with the contact area between the rolling elements and the raceway. The stiffness of a bearing describes the relationship between the bearing load and the resulting elastic deformation. The higher the stiffness, the smaller the deformation. In many cases, the elastic deformation of the bearing is very small and can be ignored. However, in some applications, such as machine tools, the rigidity of the bearing is critical. Roller bearings are often the bearing choice where a high level of bearing stiffness is required. In addition, various types of bearings can also be preloaded to increase support rigidity. For example, angular contact ball bearings and tapered roller bearings, in order to prevent shaft vibration and increase support rigidity, a certain axial force is often applied in advance during installation to press them against each other. However, the preload amount should not be too large, otherwise the bearing friction will increase, the temperature rise will increase, and the service life of the bearing will be affected.
Bearing alignment performance
When the center lines of the bearing seat and the shaft cannot be properly aligned due to manufacturing and installation errors, or when the shaft and seat holes are greatly deformed, bearings with good self-aligning performance should be used. Bearings with self-aligning capabilities are often selected for applications where misalignment is present, such as spherical ball bearings or spherical roller bearings. Mounted spherical bearings are suitable for compensating initial alignment errors caused by poor installation. The use of needle roller bearings and roller bearings with axis tilt should be avoided as much as possible. Misalignment can be caused by a variety of reasons, including loading, shaft and housing inaccuracies, and installation errors. While some bearings can tolerate misalignment, others can be damaged by it, leading to premature bearing failure. Therefore, it is important to consider the degree of misalignment in the application before selecting a bearing.
Operating noise
In certain operating environments, low operating noise may be important. Most rolling bearings produce very little operating noise. However, some electric motors and measuring instruments may require further reduction of noise levels during operation. Deep groove ball bearings are often the bearing choice where low noise levels are critical. Bearings such as cylindrical roller bearings can also be adjusted to further reduce noise levels during operation.
Operating environment
Different industrial environments will have different operating environments for each application. Before making a selection, it is critical to understand the operating conditions of the bearing. This includes contamination, temperature, shock and vibration. Some bearings feature corrosion-resistant or food-safe certified materials, making them ideal for industries such as chemical, food and pharmaceutical. Other products are designed to operate at high temperatures or withstand heavy shock loads and high levels of vibration. Understanding the operating environment of your machine will help you select the right bearings for your application, as well as the most appropriate sealing solutions and lubricants to support it. This will give your bearings the best chance of achieving a long service life, minimizing downtime and optimizing productivity.
Axial movement
When the bearing is required to move and shift in the axial direction, a cylindrical roller bearing (NU type or N type) or a needle roller bearing without ribs in the inner ring or outer ring can be used. At this time, the inner ring and the shaft or outer ring It can be installed with interference fit between it and the shell. If non-separable bearings such as deep groove ball bearings and spherical roller bearings are used, clearance fit must be used between the inner ring or outer ring and its mating parts to allow sufficient freedom of axial movement. For small axial movement, all types of bearings can be guaranteed by their own clearance.
Bearing installation
Engineers use the correct mounting tools to install the bearings onto the shaft. How you install and remove bearings will depend on the type of bearing, your operating environment and your personal preference. However, it may also be affected by available space. Removable bearings are generally easier to install and remove. This typically includes cylindrical roller bearings, tapered roller bearings and needle roller bearings. These bearings are ideal for applications that require periodic inspection. The installation of tapered bore bearings is difficult because the internal clearance needs to be adjusted during installation. Split bearings may be a good choice for applications that require regular inspection or maintenance, or where the bearings are surrounded by heavy machinery. These bearings are easy to install and do not require disassembly of surrounding equipment.
Clean lubricant flow over deep groove ball bearings Lubricant selection is critical to reliable, efficient bearing performance. Lubricants help reduce friction, thereby reducing wear and extending bearing life. Therefore, lubricant selection must be considered when specifying bearings. Choosing the right lubricant is just as important as choosing the right bearing. The lubricant you choose will depend on the bearing’s operating conditions, including load, speed, temperature and contamination.
There is no point in choosing the best bearing for your application without considering the sealing solution you will use. Always choose high-quality seals, which will protect the bearings from contamination and keep the bearings and their lubricants clean. This will give your bearings the best chance of achieving their optimal service life. When you consider the sealing solution required for a bearing, you need to consider the type of bearing, the contaminants it will be exposed to, the operating temperatures it will be exposed to, and the type of lubricant that will be used and the forces exerted on the seal. Consider the sealing solutions you need when selecting bearings to ensure they are compatible and work together effectively.
Other factors
When selecting bearings type, you should also decide whether to use bearings with stop grooves, seals, dust covers, low-noise bearings, etc. as needed, and consider the price and market supply of the bearings.
Help selecting bearings
Bearing selection is an important part of the application design process. Choose the wrong bearing and your performance will suffer, potentially leading to premature bearing failure and machine failure. If you’re not sure when to choose the right bearing for your application, it’s best to consult a bearing expert. After all, they are experts in bearings.
Aubearing can help you specify the right product for your application requirements. Our experts will take the time to understand your business to ensure you select the best bearings for your machinery.