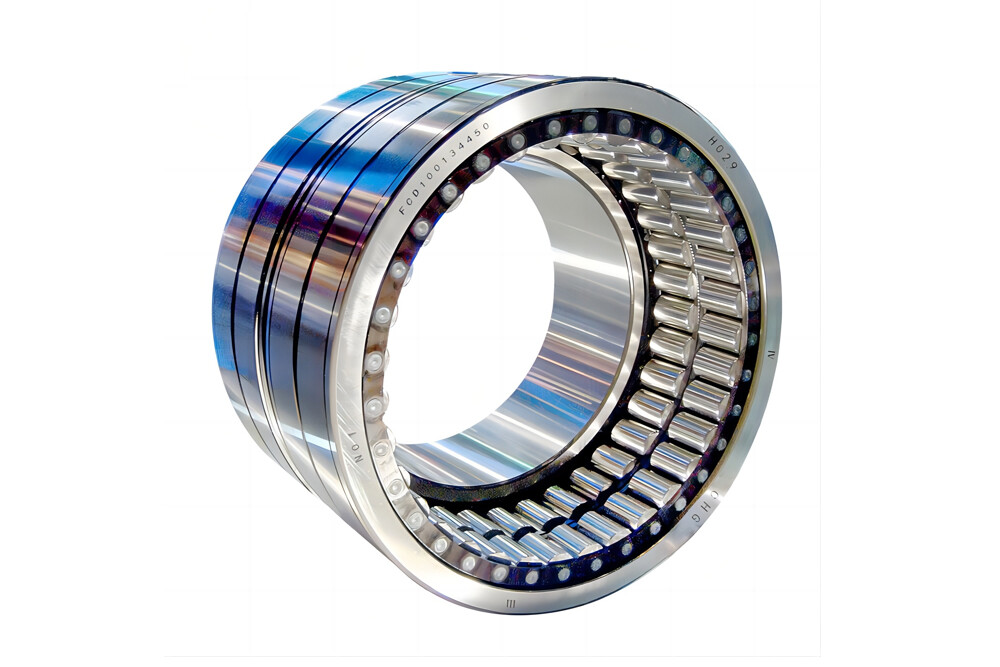
Bearing Manufacturer & Supplier
Specialize in ball bearings, roller bearings, thrust bearings, thin section bearings etc.
The Ultimate Guide to Rolling Mill Bearings
The most typical bearing among rolling mill bearings is the roll bearing. Roller bearings are important components used to support the rollers and maintain their correct position in the frame. The friction coefficient of the bearing is related to rolling energy consumption; the service life of the bearing is related to the utilization rate of the rolling mill; the stiffness of the bearing has an impact on the dimensional accuracy of the rolled products. Therefore, steel rolling production requires roll bearings to have a small friction coefficient, sufficient strength and a certain stiffness. In modern rolling mills, the structure of the roll bearings also needs to facilitate quick roll change operations. Typical four-row cylindrical roller bearings carry radial loads. Thrust roller or thrust ball bearings and radial angular contact ball or radial roller bearings bear axial load. Most rolling mill bearings use oil-air lubrication or oil mist lubrication and grease for lubrication and cooling.
Table of Contents
ToggleClassification of rolling mill bearings
Spherical roller bearings
The rolling mill bearing configuration mainly uses two sets of spherical roller bearings installed side by side on the same roll neck. This configuration basically met the production conditions at that time, and the rolling speed could reach 600rpm. However, as the speed increases, its shortcomings become and prominent: short bearing life, large consumption, low precision of finished products, serious wear of the roll neck, large axial movement of the roll, etc.
Four-row cylindrical roller bearing + thrust bearing
Cylindrical roller bearings adopt a tight fit between the inner diameter and the roll neck to withstand radial force. They have the advantages of large load capacity, high limit speed, high precision, separable and interchangeable inner and outer rings, easy processing, low production cost, and convenient installation and disassembly. ; The thrust bearing bears the axial force, and the specific structural type can be selected according to the characteristics of the rolling mill.
Under heavy load and low speed, thrust roller bearings are equipped to bear the thrust load with small axial clearance. When the rolling speed is high, equipped with angular contact ball bearings, not only the limit speed is high, but the axial clearance can be strictly controlled during operation. The rollers are tightly guided in the axial direction and can withstand general axial load forces. This type of bearing configuration not only has long bearing life and high reliability, but also has many advantages such as high precision of rolled products and easy control. Therefore, it is currently the most widely used and is mostly used in wire rod mills, plate mills, foil mills, and double support rolls. Support rolls for cold rolling mills and hot rolling mills, etc.
The tapered roller bearing can bear both radial force and axial force. There is no need to configure a thrust bearing, so the main engine is compact. The inner diameter of the tapered roller bearing and the roll neck adopt a loose fit, which is very convenient to install and disassemble. However, sometimes the loose fit may cause sliding creep, so the inner diameter is often machined with a spiral oil groove. This configuration type is still widely used, such as the work rolls of four-high hot rolling mills and cold rolling mills, blanking machines, steel beam rolling mills, etc.
Four-row cylindrical roller bearings and six-row cylindrical roller bearings are almost exclusively used in the roll necks, drums and rolling presses of rolling stands. These bearings have low friction compared to other roller bearings. Because these bearings are typically mounted with an interference fit on the roll neck, they are particularly suitable for rolling mill applications where rolling speeds are high. The low cross-section of these bearings allows the use of relatively large roll neck diameters compared to the roll diameter. Due to the large number of rollers that can be installed, the radial load capacity is very high.
Multi-row cylindrical roller bearings can only bear radial loads. Therefore, these bearings are mounted together with deep groove ball bearings or angular contact ball bearings, or tapered roller bearings of radial or thrust design, which carry the axial load. Four-row and six-row tapered roller bearings are of separate design, that is, the bearing ring with integral flange and the roller and cage assembly can be installed separately from the separate bearing ring, or all bearing components can be installed separately.
This considerably simplifies bearing installation, maintenance and inspection. The bearing can withstand a certain limit of axial displacement of the shaft relative to the bearing seat. Four-row cylindrical roller bearings have a cylindrical bore, and some sizes of bearings are also available with tapered bores. Bearings with tapered bores can be adjusted during installation to obtain a certain radial internal clearance or a defined preload.
Lubrication of rolling mill bearings
In principle, the lubrication of roller bearings is basically the same as the lubrication of other rolling bearings, except that the working conditions of roller bearings are relatively harsh, and whether their working performance can be effectively exerted depends to a large extent on the lubrication of the bearings. The main lubrication methods used in roll bearings include grease lubrication and oil lubrication.
(1) The grease of grease lubrication also has a sealing effect. The sealing structure and lubrication facilities are simple, and it is convenient to replenish grease. Therefore, as long as the working conditions permit, roll bearings are generally lubricated with grease. Oil lubrication has a strong cooling effect and can remove dirt and moisture from the bearing. The lubrication methods for roller bearings using oil lubrication include pressure oil lubrication, oil spray lubrication, oil mist lubrication and oil-air lubrication.
(2) Pressure oil supply lubrication is the most effective lubrication method for roll bearings under normal speed. Oil injection lubrication is to spray lubricating oil into the inside of the bearing through an oil injection nozzle installed on one side of the bearing at a certain pressure for lubrication. It is generally used in high-speed roller bearings or in situations where pressure oil supply lubrication cannot meet the cooling requirements.
(3) Spray lubrication is to spray dry compressed air containing oil mist into the inside of the bearing for lubrication. The amount of oil used is small. Due to the action of the air, the cooling effect is extremely strong. It is mainly used for large-scale rolling machines with high rolling speed and high rolling precision. Roller bearings, or for roller bearings that are not frequently disassembled in the bearing housing. Both pressure oil supply lubrication and oil injection lubrication require the installation of oil inlet and outlet pipes, lubrication pumps, oil reservoirs, and sometimes lubricating oil coolers. Therefore, the cost is relatively high, and generally roller bearings are rarely used.
Reasons affecting the service life of rolling mill bearings
Rolling mill bearings are important components of the rolling mill. During the operation of the rolling mill, the bearings support the rolls and bear the rolling force of the rolls while maintaining the correct position of the rolls. Whether the quality and life of the rolling mill bearings are reliable directly affects the reliability of the rolling mill operation. sex. There are many factors that affect the service life of rolling mill bearings. A series of internal and external factors such as bearing material, structural design, manufacturing accuracy, installation and sealing, lubrication, and cooling will all have an impact on the service life of rolling mill bearings. Harsh working conditions are the main cause of early failure of rolling mill bearings. Generally speaking, the working conditions of bearings mainly include load and distribution, lubrication, sealing, speed transmission, operating temperature, heat dissipation conditions, etc., bearing quality and use. If the parts are the same, but the working conditions are different, there will be a big gap in their service life.
The influence of carbides on bearing life
After quenching and low-temperature tempering, the structure of high-carbon bearing steel will change into undissolved carbides, acicular martensite and retained austenite. The content of undissolved carbides, carbide morphology distribution, and acicular martensite size and retained austenite will affect the apparent properties of the bearing. The lower the content of undissolved carbides in the bearing steel, the higher the hardness of the bearing steel. The reason is that the less the content of undissolved carbides, the lower the carbon concentration of the martensite matrix. will increase and the hardness will be higher.
The small amount of undissolved carbides present in the quenched bearing steel helps to improve the wear resistance of the bearing and also helps to obtain fine-grained cryptomartensite, thereby improving the toughness and fatigue resistance of the bearing; carbonization The particle size of the material also has a great influence on the life of the bearing. The carbide particles of bearing steel are less than 0.6um, and its service life will be significantly improved. The size of carbide particles of high-quality bearing steel is much lower than that of ordinary bearing steel, and The distribution of carbide particles is also uniform and does not appear in a banded distribution; the network carbide distribution will affect the connection between the matrix grains, thereby reducing the fatigue resistance limit of the bearing. If the stress between the bearings exceeds the fatigue limit, cracks will gradually occur and the bearing life will be shortened.
The characteristics of bainitic structure will increase the proportion limit, bending strength, yield strength and section shrinkage of carbon-chromium bearing steel, improve the toughness of bearing steel, and enhance the bearing’s ability to withstand impact force, fracture force, and friction. It also has Contributes to good maintenance of bearing dimensions.
Effect of loading conditions on bearing life
The bearings used in rolling mills mainly include the following types: multi-row cylindrical roller bearings, four-row tapered bearings and double-row spherical roller bearings. Without considering the quality of the bearing itself, the service life of the bearing used under working conditions is mainly determined by the bearing. Determined by the load received.
As the rolling force of the line rolling mill continues to increase, only multi-row bearings can be used in the roll neck. The concept of multi-row bearing design is to rely on multiple rows of rolling elements to uniformly carry the load and thereby enhance the bearing capacity. However, in the actual use of the rolling mill, the load-bearing of the multi-row rolling elements cannot be completely uniform and may even have large deviations. The main factors causing the deviation include the deviation from the design and manufacturing of the bearing itself, the installation accuracy of the bearing seat and the wear of rolling mill components. At the same time, the bearing load distribution is also affected by the rolling force, axial force and roll bending force.
This will inevitably cause the load borne by each row of rolling elements to deform under the condition that the equivalent load borne by the bearing as a whole remains unchanged, eventually leading to eccentric load. Once the eccentric load is formed, it will continue to intensify with continued use until a certain row The amount of load endured by the rolling element exceeds the ultimate load-bearing capacity of the rolling element, resulting in local overload rupture.
Unbalanced load is a situation that seriously affects the life of the bearing. In addition to the unbalanced load distribution of each row of rollers analyzed above, it can also cause a single row of rollers to tilt, causing stress to be concentrated locally, leading to rolling element sliding. Once the rolling conditions change, contact slippage will occur between the bearing rolling elements and the inner and outer rings, causing the bearing to heat up and be damaged.
The impact of lubrication quality on bearing life
Bearings can be used reliably for a long time without the guarantee of lubrication quality. Rolling mill bearings are subject to friction from many aspects during normal operation. Among them, the load area of the outer ring raceway is the most serious part of internal friction. There will definitely be a radial oil gap during the operation of the bearing, and the rolling of the rollers will only occur in the load area. In this way, the non-load area will be in a semi-rolling and semi-sliding state. When the roller enters the load area from the non-load area, the rotation speed will suddenly increase. During the sudden increase in rotation speed, the roller and the raceway will rub violently, and at the same time, they will also bear the impact load from the steel rolling process.
In this case, if the bearing is poorly lubricated, the roughness of the surface of the parts will continue to increase, which will lead to a gradual increase in wear. The pressure on the surface of the roller unit is also increasing. At the same time, during the operation of the bearing, sliding friction occurs between the running rolling element and the raceway, the running rolling element and the cage, the cage and the inner and outer rings, and this sliding friction will increase as the load increases. The existence of sliding friction will cause relative crawling between the bearing components. In order to reduce the wear caused by the relative crawling of the bearing components, it is necessary to maintain good lubrication between the bearing components. The lubricating oil film can well isolate the contact surfaces between components and avoid direct frictional contact between metal and metal. At the same time, good lubrication also plays a good role in heat dissipation and can reduce the transmission of friction heat during operation.
Due to the harsh operating environment of rolling mill bearings, the probability of contamination of the bearings during operation will increase. Therefore, the bearings must be well sealed to avoid contamination of the grease. Usually, the bearings used in steel rolling equipment are mainly contaminated by production cooling water and iron oxide scale. After the grease is contaminated by water, the fatigue resistance of the bearing material will be reduced and cracks will occur. If the grease is contaminated by iron oxide scale, the situation will be even worse. The iron oxide scale will destroy the lubrication conditions inside the bearing, and friction and particle wear will occur on the bearing surface.
For bearings contaminated by cooling water and iron oxide scale, the rings will continue to deteriorate during use. As the contaminants increase, the rings will eventually crack and the bearings will be damaged. Therefore, an ideal bearing seal can effectively improve the bearing’s durability. service life, and also reduces the probability of sudden bearing damage affecting production.