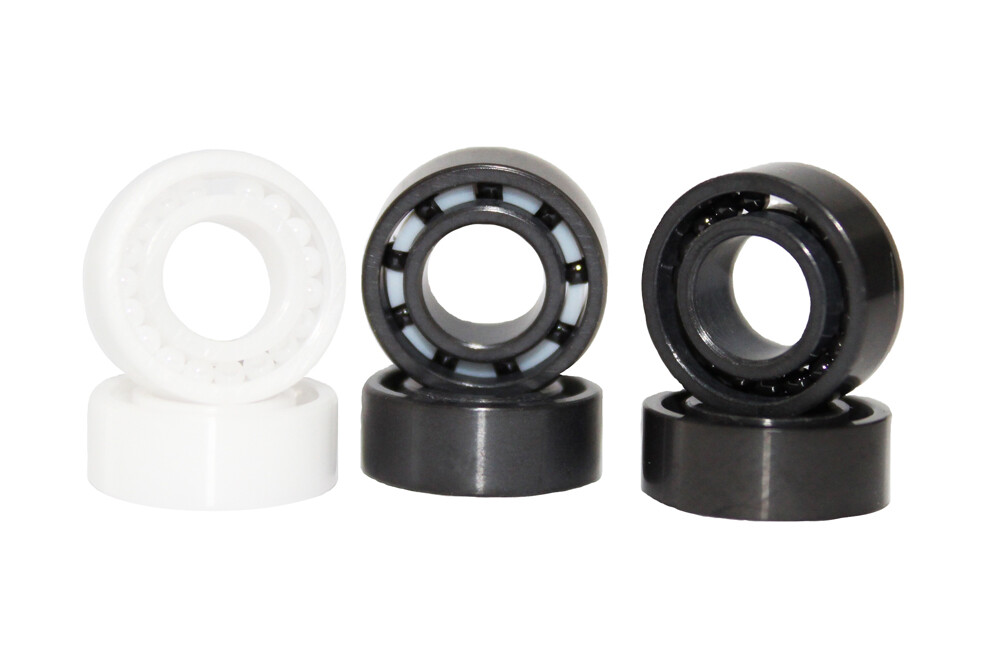
Bearing Manufacturer & Supplier
Specialize in ball bearings, roller bearings, thrust bearings, thin section bearings etc.
The Ultimate Guide to Maintaining Ceramic Bearings
In recent years, ceramic bearings, as an upgraded version of metal bearings, have become very popular components for various types of machinery and have been widely used in various fields. Even in extremely special environments, ceramic bearings can bring out their excellent performance. Ceramic bearings are high-speed bearings. During their use, they should be used regularly and maintained regularly according to their performance characteristics, in order to improve work efficiency and extend the service life of ceramic bearings. This guide will comprehensively describe some considerations for maintaining ceramic bearings.
Table of Contents
ToggleCharacteristics and performance of ceramic bearings
Advantages of ceramic bearings
Today, ceramic bearings have been standardized and widely used in general applications. It has the following advantages:
(1). Small friction coefficient. The friction coefficient of ceramic bearings is relatively small, so the transmission efficiency is also higher. The friction coefficient of traditional bearings is between 0. 08-0. 12, while the friction coefficient of ceramic bearings is only 0. 001-0. 005. Therefore, during its use, it has higher performance and is convenient to maintain.
(2) The manufacturing cost is within a reasonable range. Compared with non-ferrous metals, the manufacturing cost of ceramic bearings is relatively high, but after heat treatment, it has higher mechanical properties and a longer service life.
(3) High precision. The internal structure of ceramic bearings and the clearance between parts are very small, and the processing precision of its parts is relatively high. Especially for some precision machinery, it also has a better effect in terms of operating accuracy. It can not only achieve higher transmission efficiency, but also reduce Lubricating oil consumption is also relatively simple and convenient in installation and maintenance.
(4) Bear high load. In practical applications, ceramic bearings can be preloaded with radial loads to greatly improve the rigidity of the bearings, and can even withstand the combined effects of radial loads and axial transmission loads under various conditions at the same time.
(5) Rust-proof and corrosion-resistant. Various types of cermets will corrode to varying degrees when exposed to a certain pH environment, but ceramic bearings can operate normally in harsh environments full of corrosive media.
Disadvantages of ceramic bearings
Although ceramic bearings have many advantages over traditional metal bearings, they are not perfect bearings.
(1) Under the same volume, the composite bearing capacity of ceramic bearings is smaller than that of sliding bearings. In order to meet its use requirements, the radial size of ceramic bearings must be increased;
(2) Ceramic bearings will produce greater vibration and noise during use, so they are difficult to be used in occasions with high precision and high vibration requirements.
(3) Ceramic bearings are also very sensitive to foreign objects. Once foreign objects enter during operation, they will continuously produce large vibrations and noises, which will not only affect work efficiency, but also easily cause early damage.
Performance of ceramic bearings
Bearings were usually made of alloy bearing steel in the past, but its disadvantages gradually became apparent with the expansion of applications. Ceramic bearings are made of non-metallic materials. Silicon nitride (Si N) is generally used as the main material. According to relevant data, it has amazing high temperature resistance and can still maintain good strength even at a high temperature of 1400 °C. , which cannot be achieved by many metals, and its stability is stronger and its comprehensive performance is also strong.
Bearings are composed of three parts: inner ring, outer ring and rolling elements. Today’s ceramic bearings can be divided into full ceramic bearings and hybrid ceramic bearings according to different materials. As the name suggests, all-ceramic bearings have rolling elements and inner and outer rings made of ceramic materials. All-ceramic bearings are resistant to corrosion, high temperature and wear, so they can be used in harsh environments. It can still show unique advantages and is widely used in aerospace vehicles and medical and health care. Hybrid ceramic bearings are generally used in highly precise machine tool spindles because they have a certain degree of lubricity that can effectively prevent sticking and burning due to oil film destruction, so they can still maintain good stress even under high-speed operation.
Precautions for using ceramic bearings
Installation of ceramic bearings
Ceramic bearings themselves are relatively expensive, so they should be installed carefully and patiently to avoid improper installation that affects later use and maintenance, and once the product is damaged due to installation, the gain outweighs the loss.
Before installing ceramic bearings, the specifications should be selected according to the needs of the installation site, rather than making random judgments with the naked eye. The correct specification selection will make the installation easier and the stability of use will be higher. Once the specifications are selected, Not only is it laborious to install, but it is also difficult to achieve the desired effect. During the installation process of ceramic bearings, uniform pressure should be applied to the circumference of the bearing end face to determine the installation direction and installation position.
Remember, it is strictly prohibited to use axes, hammers and other heavy objects to hit the bearing during the installation process, because the knocking process will cause damage to the bearing end face, and once the pressure is used improperly during the installation process, it will cause certain indentations and scratches. In this way, during the later high-speed operation, the wear rate of the bearing will also increase accordingly.
Cooperation of ceramic bearings
The matching selection of ceramic bearings must be based on the load direction and load properties. Generally speaking, the load capacity of each ferrule is different, which is usually divided into rotating load, static load and indefinite load. For rotating composites and indeterminate composites, the ferrules should adopt a static fit; for static loads, a combination of overfit and dynamic fit can be used.
Disassembly of ceramic bearings
No matter what kind of mechanical equipment component it is, its life can be extended through correct use and maintenance. The same goes for ceramic bearings. After a period of use, many users hope to perform further maintenance through disassembly, but they also need to pay attention during the disassembly process. Never use sharp instruments to directly knock and disassemble, but apply even pressure to the disassembly. Use force and skill to disassemble.
Ceramic bearings are generally divided into two types: those with tapered inner sleeves and those without tapers. The disassembly methods of these two ceramic bearings should be treated differently. Remember, only reasonable disassembly will not cause damage to the bearings and the instrument itself. Once forced disassembly is carried out, it is likely that the effect of the later replacement product will be unstable, which will increase the cost of use.
Maintenance of ceramic bearings
Detection of ceramic bearings
Ceramic bearings have strong regularity during use, and their repeatability is also very good. Therefore, as long as you observe it closely, you can detect problems in time and achieve good maintenance. The content and matters of its detection mainly include the vibration and noise of the bearing, the temperature of the bearing operation, the state of the lubricating oil, etc. Only by paying attention to observation and regular inspection during its use can problems be nipped in the bud.
Cleaning of ceramic bearings
The cleaning of ceramic bearings mainly involves cleaning the powder and heavy metal mixtures produced during their use, because these mixtures will adhere to the rolling elements and inner rings of the bearings, thus affecting the normal operation of the bearings. During use, if it is not thoroughly cleaned, it is easy to cause scratches on the working surface of the parts, and these attachments are also one of the causes of noise and vibration during the operation of ceramic bearings.
Before cleaning ceramic bearings, the grease must be well tested. The key requirement is how to control the amount of grease retained. Based on this, we can accurately determine whether to refuel and the effectiveness and dosage of replenishment. Secondly, attention should also be paid to the physical changes of oil. Based on this, we can accurately judge the replacement cycle of various oils and make appropriate adjustments to the oil replenishment methods and systems. Once it is found that the oil has dryness, Hardening, caking or discoloration means that various greases need to be replaced;
In addition, regular testing of ceramic bearings is also very necessary, because the testing process can determine the degree of grease contamination and determine whether the current lubricating grease is suitable for the existing working conditions, so that the grease type can be replaced according to the actual situation. Or maintenance of ceramic bearings.
Generally speaking, the cleaning agent for ceramic bearings can be gasoline or metal cleaning agent. The cleaning process is also divided into two types: coarse cleaning and fine cleaning. Remember, during the cleaning process, the shaft ceramic bearing must be placed in the corresponding container and covered with a metal mesh pad to avoid contact with dirt in the container. Because once the dirt is rotated during the cleaning process, the ceramic bearings will be damaged. During the cleaning process, you can use a brush to remove grease and corresponding adhesives. After it is roughly clean, move to fine cleaning. During the cleaning process, handle it with care and do not turn it randomly to prevent damage to the ceramic bearings due to the intervention of external forces. Last but not least, we must pay attention to the dehydration and anti-rust treatment after ceramic cleaning.
Lubrication of ceramic bearings
Ceramic bearings themselves have a certain degree of lubrication, so there is no need to use additional lubricating oil during their actual use. However, if friction occurs between the micro-welding of the ceramic bearings and metal rolling elements or especially the surface of the raceway, To function, certain lubrication measures must be taken for it. Once the ceramic bearing is actually used for too long, its flexibility will inevitably be affected. It is also necessary to add lubricating oil to reduce wear and scrap rate. Because during the long-term operation of ceramic bearings, a certain amount of fine powder will be produced, and appropriate lubricating oil can take away some of the powder and form a protective oil film to prevent static friction.
Generally speaking, the lubrication of ceramic bearings is divided into two types: grease lubrication and oil lubrication. Therefore, when choosing, you should choose according to its applicable conditions and purpose of use, so as to promote its better performance.
Avoid overload operation of ceramic bearings
Any machinery has a service life, and the same goes for ceramic bearings. If overload or improper maintenance occurs during actual use, the ceramic bearings may be affected accordingly. Relevant surveys show that 34% of the causes of premature overload operation failure of ceramic bearings are caused by fatigue. Ceramic bearings may naturally issue an early warning when overloaded. Therefore, during the use of ceramics, the time should be adjusted appropriately in combination with the use load to avoid overload operation and affect the life of the ceramics.
In addition, during the use of ceramic bearings, cracks and rust are also very common. These situations may seem inconspicuous, but they will also shorten the service life of ceramic bearings. Therefore, the best maintenance method is to prevent them. In the future, not only should the installation and use be carried out in the correct way, but also the maintenance work should be paid attention to.
Both metal bearings and ceramic bearings have their irreplaceable advantages and are relatively successful in their respective development fields. However, the advantages of ceramic bearings are now prominent. They have been used in many cutting-edge fields, and their application atmosphere and mechanical support are also extensive. However, in order to realize other advantages of ceramic bearings and extend their service life, it is necessary to carry out regular inspections, cleaning and lubrication according to their performance characteristics, and to realize their use value through correct use and maintenance.