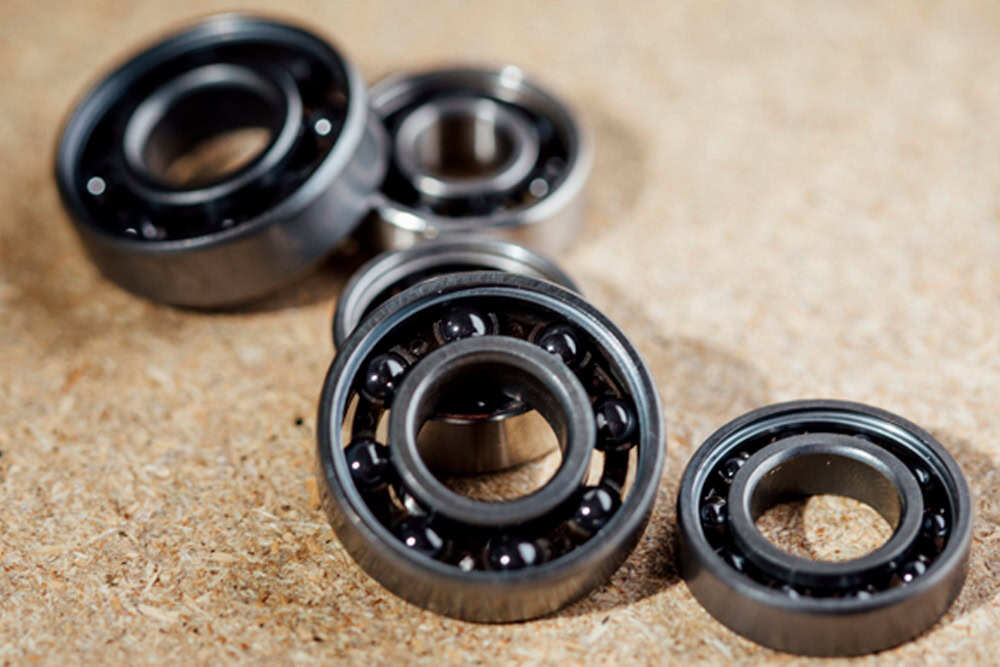
Bearing Manufacturer & Supplier
Specialize in ball bearings, roller bearings, thrust bearings, thin section bearings etc.
The Ultimate Guide to Ceramic Bearing Materials
Ceramic materials are widely used in many fields due to their unique properties such as high strength, high hardness, wear resistance, and high temperature stability. For example, studies have shown that full-ceramic bearings perform better in water than any stainless steel. Commonly used ceramic bearing materials include silicon nitride (Si3N4), zirconium oxide (ZrO2), aluminum oxide (Al2O3) or silicon carbide (SiC). The best ceramic materials for water-polluted environments are silicon nitride and zirconium oxide, which have a service life 70 times longer than stainless steel bearings. This blog aims to explore the classification and specifications of ceramic bearing materials, ceramic bearing manufacturing processes, and provide constructive suggestions for your comprehensive understanding of ceramic bearings.
Table of Contents
ToggleAlumina ceramics (Al2O3)
The main component of alumina ceramics is Al2O3, which generally contains than 45%. Alumina ceramics have various excellent properties such as high temperature resistance, corrosion resistance, high strength, high hardness, and good dielectric properties, which are 2 to 3 times that of ordinary ceramics. However, the disadvantage of alumina ceramics is that they are fragile and cannot accept sudden changes in ambient temperature. Alumina can be divided into different series according to the Al2O3 content and the additives used. For example, alumina can be divided into 75% alumina, 85% alumina, 95% alumina, 99% alumina, etc.
Material | Alumina | ||||
Property | Unit | AL997 | AL995 | AL99 | AL95 |
% Alumina | – | 99.70% | 99.50% | 99.00% | 95.00% |
Color | – | Ivory | Ivory | Ivory | Ivory and White |
Permeability | – | Airtight | Airtight | Airtight | Airtight |
Density | g/cm³ | 3.94 | 3.9 | 3.8 | 3.75 |
Straightness | – | 1‰ | 1‰ | 1‰ | 1‰ |
Hardness | Mohs Scale | 9 | 9 | 9 | 8.8 |
Water Absorption | – | ≤0.2 | ≤0.2 | ≤0.2 | ≤0.2 |
Bending Strength (Typical at 20°C) | MPa | 375 | 370 | 340 | 304 |
Compressive Strength (Typical at 20°C) | MPa | 2300 | 2300 | 2210 | 1910 |
Thermal Expansion Coefficient (25°C to 800°C) | 0-6/°C | 7.6 | 7.6 | 7.6 | 7.6 |
Dielectric Strength (5mm thickness) | AC kV/mm | 10 | 10 | 10 | 10 |
Dielectric Loss (25°C @ 1MHz) | – | <0.0001 | <0.0001 | 0.0006 | 0.0004 |
Dielectric Constant (25°C @ 1MHz) | – | 9.8 | 9.7 | 9.5 | 9.2 |
Volume Resistivity (20°C @ 300°C) | Ω·cm³ | >10^14 2*10^12 | >10^14 2*10^12 | >10^14 4*10^11 | >10^14 2*10^11 |
Long-term Working Temperature | °C | 1700 | 1650 | 1600 | 1400 |
Thermal Conductivity (25°C) | W/m·K | 35 | 35 | 34 | 20 |
Alumina is an excellent electrical insulator that can resist extremely high currents. Its resistance to electricity increases with its purity. The higher the purity of alumina, the higher its resistance. It is well known that alumina also has a very high melting point and strong mechanical strength. The melting point of ordinary Al2O3 products is very high, at 2072°C. However, when the temperature exceeds 1000 degrees Celsius, its mechanical strength decreases. Due to the huge difference in its thermal expansion coefficient, its resistance to thermal shock is poor when exposed to very high temperatures.
The excellent chemical stability of alumina is the main factor in its high corrosion resistance. Alumina is also slightly soluble in strong acids (such as hot sulfuric acid and hot HCl, HF also has a certain corrosive effect) and alkaline solutions, but is insoluble in water. Pure alumina can resist chemical corrosion, making pure alumina the main material of choice for a variety of industrial parts. Alumina ceramic materials also have very low vapor pressure and decomposition pressure. These properties of alumina ceramics make it one of the most widely used ceramics in structural, wear and corrosion environments.
Alumina ceramics are usually made from bauxite and can be molded using injection molding, compression molding, isostatic pressing, slip casting, diamond machining and extrusion. Like aluminum nitride, alumina can also be produced by dry pressing and sintering or by hot pressing with appropriate sintering aids. Due to its excellent chemical stability, alumina ceramics are widely used in bearings, acid-resistant pump impellers, pump bodies, acid pipeline linings and valves. Due to its extremely high hardness and wear resistance, alumina ceramics are also often used to manufacture textile wear-resistant parts and cutting tools.
Ceramic Materials – Sorted by Density
Zirconia > 99% Alumina > 94% Alumina > 85% Alumina > Aluminum Nitride > Silicon Carbide > Mullite > Macor© > Cordierite
Ceramic Materials – Sorted by Hardness
Silicon Carbide > 99% Alumina > YTZP Zirconia > Silicon Nitride > TTZ Zirconia > 94% Alumina > 85% Alumina > Mullite > Cordierite > Macor©
When the alumina content is higher than 95%, it can be used as an excellent electrical insulator. It also has low dielectric loss and is widely used in the fields of electronics and electrical appliances. In addition, transparent alumina has good transmittance to visible light and infrared rays and can be used to make high-pressure sodium lamps and infrared detection window materials. In addition, alumina ceramics have excellent biocompatibility (similar to titanium alloys), high strength, and high wear resistance. Therefore, they are also ideal materials for preparing artificial bones and artificial joints.
Zirconia (ZrO2)
Zirconium ceramics have low thermal conductivity (insulates) and high strength. They were first used in space travel in the 1960s to form a thermal barrier that allowed the space shuttle to enter the Earth’s atmosphere. They also handle high temperatures well, with operating temperatures for zirconia ceramics ranging from -85°C to 400°C. However, they are not as resistant to thermal shock as silicon nitride.
Zirconia has a strong corrosion resistance, which makes it a perfect choice for highly corrosive liquids. Zirconia ceramics have a very high resistance to crack growth, making them ideal for welding processes and wire forming tools. It also makes them very suitable for mechanical applications involving the risk of fracture. They also have very high thermal expansion, with a thermal expansion coefficient similar to that of steel, making them the material of choice for joining ceramics and steel. Based on its tribological properties, zirconium oxide is very suitable for rolling motion, such as linear bearings or ball bearings (such as the manufacturer TK linear). In addition, zirconium oxide and silicon nitride ceramics have the advantages of high vacuum compatibility, non-magnetic, non-conductive, high and low temperature resistance, chemical resistance, high rigidity, and long life. Zirconium oxide and silicon nitride can be made into bearings after dry running.
Compared with aluminum oxide, zirconium oxide has high mechanical properties, high strength and high toughness. If strength is the only requirement, this material is recommended. In addition, zirconium oxide (ZrO2) is a ceramic known in the health field for its biocompatibility, bioinertness, high mechanical properties and chemical stability. In the dental industry, zirconium oxide ceramics are used to manufacture various dental restoration products. For example, opaque or translucent zirconia blanks are used to make bridges, crowns, and veneers. Hot isostatically pressed zirconia is used to make dental implants and abutments. One of the main advantages of using zirconia for dental restorations is that the surface finish of the finished product closely resembles that of natural teeth. In addition, zirconia ceramics are translucent and shiny, which makes them suitable for applications where the appearance is similar to the surrounding tooth material.
Silicon carbide
Silicon carbide ceramics are mainly composed of SiC, which is a high-strength, high-hardness high-temperature ceramic. When used at high temperatures of 1200℃ to 1400℃, silicon carbide ceramics can still maintain a high bending strength and can be used for high-temperature components such as rocket tail nozzles, thermocouple sleeves, and furnace tubes. Silicon carbide ceramics also have good thermal conductivity, oxidation resistance, electrical conductivity, and high impact toughness. It is a strong and durable ceramic material that also has low density, low thermal expansion rate, and excellent thermal shock resistance, making it suitable for a variety of applications.
Composition | Silicon Carbide |
Molecular Weight | 40.1 |
Appearance | Black |
Melting Point | 2,730°C (4,946°F) (Decomposition) |
Density | 3.0 to 3.2 g/cm³ |
Electrical Resistivity | 1 to 4 x 10^5 Ω·m |
Porosity | 0.15 to 0.21 |
Specific Heat | 670 to 1180 J/kg·K |
Silicon carbide is produced by chemically combining carbon and silicon atoms. Silicon carbide particles have been used as an abrasive for many years, most commonly in the form of sandpaper. However, these particles can be bonded together through sintering to form a highly durable ceramic material that has excellent mechanical properties, which makes it an excellent choice for manufacturing bearings. Due to its high thermal and electrical conductivity, silicon carbide can be used as a static elimination component.
Nitride ceramics
Nitride ceramics are made of metal nitrides, such as silicon nitride and aluminum nitride. Silicon nitride ceramics (Si3N4) Si3N4 is the main component of silicon nitride ceramics, which is a high-strength, high-hardness, wear-resistant, corrosion-resistant, and self-lubricating high-temperature ceramic.
Property | Value |
Color | Gray and Dark Gray |
Density | 3.2 to 3.25 g/cm³ |
Hardness | HRA 92 to 94 |
Maximum Operating Temperature | 1300 to 1600°C |
Thermal Conductivity | 23 to 25 W/(m·K) |
Flexural Strength | ≥900 MPa |
Fracture Toughness | 6 to 8 MPa·m¹/² |
Thermal Expansion Coefficient | 2.95 to 3 x 10⁻⁶ /°C (0 to 1400°C) |
If you are looking for a material that can withstand high temperatures and harsh mechanical conditions, then silicon carbide is a good choice, although this material is relatively expensive. When it comes to withstanding high temperatures, silicon nitride is superior to metal solutions, and Si3N4 has an operating temperature range of -100°C to 900°C. In addition, the linear expansion coefficient of silicon nitride is the smallest among all types of ceramics. The thermal expansion coefficient of silicon nitride is 3.2 x 10-6/k, while the thermal expansion coefficient of silicon carbide is 3 x 10-6/k. The thermal expansion coefficients of zirconium oxide and aluminum oxide are 10.5 x 10-6/k and 8.5 x 10-6/k respectively, but both are much lower than bearing steel, which has a coefficient of 12.5 x 10-6/k.
Classification | Aluminum Oxide | Aluminum Oxide | Aluminum Oxide | Aluminum Oxide | Silicon Carbide | Silicon Carbide | Silicon Nitride | Mullite | Zirconium Oxide | Talc |
| KMA995 | KMG995 | KMA96 | KMA96 | KMG96 | KMG96 | Kai170 | Talc | KYCS | —- |
Main Component | 99.7 | 99.6 | 96 | 96 | 92 | 92 | 92 | 92 | 92 | 92 |
Color | Milky | White | White | White | White | Black | Black | Gray | White | Gray |
Bulk Density (g/cm³) | 3.9 | 3.9 | 3.7 | 3.7 | 6 | 3.1 | 3.2 | 2.7 | 3.5 | 2.7 |
Flexural Strength (MPa) | 400 | 390 | 320 | 320 | 1000 | 450 | 420 | 200 | 120 | 150 |
Young’s Modulus (GPa) | 380 | 370 | 340 | 340 | 410 | 350 | 310 | 210 | 130 | 170 |
Mechanical | Hardness (GPa) | 21 | 20 | 19 | 19 | 24 | 13 | 22 | 13 | 22 |
Poisson’s Ratio | – | 0.24 | 0.24 | 0.23 | 0.31 | – | – | – | – | – |
Fracture Toughness (MPa·m¹/²) | 4.1 | 4 | 3.5 | 3.5 | 4 | 4.6 | 6 | 2.5 | 4 | 3.2 |
Thermal Expansion Coefficient (×10⁻⁶/°C) | 6.4 | 5.8 | 5.7 | 5.7 | 7.7 | 11 | 3.2 | 2.5 | 2.5 | 3.0 |
Thermal | Thermal Conductivity (W/m·K) | 30 | 28 | 21 | 21 | 120 | 80 | 17 | 1.2 | 1.2 |
Specific Heat (J/g·K) | 0.78 | 0.78 | 0.78 | 0.78 | 1.4 | 1.2 | 1.2 | 1.2 | 1.2 | 1.2 |
Dielectric Constant (1 MHz) | 10.1 | 10.1 | 9.4 | 9.5 | 11 | 7 | 7 | 8.5 | 8.5 | 6.5 |
Dielectric Loss (×10⁻⁴) | 50 | 50 | 40 | 50 | 50 | 50 | 50 | 50 | 50 | 50 |
Volume Resistivity (Ω·cm) | 10¹⁵ | 10¹⁵ | 10¹⁴ | 10¹⁴ | 10¹² | 10¹² | 10¹² | 10¹³ | 10¹³ | 10¹³ |
Breakdown Voltage (kV/mm) | 10 | 10 | 10 | 10 | 11 | 11 | 11 | 10 | 10 | 10 |
Features | High Strength | High Strength | High Strength | High Strength | High Hardness | High Hardness | High Toughness | High Toughness | Low Thermal Conductivity | Low Thermal Conductivity |
| Insulating | Insulating | Insulating | Insulating | Conductive | Conductive | Insulating | Insulating | Light Weight | Light Weight |
Uses | Abrasive Material | Abrasive Material | Abrasive Material | Abrasive Material | Abrasive Material | Abrasive Material | Sealing Material | Sealing Material | Thermal Insulation | Thermal Insulation |
| Wear-resistant Parts | Wear-resistant Parts | Wear-resistant Parts | Wear-resistant Parts | High Temperature Resistance Parts | High Temperature Resistance Parts | Aerospace Parts | Aerospace Parts | Semiconducting Equipment Parts | Semiconducting Equipment Parts |
| High Temperature Parts | High Temperature Parts | High Temperature Parts | High Temperature Parts | Tool Parts | Tool Parts | Electrode Parts | Electrode Parts | Dental Implants | Dental Implants |
| Semiconductor Parts | Semiconductor Parts | Semiconductor Parts | Semiconductor Parts | – |
|
|
|
|
Item | Unit | Si₃N₄ | ZrO₂ | Al₂O₃ (99.5%) | SiC | Bearing Steel |
Density | g/cm³ | 3.23 | 6.05 | 3.92 | 3.12 | 7.85 |
Water Absorption | % | 0 | 0 | 0 | 0 | 0 |
Coefficient of Linear Thermal Expansion | 10⁻⁶/k | 3.2 | 10.5 | 8.5 | 3 | 12.5 |
Modulus of Elasticity (Young’s Mod.) | GPa | 300 | 210 | 340 | 440 | 208 |
Poisson’s Ratio | / | 0.26 | 0.3 | 0.22 | 0.17 | 0.3 |
Hardness (Hv) | MPa | 1500 | 1200 | 1650 | 2800 | 700 |
Flexural Strength (@ R.T.) | MPa | 720 | 950 | 310 | 390 | 520 (tensile strength) |
Flexural Strength (700°C) | MPa | 450 | 210 | 230 | 380 | / |
Compressive Strength (@ R.T.) | MPa | 2300 | 2000 | 1800 | 1800 | / |
Fracture Toughness, K₁c | MPa·m¹/² | 6.2 | 10 | 4.2 | 3.9 | 25 |
Thermal Conductivity (@ R.T.) | W/m·k | 25 | 2 | 26 | 120 | 40 |
Electrical Resistivity (@ R.T.) | Ω·mm²/m | >10¹³ | >10¹⁵ | >10¹⁶ | >10³ | 0.1~1 |
Max. Use Temperature (no loading) | °F | 1050 | 750 | 1500 | 1700 | 1700 |
Corrosion Resistance | / | Excellent | Excellent | Excellent | Excellent | Poor |
Silicon nitride has a thermal shock resistance of up to 600°C, while silicon carbide has a thermal shock resistance of only 400°C, indicating that the risk of fracture due to temperature changes is minimal. In environments with large temperature changes, when thermal shock resistance is a top priority, silicon nitride and silicon carbide are the best choices. In addition, silicon nitride has excellent corrosion resistance and can resist corrosion from various acids except hydrofluoric acid, as well as corrosion from alkalis and various metals. It has excellent electrical insulation and radiation resistance.
These properties of silicon nitride ceramics make it useful as high-temperature bearings, seals used in corrosive media, thermowells, metal cutting tools, etc. For example, the ball bearing industry has been using this material for decades because its performance has been proven and it is often used in rolling elements of ceramic bearings, such as balls and rollers. Its extremely high mechanical toughness and excellent heat resistance, corrosion resistance and wear resistance are the reasons why it is used in various high-load applications.
Ceramic bearing manufacturing process
1. Powder processing. Ceramic powder processing is very similar to metal powder processing. Ceramic powder processing involves producing powder by grinding, then making green products, and then consolidating them to obtain the final product. Powder is a collection of fine particles. Ceramic powder can be obtained by crushing, grinding, separating impurities, mixing, and drying the raw materials.
2. Mixing. The ceramic components are mixed together through various procedures and machines, and they are turned into slurry by adding water or other liquids.
3. Molding method. There are two main common ceramic bearing molding methods, namely injection molding and powder molding. Injection molding is to mix ceramic powder, organic binder, rheological agent, sub-micron powder, etc., and inject them into the mold for molding. Powder molding is to compress ceramic powder into a molded body and then sinter it. These two methods have their own advantages and disadvantages, and they should be selected according to specific engineering requirements.
4. Sintering process. During the production process of ceramic bearings, sintering treatment is required to solidify the molded body into a finished product, and at the same time, its hardness and strength can also be improved. The sintering process of ceramic bearings mainly includes oxide sintering and non-oxide sintering. According to the process flow, sintering is first carried out in an oxidizing atmosphere, and then sintering is carried out in a non-oxidizing atmosphere. During the entire sintering process, environmental parameters such as temperature, pressure, and atmosphere need to be controlled to achieve the desired effect.
5. Precision machining. The sintered ceramic bearings need to undergo subsequent precision machining, including grinding, polishing, and other steps to ensure their geometric accuracy and surface quality. At the same time, quality inspection is also required, including the detection and analysis of indicators such as hardness, density, dimensional deviation, and noise to ensure that the products meet international standards and customer requirements.
Factors affecting the quality of ceramic bearings
The quality and efficiency of ceramic bearing processing are affected by many factors, including material quality, molding method, sintering process, precision machining technology and equipment. In addition, it is also affected by environmental parameters such as temperature, pressure, speed, and atmosphere during the processing. In view of these factors, processing technicians need to select appropriate process flows, equipment, and tools to ensure processing quality. In the current application field of ceramic materials, ceramic bearings have become an indispensable core technology.