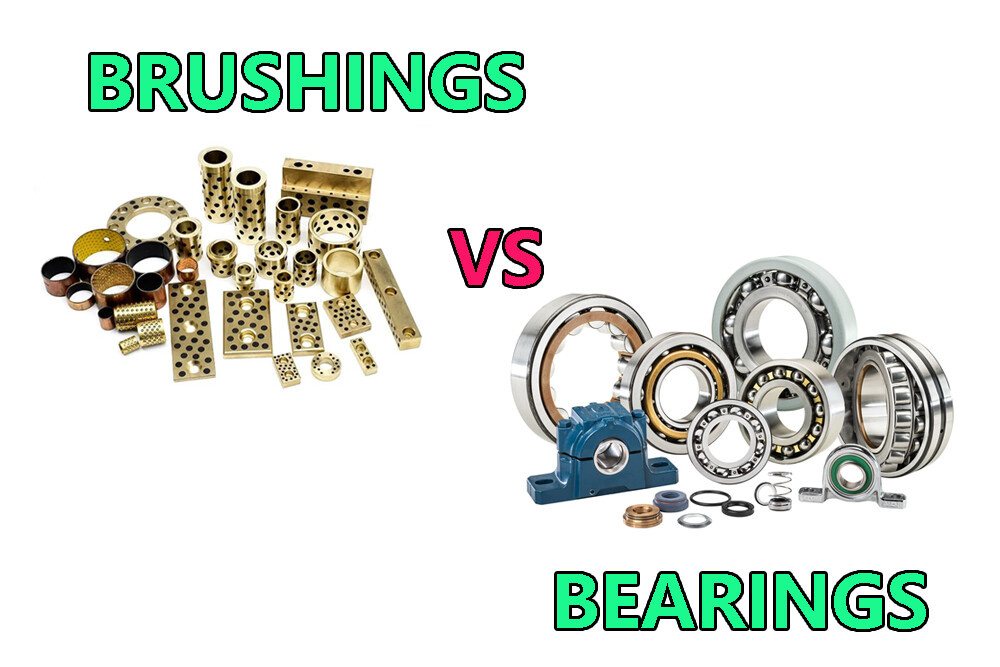
Bearing Manufacturer & Supplier
Specialize in ball bearings, roller bearings, thrust bearings, thin section bearings etc.
The Ultimate Guide to Bushings vs Bearings
In today’s world, almost all machines rely heavily on bushings and bearings, otherwise they will stop functioning. The main function of bushings vs bearings is to reduce the friction generated when two moving parts interact and reduce wear between components. Bushings vs Bearings help reduce noise, extend service life, reduce power consumption, maximize machine efficiency and speed applications. Bushings and bearings adapt to different operations and environments. Choosing Bushings vs Bearings? You need to understand the differences between the two, their advantages and disadvantages, and typical applications. Selecting the right type of bushing or bearing for your industrial application to meet certain requirements requires extensive knowledge. Let’s take a closer look at bushings and bearing assemblies, their main features and uses, and how the materials you use can have a huge impact on the final application.
Table of Contents
ToggleThe difference between bushings VS bearings
Essentially, there’s no real difference between bushings vs bearings: a bushing is also a type of bearing. Generally speaking, “bearings” facilitate movement between two components while reducing friction. A typical bearing is a simple design with two surfaces that roll against each other, allowing two mating parts to move without friction. They are broadly classified as radial bearings, thrust bearings and linear bearings, depending on whether they have rotary or linear motion. A “bushing” is a special design of bearings used in certain applications. To summarize: a bushing is a bearing, but a bearing is not always a bushing. Now that that’s clear, we’re going to take a closer look at the different types of bearings and how bushings differ from bearings.
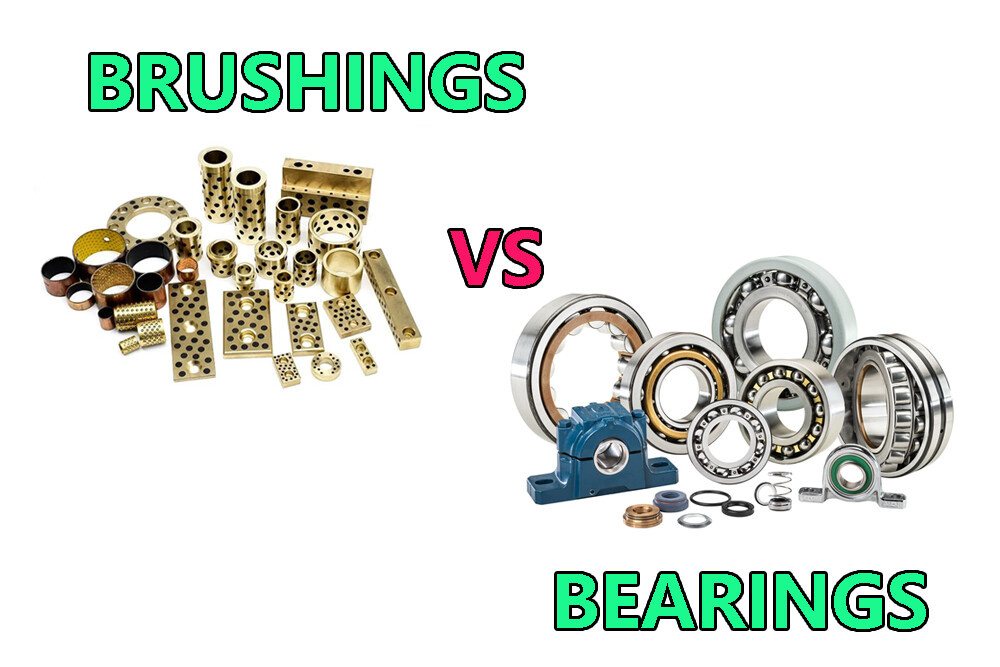
What are bearings?
Bearings are precision-made machine components that allow machines to move at extremely high speeds while reducing friction and handling stress between moving parts. It can also be said that when other parts move relative to each other on the shaft, it is used to reduce the friction coefficient during the transmission of motion force and to keep the center position of the rotating shaft fixed. Most bearings are used to support rotating shafts in machines. Bearings allow relative movement between machine parts while providing some type of position between them. The form of bearing that can be used depends on the nature of the relative motion required and the type of constraints that must be imposed on it. Its accuracy, performance, lifespan and reliability play a decisive role in the accuracy, performance, lifespan and reliability of the host machine.
Bearing type
Bearings can be divided into two major categories, journal bearings and thrust bearings.
Journal bearing: The load acts at right angles to the shaft.
Thrust bearing: The load acts parallel to the axis.
Within both categories, there are different types of bearings with the same basic structure and purpose. The main differences are the type of load they handle and the type of rolling elements they use. Below are brief examples of each type.
The rolling elements in ball bearings are perfectly spherical balls that sit between the bearing races and act as rolling elements to maintain separation between the bearing races. Ball bearings can rotate in any direction due to their spherical shape, which allows them to support combined loads (radial and axial). They minimize rotational friction but have limited contact area. They are best suited for light to medium duty applications rather than heavy loads or impacts. Steel or ceramic balls are mounted between the inner and outer rings to form a classic ball bearing. These are designed to support the rotating axis while reducing friction between static and moving parts. Ball bearings support rotating axes while reducing the proportions between these components and static components. Spheres (usually steel balls, but sometimes ceramic balls, operating at high temperatures) are mounted between the inner and outer rings. Bearing assemblies can be single-row or multiple-row, depending on the application. There are broadly two types of ball bearings: deep groove ball bearings, which have a high radial load capacity, and angular contact ball bearings, which can handle both high radial and axial loads. Ball bearings are used in a wide range of applications, from complex aerospace engineering to everyday skateboards. Common ball bearing types are:
Roller bearings
Roller bearings can handle heavier loads than ball bearings. The rolling elements are cylindrical or tapered in shape and are installed between the inner and outer rings. Their purpose is to minimize friction between moving shafts and static components. Cylindrical roller bearings are usually made of stainless steel and are suitable for heavy radial loads. They are ideal for high-speed applications because their low-friction design does not generate heat or noise. You’ll find cylindrical roller bearings in gearboxes, electric motors and pumps in numerous industries including automotive, mining and construction. For lower speed applications, use spherical roller bearings. These self-aligning bearings can handle severe misalignment, vibration and sudden shocks and, when mounted in double rows, can withstand extremely heavy radial and axial loads. Roller thrust bearings have similar misalignment management characteristics. Common roller bearing types are:
Compact, lightweight and easy to install, rod ends are a reliable choice for heavy alternating loads. The basic design is a round head with an integral shank in which a spherical bearing is installed. Because they are fixed, rod ends do not have the misalignment characteristic of some other bearings. A rod end is a mounted bearing, which is a set of bearings installed in a bolted assembly (including the pillow block). They are typically used on machines with exposed rotating shafts. Cam followers are another variation. They have thicker outer rings and softer inner rings to withstand impacts, and work with cams to convert rotational motion into linear motion. Spherical bearings mounted on rod ends require a constant contact area to minimize stick-slip and keep friction stable. Lubrication is critical, which can cause problems in applications where the presence of impurities is not tolerated.
What are bushings?
A bushing is a cylindrical component designed to support loads on a shaft that operates by sliding motion between moving surfaces. The bushing is a single element assembly, although it may be composed of several different materials. Also known as sleeve bearings, bushings slide on a rod or shaft to provide extremely low-friction motion, providing excellent shock absorption and working to minimize energy use, noise and wear.
What types of bushings are there?
There are several bushing types on the market with different material compositions. Some handle high pressure and shock well, while others can withstand corrosion. You can select the ideal bushing type based on your application and operating environment for industrial or manufacturing use. Bushings can be classified based on two main elements; material and shape. According to material, there are three common types of bushings: composite bushings, metal bushings, and plastic bushings. There are four types of bushings according to their shapes: cylindrical sliding bushings, flange bushings, thrust washers and sliding plates.
Polymer or composite bushings
Polymer bushings, also known as composite bushings, are better suited for carrying heavy loads. These are the most commonly used bushings because of their low friction and wear-resistant properties. Polymer or composite bushings reduce equipment damage caused by improper lubrication. Further, polymer or composite bushings are used to transmit rotational motion when at least one of the two friction parts in a machine or micromechanism is composed of a polymer. Polymer or composite bushings can be used in hazardous environments where traditional bearings are not suitable. These bushings are used in a variety of industries, including construction equipment, hydraulic systems, medical equipment, aerospace and .
Composite bushings can be further divided into the following two categories based on different materials:
POM composite bushing
POM bushings are mainly used to reduce vibration and noise in machines. Because composite bushings are typically made from durable materials, they are ideal for reducing bearing wear. POM composites also help reduce heat buildup caused by friction. This helps extend bearing life up to four times that of other traditional materials such as steel.
PTFE composite bushing
This bushing is made using two different materials, including Teflon and metal. These types of bushings are used as bearings in a variety of industrial applications. The core purpose is to reduce friction between moving parts in a machine.
Metal Bushing
As the name suggests, these bushings are made of metal or metal alloys and form a two- to three-layer structure with a steel backing. These bushings have very high mechanical strength, making them suitable for high speed and load applications involving lubrication. The metal used depends on the type of industrial environment or application. These bushings have different lubrication methods based on their size, structure and application. Metal bushings can be further divided into 6 major types based on different materials, including:
Bronze bushing
Bronze is the material of choice for bushings and is commonly found in a variety of alloys and compositions. You can use bronze bushings for a variety of purposes in industrial manufacturing. Bronze bushings resist deformation and breakage better than other materials. Like plastic, bronze bearings are strong and rust-resistant. There are also self-lubricating bronze bushings on the market for a variety of applications. You can use bronze bushings in a variety of applications, including food processing, injection molding, automotive machinery, earthmoving machinery, steel manufacturing, and .
Graphite bushing
Graphite bushings are used in many applications due to their unique mechanical and physical properties. Graphite bushings have a low coefficient of friction, helping to improve the efficiency, productivity and performance of spinning machinery. Graphite, a naturally oily mineral, is one of the best materials for bushings because it reduces friction without the use of additional fluid. Bronze bushings with graphite plugs are used to manufacture graphite lubricated bearings. Graphite has the highest temperature stability, maintaining its shape and structure at temperatures up to 5000°F. Graphite is widely used in thermal environments such as load-carrying systems where metal lubricants and greases will deteriorate. You can use graphite liners for a variety of purposes including furnaces and ovens, food applications, chemical industry, automotive industry, metals, and .
Steel bushing
As the name suggests, steel bushings are made of steel or stainless steel. These bushings are made from highly durable steel, making them the perfect tool for low speed pivot applications. Steel bushings are manufactured using environmentally friendly production methods that increase material yield and reduce chipping.
Brass bushing
Brass bushings, also known as brass sleeves, are usually made of brass. The brass bushing is a component of the pivot that helps protect the body from any damage caused by any force transmitted through the shaft. Brass bushings are used in a variety of applications, including electric motors, automotive engines, and . Additionally, brass bushings come in a variety of sizes as they can fit thin and thick walls, flanges, cylindrical, flanged, etc.
Aluminum bushing
Aluminum bushings are preferred for their hardness, ensuring a long service life. Initially, it was used on bicycles, but gradually it was used on cars and is currently used on a variety of different machinery. Aluminum bushings can withstand large axial and radial loads, making them an important candidate for use in the aerospace and agricultural industries. Some of their common applications include use in hydraulic cylinders used to install instrumentation (such as drain plugs/fluid fills, fluid sight glasses, or breather elements), vessels, and tanks.
Bimetal bushing
As the name suggests, bimetal bushings are made of two different metals. In most cases, the first metal is steel, while other metals may range from copper to aluminum or even brass. This bimetallic layer acts as an internal covering for the bushing, providing good protection against wear. They are particularly useful in applications that run moderate loads at medium speeds or high loads at low speeds.
Plastic bushing
Plastic bushings are an excellent alternative to metal bushings in many applications due to their lower wear rates. Plastic bushings are lightweight and have a lower coefficient of friction than metal bushings. Since they are made of plastic, they can easily adapt under load and maintain their ability to perform optimally. Made from composite plastic, they have high tensile strength and can be used in a variety of industrial applications. Plastic bushings are mainly composed of thermoplastic alloys and solid lubricants. They also have a fibrous matrix that enhances their structural strength. They are relatively cheaper because they are made from low-cost materials such as polyethylene, nylon, Teflon, and ultra-high molecular weight. High-end plastics such as Torlon, PEEK and Vespel make up a range of expensive plastic bushings.There are four other types of plastic bushings:
Nylon bushing
Nylon bushings are strong and durable and are increasingly replacing metal bushings in many applications. The material has excellent wear resistance and requires no external lubrication. Nylon bushings, although strong, are lightweight and do not make as much noise when operating as metal bushings. They have a low coefficient of friction and high resistance to weak acids, fuels and alkalis.
Polymer bushing
Self-lubricating and maintenance-free, polymer bushings are manufactured with a braided construction that ensures high tensile strength and easily outperforms injection mold bushings. They are highly resistant to heavy loads and wear, making them suitable for applications involving oscillations and high speeds. Polymer bushings are mostly chemically inert; they have low water absorption and can operate at high temperatures without deforming.
PTFE bushing
PTFE bushings have low friction and can withstand high temperature fluctuations, making them suitable for a variety of industrial applications. They are classified as multi-purpose bushings as they can be used in a variety of industries such as electrical, thermal, nuclear, chemical, pharmaceutical and even power plants. They are commonly found in trains and high-performance machines. They are made of materials with high resistance to environmental factors, heat resistance, low coefficient of friction and non-adhesive properties. The only drawback is that they are very flexible, which means they can often crawl or twist. By adding fillers, this problem can also be solved and allow manufacturers to offer highly versatile bushings.
Polyacetal bushing
Polyacetal bushings are developed with self-lubrication in mind and are suitable for heavy loads operating at low speeds. They have good wear resistance and low coefficient of friction. Applications of POM bushings are widely used in agriculture, civil engineering, machinery and construction industries. Polyoxymethylene bushings or POM bushings are typically made from a steel backing coated with a sintered copper/bronze layer. Finally, a POM layer is added over the copper/bronze layer, which contains grease pits that retain the lubricant.
Bushing Types by Shape
In terms of shape, there are four main types of bushings.
Cylindrical sliding bushing
As the name suggests, cylindrical bushings are cylindrical in shape, manufactured to industry standard dimensions, and are machine parts ready for installation. The cylindrical bushing has backings on the inside and outside that support the sliding layer in the middle. Cylindrical bushings are stronger than bearings and can withstand higher forces than metal bearings, making them ideal for one-way variable loads, pivoting movements and axial guide bearings.
Flange bushing
Flange bushings are nearly identical to cylindrical bushings, but with one obvious difference: they have a flange on one end. Flanges can be used for a variety of purposes, from bushing installation or alignment to convenient installation. Typically used in through-bolt applications, they allow the use of smaller diameter bolts to reduce weight without resulting in less fastener support surface for the spar wall, while also reducing stress on the mounting bolt threads.
Thrust washer
The thrust washer itself is not a bushing, but it is a very important component. They are basically flat washers that sit between the fixed component and the rolling surface and support axial loads or side-to-side motion on the shaft, restricting any movement along the shaft. They form a surface on top of which the bearing or bushing is supported.
Sliding Plates
Sliding Plates are common components used in tool and mold making. They are low maintenance and are popular in industries such as automotive, mechanical engineering, lifting, welding technology, injection molding machines and conveyor technology. Sliding Plates are considered linear bearings and can be extension joints of bridges or other mechanical components. The principle is very similar to that of a bearing or bushing. One of the plates is stationary and the other slides against it to resist expansion or contraction. Skateboards can be made from a variety of materials, from steel to PTFE and TEF-MET.
Bushing load and speed limits
Bushings are typically used for heavier loads and slower speeds. Industrial machinery benefits from durable bushings that can withstand extensive load transfer and shock loads. For bushings, frictional heating must be considered. The two main factors affecting heat are unit pressure (P) and surface velocity (V). The product of unit pressure and surface velocity is pressure velocity (PV). To determine whether a bushing is suitable for any application, first find the limiting PV value from the manufacturer. For safe operation, the PV value calculated by the application must be below the manufacturer’s limiting PV value.
Calculate the PV value of the application: PV=P×V
Determine surface speed (V): V=0.262×rpm×D Rpm = shaft revolutions per minute D = shaft diameter (inches)
Determine Pressure (P): P = Total Load (lbs) / Contact Area (in²) Contact Area = D (shaft diameter in inches) x L (casing length)
The effect of limiting the PV value can be seen in this graph, which compares velocity versus load for bronze and Nyloil bushings. In an internal engineering study, Reliance Foundry’s R-3320 grinding wheels were used with Nycast Nyloil and C93200 bronze bushings to test the effects of the PV limits of the bushings. As mentioned previously, bushings are typically used for heavier loads at slower speeds. This is evident in the diagram as neither bushing is capable of handling significant loads at high speeds. The faster the speed, the lower its load capacity. P-max (psi) and V-max (fpm) values are provided by the manufacturer for each product. P-max is the maximum load at 0 rpm and V-max is the maximum speed at light load (maximum shaft rpm). For practical applications, compare the calculated P, V, and PV values to the maximum tolerances to determine if the bushing will operate. Ensure that the bushing operates within a range below the limiting PV curve.
Bushings vs Bearings
There are a variety of factors that determine whether a bushing or bearing is suitable for your specific application. Each has its advantages and disadvantages that must be taken into consideration during the selection process.
Advantages of bushings
While a bushing is technically a type of bearing, it is a single component designed to support a shaft. It operates by sliding motion between moving surfaces, providing extremely low friction motion, thereby minimizing power consumption, noise and parts wear.
As a single component, bushings have advantages over bearings during assembly and are less expensive. They tend to be self-lubricating and provide quieter operation than most bearings.
Disadvantages of bushings
The bushing must overcome static friction, known as stick and slip, before it can move, especially when the linear motion system is worn or misaligned, causing the bushing to move in an erratic, uneven motion.
Bushings, especially cheaper ones, tend to have wider tolerances and therefore have a less precise fit on smooth rods.
Advantages of bearings
Bearings generally provide smoother motion than bushings, overcoming stiction by rolling rather than sliding.
They tend to be precisely manufactured than bushings, with tighter tolerances for a better fit, resulting in less slop and play.
Bearings also offer significant advantages over bushings in high-speed environments.
Bearing Disadvantages
High cost compared to casing cost (about sixty times).
Requires extensive maintenance, often including lubrication
Loud operation sound
Improperly installed or damaged bearings may cause damage to other components if they crack.
Choice between bearings vs bushings
Factors to remember when deciding between bushings or bearings should include the following (in order of preference):
Speed and load: Will the wheel carry a heavier load at slower speeds or a lighter load at higher speeds? Where high speed is a factor, bearings offer a better solution, while bushings respond well to low-speed, heavy-load applications.
Smooth operation: Bearings are a better choice for smoother operation due to “stick-slip”, a common problem with bushings.
Maintenance/Lubrication: Maintenance-free applications with self-lubricating capabilities, especially in the dry food and textile industries, often favor bushings.
Operating noise: When quiet operation is a key consideration, bushings are generally quieter than bearings.
Budget: Budget is a key factor as bushings typically cost much less than bearings, making them a cost-effective option. Bushings tend to cost six to ten times less than bearings.
When choosing between bearings and bushings, the specific application, its operating environment, and various operating conditions and limitations must be considered. Understanding the advantages and disadvantages of each type can help determine which type provides the best solution. Whether you’re looking for bushings or bearings, learn why each product exists and what benefits they bring. Aubearing can help you make a good choice. If you need a product that can handle long-term use at heavier loads and higher speeds, then bearings are your best choice. But if you don’t need something too intense, then a bushing will suffice. Generally speaking, bushings are cost-effective than bearings, so if you’re on a tight budget, bushings are a good option too! Bottom line, when it comes to bearing and bushing selection, it really depends on your application needs.