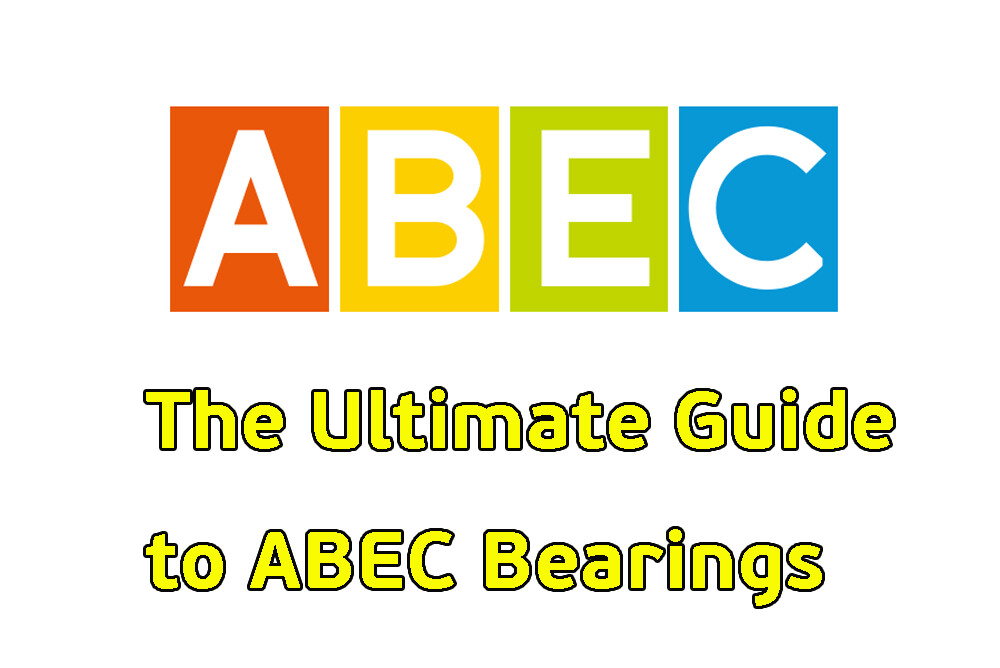
Bearing Manufacturer & Supplier
Specialize in ball bearings, roller bearings, thrust bearings, thin section bearings etc.
The Ultimate Guide to ABEC Bearings
The Annular Bearing Engineering Committee (ABEC) has been around for over 50 years and is a division of the American Bearing Manufacturers Association (AMBA). The ABEC rating system is designed to establish acceptable tolerances and specifications for the dimensional and geometric accuracy of all bearings. The tolerance class of a bearing is called the ABEC class. ABEC ratings are the accepted industry standard for ball bearing and roller bearing tolerances, so bearing manufacturers around the world are required to have ABEC ratings for their products. Once evaluated, the rating is etched onto the bearing. Of course, depending on the local standard designation, bearing tolerances may also be specified by equivalent ISO 492 and JIS B 1514 standards. ABEC ratings serve as one of the reference guides designed to help consumers make informed decisions about the type of bearing best suited for their application, but they are not the only guide. Therefore, the ABEC rating system is just one of many tools that should be used when determining appropriate bearing options.
Table of Contents
ToggleWhat is ABEC bearing rating?
The ABEC bearings rating system uses odd numbers (1, 3, 5, 7, 9) for classification ratings. Its ratings are the accepted standard for ball bearing tolerances. The scale shows five levels from widest to tightest tolerance: 1, 3, 5, 7, and 9. Five different classifications are arranged in ascending order of bearing grade. Higher ABEC grades mean tighter tolerances and correspondingly higher bearing accuracy, efficiency and speed capabilities. It should be noted that the rotational speed of a bearing depends on several other factors besides the specific ABEC rating, but is not the only factor. Bearings that do not meet at least ABEC 1 standards cannot be classified as precision bearings because their tolerances are too loose. Typically, high-rated ABEC bearings (ABEC 5, 7, 9) are suitable for precision applications such as aircraft instrumentation, machine tools, and surgical equipment. Lower grade ABEC bearings (ABEC 1 and 3) are suitable for most other applications requiring ball bearings, including vehicles, skateboards, hobby mechanics, fishing reels, etc.
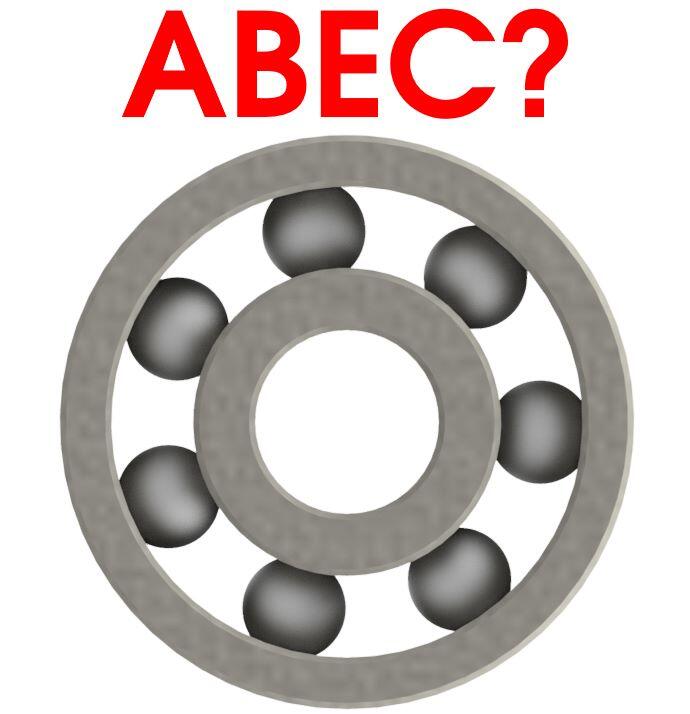
ABEC Bearing Tolerance Classes
The table below lists actual ABEC and RBEC tolerances in compliance with ABMA Standard 20. These tables list the tolerances of the inner and outer rings in inches and metric units. These tables can be used to determine dimensions and tolerances for components such as shafts and housings. When sizing bearings, designers should always perform a tolerance stackup study at maximum and minimum material conditions, especially when designing miniature ball bearings. ABEC uses two main factors to determine tolerance levels: dimensional accuracy and running accuracy. Dimensional accuracy includes physical bearing characteristics, such as: bore diameter, outer diameter, bearing width, inner ring taper allowable deviation, shape error, etc. Running accuracy, on the other hand, measures parameters related to inaccuracy, such as axial runout or inner and outer ring runout, etc.
ABEC 1 is the roughest, least accurate, most durable and least expensive bearing grade.
ABEC 3 is the most cost-effective grade of most inexpensive bearings suitable for most applications.
ABEC 5 is a bearing grade that achieves reasonable speeds at a reasonable cost.
ABEC grade 7 bearings are very fast and smooth, but very expensive.
ABEC 9 and higher grades are very expensive and may not even be available for daily purchase.
Tolerance values in 0.0001 inch
Bore Diameter (d) | Bore | Radial Runout (Kia) | Width Tolerance (ΔBS) | ||||||
mm | inch | all | single bearing | paired bearings | |||||
over | incl. | over | incl. | high | low | max. | high | low | |
0.6 | 2.5 | 0.0236 | 0.0984 | 0 | -3 | 4 | 0 | -16 | – |
2.5 | 10 | 0.0984 | 0.3937 | 0 | -3 | 4 | 0 | -47 | -98 |
10 | 18 | 0.3937 | 0.7087 | 0 | -3 | 4 | 0 | -47 | -98 |
18 | 30 | 0.7087 | 1.1811 | 0 | -4 | 5 | 0 | -47 | -98 |
30 | 50 | 1.1811 | 1.9685 | 0 | -4.5 | 6 | 0 | -47 | -98 |
50 | 80 | 1.9685 | 3.1496 | 0 | -6 | 8 | 0 | -59 | -150 |
80 | 120 | 3.1496 | 4.7244 | 0 | -8 | 10 | 0 | -79 | -150 |
120 | 180 | 4.7244 | 7.0866 | 0 | -10 | 12 | 0 | -98 | -197 |
180 | 250 | 7.0866 | 9.8425 | 0 | -12 | 16 | 0 | -118 | -197 |
250 | 315 | 9.8425 | 12.4016 | 0 | -14 | 20 | 0 | -138 | -197 |
315 | 400 | 12.4016 | 15.7480 | 0 | -16 | 24 | 0 | -157 | -248 |
Metric Tolerance values in micrometers
Bore Diameter (d) | Bore | Radial Runout (Kia) | Width Tolerance (ΔBS) | ||||||
mm | inch | all | single bearing | paired bearings | |||||
over | incl. | over | incl. | high | low | max. | high | low | |
0.6 | 2.5 | 0.0236 | 0.0984 | 0 | -8 | 10 | 0 | -40 | – |
2.5 | 10 | 0.0984 | 0.3937 | 0 | -8 | 10 | 0 | -120 | -250 |
10 | 18 | 0.3937 | 0.7087 | 0 | -8 | 10 | 0 | -120 | -250 |
18 | 30 | 0.7087 | 1.1811 | 0 | -10 | 13 | 0 | -120 | -250 |
30 | 50 | 1.1811 | 1.9685 | 0 | -12 | 15 | 0 | -120 | -250 |
50 | 80 | 1.9685 | 3.1496 | 0 | -15 | 20 | 0 | -150 | -380 |
80 | 120 | 3.1496 | 4.7244 | 0 | -20 | 25 | 0 | -200 | -380 |
120 | 180 | 4.7244 | 7.0866 | 0 | -25 | 30 | 0 | -250 | -500 |
180 | 250 | 7.0866 | 9.8425 | 0 | -30 | 40 | 0 | -300 | -500 |
250 | 315 | 9.8425 | 12.4016 | 0 | -35 | 50 | 0 | -350 | -500 |
315 | 400 | 12.4016 | 15.7480 | 0 | -40 | 60 | 0 | -400 | -630 |
Table IB
Tolerance Class ABEC-1, RBEC-1
(ISO Class Normal)
Outer Ring
Tolerance values in 0.0001 inch
Outer Diameter (D) | Outer Dia. Tolerance | Radial Runout (Kea) | Width Tolerance (ΔBS) | ||||||
mm | inch | all | single bearing | paired bearings | |||||
over | incl. | over | incl. | high | low | max. | high | low | |
2.5 | 6 | 0.0984 | 0.2362 | 0 | -3 | 6 | Identical to Width Tolerance (ΔBS) of Inner Ring of the same Bearing | ||
6 | 18 | 0.2362 | 0.7087 | 0 | -3 | 6 | |||
18 | 30 | 0.7087 | 1.1811 | 0 | -3.5 | 6 | |||
30 | 50 | 1.1811 | 1.9685 | 0 | -4.5 | 8 | |||
50 | 80 | 1.9685 | 3.1496 | 0 | -5 | 10 | |||
80 | 120 | 3.1496 | 4.7244 | 0 | -6 | 14 | |||
120 | 150 | 4.7244 | 5.9055 | 0 | -7 | 16 | |||
150 | 180 | 5.9055 | 7.0866 | 0 | -10 | 18 | |||
180 | 250 | 7.0866 | 9.8425 | 0 | -12 | 20 | |||
250 | 315 | 9.8425 | 12.4016 | 0 | -14 | 24 | |||
315 | 400 | 12.4016 | 15.7480 | 0 | -16 | 28 | |||
400 | 500 | 15.7480 | 19.6850 | 0 | -18 | 31 | |||
500 | 630 | 19.6850 | 24.8031 | 0 | -20 | 39 | |||
630 | 800 | 24.8031 | 31.4961 | 0 | -30 | 47 | |||
800 | 1000 | 31.4961 | 39.3701 | 0 | -39 | 55 |
Metric Tolerance values in micrometers
Outer Diameter (D) | Outer Dia. Tolerance | Radial Runout (Kea) | Width Tolerance (ΔBS) | ||||||
mm | inch | all | single bearing | paired bearings | |||||
over | incl. | over | incl. | high | low | max. | high | low | |
2.5 | 6 | 0.0984 | 0.2362 | 0 | -8 | 15 | Identical to Width Tolerance (ΔBS) of Inner Ring of the same Bearing | ||
6 | 18 | 0.2362 | 0.7087 | 0 | -8 | 15 | |||
18 | 30 | 0.7087 | 1.1811 | 0 | -9 | 15 | |||
30 | 50 | 1.1811 | 1.9685 | 0 | -11 | 20 | |||
50 | 80 | 1.9685 | 3.1496 | 0 | -13 | 25 | |||
80 | 120 | 3.1496 | 4.7244 | 0 | -15 | 35 | |||
120 | 150 | 4.7244 | 5.9055 | 0 | -18 | 40 | |||
150 | 180 | 5.9055 | 7.0866 | 0 | -25 | 45 | |||
180 | 250 | 7.0866 | 9.8425 | 0 | -30 | 50 | |||
250 | 315 | 9.8425 | 12.4016 | 0 | -35 | 60 | |||
315 | 400 | 12.4016 | 15.7480 | 0 | -40 | 70 | |||
400 | 500 | 15.7480 | 19.6850 | 0 | -45 | 80 | |||
500 | 630 | 19.6850 | 24.8031 | 0 | -50 | 100 | |||
630 | 800 | 24.8031 | 31.4961 | 0 | -75 | 120 | |||
800 | 1000 | 31.4961 | 39.3701 | 0 | -100 | 140 |
Table II A
Tolerance Class ABEC-3, RBEC-3
(ISO Class 6)
Inner Ring
Tolerance values in 0.0001 inch
Bore Diameter (d) | Bore | Radial Runout (Kia) | Width Tolerance (ΔBS) | ||||||
mm | inch | all | single bearing | paired bearings | |||||
over | incl. | over | incl. | high | low | max. | high | low | |
0.6 | 2.5 | 0.0236 | 0.0984 | 0 | -3 | 2 | 0 | -16 | – |
2.5 | 10 | 0.0984 | 0.3937 | 0 | -3 | 2.5 | 0 | -47 | -98 |
10 | 18 | 0.3937 | 0.7087 | 0 | -3 | 3 | 0 | -47 | -98 |
18 | 30 | 0.7087 | 1.1811 | 0 | -3 | 3 | 0 | -47 | -98 |
30 | 50 | 1.1811 | 1.9685 | 0 | -4 | 4 | 0 | -47 | -98 |
50 | 80 | 1.9685 | 3.1496 | 0 | -4.5 | 4 | 0 | -59 | -150 |
80 | 120 | 3.1496 | 4.7244 | 0 | -6 | 5 | 0 | -79 | -150 |
120 | 180 | 4.7244 | 7.0866 | 0 | -7 | 7 | 0 | -98 | -197 |
180 | 250 | 7.0866 | 9.8425 | 0 | -8.5 | 8 | 0 | -118 | -197 |
250 | 315 | 9.8425 | 12.4016 | 0 | -10 | 10 | 0 | -138 | -197 |
315 | 400 | 12.4016 | 15.7480 | 0 | -16 | 24 | 0 | -157 | -248 |
Metric Tolerance values in micrometers
Bore Diameter (d) | Bore | Radial Runout (Kia) | Width Tolerance (ΔBS) | ||||||
mm | inch | all | single bearing | paired bearings | |||||
over | incl. | over | incl. | high | low | max. | high | low | |
0.6 | 2.5 | 0.0236 | 0.0984 | 0 | -7 | 5 | 0 | -40 | – |
2.5 | 10 | 0.0984 | 0.3937 | 0 | -7 | 6 | 0 | -120 | -250 |
10 | 18 | 0.3937 | 0.7087 | 0 | -7 | 7 | 0 | -120 | -250 |
18 | 30 | 0.7087 | 1.1811 | 0 | -8 | 8 | 0 | -120 | -250 |
30 | 50 | 1.1811 | 1.9685 | 0 | -10 | 10 | 0 | -120 | -250 |
50 | 80 | 1.9685 | 3.1496 | 0 | -12 | 10 | 0 | -150 | -380 |
80 | 120 | 3.1496 | 4.7244 | 0 | -15 | 13 | 0 | -200 | -380 |
120 | 180 | 4.7244 | 7.0866 | 0 | -18 | 18 | 0 | -250 | -500 |
180 | 250 | 7.0866 | 9.8425 | 0 | -22 | 20 | 0 | -300 | -500 |
250 | 315 | 9.8425 | 12.4016 | 0 | -25 | 25 | 0 | -350 | -500 |
315 | 400 | 12.4016 | 15.7480 | 0 | -30 | 30 | 0 | -400 | -630 |
Tolerance Class ABEC-3, RBEC-3
(ISO Class 6)
Outer Ring
Tolerance values in 0.0001 inch
Outer Diameter (D) | Outer Dia. Tolerance | Radial Runout (Kea) | Width Tolerance (ΔBS) | ||||||
mm | inch | all | single bearing | paired bearings | |||||
over | incl. | over | incl. | high | low | max. | high | low | |
2.5 | 6 | 0.0984 | 0.2362 | 0 | -3 | 3 | Identical to Width Tolerance (ΔBS) of Inner Ring of the same Bearing | ||
6 | 18 | 0.2362 | 0.7087 | 0 | -3 | 3 | |||
18 | 30 | 0.7087 | 1.1811 | 0 | -3 | 3.5 | |||
30 | 50 | 1.1811 | 1.9685 | 0 | -3.5 | 4 | |||
50 | 80 | 1.9685 | 3.1496 | 0 | -4.5 | 5 | |||
80 | 120 | 3.1496 | 4.7244 | 0 | -5 | 7 | |||
120 | 150 | 4.7244 | 5.9055 | 0 | -6 | 8 | |||
150 | 180 | 5.9055 | 7.0866 | 0 | -7 | 9 | |||
180 | 250 | 7.0866 | 9.8425 | 0 | -8 | 10 | |||
250 | 315 | 9.8425 | 12.4016 | 0 | -10 | 12 | |||
315 | 400 | 12.4016 | 15.7480 | 0 | -11 | 14 | |||
400 | 500 | 15.7480 | 19.6850 | 0 | -13 | 16 | |||
500 | 630 | 19.6850 | 24.8031 | 0 | -20 | 39 | |||
630 | 800 | 24.8031 | 31.4961 | 0 | -18 | 24 | |||
800 | 1000 | 31.4961 | 39.3701 | 0 | -24 | 30 |
Metric Tolerance values in micrometers
Outer Diameter (D) | Outer Dia. Tolerance | Radial Runout (Kea) | Width Tolerance (ΔBS) | ||||||
mm | inch | all | single bearing | paired bearings | |||||
over | incl. | over | incl. | high | low | max. | high | low | |
2.5 | 6 | 0.0984 | 0.2362 | 0 | -7 | 8 | Identical to Width Tolerance (ΔBS) of Inner Ring of the same Bearing | ||
6 | 18 | 0.2362 | 0.7087 | 0 | -7 | 8 | |||
18 | 30 | 0.7087 | 1.1811 | 0 | -8 | 9 | |||
30 | 50 | 1.1811 | 1.9685 | 0 | -9 | 10 | |||
50 | 80 | 1.9685 | 3.1496 | 0 | -11 | 13 | |||
80 | 120 | 3.1496 | 4.7244 | 0 | -13 | 18 | |||
120 | 150 | 4.7244 | 5.9055 | 0 | -15 | 20 | |||
150 | 180 | 5.9055 | 7.0866 | 0 | -18 | 23 | |||
180 | 250 | 7.0866 | 9.8425 | 0 | -20 | 25 | |||
250 | 315 | 9.8425 | 12.4016 | 0 | -25 | 30 | |||
315 | 400 | 12.4016 | 15.7480 | 0 | -28 | 35 | |||
400 | 500 | 15.7480 | 19.6850 | 0 | -33 | 40 | |||
500 | 630 | 19.6850 | 24.8031 | 0 | -38 | 50 | |||
630 | 800 | 24.8031 | 31.4961 | 0 | -45 | 60 | |||
800 | 1000 | 31.4961 | 39.3701 | 0 | -60 | 75 |
Table III A
Tolerance Class ABEC-5, RBEC-5
(ISO Class 5)
Inner Ring
Tolerance values in 0.0001 inch
Bore Diameter (d) | Bore | Radial Runout (Kia) | Width Tolerance (ΔBS) | ||||||
mm | inch | all | single bearing | paired bearings | |||||
over | incl. | over | incl. | high | low | max. | high | low | |
0.6 | 2.5 | 0.0236 | 0.0984 | 0 | -2 | 1.5 | 0 | -16 | -98 |
2.5 | 10 | 0.0984 | 0.3937 | 0 | -2 | 1.5 | 0 | -16 | -98 |
10 | 18 | 0.3937 | 0.7087 | 0 | -2 | 1.5 | 0 | -31 | -98 |
18 | 30 | 0.7087 | 1.1811 | 0 | -2.5 | 1.5 | 0 | -47 | -98 |
30 | 50 | 1.1811 | 1.9685 | 0 | -3 | 2 | 0 | -47 | -98 |
50 | 80 | 1.9685 | 3.1496 | 0 | -3.5 | 2 | 0 | -59 | -98 |
80 | 120 | 3.1496 | 4.7244 | 0 | -4 | 2.55 | 0 | -79 | -150 |
120 | 180 | 4.7244 | 7.0866 | 0 | -5 | 3 | 0 | -98 | -150 |
180 | 250 | 7.0866 | 9.8425 | 0 | -6 | 4 | 0 | -118 | -197 |
250 | 315 | 9.8425 | 12.4016 | 0 | -7 | 5 | 0 | -138 | -197 |
315 | 400 | 12.4016 | 15.7480 | 0 | -9 | 6 | 0 | -157 | -248 |
Metric Tolerance values in micrometers
Bore Diameter (d) | Bore | Radial Runout (Kia) | Width Tolerance (ΔBS) | ||||||
mm | inch | all | single bearing | paired bearings | |||||
over | incl. | over | incl. | high | low | max. | high | low | |
0.6 | 2.5 | 0.0236 | 0.0984 | 0 | -5 | 4 | 0 | -40 | -250 |
2.5 | 10 | 0.0984 | 0.3937 | 0 | -5 | 4 | 0 | -40 | -250 |
10 | 18 | 0.3937 | 0.7087 | 0 | -5 | 4 | 0 | -80 | -250 |
18 | 30 | 0.7087 | 1.1811 | 0 | -6 | 4 | 0 | -120 | -250 |
30 | 50 | 1.1811 | 1.9685 | 0 | -8 | 5 | 0 | -120 | -250 |
50 | 80 | 1.9685 | 3.1496 | 0 | -9 | 5 | 0 | -150 | -250 |
80 | 120 | 3.1496 | 4.7244 | 0 | -10 | 6 | 0 | -200 | -380 |
120 | 180 | 4.7244 | 7.0866 | 0 | -13 | 8 | 0 | -250 | -380 |
180 | 250 | 7.0866 | 9.8425 | 0 | -15 | 10 | 0 | -300 | -500 |
250 | 315 | 9.8425 | 12.4016 | 0 | -18 | 13 | 0 | -350 | -500 |
315 | 400 | 12.4016 | 15.7480 | 0 | -23 | 15 | 0 | -400 | -630 |
Table III B
Tolerance Class ABEC-5, RBEC-5
(ISO Class 5)
Outer Ring
Tolerance values in 0.0001 inch
Outer Diameter (D) | Outer Dia. Tolerance | Radial Runout (Kea) | Width Tolerance (ΔBS) | ||||||
mm | inch | all | single bearing | paired bearings | |||||
over | incl. | over | incl. | high | low | max. | high | low | |
2.5 | 6 | 0.0984 | 0.2362 | 0 | -2 | 2 | Identical to Width Tolerance (ΔBS) of Inner Ring of the same Bearing | ||
6 | 18 | 0.2362 | 0.7087 | 0 | -2 | 2 | |||
18 | 30 | 0.7087 | 1.1811 | 0 | -2.5 | 2.5 | |||
30 | 50 | 1.1811 | 1.9685 | 0 | -3 | 3 | |||
50 | 80 | 1.9685 | 3.1496 | 0 | -3.5 | 3 | |||
80 | 120 | 3.1496 | 4.7244 | 0 | -4 | 4 | |||
120 | 150 | 4.7244 | 5.9055 | 0 | -4.5 | 4.5 | |||
150 | 180 | 5.9055 | 7.0866 | 0 | -5 | 5 | |||
180 | 250 | 7.0866 | 9.8425 | 0 | -6 | 6 | |||
250 | 315 | 9.8425 | 12.4016 | 0 | -7 | 7 | |||
315 | 400 | 12.4016 | 15.7480 | 0 | -8 | 8 | |||
400 | 500 | 15.7480 | 19.6850 | 0 | -9 | 9 | |||
500 | 630 | 19.6850 | 24.8031 | 0 | -11 | 10 | |||
630 | 800 | 24.8031 | 31.4961 | 0 | -14 | 12 |
Metric Tolerance values in micrometers
Outer Diameter (D) | Outer Dia. Tolerance | Radial Runout (Kea) | Width Tolerance (ΔBS) | ||||||
mm | inch | all | single bearing | paired bearings | |||||
over | incl. | over | incl. | high | low | max. | high | low | |
2.5 | 6 | 0.0984 | 0.2362 | 0 | -5 | 5 | Identical to Width Tolerance (ΔBS) of Inner Ring of the same Bearing | ||
6 | 18 | 0.2362 | 0.7087 | 0 | -5 | 5 | |||
18 | 30 | 0.7087 | 1.1811 | 0 | -6 | 6 | |||
30 | 50 | 1.1811 | 1.9685 | 0 | -6 | 6 | |||
50 | 80 | 1.9685 | 3.1496 | 0 | -9 | 8 | |||
80 | 120 | 3.1496 | 4.7244 | 0 | -10 | 10 | |||
120 | 150 | 4.7244 | 5.9055 | 0 | -11 | 11 | |||
150 | 180 | 5.9055 | 7.0866 | 0 | -13 | 13 | |||
180 | 250 | 7.0866 | 9.8425 | 0 | -15 | 15 | |||
250 | 315 | 9.8425 | 12.4016 | 0 | -18 | 18 | |||
315 | 400 | 12.4016 | 15.7480 | 0 | -20 | 20 | |||
400 | 500 | 15.7480 | 19.6850 | 0 | -23 | 23 | |||
500 | 630 | 19.6850 | 24.8031 | 0 | -28 | 25 | |||
630 | 800 | 24.8031 | 31.4961 | 0 | -35 | 30 |
Table IV A
Tolerance Class ABEC-7, RBEC-7
(ISO Class 4)
Inner Ring
Tolerance values in 0.0001 inch
Bore Diameter (d) | Bore | Radial Runout (Kia) | Width Tolerance (ΔBS) | ||||||
mm | inch | all | single bearing | paired bearings | |||||
over | incl. | over | incl. | high | low | max. | high | low | |
0.6 | 2.5 | 0.0236 | 0.0984 | 0 | -1.5 | 1 | 0 | -16 | -98 |
2.5 | 10 | 0.0984 | 0.3937 | 0 | -1.5 | 1 | 0 | -16 | -98 |
10 | 18 | 0.3937 | 0.7087 | 0 | -1.5 | 1 | 0 | -31 | -98 |
18 | 30 | 0.7087 | 1.1811 | 0 | -2 | 1 | 0 | -47 | -98 |
30 | 50 | 1.1811 | 1.9685 | 0 | -2.5 | 1.5 | 0 | -47 | -98 |
50 | 80 | 1.9685 | 3.1496 | 0 | -3 | 1.5 | 0 | -59 | -98 |
80 | 120 | 3.1496 | 4.7244 | 0 | -3 | 2 | 0 | -79 | -150 |
120 | 180 | 4.7244 | 7.0866 | 0 | -4 | 2.5 | 0 | -98 | -150 |
180 | 250 | 7.0866 | 9.8425 | 0 | -4.5 | 3 | 0 | -118 | -197 |
Metric Tolerance values in micrometers
Bore Diameter (d) | Bore | Radial Runout (Kia) | Width Tolerance (ΔBS) | ||||||
mm | inch | all | single bearing | paired bearings | |||||
over | incl. | over | incl. | high | low | max. | high | low | |
0.6 | 2.5 | 0.0236 | 0.0984 | 0 | -4 | 2.5 | 0 | -40 | -250 |
2.5 | 10 | 0.0984 | 0.3937 | 0 | -4 | 2.5 | 0 | -40 | -250 |
10 | 18 | 0.3937 | 0.7087 | 0 | -4 | 2.5 | 0 | -80 | -250 |
18 | 30 | 0.7087 | 1.1811 | 0 | -5 | 3 | 0 | -120 | -250 |
30 | 50 | 1.1811 | 1.9685 | 0 | -6 | 4 | 0 | -120 | -250 |
50 | 80 | 1.9685 | 3.1496 | 0 | -7 | 4 | 0 | -150 | -250 |
80 | 120 | 3.1496 | 4.7244 | 0 | -8 | 5 | 0 | -200 | -380 |
120 | 180 | 4.7244 | 7.0866 | 0 | -10 | 6 | 0 | -250 | -380 |
180 | 250 | 7.0866 | 9.8425 | 0 | -12 | 8 | 0 | -300 | -500 |
Tolerance Class ABEC-7, RBEC-7
(ISO Class 4)
Outer Ring
Tolerance values in 0.0001 inch
Outer Diameter (D) | Outer Dia. Tolerance | Radial Runout (Kea) | Width Tolerance (ΔBS) | ||||||
mm | inch | all | single bearing | paired bearings | |||||
over | incl. | over | incl. | high | low | max. | high | low | |
2.5 | 6 | 0.0984 | 0.2362 | 0 | -1.5 | 1 | Identical to Width Tolerance (ΔBS) of Inner Ring of the same Bearing | ||
6 | 18 | 0.2362 | 0.7087 | 0 | -1.5 | 1 | |||
18 | 30 | 0.7087 | 1.1811 | 0 | -2 | 1.5 | |||
30 | 50 | 1.1811 | 1.9685 | 0 | -2.5 | 2 | |||
50 | 80 | 1.9685 | 3.1496 | 0 | -3 | 2 | |||
80 | 120 | 3.1496 | 4.7244 | 0 | -3 | 2.5 | |||
120 | 150 | 4.7244 | 5.9055 | 0 | -3.5 | 3 | |||
150 | 180 | 5.9055 | 7.0866 | 0 | -4 | 3 | |||
180 | 250 | 7.0866 | 9.8425 | 0 | -4.5 | 4 | |||
250 | 315 | 9.8425 | 12.4016 | 0 | -5 | 4.5 | |||
315 | 400 | 12.4016 | 15.7480 | 0 | -6 | 5 |
Metric Tolerance values in micrometers
Outer Diameter (D) | Outer Dia. Tolerance | Radial Runout (Kea) | Width Tolerance (ΔBS) | ||||||
mm | inch | all | single bearing | paired bearings | |||||
over | incl. | over | incl. | high | low | max. | high | low | |
2.5 | 6 | 0.0984 | 0.2362 | 0 | -4 | 3 | Identical to Width Tolerance (ΔBS) of Inner Ring of the same Bearing | ||
6 | 18 | 0.2362 | 0.7087 | 0 | -4 | 3 | |||
18 | 30 | 0.7087 | 1.1811 | 0 | -5 | 4 | |||
30 | 50 | 1.1811 | 1.9685 | 0 | -6 | 5 | |||
50 | 80 | 1.9685 | 3.1496 | 0 | -7 | 5 | |||
80 | 120 | 3.1496 | 4.7244 | 0 | -8 | 6 | |||
120 | 150 | 4.7244 | 5.9055 | 0 | -9 | 7 | |||
150 | 180 | 5.9055 | 7.0866 | 0 | -10 | 8 | |||
180 | 250 | 7.0866 | 9.8425 | 0 | -11 | 10 | |||
250 | 315 | 9.8425 | 12.4016 | 0 | -13 | 11 | |||
315 | 400 | 12.4016 | 15.7480 | 0 | -15 | 13 |
Table V A
Tolerance Class ABEC-9, RBEC-9
(ISO Class 2)
Inner Ring
Tolerance values in 0.0001 inch
Bore Diameter (d) | Bore | Radial Runout (Kia) | Width Tolerance (ΔBS) | ||||||
mm | inch | all | single bearing | paired bearings | |||||
over | incl. | over | incl. | high | low | max. | high | low | |
0.6 | 2.5 | 0.0236 | 0.0984 | 0 | -1 | 0.5 | 0 | -16 | -98 |
2.5 | 10 | 0.0984 | 0.3937 | 0 | -1 | 0.5 | 0 | -16 | -98 |
10 | 18 | 0.3937 | 0.7087 | 0 | -1 | 0.5 | 0 | -31 | -98 |
18 | 30 | 0.7087 | 1.1811 | 0 | -1 | 1 | 0 | -47 | -98 |
30 | 50 | 1.1811 | 1.9685 | 0 | -1 | 1 | 0 | -47 | -98 |
50 | 80 | 1.9685 | 3.1496 | 0 | -1.5 | 1 | 0 | -59 | -98 |
80 | 120 | 3.1496 | 4.7244 | 0 | -2 | 1 | 0 | -79 | -150 |
120 | 150 | 4.7244 | 5.9055 | 0 | -3 | 1 | 0 | -98 | -150 |
150 | 180 | 5.9055 | 7.0866 | 0 | -3 | 2 | 0 | -98 | -150 |
180 | 250 | 7.0866 | 9.8425 | 0 | -3 | 2 | 0 | -118 | -197 |
MetricTolerance values in micrometers
Bore Diameter (d) | Bore | Radial Runout (Kia) | Width Tolerance (ΔBS) | ||||||
mm | inch | all | single bearing | paired bearings | |||||
over | incl. | over | incl. | high | low | max. | high | low | |
0.6 | 2.5 | 0.0236 | 0.0984 | 0 | -2.5 | 1.5 | 0 | -40 | -250 |
2.5 | 10 | 0.0984 | 0.3937 | 0 | -2.5 | 1.5 | 0 | -40 | -250 |
10 | 18 | 0.3937 | 0.7087 | 0 | -2.5 | 1.5 | 0 | -80 | -250 |
18 | 30 | 0.7087 | 1.1811 | 0 | -2.5 | 2.5 | 0 | -120 | -250 |
30 | 50 | 1.1811 | 1.9685 | 0 | -2.5 | 2.5 | 0 | -120 | -250 |
50 | 80 | 1.9685 | 3.1496 | 0 | -4 | 2.5 | 0 | -150 | -250 |
80 | 120 | 3.1496 | 4.7244 | 0 | -5 | 2.5 | 0 | -200 | -380 |
120 | 150 | 4.7244 | 5.9055 | 0 | -7 | 2.5 | 0 | -250 | -380 |
150 | 180 | 5.9055 | 7.0866 | 0 | -7 | 5 | 0 | -250 | -380 |
180 | 250 | 7.0866 | 9.8425 | 0 | -8 | 5 | 0 | -300 | -500 |
Table V B
Tolerance Class ABEC-9, RBEC-9
(ISO Class 2)
Outer Ring
Tolerance values in 0.0001 inch
Outer Diameter (D) | Outer Dia. Tolerance | Radial Runout (Kea) | Width Tolerance (ΔBS) | ||||||
mm | inch | all | single bearing | paired bearings | |||||
over | incl. | over | incl. | high | low | max. | high | low | |
2.5 | 6 | 0.0984 | 0.2362 | 0 | -1 | 0.5 | Identical to Width Tolerance (ΔBS) of Inner Ring of the same Bearing | ||
6 | 18 | 0.2362 | 0.7087 | 0 | -1 | 0.5 | |||
18 | 30 | 0.7087 | 1.1811 | 0 | -1 | 0.5 | |||
30 | 50 | 1.1811 | 1.9685 | 0 | -1.5 | 1 | |||
50 | 80 | 1.9685 | 3.1496 | 0 | -1.5 | 1.5 | |||
80 | 120 | 3.1496 | 4.7244 | 0 | -2 | 2 | |||
120 | 150 | 4.7244 | 5.9055 | 0 | -2 | 2 | |||
150 | 180 | 5.9055 | 7.0866 | 0 | -3 | 2 | |||
180 | 250 | 7.0866 | 9.8425 | 0 | -3 | 3 | |||
250 | 315 | 9.8425 | 12.4016 | 0 | -3 | 3 | |||
315 | 400 | 12.4016 | 15.7480 | 0 | -4 | 3 |
MetricTolerance values in micrometers
Outer Diameter (D) | Outer Dia. Tolerance | Radial Runout (Kea) | Width Tolerance (ΔBS) | ||||||
mm | inch | all | single bearing | paired bearings | |||||
over | incl. | over | incl. | high | low | max. | high | low | |
2.5 | 6 | 0.0984 | 0.2362 | 0 | -2.5 | 1.5 | Identical to Width Tolerance (ΔBS) of Inner Ring of the same Bearing | ||
6 | 18 | 0.2362 | 0.7087 | 0 | -2.5 | 1.5 | |||
18 | 30 | 0.7087 | 1.1811 | 0 | -4 | 2.5 | |||
30 | 50 | 1.1811 | 1.9685 | 0 | -4 | 2.5 | |||
50 | 80 | 1.9685 | 3.1496 | 0 | -4 | 4 | |||
80 | 120 | 3.1496 | 4.7244 | 0 | -5 | 5 | |||
120 | 150 | 4.7244 | 5.9055 | 0 | -5 | 5 | |||
150 | 180 | 5.9055 | 7.0866 | 0 | -7 | 5 | |||
180 | 250 | 7.0866 | 9.8425 | 0 | -8 | 7 | |||
250 | 315 | 9.8425 | 12.4016 | 0 | -8 | 7 | |||
315 | 400 | 12.4016 | 15.7480 | 0 | -10 | 8 |
What other important bearing tolerance classes are there?
Many countries in the world have their own bearing standards organizations. For example, Germany, Japan, South Korea, Russia and China are major bearing producing countries and all have industry standards covering ball and roller bearings. In almost all cases, these standards are similar or equivalent to ISO 492. The table below shows equivalent tolerance classes for the three most common standards.
ANSI Standard 20 | ISO 492 | DIN 620 |
ABEC 1 | Class Normal | P0 |
ABEC 3 | Class 6 | P6 |
ABEC 5 | Class 5 | P5 |
ABEC 7 | Class 4 | P4 |
ABEC 9 | Class 2 | P2 |
Limitations of ABEC Bearing Ratings
While bearing tolerance classes primarily control the boundary dimensions of the rings, it should also be noted that some features critical to bearing performance and life are not controlled by ABEC (or ISO) specifications. These include internal clearance, surface finish, ball accuracy, torque, noise, cage type and lubrication, etc. These items, along with the accuracy grade, should be specified when selecting bearings to ensure optimal service life and performance. In many cases, it is one of these features, not the level of accuracy, that will yield the desired performance and/or longevity, as long as it is correctly specified.
The ABEC rating system can be misleading for several reasons:
Limited scope: ABEC only measures dimensional tolerances, not real-world performance requirements such as speed or durability.
Misleading Metrics: A high ABEC rating does not guarantee better performance; other factors play a important role.
Special Applications: Selecting bearings for special applications, such as inline speed skate pulleys, requires bearings that can withstand specific stresses, and ABEC does not solve this problem.
Additionally, the ABEC rating system does not include: side load, impact resistance, material selection and grade, clearance between balls and races, installation requirements, and the need for maintenance and cleaning. All of these bearing design requirements are important to the performance of your bearings.
In fact, we have found that in many cases, bearings with high ABEC ratings do not even perform as well as other bearings with lower ABEC ratings, such as in skates or scooter wheels. The performance difference between two bearings with the same ABEC rating is also huge. Therefore, relying solely on ABEC ratings cannot be the only factor in selecting the right bearing for you.
How do you measure the ABEC grade of a bearing?
Of course it is possible to measure the ABEC rating of a bearing, but it is not a simple matter. The ABEC rating of a bearing is usually indicated on the bearing packaging or on the manufacturer’s data sheet. If this information is not available, the ABEC rating of a bearing can be measured using a variety of very precise measuring instruments, such as micrometers and optical comparators. To measure the ABEC rating of a bearing, the bearing must first be removed from the application in which it is used, and then the following measurements must be taken:
1. Bearing outer diameter: Use a micrometer or optical comparator to measure the outer diameter of the bearing.
2. Bearing inner diameter: Use a micrometer or optical comparator to measure the inner diameter of the bearing.
3. Bearing wall thickness: Use a micrometer or optical comparator to measure the bearing wall thickness.
Once these measurements are obtained, a conversion table can be used to determine the ABEC rating of the bearing. Generally speaking, the higher the ABEC grade, the higher the accuracy of the bearing. However, it is worth noting that ABEC ratings do not take into account other factors that may affect bearing quality, such as the quality of balls and fittings. Therefore, measuring the ABEC rating of a bearing is often beyond the capabilities of private users such as skaters. If you are interested in learning about the ABEC rating of the bearings you use, please contact Aubearing today!
Which is important, ABEC grade or quality of the bearing material?
Both the ABEC grade and the quality of the materials used to make the bearing affect the performance of the bearing. However, the quality of the materials used is often important, as higher quality materials contribute to longer bearing life and consistent performance. Generally speaking, manufacturers use better materials to produce higher ABEC ratings.
Do ceramic bearings also have ABEC ratings?
The ABEC rating system was originally developed for steel ball bearings. However, some bearing manufacturers also extend ABEC systems to hybrid and ceramic bearings. Hybrid bearings are made from a combination of materials such as steel and ceramic or steel and polymer. They are often used in applications where good load capacity and good smoothness are required, such as electric motors (e.g. motorized spindles) in certain applications. Ceramic bearings are made entirely of ceramic materials, such as silicon nitride. They are often used in applications where good wear resistance, good heat resistance and good smoothness are required (for example, they are also used in “speed” professional roller skates). If the bearing manufacturer offers an ABEC system for hybrid or ceramic bearings, the definitions of the various grades may differ from the ABEC grades for steel ball bearings. In general, it is important to consult the bearing manufacturer or supplier for accurate information on the ABEC grade definitions available for ceramic or hybrid bearings.
How to choose the right ABEC grade for your bearings?
Choosing the right ABEC grade for your bearing application requires a full understanding of what the ABEC grade represents. Most bearings sold are ABEC Class 1 and 3 and perform very well. These bearings are at the middle end of the range and are commonly found in non-precision applications such as automotive components, skateboards, electric motors and gearboxes. In applications where bearings need to operate at very high rotational speeds, or in equipment that requires precise positioning, tighter tolerances are often required. For example, products with rotation speeds exceeding 30,000 rpm, such as high-speed routers, are called high-precision, ultra-precision, and ultra-high precision. In these cases, an ABEC rating of 7 or 9 is typically required. Manufacturing these higher rated bearings requires precise machining and longer production times. They are also significantly expensive, often as much as five times than lower rated bearings.
It is important to note that while ABEC grades can help determine bearing performance to some extent, there are several other factors that need to be evaluated when selecting the appropriate bearing. For example, impact resistance, side loading, lubrication, clearance, noise and installation requirements. Therefore, significant differences in performance between two similarly rated bearings in different environments can be observed. For similar reasons, in some cases a bearing with a lower ABEC rating may perform better in a particular application than a bearing with a higher ABEC rating.
Conclusion
Aubearing has been distributing ball and roller bearings to U.S. and international buyers for over twenty years. We specialize in manufacturing application-specific bearings to ensure our products can meet the requirements of our customers in any industry. To determine the bearing accuracy and ABEC rating appropriate for your application, please contact Aubearing.