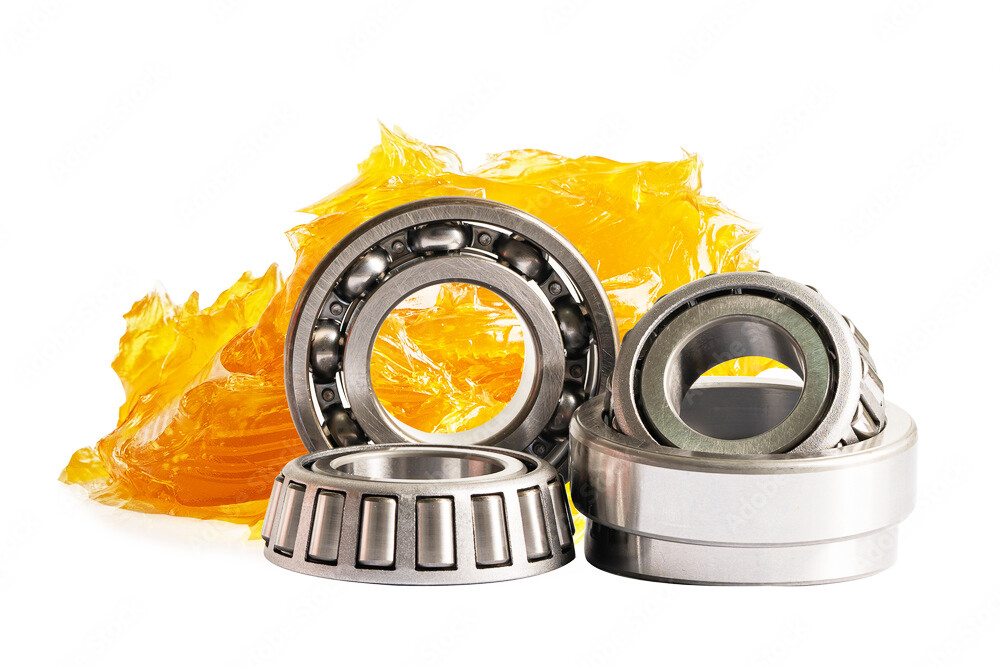
Bearing Manufacturer & Supplier
Specialize in ball bearings, roller bearings, thrust bearings, thin section bearings etc.
The Complete Guide to Bearings
A bearing is a precision part that achieves rotary or linear motion in equipment, and is used to reduce friction between moving parts and increase the speed and efficiency of moving parts. At the same time, bearings are also subjected to various stress loads to support other parts of the machine.
When two metal parts come into contact inside a machine, a lot of friction is created, which in time leads to material wear. Bearings reduce friction and facilitate motion by having two surfaces that roll against each other.
The type of rolling elements in a bearing These surfaces may vary depending on the actual application of the bearing, but generally a bearing consists of two rings or discs with raceways, rolling elements such as rollers or balls Rolling on metal surfaces and outer metal surfaces, and cages that hold the rollers and guide the rolling elements.
Similar to wheels, bearings have two key functions in a system: they transmit motion by allowing components to turn relative to each other, and they transmit force by sliding or rolling. Depending on the bearing construction, the load acting on the bearing can be radial or axial.
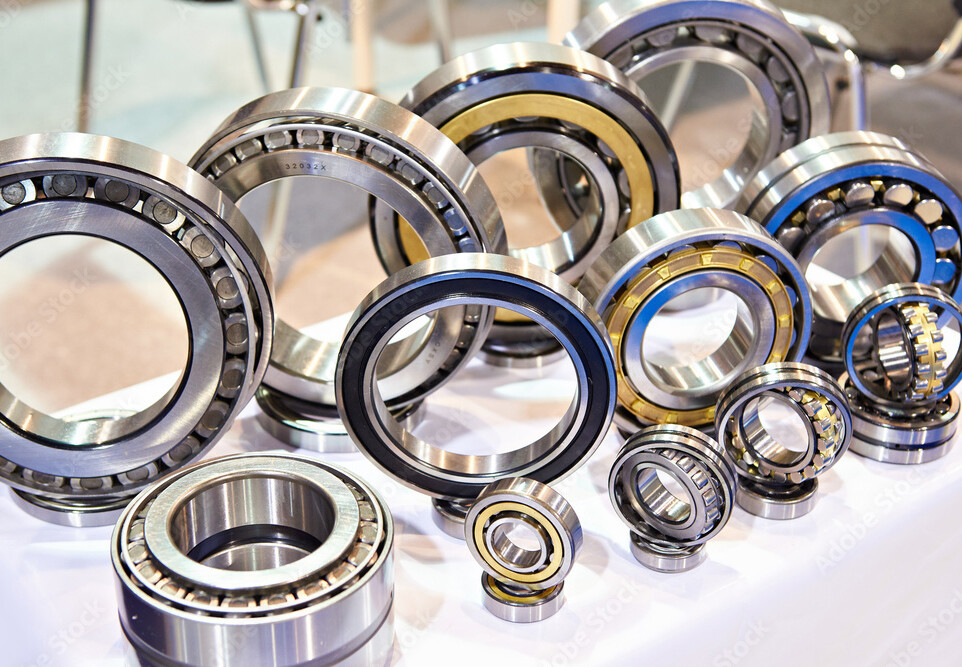
The purpose of this guide is to familiarize you with the most common types of bearings, their design features and modes of operation, the way they handle forces, proper installation and maintenance procedures, and the most common problems that can cause bearings to fail.
Table of Contents
Toggle1. Classification of bearings
Bearings can be classified according to different criteria such as design and mode of operation, permissible movement or direction of load. From a design point of view, bearings can be divided into:
Plain Bearings – Also known as bushing or sleeve bearings, these are the simplest type of bearing. They have a cylindrical shape with no moving parts and are typically used in machines with rotating or sliding shaft assemblies. Plain bearings can be made of metal or plastic and can use a lubricant such as oil or graphite to reduce friction between the shaft and its rotating bore. Typically, they are used for sliding, rotating, oscillating or reciprocating motions.
Types of rolling elements in bearings
Rolling Bearings – These bearings are complex in design and are used to support higher loads. They consist of rolling elements such as balls or cylinders placed between rotating and fixed races. The relative movement of the seat ring causes the movement of the rolling elements, with less friction and less sliding. Rolling bearings are used in rotating applications to transfer loads between machine parts or to guide machine elements such as wheels, axles and shafts. They have low friction, high precision and are capable of high rotational speeds with low noise, low heat and low energy consumption. Bearings are cost-effective, interchangeable and conform to international dimensional standards.
According to the shape of the rolling elements, these bearings can be further divided into ball bearings and roller bearings, and there are various subtypes: cylindrical roller bearings, spherical roller bearings, tapered roller bearings, needle roller bearings and gear bearings.
Fluid Bearings – As the name suggests, these bearings contain a layer of fluid between the bearing surfaces. The fluid can be a pressurized liquid or gas and is distributed in a thin, fast-moving layer between the inner and outer rings. Since the bearing surfaces are not in direct contact, there is no sliding friction in these types of bearings, so the overall friction and wear of these components is much lower than in rolling bearings.
Magnetic Bearings – These bearings use magnetic levitation to support the load, which means there is no surface contact within the bearing. By eliminating friction and material wear, magnetic bearings provide longer life and can support the highest speeds of all bearing types. These components are often the first choice for industrial applications such as oil refining, gas processing, or power generation, but also for high-speed optics and vacuum applications.
We will discuss the most common types of bearings in detail in subsequent chapters of this guide, but for now we will move on to the classification of bearings.
Bearing load direction
Another criterion for classifying bearings is the direction of load they can accommodate. From this point of view, bearings are divided into three categories: radial bearings, thrust bearings and linear bearings.
The contact angle between the bearing and the shaft determines the type of bearing: the contact angle of the radial bearing is below 45°, while the contact angle of the thrust bearing is above 45°.
Linear bearings guide moving parts in a straight line. They are also known as linear guides and come in two main shapes: round and square.
Radial bearings can support loads falling vertically on the shaft. Depending on the design, they can also carry some axial loads in one or both directions. Radial bearings are mounted perpendicular to the axis of the shaft. Plain bearings – also known as journal bearings – are commonly used as radial bearings.
Thrust bearings experience loads parallel to the axis of the bearing, so they are designed to accommodate forces in the same direction as the shaft (axial load).
Depending on their design, these bearings can accommodate purely axial loads in one or both directions, and sometimes some radial loads, but unlike radial bearings, these components cannot withstand very high speeds.
Note: Given that both plain and rolling bearings can transmit loads in both radial and axial directions, the choice of bearing design depends on the application requirements.
2. Plain bearings design and applications
As mentioned earlier, there are two main types of bearing structures: plain bearings and rolling bearings. Let’s see what the most common subtypes of these categories are and what differentiates them in terms of design, material, and application.
Plain bearing
Plain bearings are made from a single bearing surface and have no rolling parts. The design depends on the type of motion required, and the loads the bearing must carry. These machine parts are quieter in operation than rolling bearings, cost less and require less space.
On the other hand, they have higher friction between their surfaces, which leads to higher power consumption of the machine and is prone to damage if impurities get into the lubricant.
Plain bearings can be made of different materials, but they must be durable, low wear and friction, resistant to high temperatures and corrosion. Typically, the bearing surface is made of at least two components, one softer and one harder. Common materials include babbitt (a dual material consisting of a metal housing and a plastic bearing surface), cast iron, bronze, graphite, as well as ceramics and plastics.
Although plain bearings generally require lubrication, they are – at least in theory – capable of operating indefinitely, so they can be used in applications where failure of these components would have serious consequences. Examples include large industrial turbines such as steam turbines in power plants, compressors operating in critical applications, automotive engines, marine applications, etc.
As far as the main types of plain bearings are concerned, there are three important categories from a structural point of view: sleeves or bushings, solid bearings and two-piece plain bearings. Another classification of plain bearings divides them into hydrodynamic and hydrostatic bearings.
Spherical plain bearings
Spherical plain bearings have an inner ring with a convex outer surface and an outer ring with a concave inner surface. The two rings fit together so there are no rolling elements in between. However, depending on the material used for the ring, a coating may be applied to reduce wear.
Bearings with both rings made of steel require maintenance because they have hardened sliding contact surfaces on both rings. They are coated with materials such as molybdenum disulphide, hard chrome or phosphate for increased wear and corrosion resistance. To facilitate relubrication, these bearings have lubrication holes and annular grooves.
Spherical plain bearings (steel on steel) requiring maintenance are suitable for applications involving heavy loads in alternating directions, heavy static loads or shock loads.
Maintenance-free spherical plain bearings are suitable for applications requiring long, maintenance-free bearing life, such as machines and components that are difficult to relubricate. These bearings are usually made of materials such as steel and PTFE composites, PTFE fabrics or copper alloys. The ability to withstand dynamic loads is higher than steel-on-steel bearings, and due to the materials used, these bearings have lower friction.
Depending on the material, the outer ring may be pressed around the inner ring or may or may have radial splits which are held together by screws. Contact surfaces can be coated with chrome, PTFE or phosphate for increased wear and corrosion resistance. In some designs, seals can be added to reduce contamination and extend bearing life.
Spherical plain bearings are used in applications where aligned motion between the shaft and housing must be accommodated. When they can withstand heavy loads and shocks, they are also called heavy-duty spherical plain bearings.
Rod ends
Rod ends consist of an eye head with integral shank, which serves as a housing for spherical plain bearings. Internal threads are usually left-handed or internal, while external threads are external.
The bearing is fixed within the housing, so unlike spherical plain bearings which provide misalignment capability, rod ends do not have this feature. However, they are very easy to install, offer a compact and lightweight design and are good alternatives to traditional enclosure elements. Commonly used in control rods, mechanisms and linkages, rod ends are easy to integrate into a variety of applications.
Like spherical plain bearings, rod ends can be maintenance-free or require maintenance. Steel-on-steel and steel-on-bronze rod ends have good wear-resistant sliding surfaces, but require regular lubrication. They are suitable for applications involving heavy alternating loads. In the case of maintenance-free rod ends, they are usually made of materials such as steel and PTFE composite or steel and PTFE fabric, in which case the friction is much lower. These bearings are suitable for applications requiring long bearing life, difficult to relubricate and constant load direction.
Bushing
The most common type of plain bearing is the bushing, which is a separate element inserted into the housing to provide a bearing surface. The shape is usually cylindrical, and the standard configuration is sleeve bearing and flange bearing. Sleeve bearings have straight inner and outer surfaces and the same diameter, while flanged bearings have a flange at one end that is used to locate components in the assembly and sometimes to cover mounting holes and hold the bearing in place.
In addition, plain bearings can also be lined, in which case different materials are used for the inner and outer surfaces. Bushings are used for linear motion, oscillating motion, and rotary motion, straight bushings are suitable for bearing radial loads, and flanged bushings can bear radial and axial loads in one direction.
Unlike rolling bearings, plain bearings (including bushings) function by sliding. Their construction can be single or multilayered, depending on the required strength. Plain bearings are made from a variety of materials and are usually self-lubricating, a specificity that ensures smoother running and greater durability.
The most common materials for bushings are cast and machined metals, ceramics, filament wound composites, stabilized polymer materials, and combinations of these materials. As for lubricants, both solids and liquids can be used, but solid lubricants can usually operate at higher temperatures than oil- or grease-based lubricants. For some applications, the bushing will run dry without additional lubrication.
Sleeves can be solid, split or snapped in construction. The difference between solid and split bushings (wrapped bearing) is that the latter has a cutout along its length to facilitate installation. Snap bearings are similar to split bearings, but have snaps in the cutouts where the parts are joined.
Typically, rather than being pressed into a housing, linear bushings are secured using retaining rings or rings molded into the outside diameter of the bushing. When bushings are used similarly to washers, they are called thrust washers. However, there is a difference between them: Unlike standard shims or washers, thrust washers must carry loads and should not wear down over time.
Self-lubricating bushing
A special type of bushing is a self-lubricating bushing in which a solid lubricating film is formed inside the bearing by the transfer of a small amount of surface material. This occurs during the initial run-in period of the bearing, but the amount of material transferred is small enough that it does not affect the function and load handling characteristics of the bearing.
The film is in contact with all moving parts of the equipment, lubricating and protecting them, thus helping to extend the life of the bearings. By doing so, it eliminates the need for additional lubrication and reduces maintenance costs. Due to the thinner walls, self-lubricating bushings have the advantage of being lighter in weight and having excellent wear resistance. They can withstand high loads and have a simplified design, which is economical in the long run.
Two-piece plain bearing
As referred to as full bearings, two-piece plain bearings are used in industrial machinery where larger diameters are required, such as crankshaft bearings. They consist of two parts called shells that are held in place using different mechanisms.
If the shells are large and thick, you can use button stops or dowels to position them. The button stop is screwed onto the housing, and the dowels connect the two housings together. Another possibility is to use lugs on the edge of the parting line relative to the notch in the housing to prevent the housing from moving after installation.
Rolling bearings have lower friction and lower lubrication requirements than plain bearings. Their function is to support and guide rotating and oscillating machine elements, such as shafts, wheels or shafts, and to transfer loads between the different parts of the assembly.
They come in standard sizes, are easy and cost-effective to replace. By minimizing friction and enabling high rotational speeds, these bearings reduce heat and energy consumption, increasing process efficiency.
Anti-friction bearings usually consist of two raceways – an inner and an outer ring, the rolling elements can be balls or rollers, and a cage that separates the rolling elements at specific intervals and holds them in place within the raceway. position while enabling them to rotate freely.
The raceways are the part of the bearing that support the loads applied to the equipment. When a bearing is installed in an assembly, the inner ring of the bearing fits around the shaft or axle and the outer ring fits on the housing.
The ring is usually made of special chromium alloy steel with high purity and high hardness, which is quenched, ground and honed. Stainless steel, ceramic and plastic materials can also be used, especially in areas where lighter weight may be required, such as the automotive industry. Still, these materials cannot withstand the same temperatures or loads as steel.
Cage_holds the rolling elements in place and prevents them from falling out while spinning. Due to the design of the bearing, the load does not act directly on the cage. The component can be manufactured using different methods, but common types include stamped, formed and machined cages. As for materials, common choices include steel, plastic, and brass.
Finally, rolling elements are divided into two main groups, which also distinguish the basic types of rolling bearings: ball elements in ball bearings and rollers in roller bearings. For balls, the contact with the raceway is at a specific point, while for rollers, the contact surface is slightly larger and linear.
These characteristics make ball bearings suitable for applications requiring higher speeds because the small contact area provides low rolling friction. However, ball bearings have limited load carrying capacity, so in applications involving heavier loads, roller bearings may be preferred. Roller bearings have higher friction and better load carrying capacity due to greater contact with the raceways, but at lower speeds.
The rollers can be cylindrical, conical, spherical or needle-shaped and, like the balls, are made of high-purity chromium-alloy steel. Sometimes, special materials such as ceramics or plastics can also be used.
Rolling bearings and ball bearings
Ball Bearings: Ball bearings consist of balls that form contact points with the ring raceways. As the load on the bearing increases, it causes the contact area of the bearing to become oval. Due to the small contact area, ball bearings can accommodate high speeds, but their load carrying capacity is limited by their design.
Rolling bearings: In rolling bearings, the rollers form a line of contact with the annular raceway. An increase in load causes the contact line to become rectangular, see Figure 2. Because of the larger contact area, it can carry heavier loads, but it will spin slowly than a similarly sized ball bearing.
Inner Ring and Raceway (A): The inner ring is a smaller ring on the shaft. It is located in the outer raceway (D).
On roller bearings, the raceways are flat or tapered with flanges that hold the rollers in place.
On the ball bearing, cut a groove in its outer circumference.
Rolling elements (B): The bearing is free to rotate due to balls or rollers fixed between the inner and outer rings. If they are not present, the friction between the races can quickly damage the bearing. Balls and rollers in bearings are manufactured to exact symmetrical specifications, as asymmetrical rolling elements degrade bearing performance. Rolling elements are highly dependent on their surface quality as it affects how smoothly they rotate. Friction generates heat, shortening bearing life and increasing bearing noise.
Bearing cage (C): The bearing cage holds the balls or rollers between the inner and outer raceways. This ensures that the balls/rollers can spin freely, but they maintain the pitch.
Outer Raceway (D): The bearing consists of an outer raceway and an inner raceway (ring) that contains balls or rollers.
On roller bearings, the outer raceway is flat, spherical, or tapered with flanges that hold the rollers in place.
On the ball bearings, cut a groove along the inner circumference of the raceway to hold the balls in place.
Complete Bearing (E): When all the parts are assembled together, they make up the bearing. Rolling elements can be exposed, as shown in Figure 3 (E), and these require proper lubrication to function properly. Bearings can be equipped with seals, which protect the rolling elements from the environment and are already lubricated.
When discussing bearings, it is important to discuss loads. Load is the force acting on the bearing. A loaded bearing currently has a force acting on it, while an unloaded bearing does not. Various load factors need to be considered, such as load direction, load type, and load conditions.
Radial Load: A radial load is any load that acts at right angles to the axis of the bearing.
Axial Load: An axial or thrust load is any load acting along the axis of the bearing.
Combined Load: A combined load is a combination of radial and axial load components.
Radial Load
Axial Load
Combined Load
load type
Dynamic Loads: These are the rotational forces acting on the bearing as it rotates. These loads lead to bearing wear.
Static loads: Continuously high or intermittent peak loads. Under static load, the material strength of the bearing is the limiting factor.
load condition
load condition
Constant load: Under constant load, the load direction does not change, and the same part of the bearing is continuously loaded, also known as the load zone.
Alternating Loading: Under alternating loading, areas of the bearing adjacent to each other are alternately loaded and unloaded.
These characteristics make ball bearings suitable for applications requiring higher speeds because the small contact area provides low rolling friction. However, ball bearings have limited load carrying capacity, so in applications involving heavier loads, roller bearings may be preferred. Roller bearings have higher friction and better load carrying capacity due to greater contact with the raceways, but at lower speeds.
The rollers can be cylindrical, conical, spherical or needle-shaped and, like the balls, are made of high-purity chromium-alloy steel. Sometimes, special materials such as ceramics or plastics can also be used.
Ball Bearings
According to the configuration of the rings, ball bearings are divided into two categories: deep groove ball bearings and angular contact ball bearings. Both types can withstand radial force and axial force, so they can be divided into radial ball bearings and thrust ball bearings.
Another classification criterion includes the number of rolling rows – single, double or quadruple, and the separation or non-separation between the rings.
Considering all these criteria, we can distinguish several ball bearing models:
Single row deep groove ball bearings,
Single row angular contact ball bearings,
Double row angular contact ball bearings,
Four point contact ball bearings,
Self-aligning ball bearings,
Thrust ball bearings, etc.
Ball bearings are used in a variety of applications, from simple devices like skateboards to complex machines or engines. For example, in the aerospace industry, bearings are used in gearboxes, engines and pulleys. Materials for these bearings include not only steel but also special ceramics such as silicon nitride or titanium carbide coated 440C stainless steel.
Other common applications for ball bearings include electric motors and generators, pumps and compressors, blowers, fans, gearboxes and drives, turbines, agricultural machinery, conveying systems, oilfield machinery, robotics, industrial valves, and .
Deep Groove Ball Bearings
The balls of deep groove ball bearings are held in place by deep grooves in the raceways and can carry radial and axial loads. They are suitable for very high speeds, offer low friction, produce minimal noise and vibration, are easy to install, and require less maintenance than other types of bearings. Ball bearings are the most common type of rolling bearings, of which deep groove ball bearings are the most used.
In the AUB design, the inner ring is initially placed in an eccentric position relative to the outer ring, and the balls are inserted into the bearing through the gap formed between the two rings.
Once they are evenly distributed in the bearing assembly, the rings become concentric, so the cage can also be added to the bearing. As mentioned earlier, the role of the cage is not to support the load, but to keep the ball in place during operation.
The inner ring is usually fixed on the rotating shaft, while the outer ring is mounted on the bearing housing. When a load acts on the bearing housing, the load is transferred from the outer ring to the balls, and from the balls to the inner ring. Deep groove ball bearings are suitable for applications involving high loads and high speeds.
In the slot-fill design, balls can be assembled between the two rings, so the radial load capacity of the bearing is higher than that of Conrad bearings. However, the axial load carrying capacity of these components is not very good.
Deep groove ball bearings can be used as open bearings and are easy to lubricate, but the disadvantage is that the balls will accumulate dust. Another configuration is a bearing with metal shields and/or seals where contamination is moderate. Bearings with shields or seals on both sides are lubricated for life and therefore require little maintenance.
Bearings with shields or seals are also known as covered bearings. Although the design may vary, the seals are usually mounted on the outer ring and can take the form of non-contacting seals, low friction seals or shields .
Boots are used in applications where the inner ring rotates and is mounted on the outer ring, creating a narrow gap with the inner ring. They keep out dust and dirt and are usually made of steel plates. Seals are usually effective than boots because they have less clearance from the inner ring. They can run at shield-like speeds or higher and are made of steel plate reinforced NBR or similar for wear resistance.
As for the cages in deep groove ball bearings, they also vary in construction, but some common designs are strip cages made of steel or brass sheets, brass sheet or steel riveted cages, machined yellow Copper cage or snap-fit cage made of steel polyamide 66.
In conclusion, deep groove ball bearings are versatile devices suitable for high and very high speeds, operating robustly and requiring little maintenance. They can accommodate radial loads and axial loads in both directions, and in single row designs, deep groove ball bearings are the most widely used bearing type.
Angular contact ball bearings
Angular contact ball bearings are also available in various designs and are available as single or double row, pair or four point contact bearings. Their construction enables these elements to withstand axial and radial forces, so they are suitable for high load and high speed applications.
Unlike deep groove ball bearings, angular bearings use axially asymmetrical races, which create a contact angle between the ring and the balls when the bearing is in use. A peculiarity of these bearings is that one or both rings – usually the outer ring – have one shoulder higher than the other.
These bearings work well when fitted with thrust loads. The contact angle typically varies between 10 and 45 degrees, and as this angle increases, thrust capacity also increases.
Angular contact bearings are available in different design styles, with seals or shields. Not only do they prevent contamination, they also act as a retainer for lubricants. These bearings can be made of stainless steel, ceramic hybrid or plastic and can be plated with chrome, cadmium or other materials. In addition, they can be pre-lubricated, re-lubricated or have solid lubrication capabilities.
Single Row Angular Contact Ball Bearings
They can only bear axial load in one direction, which is why single row angular contact ball bearings are usually installed by placing two single row angular contact ball bearings back to back, face to face or in series. Therefore, multiple directions of force can be accommodated. The bearings are locked in place with the help of locking rings to prevent sliding along the shaft.
Back-to-back: By mounting the bearings in this manner, they can accommodate radial and axial loads in any direction. Because the distance between the center of the bearing and the load point is larger than other installation methods, it can withstand large instantaneous and alternating load forces.
Face-to-face: With this mounting sequence, the bearings can withstand radial and axial loads in either direction. However, due to this mounting method, the distance between the bearing center and the loading point is small, so the instantaneous and alternating force capacity is low.
Tandem: Tandem installation can bear one-way axial load and radial load. Since the load on the shaft is carried by two bearings, it can withstand heavy axial loads.
Double Row Angular Contact Ball Bearings
A double row angular contact ball bearing is similar to two single row angular contact ball bearings arranged back to back, but requires less axial space. In addition to radial and axial loads, they are also able to absorb tilting moments.
Self-aligning ball bearings are used when the application is likely to suffer from misalignment or shaft misalignment. It has two rows of balls sharing the outer spherical raceway, while the inner ring has two corner contact deep groove raceways. Since the balls remain in place in the inner raceway but have some freedom of movement in the outer raceway, they can operate even if the bearing is misaligned with the shaft. However, they are not suitable for high load applications.
Thrust ball bearing
Thrust ball bearings are used to accommodate axial loads. There are two key designs to choose from: unidirectional and bidirectional.
One-way thrust ball bearings consist of two rings (called the shaft and housing washer) and a ball and cage assembly. They can only take axial loads in one direction, depending on the position of the flange on the inner race, the outer race, or both raceways.
Dual direction thrust ball bearings consist of three washers and two ball and cage assemblies. The shaft washer separates the ball and cage assembly. These bearings are designed for axial loads and not for radial loads. They can withstand axial loads in both directions.
Roller bearing
Roller bearings are divided into different types according to the shape of the rolling elements. The main categories of roller bearings are cylindrical bearings, needle roller bearings, tapered bearings and spherical roller bearings.
Cylindrical roller bearings are designed to accommodate heavy radial loads and moderate thrust loads, they contain cylindrical rollers designed to reduce stress concentrations.
The rollers are in line contact with the raceways and are usually made of steel. Materials such as polyamide or brass can also be used for cylindrical roller bearings with cages.
These types of bearings have low friction and long service life, low noise and low heat generation, and can be used in applications involving high speeds. Cylindrical roller bearings come in different styles, with names that vary by manufacturer.
These bearings can be classified according to the number of roller rows. From this point of view, these machine parts are divided into single row cylindrical roller bearings, double row and four row cylindrical roller bearings. In single row models, the inner and outer rings are separable for all models, which means that the inner ring with rollers and cage assembly can be mounted independently of the outer ring.
Depending on the design, the rings can be ribbed or not so they can move axially relative to each other. There are also models without cages, in which case they are equipped with complete rollers for higher loads but lower speeds.
Cylindrical roller bearings are commonly used in industries such as petroleum production, power generation, mining, construction equipment, gears and drives, electric motors, blowers, fans as well as pumps, machine tools and rolling mills.
Spherical roller bearings are suitable for low to medium speed applications and can accommodate heavy loads. Because they are self-aligning, they are used in applications with severe misalignment, vibration and shock, and contaminated environments.
These bearings are usually made of alloy steel, brass, polyamide or mild steel and are also available in chrome plated versions.
The axis of rotation supported in the bore of the inner ring may be misaligned relative to the outer ring, this particularity is possible thanks to the spherical inner shape of the outer ring and the shape of the rollers, which are not actually spherical, but is cylindrical.
Rugged and designed for heavy radial loads, these bearings offer long life and low friction. They are commonly used in applications such as gearboxes, pumps, mechanical fans and blowers, wind turbines, marine propulsion and offshore drilling, mining and construction equipment.
In terms of the design of these bearings, they have an inner ring with two raceways inclined at an angle to the bearing axis, a cage and an outer ring with a common spherical raceway. The spherical rollers are most often arranged in two rows, a design that enables the bearings to withstand very heavy radial and axial loads.
Spherical roller bearings can operate at lower temperatures than other bearings and they have standardized dimensions, the international standard for these devices is ISO 15:1998. Common series are 21300, 22200, 22300, 23000, 23100, 23200, etc.
Spherical bearings are available with seals and are delivered lubricated. This design reduces grease, keeps out dirt, dust and other contaminants, and simplifies maintenance and extends bearing life.
Similar to spherical roller bearings, spherical roller thrust bearings are designed to allow angular misalignment and low-friction rotation, and are suitable for radial loads and heavy axial loads in one direction.
These bearings consist of a shaft ring equivalent to an inner ring, a raceway equivalent to an outer ring, asymmetrical rollers and a cage. External dimensions are standardized by standard ISP 104:2002, the most common series include 292, 293 and 294.
Just like spherical roller bearings, thrust bearings can be made of different materials such as chrome steel, brass, steel plate, etc. These bearings are used in medium speed applications, some common applications include water turbines, gearboxes, cranes, marine propulsion and offshore drilling, injection molding extruders, and pulp and paper processing equipment.
In needle roller bearings, the rolling elements are thin cylinders shaped like needles. This particular design, in which the length of the rollers is several times greater than the diameter, not only makes them stand out from other types of bearings, but also gives needle roller bearings their significant load-carrying capacity.
Needle bearings are used to reduce friction on rotating surfaces within assemblies, have a small cross-sectional height, are thinner than other bearings, and require less clearance between the shaft and surrounding components.
With higher stiffness and lower inertial forces, these bearings are ideal for applications with oscillating motion and perform well in harsh conditions. They also help reduce the size and weight of machine designs and can be used as a replacement for plain bearings.
Needle roller bearings are the smallest and lightest of the roller bearing family and are widely used in components such as compressors, transmissions, rocker arm pivots or pumps in the automotive industry. These bearings are also commonly used in agricultural applications and construction equipment, portable power tools and household appliances.
When it comes to different types of needle roller bearings, depending on the direction of the load, these bearings are classified as radial bearings and thrust bearings. Thrust bearings include thrust needle roller bearings, while radial bearings include drawn cup bearings, solid needle roller bearings, radial cage needle rollers, track rollers, heavy machined needle roller bearings, and combined radial and thrust bearings.
Solid needle roller bearings have a strong, integral rib on the outer ring to keep the rollers in place and ensure high operating speeds. The rings are heat treated and precision ground to withstand high shock loads. The cage is also treated for increased wear resistance and rigidity, and if required, humps can be applied to reduce the load on the roller edges. The outer ring has lubricating holes or grooves for easy replacement of lubricant and prolonging the service life of the bearing.
Radial cage needle rollers or needle roller and cage assemblies have no inner or outer rings, they are designed with only one set of needle rollers held in place by a cage. This cage provides inward and outward retention of the rolling elements, ensuring maximum strength and precise guidance of the rollers even at high speeds.
The needle roller section of the radial cage has small cross-section and high load capacity, and its design creates good lubrication conditions. Cages can be made of steel or fiberglass reinforced polymer material and, if required, ridges can be applied to the ends of the rollers to prevent stress concentrations at the edges. Common applications include planetary gears, idlers and connecting rods.
Drawn cup needle roller bearings are available in cage and full complement versions, both of which have outer rings made of alloy steel sheets. The housing is precisely drawn into a cup shape and case hardened by pressing to ensure tight line contact with the rollers. This construction gives the bearing a high load carrying capacity and also makes it an economical solution since no additional machining of the housing is required.
The low height of drawn cup needle roller bearings makes them suitable for compact and lightweight machine designs. The curved portion of the outer ring keeps the rollers in place and prevents dust and dirt from entering the bearing, while also ensuring good bearing lubrication. Another advantage of this design is that, if the shaft is of the right stiffness and size, the bearing does not require an inner ring, thus saving space in the radial direction.
Drawn cup needle roller bearings with full complement can carry loads equal to or higher than ball bearings and roller bearings with equivalent outer diameters, and are suitable for stationary, low-speed rotating and oscillating conditions. They can be used in low durometer housings and have the greatest load capacity when the rollers are greased in place prior to assembly because the rollers have the greatest possible length.
In the case of drawn cup cage bearings, they can also be used in housings that are less rigid but have a lower load carrying capacity than full complement bearings. Nevertheless, they are still very suitable for high speed and shaft misalignment applications. The surface of the cage is hardened to improve wear resistance and rigidity while reducing frictional torque.
Since the cage creates some extra space for lubricant storage, these needle roller bearings run smoothly and have long grease life. Common applications for drawn cup needle roller bearings include gear pumps, general gearbox shaft supports, guide bearings and pulley supports.
Track rollers have a thick-walled outer ring that runs directly on the track to withstand high loads while minimizing deformation, impact and bending stress. These are commonly used in machine rails, mast rollers and cam followers, also known as cam followers.
The outer ring is usually made of high-carbon chromium steel, which is not easy to deform and has lubrication holes. If desired, ridges can be applied to the rollers to prevent overloading at the edges. Additionally, thrust washers can be integrated into the design to enhance drag.
These needle roller bearings are available in two main designs for different mounting arrangements: the yoke type, for straddle or clevis mounting, and the integral stud type, for cantilever mounting. Stud type bearings are available with or without lip contact seals and boots, while yoke type bearings are available with radial needle roller and cage assemblies, or with full complement cylindrical rollers or needle rollers.
Thrust needle roller bearings consist of a set of needle rollers held together by a cage. They have a small cross-section, and the cage is precisely pressed from two steel plates, which guide the rollers accurately and increase the rigidity and wear resistance of the device. These bearings transfer thrust loads between two rotating objects while reducing friction.
Combined radial and thrust bearings consist of thrust ball or roller bearings and radial needle bearings. Some of these are similar to drawn cup bearings, but with the addition of thrust bearings. These units are designed to withstand high speeds and high axial loads in confined spaces and can replace ordinary thrust washers when excellent load capacity and friction characteristics are required. A common application is automatic transmissions.
Tapered roller bearings consist of an inner or inner ring, an outer or outer ring, a cage and rollers that are contoured to distribute loads evenly. These bearings use tapered rollers guided by ribs on the cone and are able to accommodate high radial and axial loads in one direction.
The raceways of the inner and outer rings are conical segments, and the rollers are tapered. This design makes the cones move coaxially, and there is no slippage between the raceways and the outer diameter of the rollers. Due to their shape, tapered roller bearings can accommodate higher loads than spherical ball bearings.
An inner ring flange that keeps the rollers stable prevents the rollers from popping out. The inner ring, rollers and cage form a non-separable conical assembly, while the outer ring is cup-shaped and separable. The inner ring assembly and outer ring can be installed independently, and for two opposing bearings, proper internal clearance can be obtained by adjusting the axial distance between these assemblies.
According to different contact angles, tapered roller bearings can be divided into three types: normal angle, medium angle and steep angle. Further, according to the number of rows, they can be divided into:
Single row tapered roller bearings have an outer ring and an inner ring assembly. Included in this category are the TS and TSF series (single row with flanged outer ring).
Double row tapered roller bearings using a double cup (outer ring) and two single tapered roller assemblies (inner ring). The TDO series is included here.
Double row tapered roller bearings, using a double inner ring assembly (double inner ring) and two single outer rings (outer ring). This includes the TDI and TDIT series.
Four-row tapered roller bearings, using a combination of two and single components, such as two TDI inner rings, two TS outer rings and a TDO outer ring with outer ring or inner ring spacer. The TQO series is included here.
Single row bearings have a higher thrust load capacity, while double row bearings have a greater radial load capacity and can withstand thrust loads in both directions. The standard cage is a pin design for high loads and speeds. Stamped steel cages are generally used. In many applications, these bearings are used back-to-back to support axial forces in either direction.
In addition, tapered roller bearings are also available in metric series:
Metric single row tapered roller bearings to ISO 355:2007. These are suitable for gearboxes, pumps and conveyors used in power industry, oil and gas, wind energy, food and beverage or pulp and paper industry applications. Additionally, they are used in drive trains, gear drives and axles in the construction, automotive and mining industries.
Metric double row tapered roller bearings consist of two single row bearings with individually matched spacers. These are used in applications requiring high load capacity and where the shaft must be positioned axially with a specific clearance or preload in both directions. The outer ring spacer has lubrication holes. These bearings are suitable for applications such as gear drives and transmissions, coal handlers or cranes.
Common applications for tapered roller bearings include automotive and wheel bearings, agricultural, construction and mining equipment, gearboxes, engine motors and reducers, wind turbines, axle systems and drive shafts.
Special bearing designations
Various codes and designations exist to identify various bearing designs and design features. These codes and designations include designations for bearings with a tapered bore (designated letter K in SKF bearings), reinforced bearing designations which usually use the letter E, and . Unfortunately, not all manufacturers use the same suffixes and design features.
One area that is generally the same worldwide is the different designations of flange positions on bearings. These flanges are designed to handle radial loads applied to the bearings.
NU: These bearings have two machined flanges on the outer raceway, but no flange on the inner raceway. Rolling elements and cages are assembled in the outer raceway. Since the inner raceway has no flange, this bearing cannot withstand thrust loads.
N: The inner ring of this type of bearing has two ribs, the outer ring has no ribs, and the inner ring has rollers and cages. The outer raceway of this bearing has no ribs and therefore cannot withstand thrust loads.
NJ: One machined flange on one side of the inner raceway and two flanges on the outer raceway. The roller and cage assemblies are located in the outer raceway. Because the inner raceway has an integral flange, this bearing can accommodate axial loads and limited thrust loads.
NUP: This type of bearing is similar to an NJ type bearing, but has a unique raceway, often called a thrust ring. Thrust rings are installed on the non-flange side of the inner raceway to support axial loads in both directions. The thrust ring protrudes from the bearing on one side, so the diameter of the inner raceway is slightly larger than that of the outer raceway.
Rolling bearing selection criteria
The following are rolling bearing selection criteria to consider when applying:
Available space: The bore diameter of a bearing is one of the main dimensions and is usually determined by the design of the machine and its shaft diameter. Small diameter shafts can be fitted with any type of ball bearing. In addition to deep groove ball bearings, needle roller bearings can also be used. Bearings for large diameter shafts include cylindrical, tapered, spherical and deep groove ball bearings. Where radial space is limited, thin section bearings are preferred.
Load: The size of the bearing is usually determined by the magnitude of the load. In general, roller bearings carry heavier loads than ball bearings of similar size, and bearings with complete rolling elements can support heavier loads than cage bearings. Typically, ball bearings can accommodate light to moderate loads. Bearings with rollers are usually a suitable choice when the bearing must carry heavy loads or when the shaft diameter is large.
Misalignment: Misalignment is caused by shaft bending under load, bearing housings not machined to the same height, or bearings spaced too far apart. Deep groove ball bearings, like cylindrical roller bearings, cannot tolerate any or only small misalignments unless stressed. Self-aligning bearings, such as spherical roller bearings and spherical roller thrust bearings, can adjust for misalignment and compensate for initial misalignment caused by machining and installation errors.
Precision: Arrangements requiring high running accuracy and applications requiring very high speeds require bearings with higher precision. This is often the case in medical and aerospace applications. High precision bearings are usually manufactured to deep groove ball bearing or angular contact bearing standards, but with much tighter tolerances than standard bearings.
Speed: The speed of rolling bearings is limited by the allowable operating temperature. For high-speed operation, bearings with low friction and low internal heat generation are most suitable. By its design, thrust bearings cannot withstand speeds as fast as radial bearings.
Quiet operation: Depending on the application, such as small electric motors for household appliances or office machines, the noise generated during operation can affect bearing selection. A special type of deep groove ball bearing with a brass cage is produced for these applications. These bearings have space between the raceways, which allows lubricant to be placed inside the bearing, reducing noise levels.
Stiffness: The stiffness of a rolling bearing depends on the magnitude of its elastic deformation under load. Since the deformation is usually small, it can usually be ignored. The stiffness of the main shaft bearing arrangement or pinion bearing arrangement is critical. Due to the contact conditions between rolling elements and raceways, roller bearings have higher stiffness than ball bearings. However, this deformation does act as a lubricant.
Mounting and dismounting: When bearings with cylindrical bores are of a separable design, they can be mounted and dismounted efficiently, especially if both rings require an interference fit. If frequent mounting and dismounting is required, it is best to use a separable bearing because each bearing ring can be mounted independently. Bearings with a tapered bore can be easily mounted on cylindrical housings or tapered journals using adapters or withdrawal sleeves.
4. Bearing lubrication and maintenance
Proper installation and adjustment play a vital role in bearing performance and life, as do lubricants. In most cases, bearing failure is not due to improper installation or manufacturing defects, but due to lack of lubricant, improper selection or contamination of lubricant.
Lubricants, whether oil or grease, distribute between and separate the moving parts of a bearing assembly, reducing friction and preventing wear. Depending on the operating conditions and the lubricant chosen, a protective film forms on the bearing elements which also serves to dissipate frictional heat, protect the bearing from deterioration and protect against moisture, corrosion and contamination.
A properly selected lubricant has the right additives and viscosity to achieve all of the above goals. The most common lubricants are oil and grease, with the use of one or the other depending on the speed of the application and the amount of load on the bearing.
For oils, the most important property is viscosity and the right product depends on the temperature and speed of application. If an oil with insufficient viscosity is used, the two rotating surfaces will come into contact, which will not only cause wear, but also generate contact heat and lead to rapid deterioration of the bearing elements.
The most common bearing oils are petroleum based oils and synthetic oils such as silicones, fluorinated compounds, diesters or PAOs. Oils are often chosen for bearings with higher speed capabilities and higher operating temperatures because they can remove heat from the bearing. In some cases, such as miniature bearings, oil-based lubricants only need to be applied once during the life of the bearing. In assemblies using larger bearings, relubrication may be required as part of regular machine maintenance cycles.
For grease-based lubricants, the most important characteristics are the temperature range, penetration level, stiffness and viscosity of the base oil. Greases consist of an oil base to which thickeners have been added, the most common being organic and inorganic compounds, and metal soaps such as sodium, aluminum, calcium or lithium. Additives with anti-oxidation, anti-corrosion and anti-wear properties can also be added to enhance the performance of the lubricant.
Alternatively, a solid non-fluid film can be applied to bearing elements like a coating to reduce friction and prevent wear. These films are used in special cases where oil or grease cannot survive and they include options such as graphite, silver, PTFE or gold films. For example, in applications with extreme temperatures or radiation, oil- or grease-based lubricants may not provide adequate protection, so a durable lubricant such as a solid film may be required.
Grease is a good choice for lubricating bearings in most cases. cost-effective than oil, grease is easily retained in bearing assemblies and is easy to apply. However, it is not suitable for applications requiring heat removal by circulating oil, nor for gearboxes requiring lubricating oil.
Also, if operating conditions require re-lubricating bearings with grease at too short intervals, which becomes too time-consuming and expensive, or if removing or cleaning grease becomes too expensive and difficult to handle, it is best to choose a lubrication Oil.
Bearing lubrication level and relubrication
After selecting a lubricant, an important aspect is to apply the correct amount on the bearing. Overheating and bearing damage can result if too much lubricant is used. The speed, load and noise level of the application will all be affected by the amount of lubricant used.
Depending on the type of bearing and lubricant selected and the application, the manufacturer may recommend different levels of lubrication, expressed as a percentage. Lubricant enters the interior of the bearing and the free space of the housing. This space is important because it allows heat to dissipate away from the contact areas of the bearing, so if you add too much grease, it can cause overheating and premature bearing failure.
For this reason, a common recommendation is to fill 20-40% of the free space inside the bearing, with smaller percentages typically specified for high speed, low torque applications and higher percentages typically specified for low speed, high load applications. For housings, filling 70%-100% of the free space is also acceptable if the application involves low speeds and a high risk of contamination.
Remember that the initial fill level is also affected by the relubrication method chosen. The common methods of bearing relubrication are manual relubrication, automatic and continuous relubrication.
Manual relubrication is convenient for uninterrupted operation.
Automatic relubrication avoids over- and under-lubrication and is typically used for components where multiple points or difficult-to-access locations must be lubricated. Also, it is the first choice for operating equipment remotely and without maintenance personnel.
Continuous lubrication is used in applications where relubrication intervals are too short because of adverse effects of contamination. In this case, the initial filling of the housing will be 70%-100%, depending on the operating conditions.
Bearing maintenance tips
Proper handling and maintenance of bearings will extend their life and optimize performance. Use this basic checklist to reduce maintenance time, labor and costs.
Bearing Handling: Handle bearings with care to avoid scratching surfaces. Always handle them with clean, dry hands, or use clean canvas gloves. Do not touch the bearings with greasy or wet hands, as this will quickly lead to contamination.
Bearing storage: Wrap the bearings with oil-proof paper and store them in a cool, clean, low-humidity, dust-free, vibration- and shock-free environment. After handling bearings, place them on a clean and dry surface to avoid contamination. Do not remove the bearing from its original packaging until it is time to install it, and store it flat rather than upright.
Cleaning Bearings: Always use an uncontaminated solvent or flushing oil, and avoid wiping the bearings with cotton wool or dirty rags. Use a separate container for cleaning and final flushing of used bearings.
Bearing Installation: Use proper techniques and tools to install bearings. About 16% of bearing failures are caused by improper installation, so make sure to avoid installations that are too loose or too tight. Before installation, check whether all parts are clean and undamaged, and whether the lubricant is selected correctly. If the bearings come straight from the packaging, do not wash the bearings prior to installation.
Do not hammer or apply direct force to the bearing or its outer race as this can cause damage and misalignment of components. For small and medium-sized bearings, cold mounting or mechanical mounting is generally recommended. Thermal mounting is usually suitable for relatively large bearings, while for very large bearings hydraulic mounting may be recommended.
Use the right tools: Specialized tools are available for installing and removing bearings – bearing pullers, assembly tool kits, oiler tools, induction heaters and hydraulic nuts. All are custom made to ensure proper fit and a smooth fit to minimize the risk of bearing damage.
Check bearings: To prevent bearing failure, it is necessary to check them during and after operation. On-the-fly inspections to check for temperature, noise and vibration, and check lubricants to determine if they need to be replaced or replenished. After running, check the bearing and its components to see if there is any change. The final chapter of this guide discusses common causes of bearing failure and their solutions.
Bearings can usually be used to the end of rolling fatigue life, but can also fail prematurely due to improper assembly, installation, lubrication or handling. The main failure modes and their sub-causes are described in the ISO 15243 standard and are based on visible damage to the rolling element contact surfaces or other functional surfaces of the bearing.
These failure modes include:
Fatigue, which can be surface-induced or sub-surface-induced
Wear, including abrasive and adhesive wear
Corrosion, including moisture corrosion and fretting corrosion (sub-causes are fretting corrosion and false brinelling)
Galvanic corrosion, including excessive voltage and current leakage
Plastic deformation, including overloading, debris indentation and handling indentation
Fracture and cracking, including forced fracture, fatigue fracture and thermal cracking
Fatigue is caused by repeated stress on the contact surface between the rolling elements and the raceway, and leads to changes in the material structure. It manifests as flaking or spalling and is primarily surface induced, the cause of this type of damage is usually insufficient lubrication. Subsurface-induced fatigue is rare and occurs after prolonged operation. To prevent such damage, grease type and condition as well as sealing and loading conditions should be checked and adjusted as necessary.
Wear occurs when fine foreign material gets into the bearing assembly. Such material can be sand or fine metal particles from grinding or machining, as well as metal particles from gears wear. These foreign particles can cause internal clearance and misalignment, reducing the life of the bearing. A solution for preventing this type of damage is to add seals to the bearing assembly, or to use bearing units with polymer cages. Also, changing the type of grease might help.
Corrosion occurs when water or corrosive agents get inside the bearing units in large quantities. When this happens, the lubricant can no longer provide proper protection, therefore rust forms. Frictional corrosion happens when there are micro movements between the bearing surfaces, under certain conditions, for example when there is movement between a bearing ring and a shaft. This causes small particles to become detached from the surface. When exposed to oxygen, the particles oxidize, leading to bearing damage.
Electrical erosion appears when electric current passes through the bearing. It can be caused by earth return devices which aren’t working properly or by earth connections which are improperly done when welding.
Plastic deformation can be caused by different factors, such as overload as a result of static or shock loads, or indentation from debris or improper handling. Incorrect mounting, blows to the rolling elements, cage or rings, foreign particles that enter the bearing cavity can all cause plastic deformation.
Fracture and cracking can occur when there’s excessive load on the bearing, as a result of improper mounting or handling, or because the bearing size and capacity are not adequate for the application. This type of damage can also manifest as thermal cracking, which occurs in the inner or outer ring when the sliding movement causes high frictional heating.
The table below lists some of the most common conditions you can observe in damaged bearings, as well as the potential causes and the solutions for these types of damage.
Observed condition | Potential cause of failure | Solution |
---|---|---|
Flaking of the raceway surface | Flaking may be caused by excessive load, poor shaft or housing accuracy, poor installation or ingress of foreign objects. | If the load is too heavy, use a bearing with a larger capacity. If needed, use an oil with higher viscosity, or improve the lubrication system to form a protective film. |
Peeling of the rolling surfaces | likely to occur when lubrication is poor or the surfaces of opposite parts are rough. It may develop into flaking. | Control the surface roughness and choose a better lubricant. |
Spalling on the ribs or raceway surfaces | May be caused by poor mounting, poor lubrication of the rolling elements or discontinuation of the protective film on the contact surfaces due to excessive load. | Improve the mounting, correct the load and select an adequate lubricant. |
Smearing on the raceway surface | The rolling elements slip during the motion and the lubricant doesn’t have the right characteristics to prevent slippage. | Select a proper lubricant or lubrication system and check the clearance and pre-load. |
Raceway surface is worn and dimensions are reduced | Poor lubrication, ingress of a foreign object or contamination of lubricant with dirt or foreign objects. | Choose a proper lubricant or lubrication system, and improve the sealing efficiency. |
Changes in surface colour and finish | A matted raceway surface or a discoloured surface may indicate poor lubrication, overheating or accumulation of deteriorated oil. | Improve the sealing efficiency and lubrication system, remove the oil with an organic solvent and polish with sandpaper to remove the roughness. |
Indentations and hollows in the raceway surface | Probably caused by ingress of a solid object or by trapped particles. | Remove and keep out foreign objects, check for flakings and improve the handling procedures. |
Chipping of the inner ring, outer ring or rolling elements | Chipping may be caused by excessive load, poor handling or trapped solid objects. | Check and improve the load, and improve the sealing efficiency. |
Cracking in the rings or rolling elements | Excessive load, impact or overheating. A loose fit could also be the cause. | Examine and improve the load and correct the fit. |
Rust or corrosion of the rings or rolling elements | Moisture, ingress of water or corrosive substances, or poor packing and storing conditions. | Improve the sealing efficiency, handling and storage. |
Seizing of the rings or rolling elements | Poor heat dissipation due to poor lubrication or a too small clearance. Excessive load can also be the cause. | Improve the dissipation of heat and the lubrication. Check and improve the load. |
Fretting of the raceways | Too much vibration, a small oscillation angle or poor lubrication. | The inner and outer ring should be transported separately, or the lubrication should be improved. |
Damage of the cages | Excessive load, too high speed or large fluctuation of speed, poor lubrication or high vibration. | Improve the load conditions, reduce the vibration and improve the lubrication system. |