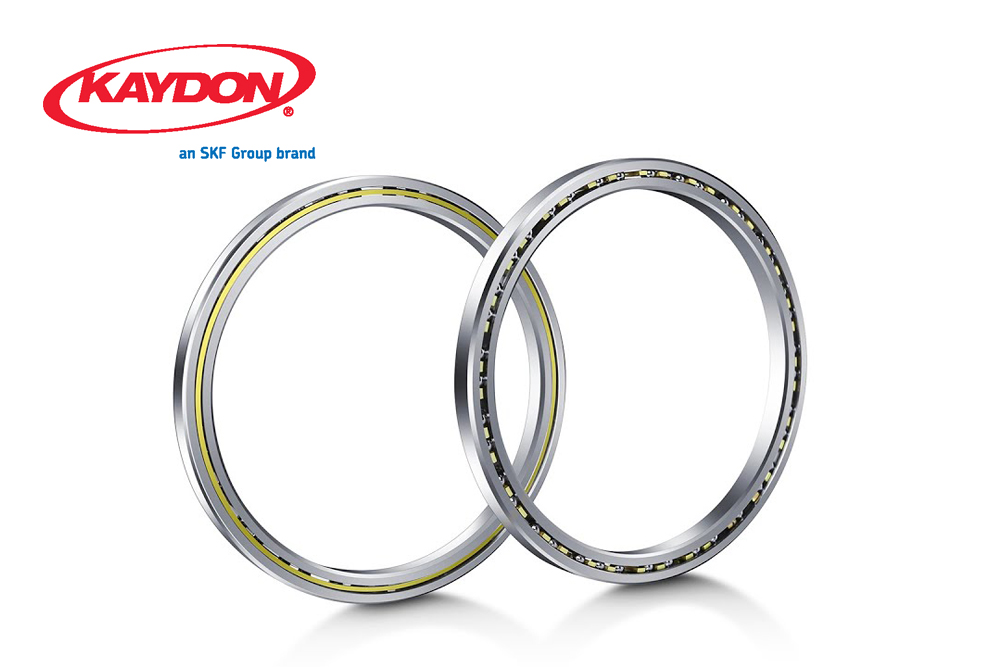
Bearing Manufacturer & Supplier
Specialize in ball bearings, roller bearings, thrust bearings, thin section bearings etc.
Overview of Thin Section Bearings
KAYDON is a leader and pioneer in thin section bearing manufacturing. KAYDON was founded in 1941 and is headquartered in the United States. It has 17 factories and 4 independent business divisions around the world. Since 1941, the precision and reliability of KAYDON thin-section bearings have been fully capable even in very demanding situations such as military industry and aerospace. Since the modern concepts of simplification, miniaturization, lightweight and compactness have been deeply embedded in the design of rotating equipment, in order to meet the needs of customers in this regard, REALI-SLIM bearings are designed as hardened, thin-section anti-friction bearings. KAYDON thin-section bearings solve the size/weight problems of traditional bearings, shafts and bearing seats, greatly reducing the weight of the equipment. All thin-section bearings manufactured by KAYDON can provide various precisions from ABEC1F (P0) to ABEC7F (P4) to meet different customer needs. KAYDON bearings comply with ISO international standards and the US military’s MIL standards.
Table of Contents
ToggleWhat are thin section bearings?
Thin-section bearings are a special type of rolling bearing, generally composed of an inner ring, an outer ring, spherical rolling elements and a cage. They have a smaller bearing inner diameter and a thinner bearing wall thickness. The cross-section of the thin-section bearing is a constant cross-section. It is a bearing series designed according to the width and thickness (cross-section) of a fixed size and does not increase with the increase of the inner diameter. It has a thin-walled structure, which can be used to solve the problem of limited bearing space, because the thickness of its outer ring and inner ring is very small, which can save space. Thin-section bearings have relatively larger inner and outer diameters, which allow them to withstand greater loads and have a longer service life.
Kaydon thin section bearings apply engineering experience and expertise to solve the world’s most demanding applications. Reali-Slim® Kaydon thin section bearing solutions reduce weight, save space, reduce friction, increase design flexibility and provide superior operating accuracy. Kaydon Reali-Slim® and Ultra-Slim® bearings offer customers a wide range of options, from materials, cages, cross-section designs, bearing internal settings, lubrication to corrosion resistance and contact angles. Kaydon offers the industry’s largest range of thin section bearings, with bore sizes from 19mm to 1 meter (3/4″ to 40″) and cross-section sizes from 0.1875″X0.1875″ to 1.000″X1.000″. Kaydon Reali-Slim bearings are lightweight and compact, making them ideal where space is limited. They are available in three different bearing types: radial contact ball bearings (type C), angular contact ball bearings (type A), four-point contact ball bearings (type X). Kaydon thin-section bearings have low friction torque, high rigidity, and good rotation accuracy, and use small outer diameter steel balls. Thin-section bearings can reduce vibration, reduce noise, and prevent pollution in machinery. Thin-section bearing structure and light weight can reduce the size of the machine.
Advantages of thin section bearings
As a new type of bearing, thin-section bearings have many advantages that traditional bearings do not have. Since the outer dimensions are miniaturized to the maximum extent, and the bearings have high rigidity, rotational accuracy, and combined load-bearing capacity, they are most suitable for joints or rotating parts of industrial robots, direct drive motors, medical equipment, measuring instruments, etc. .
High rigidity and stability
The structure of thin-section bearings is relatively simple, so their processing and manufacturing are also relatively easy. This ease of processing and manufacturing makes the production cost of thin-section bearings lower and also improves production efficiency.
Good carrying capacity
Thin-section bearings adopt a point contact design between the rolling elements and the inner and outer rings of the bearing, which has better load-bearing capacity. This good load-bearing capacity enables thin-section bearings to withstand larger loads and is suitable for various heavy-load situations.
Strong adaptability
The structure and size of thin-section bearings can be customized according to actual needs, so they are highly adaptable. This adaptability makes thin-section bearings widely used in different fields and occasions, such as machinery manufacturing, metallurgy, chemical industry and other fields.
Long life and reliability
Thin-section bearings are made of high-quality materials (chromium steel 52100, SS440, stainless steel) and undergo precise machining and heat treatment processes to have a long service life and reliability. At the same time, due to its simple structure and easy maintenance, it also reduces the frequency of repair and replacement during use and improves the reliability of use.
Suitable for high-speed rotation
Since the rolling elements of thin-section bearings adopt a spherical design and the contact area with the inner and outer rings of the bearing is small, their friction resistance is small and they are suitable for high-speed rotation. This characteristic suitable for high-speed rotation makes thin-section bearings widely used in many fields, such as aerospace, high-speed machine tools, precision instruments and other fields.
Factors affecting the performance of thin-section bearings
Bearing material
Bearing material is an important factor affecting the performance of thin-section bearings. The rings and rolling elements of bearings generally use high-carbon chromium bearing steel. The difference between different quality steel raw materials is mainly the oxygen content and titanium content, followed by the phosphorus and sulfur content. These non-metallic elements in steel will form non-metallic inclusions, which will promote the initiation of cracks when the bearing is subjected to large loads. The oxygen content has the greatest influence and has been shown to be correlated with rolling contact fatigue life. Because oxygen atoms mostly exist in the form of oxides in metals, when the oxygen content is high, the inclusion particles are large, and the rolling contact fatigue life is related to the inclusions, so controlling the oxygen content is an effective measure to extend the fatigue life.
Clearance
The radial clearance of thin-section bearings is divided into original clearance, residual clearance and working clearance. The original clearance is the clearance in the free state of the bearing before installation; the residual clearance is the clearance when it is installed into the shaft or bearing seat with interference; the residual clearance is caused by the dimensional deformation caused by the temperature difference inside the bearing and the load. The bearing increases or decreases due to elastic deformation. The clearance at this time is the working clearance. The radial clearance of the rolling bearing directly affects the load distribution inside the bearing, thereby affecting the vibration characteristics and fatigue life of the bearing. Excessive clearance will cause the internal load-bearing area of the bearing to decrease, causing elastic deformation of the rolling elements and rings, increasing the stress on the contact surface, resulting in shortened bearing life and reduced bearing rotation accuracy, resulting in radial circular runout, thereby causing vibration and Noise; too small clearance can easily lead to increased frictional heat and temperature rise, which can lead to smaller effective clearance or greater interference, leading to bearing lockup.
Grease
Grease consists of base oil, thickener and additives. The fatigue wear resistance of thin-section bearings is related to the viscosity of the lubricating oil. Under certain conditions, it increases with the increase of the viscosity of the lubricating oil. The adverse effects of the grease filling amount on the bearing performance are: too much grease filling, the bearing generates a large amount of heat energy during operation and is prone to leakage. However, the main cause of bearing failure at this time is the weakness of the material itself under the contact surface, such as inclusions or Uneven structure, etc.; there is too little grease, and there is not a thick enough oil film at the rolling contact position inside the bearing to isolate the rolling elements and rings. There will be varying degrees of direct contact between materials, resulting in mixed friction, causing material surface wear and reducing fatigue. life.
Sealing and shielding
Wear particles, foreign matter or moisture mixed inside thin-section bearings will affect the lubrication performance and film-forming properties of the grease, thereby exacerbating bearing failure. Therefore, a dust cover or sealing ring is required to ensure effective lubrication and vibration and noise reduction. performance. The dust-proof cover type is mainly used to prevent external dust from entering, and its waterproof performance is average; the contact rubber seal type can prevent external contamination from entering while also preventing internal grease. The dust-proof performance is better than the dust-proof cover, but due to the contact with the bearing sleeve Ring contact, the friction torque generated during operation is large, there is a limit on the speed of use, and the applicable temperature range is relatively small.
Manufacturing process
The common bearing manufacturing process mainly consists of inner and outer ring processing, inner and outer ring assembly, cleaning and inspection, grease injection and packaging. For the inner and outer rings of deep groove ball bearings, the main technical indicators that affect vibration are the inner and outer groove waviness and surface roughness, followed by roundness and surface bumps. For the rolling elements of deep groove ball bearings, the main technical indicators that affect vibration are waviness, roughness and circular deviation. Vibration and noise performance can be improved by increasing the number of rough grinding times in the process, controlling the roundness and waviness of the inner and outer grooves, and increasing the number of super-fine inner and outer grooves to ensure roughness requirements.
The above is the key to how to improve the performance of thin-section bearings. According to the usage conditions of thin-section bearings and the performance requirements of the bearings, specific measures to improve bearing performance include providing sealing and dustproof, coating, lubrication, internal coordination, etc. for the bearings.
Options to improve thin-section bearing performance
Thin section bearings provide higher load carrying capacity in applications. Due to the cross-sectional characteristics of bearings and their large load-bearing capacity, thin-section bearings are widely used in automobiles, engineering machinery, rail transit (subway, etc.), aerospace, textile machinery, petrochemical industry, mining machinery and precision processing fields. For example, the NASA satellite developed by NASA uses two types of thin-section bearings with different diameters in its orbiting satellites. One of them uses this kind of thin-section bearing as its key component. It is understood that in the field of aerospace engineering, spacecraft, rockets, various types of military transport aircraft and various aerospace engines manufactured by various countries also use key components and related technologies similar to thin-section bearings. Thin-section bearings are characterized by small friction resistance and high rotation speed, and can be used on machinery that can withstand radial loads or combined loads that act simultaneously in radial and axial directions. So how to improve the performance of thin-section bearings?
Sealing and shielding
Standard industrial seals are usually made of nitrile rubber. Customized seals such as silicone rubber and Vi materials can also be provided for thin-section bearings to meet high temperatures and other extreme conditions that may be encountered.
Lubrication
Thin-section bearings provide a full range of lubricants that can improve bearing performance in applications with special requirements such as moisture resistance, high temperature, low temperature, vacuum and low torque.
Internal cooperation
Thin-section bearings can meet expected operating performance requirements by improving internal fit. Preloaded bearings are used for high stiffness applications, and radial clearance bearings are used for low friction torque applications. Additionally, standard crossed roller bearings typically do not have the protection against corrosion, custom sealing, special application greases, and high temperature capabilities for extreme environments.
Coating
For ultra-strong anti-corrosion requirements, a very thin, dense chromium coating can be provided to give thin-section bearings stronger anti-corrosion capabilities. Unlike many traditional chrome platings, the coating will not peel or flake under pressure, so it maintains corrosion resistance and requires minimal wear. The performance of the coating has been proven in critical military, aerospace and deep space applications.
Parameter design
In the design, not only the largest possible dynamic load rating must be considered, but also in view of the small cross-section characteristics of thin-section bearings, the value of each structural parameter must be carefully selected to improve the contact stress distribution of bearing parts and facilitate the formation of lubricating oil film. The good contact state improves the performance and service life of the bearing.
Cleaning of Thin Section Bearings
A clean usage environment is very important for bearings. The surface roughness accuracy of thin-section bearing rings and rolling elements is about 1/10 μm. If such smooth ball surfaces are contaminated, the impact will be serious. The lubricating layer between the rolling surfaces is usually 0.2~1 μm. Particulate impurities larger than the lubricant particle size will be excessively crushed by the rolling elements and generate local pressure in the spherical roller bearing steel, which will eventually lead to permanent material fatigue. In addition to this, dust particles in the external environment can reach a size of 10 μm, which can also cause damage to bearings. Because of this, a clean and tidy working environment is crucial for bearings.
Process inspection of thin section bearings
During use, the operating temperature of the bearing is sensed by heating it up. If the temperature exceeds the specified limit, it will automatically alarm to prevent shaft burning. High temperatures often indicate that the bearing is in an abnormal condition. High temperatures are also harmful to bearing lubricants. Sometimes overheating of thin-section bearings can be attributed to the bearing’s lubricant. If the bearing rotates continuously for a long time at a temperature exceeding 125°C, the service life of the bearing will be reduced. Causes of high-temperature bearings include: the bearing may be insufficiently lubricated, the lubricant may be unqualified, and it may contain impurities. When the load is too large, it may be that the internal clearance of the bearing is insufficient and the oil seal may cause friction, etc.
Applications of Thin Section Bearings
Aerospace field
The application of thin-section bearings in the aerospace field is mainly reflected in their ability to provide efficient holding and rotational motion while maintaining a lightweight and compact design to meet the demanding space and weight requirements of spacecraft.
(1) Aircraft landing gear: Thin-section bearings are widely used in aircraft landing gear systems. This is because the aircraft landing gear needs to provide strong support and movement capabilities in a limited space. The thin-section bearing design enables it to provide necessary support while keeping the structure lightweight, helping to reduce the overall weight of the aircraft and improve fuel efficiency.
(2) Aviation systems: In aviation missile systems such as missiles and fire nodes, space and weight are crucial considerations. The compact design of thin-section bearings makes them ideal in missile control and navigation systems. They provide the necessary support and withstand the high speeds and temperatures encountered during missile flight.
(3) Satellite technology: Satellites need to operate in space for a long time and work under various environmental conditions. Thin-section bearings are used in key mechanical components of satellites, such as the directional systems of solar panels and the pointing systems of satellite antennas. Their lightweight and highly precise rotational motion make them suitable for the space-constrained environment of satellites.
Mechanical device
In some mechanical devices, especially when space requirements are high, thin-section bearings can provide effective support and rotation functions, such as robot joints, rotary tables, etc.
(1) Robot joints: Thin-section bearings are widely used in robot joints. Robots require flexible and precise movements, and the design characteristics of thin-section bearings enable them to provide smooth rotational motion to meet the needs of robots performing various tasks, such as assembly, operation, or fine operations.
(2) Rotary table: In mechanical devices that require orientation or angle adjustment, thin-section bearings are used to support the rotary table. This includes laboratory equipment, testing instruments or production lines that require precise orientation adjustments during the work process.
(3) Automation equipment: Thin-section bearings are widely used in automated production lines and factory equipment. They are used to support critical components in rotational motion, helping to make equipment run efficiently. The lightweight design helps reduce the overall load and improves the response speed of the equipment.
Medical equipment
Due to the compact structure of thin-section bearings, they are also commonly used in medical equipment, such as surgical robots, imaging equipment, etc.
(1) Surgical robot: In the joint part of the surgical robot, precise and smooth rotational movement is required. Thin-section bearings can provide the required support and help doctors perform minimally invasive surgeries and precise operations.
(2) Imaging equipment: Medical imaging equipment, such as CT scanners and MRI machines, usually require rotating parts to obtain comprehensive in-vivo images. Thin-section bearings are used to support these rotating parts to ensure they remain stable and precise when rotating at high speeds.
Precision instruments
In instruments that require a high degree of accuracy and stability, thin-section bearings can provide smooth rotational motion and are suitable for optical equipment, measuring instruments and other fields.
(1) Optical equipment: Optical instruments have extremely high requirements for precise rotation and positioning. The design characteristics of thin-section bearings make them an ideal choice for optical equipment. They are used in rotating parts of telescopes, microscopes, lasers and other equipment to ensure precise optical positioning and movement.
(2) Measuring instruments: In measuring instruments that require high accuracy, thin-section bearings are widely used as key components to support rotational motion. This includes a variety of laboratory instruments, measuring equipment, and precision instruments used in scientific research.
(3) Semiconductor manufacturing equipment; In the field of semiconductor manufacturing, high-precision processing and positioning of tiny sizes is required. Thin-section bearings are used in semiconductor equipment to hold and control various rotating components, ensuring the accuracy and reliability of the manufacturing process.
Automobile industry:
Thin-section bearings are also used in some key components of automobiles, such as steering systems, engine parts, etc., helping to reduce overall weight and improve efficiency.
(1) Steering system: The steering system of a car requires highly precise rotational support to ensure vehicle stability and controllability. Thin-section bearings are used to hold steering wheels and other steering-related components.
(2) Engine parts: In the engine, various rotating parts need to be maintained, including crankshafts, camshafts, etc. Thin-section bearings provide lightweight and compact solutions in these engine components, helping to improve engine efficiency and performance.
In general, thin-section bearings have a wide range of applications in applications that require lightweight, compact bearings and limited axial space. Uses of thin-section bearings In the aerospace field, thin-section bearings are widely used in aircraft landing gear, missile systems, etc. to meet the stringent requirements of space and weight. In mechanical devices, they support components such as robot joints and rotary tables, providing flexible and precise movement. In the field of precision instruments, thin-section bearings are used in optical equipment, measuring instruments, semiconductor manufacturing equipment, etc. to ensure highly precise rotation and positioning. In medical equipment, they are used in surgical robots, imaging equipment, etc. to support delicate medical operations. In the automotive industry, thin-section bearings are used in steering systems and engine components to improve the vehicle’s handling and efficiency.