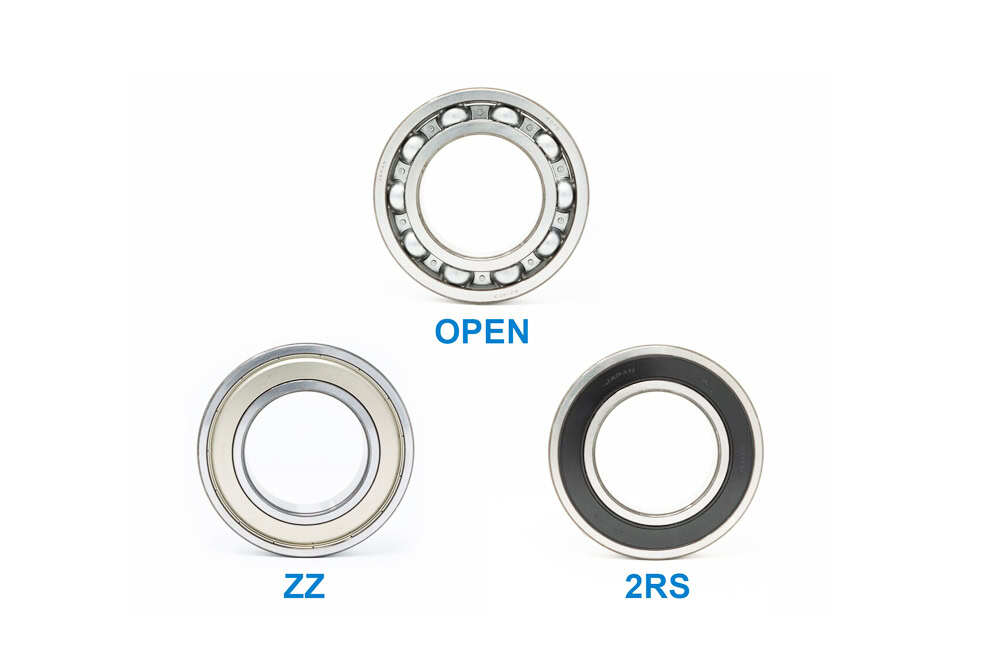
Bearing Manufacturer & Supplier
Specialize in ball bearings, roller bearings, thrust bearings, thin section bearings etc.
Open Bearings, Sealed Bearings, Shielded Bearings?
Bearings are key parts that ensure smooth rotation of machinery and reduce friction. They are divided into closed and open structures. The main difference between closed bearings and open bearings is whether they are sealed and shielded. Sealed bearings generally have better performance and can effectively prevent dust, particles, moisture and other contaminants from entering the bearing interior. This approach helps improve bearing reliability and service life. Open bearings, on the other hand, have no seals and their balls or rollers are directly exposed, making them susceptible to the intrusion of dust and other contaminants, affecting their performance and service life. Sealed bearings and shielded bearings are common enclosed types that sound similar, but each type has unique characteristics, advantages and disadvantages that apply to specific operating needs. This blog aims to explain the features, advantages and disadvantages of sealed, shielded and open bearings, the differences and how to choose the best performing bearing.
Table of Contents
ToggleWhat is an open bearing?
Open bearings do not have any closures, so they are “open”. Open bearings are suitable for high-speed or even ultra-high-speed operation, with small friction coefficient, high limit speed, and various size ranges and forms. Used in industries such as precision instruments, low-noise motors, automobiles, motorcycles and general machinery. It is the most widely used open bearing type in the machinery industry. It mainly bears radial load and can also bear certain axial load.
What are sealed bearings?
In order to prevent grease leakage during bearing operation, the rolling elements (such as balls, rollers or rollers) and the internal lubricant must be completely sealed(2RS). This is the beginning of bearing sealing. These seals are usually made of rubber or synthetic material and are molded or stamped onto the bearing outer ring. Sealed bearings are designed to prevent external contaminants such as dust, dirt, moisture and other environmental factors from entering the bearing, thereby protecting the rolling elements and lubricant from contamination and corrosion. This helps extend the service life of the bearings and also avoids the need for regular maintenance. Sealed bearings are often used in applications where contamination is a concern, such as automotive, industrial and agricultural equipment. Sealing plays an increasingly important role in it. After decades of development, bearing sealing has formed a specialized discipline, and various sealing methods emerge in endlessly.
What is a shielded bearing?
The cover of the shielded bearing(ZZ) is a pure metal sheet stamped part. It is generally fixed on the outer ring and has an appropriate gap with the outer diameter of the inner ring. It is not allowed to contact the cage inside the bearing. The commonly used structure now is a rolled-edge dust cover, which is press-fitted after the bearing is filled with grease and fixed in the teeth of the outer ring by mold deformation. Generally, the dust cover can no longer be removed after it is pressed. If removed, the dust cover will become useless. Because there is a gap between the dust cover and the inner ring of the bearing, the grease cannot be completely sealed in the bearing, nor can excessively fine dust or foreign matter be kept out, so the effect is poor. Since the dust cover is pressed into the bearing, it rarely falls off, the structure is solid, and the heat dissipation is better than that of contact sealed bearings.
Advantages of sealed and shielded bearings
Sealed and shielded bearings have many advantages, the most important of which, as mentioned above, are that they effectively prevent the intrusion of external contaminants (such as dust, dirt, moisture, etc.). Because of this advantage, a series of benefits are derived, mainly including the following aspects:
Excellent protective measures
Sealed and shielded bearings completely enclose the rolling elements and lubricant inside the bearing. This design protects rolling elements and lubricants from contamination and corrosion and extends bearing life.
Long lubricant life
The sealed and shielded design allows the lubricant to remain inside the bearing for extended periods of time, reducing the possibility of lubricant deterioration due to external contaminants. As a result, sealed bearings typically have longer lubrication intervals, resulting in less frequent lubricant changes and lower maintenance costs.
Reduce maintenance
Seals and shields require less maintenance because they effectively block the intrusion of external contaminants, leaving the interior of the bearing relatively clean and clear. Less frequent cleaning and lubrication reduces maintenance costs and workload.
Suitable for harsh environments
Due to their excellent protection against contamination, sealing and shielding are particularly suitable for applications in harsh working environments such as high humidity and dust conditions.
Improve system reliability
The stability and reliability of sealing and shielding can improve the stability and reliability of the entire mechanical system. Sealed bearings are ideal for applications requiring high stability and reliability of mechanical equipment.
A shielded bearing, on the other hand, is a bearing that has a metal shield or plate covering the open side of the bearing. While shielded bearings provide some protection against contaminants, they are not completely sealed like sealed bearings. This means that shielded bearings are less effective at protecting against dust, dirt and moisture. One of the main advantages of shielded bearings is lower friction and heat generation compared to sealed bearings. This results in smoother operation and improved efficiency, making shielded bearings ideal for applications requiring high speed or low torque. Shielded bearings also tend to be cost-effective than sealed bearings.
Sealed bearings VS shielded bearings
Friction: One of the main advantages of shielded bearings is lower friction and heat generation compared to sealed bearings. This results in smoother operation and improved efficiency, making shielded bearings ideal for applications requiring high speed or low torque. Shielded bearings also tend to be cost-effective than sealed bearings.
Maintenance and Lubrication: However, shielded bearings’ lack of complete sealing means they are susceptible to contamination. This can lead to premature wear and shortened service life, especially in applications where the bearings are exposed to harsh conditions. Shielded bearings also require frequent maintenance and relubrication than sealed bearings.
Rotational speed: One of the key factors to consider when selecting the right bearing is the maximum operating speed of the bearing. One of the main differences between sealed and shielded bearings is their maximum speed rating. The maximum speed of a bearing is the highest speed at which the bearing can operate without premature failure or damage. This speed is usually specified by the bearing manufacturer and is affected by factors such as the type of lubrication used, bearing material and bearing design.
Generally speaking, shielded bearings have a higher maximum speed rating than sealed bearings. This is because seals on sealed bearings create friction and drag, limiting the speed at which the bearing can operate. Shielded bearings, on the other hand, have less resistance and therefore can run at higher speeds. For example, a typical sealed bearing might have a maximum speed rating of 15,000 RPM, while a shielded bearing of the same size and construction might have a maximum speed rating of 18,000 RPM. In applications requiring high speed, such as motors, pumps and compressors, this maximum speed can vary significantly. It should be noted that the maximum rated speed of the bearing is only a reference value, and the actual operating speed of the bearing may be lower, depending on factors such as load, lubrication and operating conditions.
Conclusion
When selecting the appropriate bearing, factors such as maximum speed, contaminant protection and lubrication requirements need to be considered. If the application requires a high level of protection from contaminants and the speed requirements are not particularly stringent, sealed bearings may be a suitable choice. For applications where speed requirements are high but contaminant protection requirements are relatively low, shielded bearings may be suitable. However, selecting the appropriate bearing type still requires consideration of the specific requirements of the application, environmental conditions, and other factors.