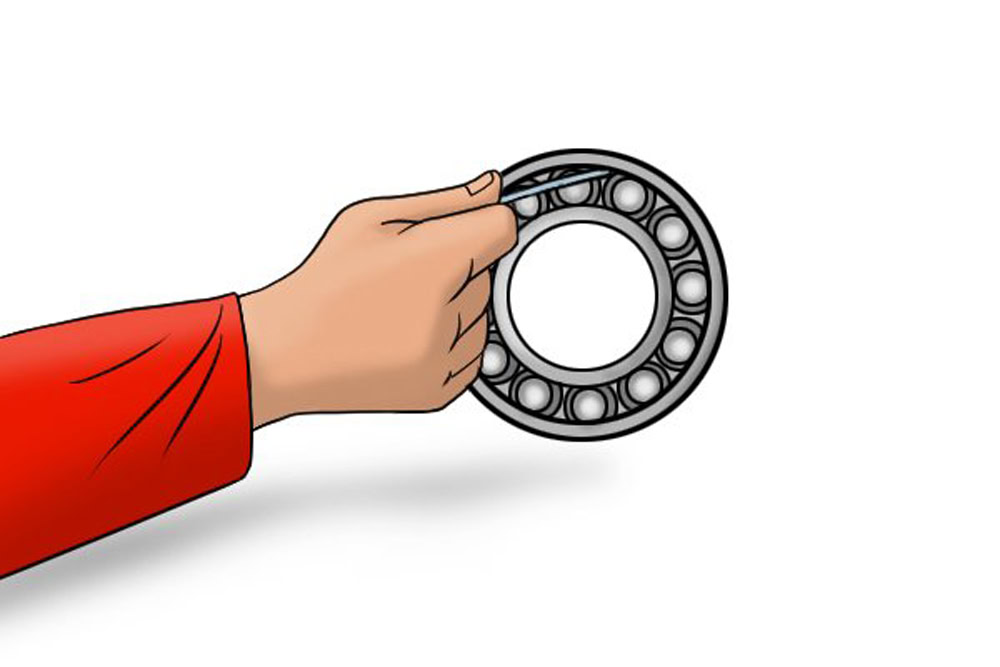
Bearing Manufacturer & Supplier
Specialize in ball bearings, roller bearings, thrust bearings, thin section bearings etc.
Information on Bearing Clearance
Bearing clearance refers to the amount of radial or axial movement that the bearing can make to the unfixed side when one of its rings is fixed before the bearing is installed on the shaft or bearing box. It is usually divided into radial clearance and axial clearance. The size of the working clearance during the operation of the bearing will affect its service life, temperature rise, noise and vibration performance.
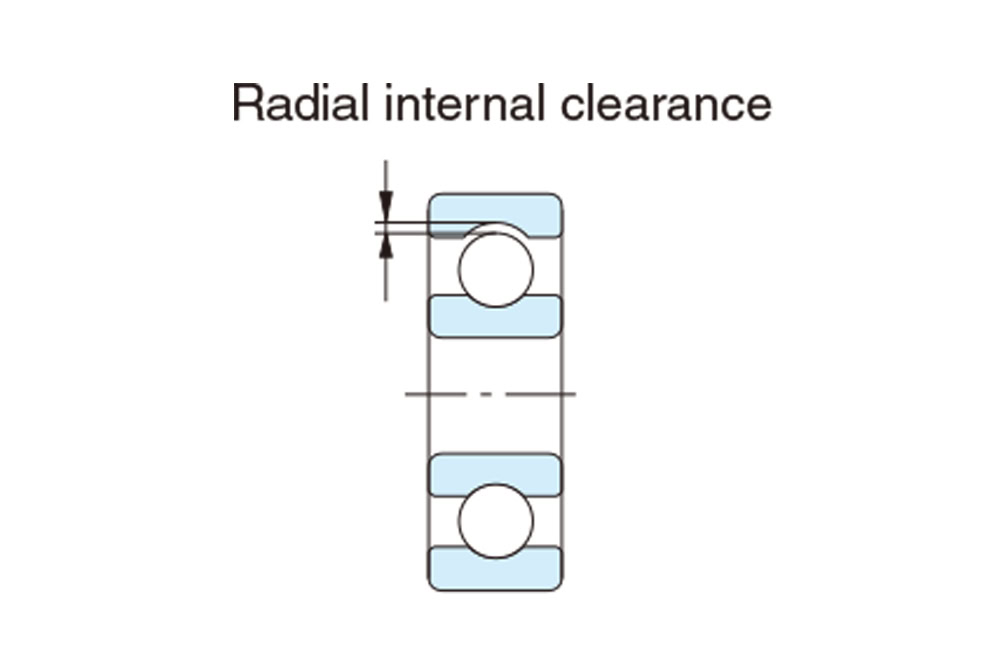
Table of Contents
ToggleRadial clearance
When the bearing that bears radial load is in a non-preloaded state, its radial clearance G is: under the condition of no external load, the outer ring moves from the radial eccentric limit position on one side to the opposite limit position; the average radial distance generated.
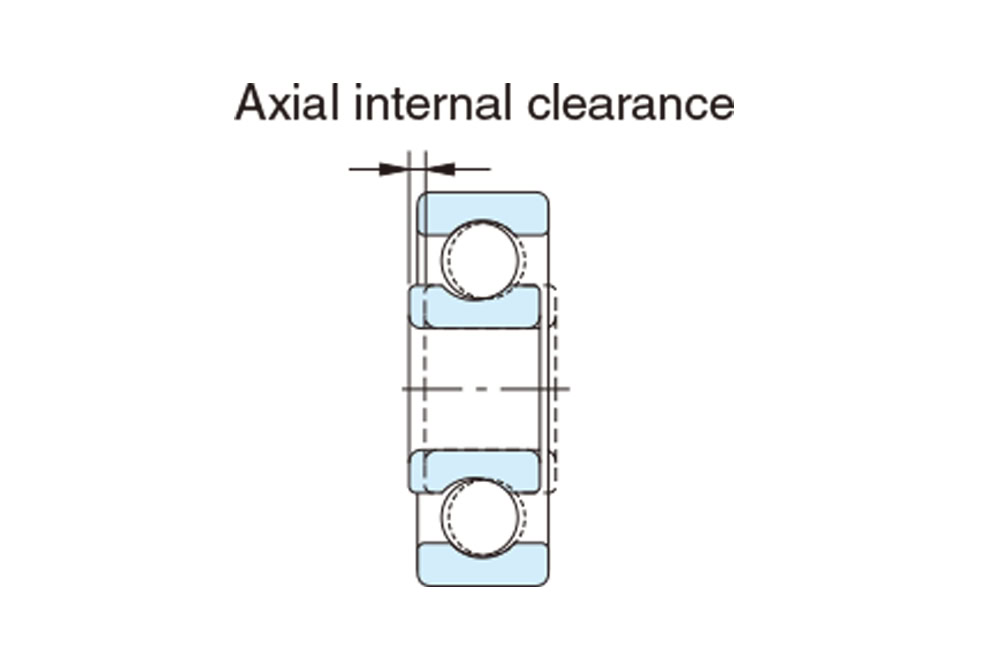
Axial clearance
When the bearing that can bear bidirectional axial load is in a non-preloaded state, its axial internal clearance G is: under the condition of no external load, one of the rings moves from the axial limit position on one side to the opposite limit position; the average axial distance generated.
Allowable Tolerance for Shaft Roundness
Newly Machined Shafts | Unmachined Old Shafts | |
---|---|---|
Shaft Diameter (mm) | High Speed > 1000 rpm | Low Speed ≤ 1000 rpm |
—————— | ————————- | ————————— |
50 ~ 70 | 0.01 | 0.03 |
70 ~ 150 | 0.02 | 0.04 |
Note: All values are in millimeters (mm).
Maximum Allowable Wear for Rolling Bearings
Bearing Diameter (mm) | Radial Clearance (mm) | Axial Clearance (mm) |
---|---|---|
≤ 30 | 4D/1000 | 0.2 |
35 ~ 70 | 3.5D/1000 | 0.3 |
75 ~ 100 | 3D/1000 | 0.3 |
> 100 | Not than 0.3 | 0.3 |
Note: D = Bearing Inner Diameter or Shaft Diameter
The maximum amount of movement that can be made by fixing one ring of a rolling bearing in the radial or axial direction is the clearance of the rolling bearing. In most cases, the larger the radial clearance of the bearing, the larger the axial clearance. According to the state of the bearing, the clearance can be divided into three types: original clearance, installation clearance, and working clearance; the installation clearance directly affects the normal operation of the rolling bearing. Too small a clearance will cause a high temperature rise in the rolling bearing, and even the rolling element to get stuck; if the clearance is too large, it will cause the equipment to vibrate and generate noise.
Initial Radial Clearance
Original clearance: the clearance of the bearing in a free state before installation, which is generally determined during processing and assembly.
Bearing Diameter (mm) | Single Row Radial Ball Bearing (μm) | Double Row Ball Bearing (μm) | Spherical Roller Bearing (μm) | Applied Axial Load During Measurement (MPa) | Allowable Wear Value After Use (μm) | ||||
Over | To | Min | Min | Min | Max | Min | Max | 0.5 | 10 |
18 | 24 | 1.0 | 2.4 | — | — | 0.5 | |||
24 | 30 | 1.0 | 2.4 | — | — | 1.0 | 20 | ||
30 | 40 | 1.2 | 2.6 | — | — | 1.0 | |||
40 | 50 | 1.2 | 2.9 | 2.0 | 5.5 | 1.0 | 25 | ||
50 | 65 | 1.3 | 3.3 | 2.5 | 6.5 | 1.0 | |||
65 | 80 | 1.4 | 3.4 | 3.0 | 7.0 | 5.0 | 8.0 | 1.0 | |
80 | 100 | 1.6 | 3.5 | 3.5 | 8.0 | 6.0 | 10.0 | 1.0 | |
100 | 120 | 2.0 | 4.0 | 4.0 | 9.0 | 1.5 | |||
120 | 140 | 2.3 | 4.5 | 4.5 | 10.0 | 1.5 | 30 |
Installation clearance: also known as fit clearance, which is the clearance after the bearing and shaft or bearing seat are assembled but not yet working. Usually the installation clearance is smaller than the original clearance, mainly because the inner ring of the bearing increases or the outer ring decreases after installation.
Working clearance: the clearance of the bearing in the working state. During the working process, the bearing will reduce the clearance due to the temperature rise and thermal expansion of the inner ring; it will also increase the clearance due to the elastic deformation of the contact position between the rolling element and the raceway under the action of load.
Selection of radial clearance
The radial clearance of the bearing must be selected according to the conditions, not the smaller the better. The radial clearance of rolling bearings is divided into 5 groups. Group 0 is the standard basic radial clearance group; bearings in group 0 are commonly used in general operating conditions, normal temperatures and common interference fit conditions; bearings with larger radial clearance are suitable for special working conditions such as high temperature, high speed, low noise, and low friction; bearings with larger radial clearance are suitable for precision spindle bearings, etc.
Axial Clearance of Deep Groove Ball Bearings
Nominal Bore Diameter (d) | Clearance | Working Clearance (Axial Clearance) | Notes |
---|---|---|---|
≤30 mm | 0.4 (C3) | Gr 18 / Dw 3.5 / 0.08 mm / Ga 0.032 | Range: 0.02-0.05 mm |
>30-50 mm | 0.4 (C3) | Gr 27 / Dw 4 / 0.1 mm / Ga 0.04 | Range: 0.03-0.07 mm |
>50-80 mm | 0.4 (C3) | Gr 38 / Dw 4 / 0.14 mm / Ga 0.056 | Range: 0.04-0.08 mm |
>80-100 mm | 0.4 (C3) | Gr 51 / Dw 7 / 0.19 mm / Ga 0.076 | Range: 0.07-0.10 mm |
>100-120 mm | 0.4 (C3) | Gr 61 / Dw 8 / 0.23 mm / Ga 0.092 | Range: 0.09-0.12 mm |
>120-140 mm | 0.4 (C3) | Gr 68.5 / Dw 9 / 0.25 mm / Ga 0.1 | Range: 0.10-0.14 mm |
Notes:
Gr: Radial clearance
Dw: Ball diameter
Ga: Specific clearance coefficient
Range: The acceptable range for axial clearance in mm.
This table provides the standard values for axial clearance in deep groove ball bearings based on the nominal bore diameter. It includes the corresponding radial clearance, ball diameter, working clearance, specific clearance coefficient, and the acceptable range for axial clearance.
Selection of axial clearance
Taking deep groove ball bearings and tapered roller bearings as examples, when they are installed face to face or back to back, the internal clearance or preload usually requires the axial position of a ring to determine, and the bearing configuration performance and operating requirements should be considered. The axial clearance and radial clearance of this type of bearing usually only need to meet one of the values.