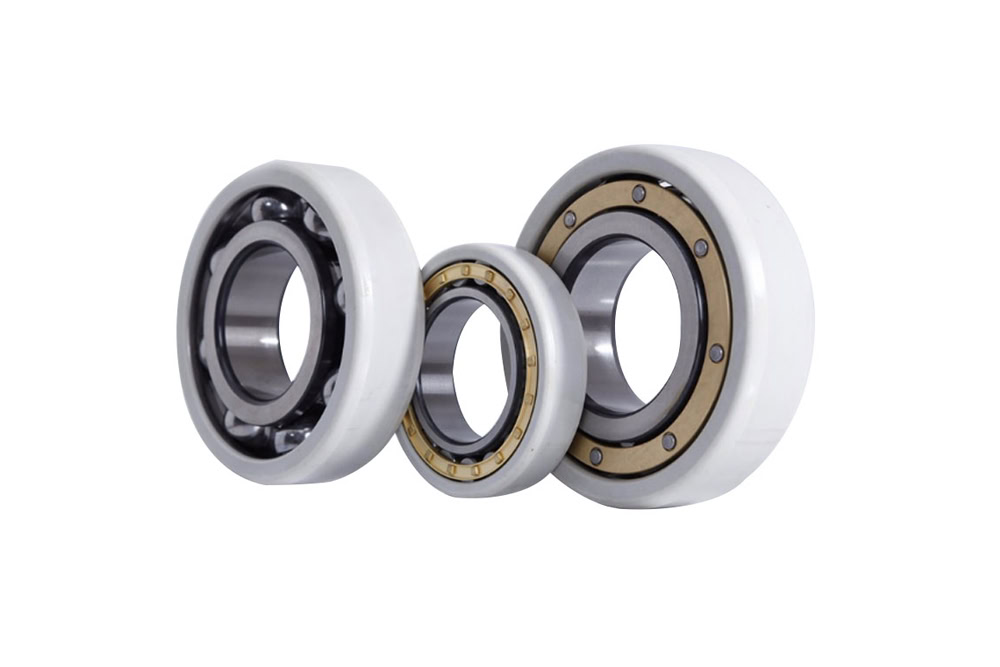
Bearing Manufacturer & Supplier
Specialize in ball bearings, roller bearings, thrust bearings, thin section bearings etc.
Information About Electrically Insulated Bearings
Under harsh environments such as high speed, high temperature, and high humidity, electrically insulated bearings not only have to withstand huge mechanical stress, but also need to have excellent electrical insulation performance to ensure the safe and stable operation of the equipment. They are one of the key components in modern industry.
Table of Contents
TogglePrinciple of electrically insulated bearings
In equipment such as motors, potential differences or currents may be generated due to various reasons (such as friction between bearings and shafts, electromagnetic induction, etc.). If these currents pass through the bearings, they may cause electrical corrosion of the bearings, thereby shortening the service life of the bearings and even causing equipment failure. Therefore, the use of electrically insulated bearings can effectively block these currents and protect the safe operation of bearings and equipment.

What are electrically insulated bearings?
The insulating layer of electrically insulated bearings is usually added to the surface or inside of the bearings through special spraying, coating, or filling processes. These insulating layers need to have sufficient insulation strength and wear resistance to withstand various stresses and environmental conditions during the operation of the equipment. This ability enables the bearing to effectively prevent current from passing through the bearing itself when it is running in a conductive medium. At the same time, the insulating layer also needs to have good chemical stability and anti-aging properties to ensure its long-term effectiveness.
Advantages of electrically insulated bearings
The advantages of electrically insulated bearings are that they can improve equipment reliability, extend equipment life, reduce maintenance costs, and avoid damage caused by electrical corrosion. However, their disadvantages cannot be ignored, including high cost, technical challenges, and possible maintenance and replacement costs. Therefore, when choosing whether to use electrically insulated bearings, it is necessary to comprehensively consider their advantages and disadvantages as well as specific application scenarios.
Improve equipment reliability: electrically insulated bearings can isolate current and avoid the impact of current on bearings, thereby protecting the safe operation of equipment and improving equipment reliability.
Reduce maintenance costs: The use of electrically insulated bearings can reduce equipment failures and maintenance times, thereby reducing maintenance costs.
Extend equipment life: electrically insulated bearings use special materials and manufacturing processes, have better high temperature resistance, corrosion resistance and other properties, can operate normally in harsh environments, and extend the service life of equipment.
Avoid damage caused by electrical corrosion: electrically insulated bearings can avoid damage caused by electrical corrosion, so they are reliable than ordinary bearings in motor applications. Compared with other insulation methods, such as insulation of shafts or housings, electrically insulated bearings are economical and reliable.
Excellent insulation performance: Its DC impedance under high temperature conditions can reach the G ohm range, the rolling elements have excellent wear resistance and low lubrication requirements, and are particularly suitable for high-speed, low-friction and low-temperature operating occasions.
Disadvantages of electrically insulated bearings
Higher cost: Electrically insulated bearings usually require the use of special materials and manufacturing processes, such as spraying ceramic coatings, etc., which will increase their manufacturing costs. Therefore, the price of electrically insulated bearings is usually higher than that of ordinary bearings.
Maintenance and replacement costs: While electrically insulated bearings can extend the life of equipment and reduce maintenance costs, in some cases the entire bearing may need to be replaced if the insulation is damaged or fails. This may increase the cost of maintenance and replacement.
Environmental limitations: The insulation performance of electrically insulating bearings may be affected by environmental conditions, such as high temperature, high humidity, chemical corrosion, etc. These conditions can damage the insulation, causing bearing failure.
Dimensional and mounting limitations: Electrically insulated bearings may need to be customized for specific applications to meet specific dimensional and mounting requirements. This can increase design and manufacturing complexity.
Technical challenges: Although electrically insulated bearings have made significant progress, in some applications, some technical challenges still need to be solved, such as how to further improve electrical insulation properties while ensuring mechanical properties.
Applications of electrically insulating bearings
Electrically insulating bearings are widely used in various situations that require electrical isolation, especially in the fields of motors, generators, power tools, medical equipment, etc., and their role is particularly prominent. In these equipment, electrically insulated bearings not only ensure the efficient operation of the equipment, but also greatly reduce the risk of electrical failure and improve the safety and reliability of the equipment. Due to its unique process and characteristics, electrically insulating bearings are widely used in many industries.
Electric power industry: Electrically insulating bearings are widely used in the electric power industry, especially in wind turbines, hydroelectric generators and thermal generators. In these devices, electrically insulating bearings are used to support rotating parts and ensure that electrical current does not pass through the bearings and cause damage.
Mechanical and metallurgical industry: In the mechanical and metallurgical industry, high-power variable frequency motors require the use of electrically insulated bearings. These bearings are used in cranes, textile machines, printing presses, iron-making equipment, steel-making equipment, steel rolling equipment, cutting equipment, coking equipment and complete sets of smelting equipment.
Railway Industry: In the railway industry, electrically insulating bearings are used in traction motors of diesel locomotives. These bearings are able to withstand high speeds and heavy loads while preventing damage caused by the passage of electrical current through the bearings.
Mining machinery industry: In the mining machinery industry, high-power and high-voltage motors require the use of electrically insulated bearings. These bearings are used in mining machines, coal preparation machines, coal washers, crushers, ball mills, grinders, sand mills and other equipment.
In addition, electrically insulated bearings are also widely used in high-voltage motors to drive various machinery, such as compressors, water pumps, crushers, cutting machine tools, transportation machinery, etc. These bearings can meet the insulation requirements for bearings in various power equipment and ensure the safe and stable operation of the equipment.
Conclusion
As an important component in modern industry, the development and application of electrically insulated bearings are not only related to the safety and stability of equipment, but also represent the progress of the entire industrial technology. We have reason to believe that in the near future, with continuous technological innovation and breakthroughs, electrically insulated bearings will bring excellent performance and broader application prospects to our industrial production.