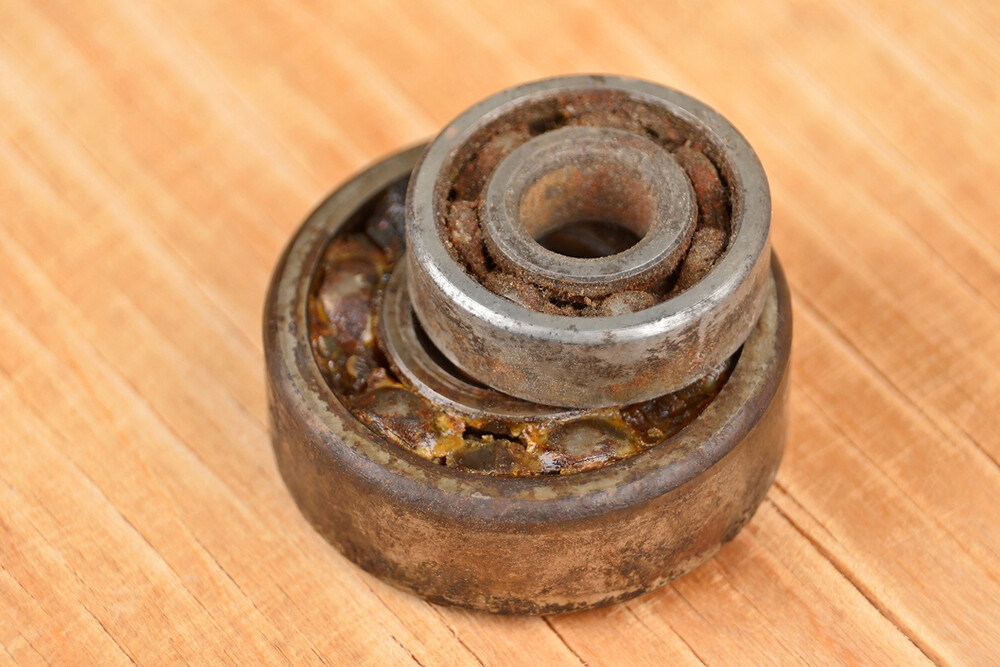
Bearing Manufacturer & Supplier
Specialize in ball bearings, roller bearings, thrust bearings, thin section bearings etc.
How To Prevent Bearings From Rusting?
Bearings are an important part of mechanical equipment, and their normal operation is crucial to the performance and service life of the equipment. However, in some environments, bearings are susceptible to corrosion and rust, affecting their normal operation. Bearings require extremely high dimensional accuracy, especially the rolling elements (balls, needle rollers or rollers). Slight corrosion will affect the performance and life of the bearing, so the packaging of the bearing must have anti-rust function. Therefore, how to effectively prevent bearings from rusting has become an important task to maintain the normal operation of equipment. The most commonly used anti-rust packaging is bubble anti-rust packaging. The commonly used materials are anti-rust bags and anti-rust paper. Under good sealing conditions, it can provide a rust-proof period for bearings for several years.
Table of Contents
ToggleWhy do bearings rust?
Bearing rust is related to its material and use environment. The bearing steel itself contains carbon. Since the steel itself contains inclusions, there is also dust and debris on the surface. Under the action of water molecules, the metal surface undergoes a chemical reaction and is eroded, damaged and corroded. If you want to delay the speed of bearing rust as much as possible, you need to do anti-rust treatment for the bearing. Steel products are prone to rust after oxidation, and stainless steel bearings are no exception. However, there are many factors that affect bearing rust, such as the chemical composition and structure of the metal material itself; surface finish (battery corrosion due to poor oxygen concentration); the composition and ph value of the solution in contact with the metal surface, etc., which all can cause bearings to rust. direct factors.
If acid is adsorbed on the metal surface, it will cause a chemical reaction on the surface of the product and cause it to be corroded. Therefore, the cleaning of bearing products is very important. Corrosive salts, dust, impurities, and ingredients of anti-rust materials may also cause corrosion if the ingredients are not used correctly or are not tested in time, or even if the wrong anti-rust materials are used. In addition, failure to comply with reasonable anti-rust systems and procedures, poor quality of anti-rust grease, poor quality of packaging materials, and poor storage environment are also causes of bearing corrosion.
Bearings cannot be painted or electroplated. In addition, anti-rust materials cannot condense into solid matter on the covering layer, which determines the particularity of its anti-rust technology. In the process of manufacturing bearings, there are than a dozen processes in total, and after each process is completed, its dimensions must be measured by surveyors. Therefore, the workload of rust prevention between processes is very large, and rust often occurs during this process. Although the regions and climate conditions of each bearing factory are different, there are still similarities in the parts where rust often occurs. For example: rust occurs during the process, mostly on the end face and outer diameter of the bearing. Most of the types of corrosion are pitting corrosion or localized flaky corrosion; while most of the corrosion after the oil seal is on the outer diameter, end face and inner diameter (where it contacts the wrapping paper). In some cases, there is rust on the ball or roller cage.
In addition, when using bearings, we need to try to avoid direct contact with the bearing surface with our hands. This is because sweat is a colorless, transparent and slightly acidic liquid. In addition to containing various trace elements such as sodium, magnesium, and calcium, it also contains A small amount of urea, lactic acid, citric acid and other organic acids. When sweat comes into contact with the bearing, a sweat film will be formed on the bearing surface. The sweat film will cause an electrochemical reaction on the bearing surface and cause corrosion. Therefore, we need to use special gloves or finger cots to pick up the bearings, and we must not touch the bearings directly with our hands.
1) During the grinding process, the instantaneous high temperature will cause the surface of the workpiece to reach a molten state, and a chemical reaction will occur between the steel surface and the oxygen in the air, forming an extremely thin (20–30nm) iron oxide film. If it is not completely removed in subsequent processing, even if the bearing is coated with anti-rust oil, the internal corrosion will appear on the surface of the bearing after a period of time.
2) When the bearing is finely ground or super-ground, it does not reach the specified accuracy, and pits of a certain depth are formed on the surface. Once corrosive particles or moisture in the air enter these pits, corrosion will gradually appear.
3) After the bearing is acid-stamped and engraved, if it is not cleaned or neutralized thoroughly, it will cause corrosion.
4) The method of applying anti-rust oil is unreasonable. First, use a rag soaked in anti-rust oil and roll the bearing on the rag. Sweat on your hands, corrosion on the rag, and parts of the bearing that have not been coated with anti-rust oil will cause corrosion; The second is to stack the bearings together, and then spray anti-rust oil with a sprayer. It is difficult for the anti-rust oil to be sprayed between the bearings and the stacked surfaces of the bearings. In this way, the corrosion will slowly occur after long-term contact with moisture and oxygen in the air. produced.
5) Effect of humidity. The critical humidity of steel is around 65%, but in many bearing manufacturing factories, the production environment humidity mostly exceeds 65%, and some even reach 80%, which can easily cause bearings to rust.
6) When the bearings are cleaned with water, if the bearings are not dehydrated or the dehydration is not clean, or an air compressor is used to dry the bearings without drying, it will also cause serious corrosion of the bearings.
7) When the bearing is assembled and inspected, the operator directly touches the bearing parts with his hands, causing all the sweat on his hands to stay on the bearing surface, which will cause corrosion on the outer ring of the bearing.
8) A large amount of moisture and corrosive substances containing salt in the air blow down to the bearing surface, and the temperature of the product drops due to ventilation to produce “condensation”, which can also cause the bearing to rust.
9) The material of the bearing steel does not meet the requirements, such as the content of non-metallic impurities in the steel is too high (the increase in sulfur content in the steel reduces the corrosion resistance of the material itself).
Tips to Prevent Bearings from Rusting
Bearing anti-rust is to protect the bearings from oxidation and corrosion and extend bearings service life.
The corrosion resistance of bearing materials plays an important role in preventing bearings from rusting. Bearings made of GCr15 will rust like ordinary steel. The Cr content of Gcr15 steel is only about 1.5% (the value after the bearing steel is the Cr content, in thousandths). If the Cr content is close to the 13% boundary, the anti-rust effect will be better. For example, Cr12 (containing about 12% Cr) steel will basically not rust. Choosing bearing materials with better corrosion resistance, such as stainless steel, ceramics, etc., can effectively reduce the risk of bearing corrosion.
Keep a dry environment
Moisture is one of the main causes of bearing rust. Keeping the bearing working environment dry can greatly reduce the risk of bearing rust. Moisture-proof measures can be taken, such as using moisture-proof cabinets, dehumidifiers, etc., to ensure that the ambient humidity is controlled within an appropriate range.
Prevent contact with liquids
Avoid direct contact of bearings with water or other liquids, especially corrosive liquids. If you need to use bearings in a humid environment, you can choose sealed bearings with waterproof properties or take sealing measures to prevent moisture and other liquids from entering the inside of the bearing.
Apply rust inhibitor
Applying rust inhibitor is an effective way to prevent bearings from rusting. Apply anti-rust agent on the surface of the bearing to form a protective film, which can effectively prevent the bearing from being corroded by moisture, acid and alkali and other corrosive substances. Choose a rust inhibitor of reliable quality and apply it correctly according to the instructions to achieve a good anti-rust effect.
Vacuum packaging
Place the bearing into a vacuum bag, remove the air, and seal the bag. Vacuum packaging prevents moisture and oxygen in the air from contacting the bearing surface, reducing the possibility of oxidation and corrosion. This method is suitable for long-term storage or transportation of bearings.
Regular inspection and maintenance
Regular inspection and maintenance of bearings are important measures to prevent rust. Through regular inspections, abnormal conditions of bearings, such as wear, looseness, rust, etc., can be discovered in time. Once an abnormality is discovered, timely measures should be taken to repair or replace it. At the same time, add lubricant or replace lubricating oil to the bearings regularly according to maintenance requirements to ensure the normal operation of the bearings.
Control the storage environment
For bearings stored for a long time, controlling the humidity and temperature of the storage environment is also a key measure to prevent rust. Keeping the storage environment dry and controlling the humidity below 50% can effectively reduce the risk of bearing rust. At the same time, avoid exposing the bearings to high temperatures or sunlight for a long time to maintain a stable storage environment.
Regular operation:
Running the bearing regularly can help distribute the lubricant or grease evenly and prevent the bearing from rusting due to long periods of inactivity. It is recommended to maintain flexibility by rotating the bearings or performing light movements every once in a while.
Dust cover and seal:
Protect bearings with dust boots or seals to prevent dust, dirt, and moisture from entering the interior of the bearing. This reduces the bearing’s exposure to corrosive environments.
Surface cleaning:
Cleaning must be based on the properties of the surface of the object to be rusted and the prevailing conditions, and the appropriate method must be selected. Commonly used methods include solvent cleaning, chemical cleaning and mechanical cleaning. After the surface is dry and cleaned, it can be dried with filtered dry compressed air, or dried with a dryer at 120-170 ℃, or wiped dry with clean gauze.
Soaking method:
Some small items are soaked in anti-rust grease, and the cross-tapered roller bearings are coated with a layer of anti-rust grease on their surfaces. Oil film thickness can be achieved by controlling the temperature or viscosity of anti-rust grease.
Brushing method:
It is used for outdoor construction equipment or special-shaped products that are not suitable for soaking or spraying. When brushing, care must be taken not only to avoid accumulation but also to prevent missed coating.
Spray method:
Some large anti-rust objects cannot be oiled by immersion. Turntable bearings are generally sprayed in a clean air place with filtered compressed air at a pressure of about 0.7Mpa. The spray method is suitable for solvent-diluted anti-rust oil or thin-layer anti-rust oil, but complete fire prevention and labor protection measures must be adopted.
It should be noted that the following acids cannot be used for bearing rust removal: sulfuric acid, hydrochloric acid, dilute sulfuric acid, and dilute hydrochloric acid. Because these acids will destroy good metal parts, these liquids must not be used! There are several liquids in daily life that can remove rust without damaging good metal parts, but the effects vary. The first is dilute oxalic acid, with a ratio of 3:1 to water, dilute oxalic acid 3:1 water. This is slower, but works very well and is sold everywhere. The second type is gun oil, also called mechanical rust removal oil. This oil can quickly remove rust and the effect is very good.
Preventive measures for bearing corrosion, methods to prevent bearing rust during the production process, keep bearings clean, bearings should be kept clean and isolated from the air, and moisture in the atmosphere should be avoided from condensing on the bearing surface. Specific measures are as follows: Wear work gloves or liquid gloves during assembly to avoid fingerprint rust caused by direct contact of sweaty hands with bearings and their parts. Special packaging and sealing can be used for military reserve bearings or precision bearings exported to tropical countries.
Before assembly, bearings must be cleaned to remove moisture and dirt. The assembled bearings should be sealed with anti-rust grease or other anti-rust materials. Such as anti-rust water, gas-phase rust inhibitors, etc. are temporarily sealed to prevent rust. Assembly is usually performed in an air-conditioned environment to avoid moisture condensation.
Bearing rust prevention is a very important task, especially the rust prevention between processes. After the bearings are pickled, cleaned, and grinded in the heat treatment workshop, there are still many processes. When the product is not produced by flow, it must be stored in a central warehouse after one sequence of processing. Therefore, the bearing rings stored between processes must be rust-proofed. Only in this way can the quality of the bearings be ensured.
Bearing anti-rust period
The anti-rust period refers to the time from the implementation of anti-rust measures to the failure of the anti-rust measures on the bearing. According to China’s GB/T8597 “Rolling Bearing Anti-Rust Packaging” standard, the anti-rust period of bearings is divided into half a year, one year and two years. Among them, the rust-proof period for bearings that need to be installed and used in the short term is half a year, the rust-proof period for general bearings is one year, and the rust-proof period for bearings with higher usage requirements is two years.
Short-term rust prevention: The rust prevention period is 3 to 6 months. It is suitable for large quantities of bearings that will be put into use in a short period of time. Generally, plastic bags or vapor-phase anti-rust bags are used.
General anti-rust period: The anti-rust period is 6-12 months, suitable for general-purpose bearings. Generally, vapor phase anti-rust bags, vapor phase anti-rust paper, desiccant, etc. are used.
Long-term rust-proof packaging: The rust-proof period is one to three years, suitable for special and precision bearings. Generally, anti-rust oil, vapor phase anti-rust bags, anti-rust paper, etc. are used.
Commonly used anti-rust materials
Commonly used anti-rust materials for bearings include oil (grease) film anti-rust oil, emulsified anti-rust oil and other anti-rust water agents, vapor-phase anti-rust agents and vapor-phase anti-rust oil.
Oil film anti-rust oil is also called anti-rust lubricating oil. When using, the user does not need to clean off the anti-rust oil after removing the bearing packaging, and can directly install it for use.
Lipid film anti-rust oil includes liquid anti-rust grease, solvent-diluted anti-rust oil, hot-coated petroleum anti-rust grease, etc. Among them, solvent-diluted anti-rust oil can be sprayed and is easy to use.
Vapor-phase anti-rust oil adds gas-phase corrosion inhibitors to lubricating oil to perform two functions: anti-rust and lubrication. Since the gas-phase corrosion inhibitor isolates the atmosphere from contact with metal by slowly evaporating gas, it does not have to be in direct contact with the metal, and It penetrates all holes, especially suitable for bearings with many gaps and grooves. Vapor phase anti-rust materials can volatilize anti-rust gas at normal temperature, and the gas protective layer formed after being adsorbed on the bearing surface can effectively prevent oxygen and water vapor from corroding the bearing. Anti-rust gas is pervasive and can cover the entire surface of the bearing to provide comprehensive and effective anti-rust for the bearing. If the package is sealed and the concentration of anti-rust gas is maintained at a high level, the anti-rust period can last for several years.
In addition to vapor phase anti-rust materials, bearing packaging also uses coated paper, cartons, polyethylene films, nylon bags, aluminum foil bags, etc. When selecting anti-rust materials for bearings, they should comply with international environmental protection requirements and try to use environmentally friendly materials to avoid personal injury and environmental pollution.
Conclusion
Preventing bearings from rusting requires many aspects, including selecting appropriate materials, maintaining a dry environment, preventing contact with liquids, applying rust inhibitors, vacuum packaging, regular inspection and maintenance, and controlling the storage environment. Only by comprehensively applying these methods can we effectively reduce the risk of bearing rust and ensure the normal operation and service life of the equipment. Please note that the above methods are for reference only, and specific anti-rust methods and measures may vary depending on different bearing types, application environments, and manufacturer recommendations. It is recommended to read the bearing manual carefully or consult a professional for accurate advice before carrying out anti-rust treatment.