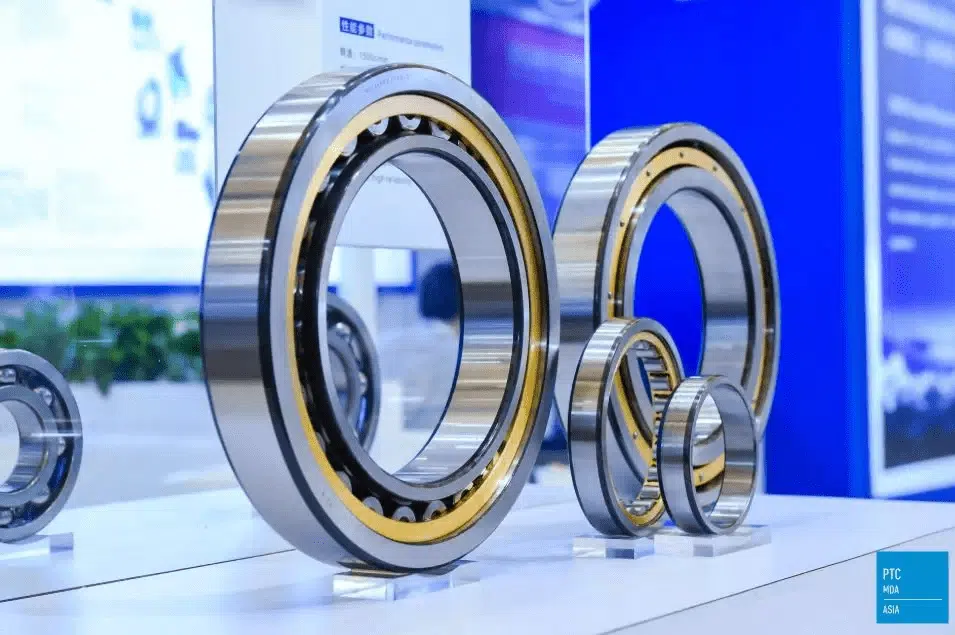
Bearing Manufacturer & Supplier
Specialize in ball bearings, roller bearings, thrust bearings, thin section bearings etc.
How to Choose The Right Bearing
A bearing is a mechanical component whose function is to guide a rotating assembly. Thus, bearings allow one element to rotate relative to the other. Therefore, bearings are high-precision parts that allow equipment to move at different speeds by efficiently transporting loads. They must be highly accurate and durable, and be able to operate at high speeds with minimal noise and vibration. This type of equipment is found in all applications such as the automotive industry, the aerospace sector, construction equipment, agricultural machinery, CNC machines, etc.
There are four main types of bearings: ball bearings, cylindrical roller bearings, tapered roller bearings, and needle roller bearings. While ball bearings are the most common type of bearing, each has its advantages and disadvantages. That is why we recommend that you compare each of these bearings to determine which is the ideal bearing for your requirements.
Table of Contents
ToggleBearing types
What is the order of priority for bearing selection?
We will select the best bearing according to the order shown in the table below. Note that the following sequence is for reference only. When you actually choose which bearing to use, the most important factors are past successes and points of improvement, so there is no need to follow this order verbatim.
Order | Examination item | Major points to confirm |
---|---|---|
① | Bearing type | What magnitude and direction of load do you need? Will it fit in the installation space? |
② | Bearing arrangement | Are you using two (or ) bearings on a single shaft? |
③ | Bearing dimensions and service life | Do the dimensions and service life satisfy your needs? |
④ | Bearing limiting speed, running accuracy, fits and internal clearance | Does it have the necessary running accuracy and rigidity for the machine? Does it have the fits and internal clearance to satisfy its service life? |
⑤ | Bearing preload and rigidity | Does it have the necessary rigidity for the machine? |
⑥ | Bearing lubrication | Can the bearing rotate stably over a long period of time? |
⑦ | Components around the bearing | What bearing surrounding structure/assembly are you looking for? |
⑧ | Bearing mounting and dismounting | Will it facilitate maintenance/inspection of the machine? |
Size
The space allowed by bearings is usually quite limited. In many cases, the shaft diameter or bearing bore diameter is determined according to the design requirements. Therefore, the type and size of the bearing must meet the established specifications.
For example, a bearing used in a dentist’s drill bit is obviously much smaller than a bearing used in an oil rig.
load
When most people design a machine, they first size the shaft to meet strength requirements, and then choose the bearings accordingly. The second factor to consider is the load the bearing can carry.
There are two types of loads:
– Axial load: parallel to the axis of rotation
– Radial load: perpendicular to the axis of rotation
1) If the load is predominantly radial (perpendicular to the shaft), use a radial bearing, and if the load is predominantly axial (in the same direction as the shaft), use a thrust bearing. Axial loads are also sometimes referred to as thrust loads.
2) Ball bearings are used when the bearing load is light, and roller bearings are used when it is heavy.
3) If the radial load and axial load act on a single bearing at the same time (combined load), deep groove ball bearings or angular contact ball bearings are selected if the combined load is light. If the combined load is large, tapered roller bearings are used.
If large axial loads are applied from two directions, you can combine two or bearings, or use double row bearings.
Each type of bearing is specifically designed to support axial or radial loads. Some bearings can accommodate both loads: in this case we refer to combined loads. For example, if you must carry combined loads, we recommend that you choose tapered roller bearings. If you need a bearing that can withstand high radial loads, then we recommend cylindrical roller bearings. On the other hand, if your bearings need to support lighter loads, ball bearings may be sufficient as they are usually cheaper.
Accuracy requirements
The third major consideration when selecting a bearing is accuracy. Certain applications, such as bearings for CNC machines, require high precision. In other applications, such as shopping cart wheels, precision is not a major concern.
Flexibility, enclosure variations, and manufacturing errors may cause some misalignment. In the case of considerable misalignment, bearing failure may occur due to the unacceptable misalignment. When misalignment is an important issue, ball bearings or bearing units with self-aligning characteristics are the right choice.
Rotating speed
RPM is another factor that should be considered. Some bearings can withstand high speeds. The presence of cages in cylindrical roller bearings and needle roller bearings allows higher speeds than bearings without cages. However, choosing a higher speed sometimes comes at the expense of load. You should also consider possible misalignment; some bearings are not suitable for this, such as double row ball bearings.
Therefore, you need to pay attention to the bearing construction: insert bearings and spherical bearings can easily support these misalignments. We recommend that you prefer self-aligning bearings, which automatically correct alignment defects caused by shaft bending or mounting errors. Likewise, operating conditions are also very important when selecting the ideal bearing. Therefore, it is necessary to analyze the environment in which you will use the bearing. Your bearings can be contaminated in a variety of ways. Certain uses may cause noise disturbance, shock and/or vibration.
Durability
When it comes to durability, there are many factors to consider, including stiffness and temperature tolerance. Under load, the bearing contact surfaces can deform, which can be a serious problem in some applications. From the sub-zero temperatures that oil rigs in Alaska must contend with to the 100-degree deserts of Saudi Arabia, the range of operating temperatures a bearing can withstand should also be a major selection consideration.
Seal
The choice of sealing system is necessary to ensure the correct and long-lasting operation of the bearing; therefore, it is important to ensure that the bearing is always well protected from any impurities and external factors, such as dust, water, corrosive liquids and even used lubrication agent. This choice depends on the type of lubricant, environmental conditions (and type of contamination), fluid pressure and rotational speed. To give you a good starting point, fluid pressure is the deciding factor in selecting a sealing system. If the pressure is high (e.g. in the range of 2-3 bar), mechanical seals are ideal. Otherwise, the choice is directly related to the type of lubricant, grease or oil. For example, for grease lubrication, the most common solutions are: deflectors or washers, machined or narrow channels with grooves;
Preload
Conditions of use can also affect your choice, especially when assembling bearings. In some cases, you can add preload to a bearing assembly to increase its stiffness. In addition, preload has a positive effect on the bearing life and noise level of the system.
Note that in order to choose preload (radial or axial), you must know the stiffness of all parts through software or experimentation. In your selection criteria, you must also consider the ideal material for the bearing. Bearings can be made of metal, plastic or ceramic. Bearing material depends on its intended use. We recommend that you choose the bearings that are most resistant to compression. But keep in mind that the material used will affect the price of the bearing.
Maintain
Some bearing applications require periodic disassembly and reassembly for inspection and maintenance. In these applications, bearings with separable rings are most suitable.
When it comes to prolonging and supporting the performance of any bearing type, the importance of thorough lubrication cannot be underestimated. Over-lubrication, under-lubrication, contamination and mixed lubricants can all have an impact on bearing performance. It’s also important to consider “grease life,” the amount of time a bearing can operate between relubrications.
Why Choose Ball Bearings?
The most commonly used bearings are deep groove ball bearings. Found in almost all kinds of products in general mechanical engineering. Ball bearings are usually optimized for radial contact: this means they are useful if you want the force in contact with the bearing to be perpendicular to its axis of rotation. If ball bearings are to be used for axial loads, care should be taken that the unit supports only moderate axial loads. However, this drawback can be avoided by using a double row ball bearing structure. Ball bearings are not only low cost, but also the most compact, making them the most widely used bearing type.
Deep groove ball bearings have the following advantages:
(a) Deep groove ball bearings have a high load carrying capacity due to the relatively large size of the balls.
(b) Deep groove ball bearings bear radial and axial loads.
(c) Due to the point contact between the balls and the races, this bearing has less friction loss and the resulting temperature rise. The maximum permissible speed of the shaft depends on the temperature rise of the bearing. Therefore, deep groove ball bearings have excellent performance, especially in high-speed applications.
(d) Deep groove ball bearings generate less noise due to point contact. (e) The bore diameter of deep groove ball bearings varies from a few millimeters to 400mm.
For small bearings operating at high speeds, we strongly recommend the use of ball bearings.
Why Choose Cylindrical Roller Bearings?
Cylindrical roller bearings can withstand large radial loads, even very large radial loads. There are many types of cylindrical roller bearings. They vary according to the number of rows of rollers (one, two or four) and whether they have cages. The cage allows the bearing to support significant radial loads and high speeds. The absence of a cage allows the bearing to have rows of rollers and therefore can accommodate greater radial loads. The only disadvantage is that cylindrical roller bearings without cages cannot withstand as high speeds as cylindrical roller bearings with cages. Cylindrical roller bearings are very robust and have a long bearing life.
Point contact in ball bearings is replaced by line contact in roller bearings when maximum load carrying capacity is required in a given space. Cylindrical roller bearings consist of relatively short rollers positioned and guided by cages.
Cylindrical roller bearings have the following advantages:
(a) Cylindrical roller bearings have a very high radial load capacity due to the line contact between the rollers and raceways.
(b) Cylindrical roller bearings are stiffer than ball bearings.
(c) Low coefficient of friction for less friction loss in high speed applications.
Why Choose Tapered Roller Bearings?
Tapered roller bearings can accommodate radial, axial and combined loads (simultaneously). Due to its high stiffness, the load can be very heavy. If you are not sure about the difference between a ball bearing and a tapered roller bearing, be aware that a tapered roller bearing of the same size can handle heavier loads.
We therefore recommend this type of bearing for machine shafts, vehicle transmissions (from cars to boats, helicopters) or for steering wheels of cars or trucks.
Tapered roller bearings have the following advantages:
(a) Tapered roller bearings can withstand large radial and thrust loads.
(b) Tapered roller bearings have greater rigidity.
(c) Tapered roller bearings use separable parts and can be easily assembled and disassembled.
Why Choose Needle Roller Bearings?
As cylindrical roller bearings, needle roller bearings are available with or without cages. If they have a cage then they can withstand very high speeds whereas needle roller bearings without cages can withstand very heavy radial or axial loads. Note also that these bearings are small in size and thus have a small footprint. For example, they are often used in gearboxes.