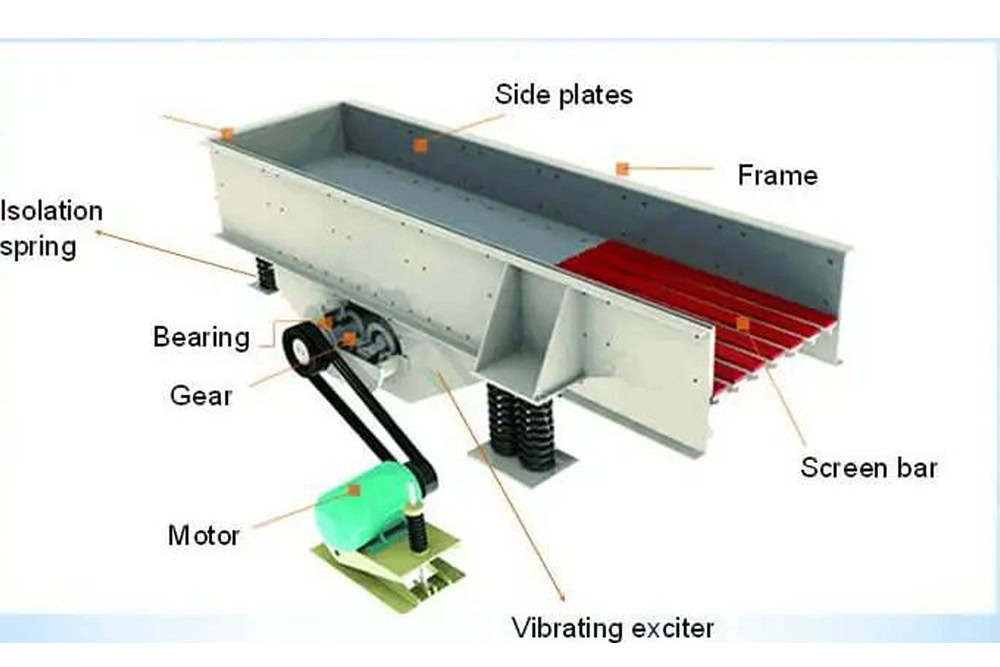
Bearing Manufacturer & Supplier
Specialize in ball bearings, roller bearings, thrust bearings, thin section bearings etc.
Guide to Selecting Vibrating Screen Bearings
Vibrating screen bearings are subject to large impact loads during operation. The centrifugal force and centrifugal acceleration generated by the high-speed rotation of the eccentric block are also large. In addition, there is a lot of dust in the working environment, so the type of bearing, limit speed, installation fit, clearance, self-lubricating performance, etc. are required to be high. Generally speaking, bearings are easily damaged when working under such harsh conditions. If the bearing is not properly selected at the beginning of the design, it will greatly affect the service life of the bearing. Based on many years of bearing manufacturing experience, Aubearing summarizes the guide to selecting vibrating screen bearings.
Commonly used vibrating screen bearings generally include cylindrical roller bearings and spherical roller bearings. Cylindrical roller bearings have a large radial load capacity, a high limit speed, and a strong load capacity for dynamic and static loads, but have high requirements for the coaxiality of the bearing seat hole. Spherical roller bearings not only have a large radial load capacity, but also can withstand axial loads in any direction, have good aligning performance, and can compensate for the different axiality problems caused by the bearing seat hole. However, spherical roller bearings cannot withstand pure axial loads. Due to the harsh operating environment of the vibrating screen, many bearing manufacturers design large clearance, special materials and structures for the vibrating screen, so that it has strong load-bearing capacity, good impact resistance and good lubrication performance.
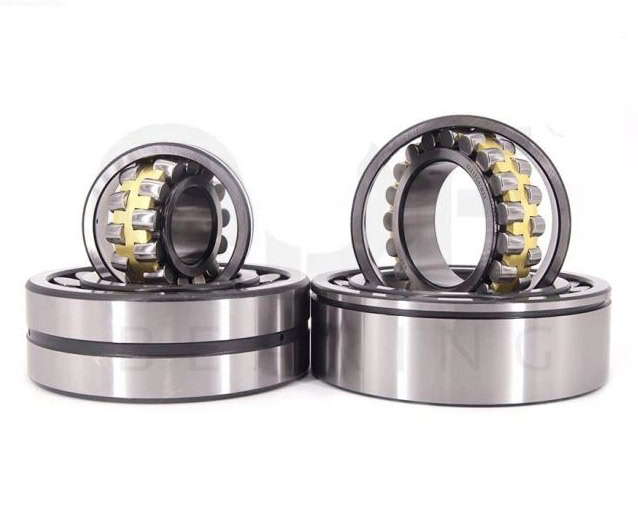
Table of Contents
ToggleWhat are vibrating screen bearings?
Used to sort and grade materials such as minerals, aggregates and ores, vibrating screen bearings are specifically designed to withstand the harsh conditions of vibration. Vibrating screen bearings can withstand the strong vibrations and high loads generated during operation. These bearings help screen machines operate efficiently and minimize downtime, which is critical in industries where productivity and equipment reliability are critical. Vibrating screen bearings usually work in an environment with high humidity, dust particles, high speeds, and strong vibration shocks, so it is necessary to select bearings that can withstand these harsh conditions.
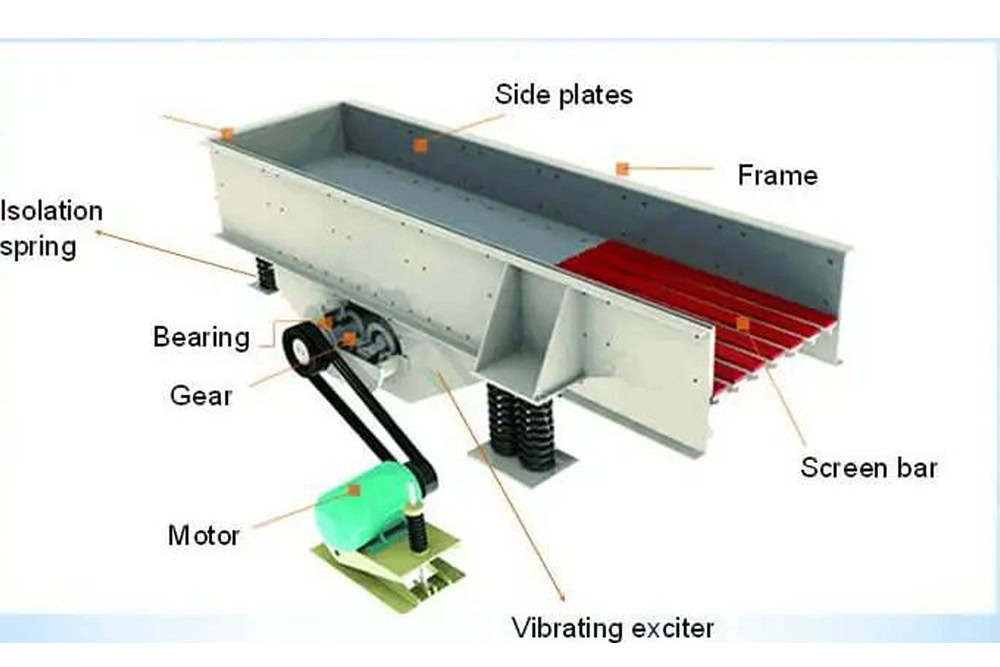
Solution 1: Vibrating screen bearing type
Vibrating screen bearings are mostly used in mining vibration machinery and equipment, vibration machinery, and vibration motors, and are one of the most critical components of such equipment. Common types include spherical roller bearings, cylindrical roller bearings, and tapered roller bearings. They all have strong load-bearing capacity, good impact resistance, high reliability, good lubrication performance, and can overcome shaft deflection.
Spherical roller bearings
Spherical roller bearings are a common bearing type on vibrating screens. They have the characteristics of large load-bearing capacity, low friction, and wide applicability. They can withstand radial and axial loads and are suitable for high-speed, high-precision, and high-reliability vibrating screen equipment. . Spherical roller bearings have double-row rollers. The outer ring has a common spherical raceway. The inner ring has two raceways and is tilted at an angle relative to the bearing axis. This structure gives it good automatic self-aligning performance and is not easily affected by the angle between the shaft and the bearing housing seat or the shaft bending. It is suitable for installation errors or angle errors caused by shaft deflection.
Cylindrical roller bearings
Cylindrical roller bearings are commonly used bearing models for heavy-load, medium and low-speed vibrating screens. They have the characteristics of strong load-bearing capacity, high temperature resistance, and wear resistance. Cylindrical roller bearings have a large radial load-bearing capacity, a high limit speed, and a strong load-bearing capacity for dynamic and static loads, but have high requirements for the coaxiality of the bearing seat hole.
223 series: 22308, 22309, 22310, 22311, 22312, etc. This bearing is suitable for most vibrating screen equipment. Its main feature is good fault tolerance, which makes the vibrating screen stable during startup and operation.
233 series: 23318, 23320. This bearing adopts a unique flange structure, which can effectively avoid stress accumulation and deformation, and improve the working life of the equipment.
Tapered roller bearings
Tapered roller bearings are also a type of bearing commonly used in vibrating screens. They are characterized by large load-bearing capacity, wear resistance, and good adjustability. This type of bearing is suitable for medium and high speed vibrating screens. It has good radial and axial load bearing capacity and can automatically adjust the angle between the bearing and the base to meet the rotor operation requirements of the equipment.
Solution 2: Materials and Quality
The foundation of reliable vibrating screen bearings lies in the materials from which they are made. High-grade steel ensures that the bearings can withstand the rigors of demanding applications. Generally, vibrating screen bearings are made of vacuum degassed bearing steel, aluminum-iron-manganese bronze for the cage, and high-strength materials for the inner and outer rings and rolling elements, which have good fatigue resistance. In contrast, ordinary bearings are made of ordinary bearing steel and zinc brass, which have low strength, poor elasticity, and inferior wear and fatigue resistance to special vibrating screen bearings.
Heat treatment: Heat treatment is a key process to strengthen steel, making it resistant to wear and fatigue. Vibrating screen bearings undergo special heat treatments such as Bayer-Martens mixed quenching or Martens quenching + high-temperature tempering to ensure uniform hardness, low internal stress, good toughness, and resistance to shock and vibration.
Corrosion resistance and long life: Bearings often operate in environments where moisture and other corrosive elements are present. A high level of corrosion resistance not only maintains the integrity of the bearing, but also ensures its long-term smooth operation. This is essential to maintain performance under challenging conditions.
Solution 3: Design and precision manufacturing
The design and manufacturing process of special bearings for vibration screens are also different from those of ordinary bearings, including the increase in rolling element diameter and length, the outer ring rib guiding the rollers to reduce the force on the rollers, the inner ring rib guiding the rollers to improve roller operation, and the cylindrical roller bearing cage adopts an integral structure to improve strength. In addition, the inner and outer diameter tolerances of special bearings for vibration screens are very small, the rolling element size difference is ≤0.002, the outer diameter of the cylindrical roller has a convexity to avoid stress concentration, and the rolling surface is super-finished for high finish.
Solution 4: Load capacity
The relationship between static load and dynamic load is an important factor.
Static load rating: Although the dynamic load rating is important, the static load rating is equally important when the bearing is not moving. The static load capacity ensures that the bearing can support the necessary weight without deformation or failure. The static load will affect the structural strength and stability of the vibrating screen. If the static load is too large, it will cause the vibrating screen to be unstable and even deform. Therefore, in the design process of the vibrating screen, it is necessary to reasonably control the size of the static load to ensure the structural strength and stability of the vibrating screen.
Dynamic load rating: Dynamic load rating refers to the ability of the bearing to withstand different loads during operation. The size of the dynamic load will also affect the screening effect of the vibrating screen. If the dynamic load is too large, the material will not be able to vibrate fully on the screen surface, affecting the screening effect. Therefore, in the design and production process of the vibrating screen, it is necessary to reasonably control the size of the dynamic load to improve the screening efficiency of the vibrating screen.
In order to ensure the structural strength and stability of the vibrating screen, the size of the static load needs to be reasonably controlled. This can be achieved by controlling the weight of the vibrating screen, such as avoiding a large amount of material from accumulating on the screen surface during the use of the vibrating screen to reduce the size of the static load. In order to improve the screening efficiency of the vibrating screen, it is necessary to reasonably control the size of the dynamic load. This can be achieved by adjusting the vibration frequency and amplitude of the vibrating screen, so that the material can fully vibrate on the screen surface and improve the screening efficiency. At the same time, the screening efficiency can be further improved by optimizing the shape and size of the screen holes and selecting the appropriate screen mesh.
Solution 5: Vibration and noise
Vibration affects life: The vibrating screen works by relying on the centrifugal force of the eccentric block to generate vibration force. If the eccentric force deforms the eccentric shaft and bends, the inner and outer bases of the bearing will deflect relative to each other, and the motion trajectory of the rolling elements will change, thus increasing the vibration noise. Excessive vibration will cause premature wear of the internal components of the bearing, thereby shortening the life of the bearing. It is important to test the vibration level of the vibrating screen bearing to ensure that the bearing can operate smoothly under the expected conditions.
Noise as an indicator of bearing health: Noise is often an early warning sign of bearing failure. Abnormal or excessive noise during operation may indicate problems such as improper lubrication, misalignment or internal damage. Frequent noise testing can help detect and prevent potential failures early.
Vibration and noise testing procedures: Implementing a strict vibration and noise testing procedure is essential to verify the quality of vibrating screen bearings. These tests should simulate actual operating conditions to ensure that the bearings can operate reliably in the field.
Solution 6: Lubrication and sealing efficiency
Lubrication is critical to the performance and life of bearings. Proper lubrication reduces friction, reduces wear and helps dissipate heat. If lubrication is insufficient, bearings will degrade quickly, resulting in expensive downtime and repairs. The seals used in bearings affect their ability to maintain lubrication and prevent contaminants from entering. Different applications require different types of seals, and choosing the right seal is critical to ensuring efficient operation and long service life of bearings.
Common seals are mainly made of three materials: rubber seals, silicone seals and polyurethane seals. Rubber seals are the mainstream in the current market. Silicone and polyurethane seals are mainly used for special materials (such as high temperature, oily, highly corrosive materials, etc.).
Silicone sealing rings have strong sealing performance, can be used for waterproofing and preservation, and are completely non-toxic and tasteless. Even if heated under high temperature conditions, they will not deform or produce harmful substances. Silicone sealing rings are resistant to high and low temperatures, have good aging resistance, high temperature resistance, and meet FDA and SGS standards. Silicone sealing rings are also cold-resistant and heat-resistant. Cold resistance: The temperature of ordinary rubber is -20°-30°, while silicone still has good elasticity at -60°-70°. Some specially formulated silicone can also withstand extremely low temperatures. Silicone can be used for a long time in a high temperature environment of up to 150° without deformation. It can be used continuously for 10,000 hours at a high temperature of 200°, and can even be used for a period of time at a high temperature of 350°. The heat resistance of silicone can be seen. Therefore, the cost is slightly higher.
Rubber sealing rings are commonly used sealing ring accessories for vibrating screen equipment. Because of their low cost and stable performance, they are currently standard for vibrating screens. However, rubber sealing rings are not suitable for materials with corrosive, high temperature, and high oil content. Usually, if the user’s materials do not have special requirements, the vibrating screen manufacturer will choose to install rubber rings as seals when the vibrating screen leaves the factory.
Polyurethane seals are rarely used in vibrating screens because of their high cost. Polyurethane plastic is known as the “king of wear resistance” and has a wide and adjustable hardness range (Shore 10A-73D). Polyurethane seals are very good at oil resistance, corrosion resistance, and high temperature resistance, and can adapt to temperatures from -40 to 80 degrees. It has good elasticity, and the shape becomes smaller after long-term pressure, and it can be used for a long time to resist aging. Generally, when screening materials with special characteristics, users should choose to install polyurethane seals.
Solution 7: Wear Resistance Assessment
The hardness of the bearing surface directly affects its wear resistance. Bearings with higher surface hardness are durable and able to withstand the wear conditions often encountered in industrial applications. Assessing bearing surface hardness is therefore a weight-based quality check. Advanced coating technology can significantly improve the wear resistance of bearings. Coatings such as chrome or ceramic provide an extra layer of protection against wear and corrosion, extending the life of the bearing.
Solution 8: Tolerances and Clearances
The tolerance level of vibrating screen bearings is generally required to be at least P5 level, and the clearance is C4 level.
Tolerances: Tolerance classes define the allowable variation in bearing dimensions. Precise tolerances are critical to ensuring a bearing is a perfect match for the application. Tight tolerances improve operating efficiency, reduce friction and minimize the risk of premature wear. Ensuring that all critical dimensions are within specified tolerances is a critical aspect of quality control.
Clearance: Vibrating screen bearings generally adopt C4 level. C3 and C4 are bearing tolerance classes and are used to describe the internal clearance of the bearing. The internal clearance of C4 grade bearings is larger than that of C3 grade bearings. When running at high speed, C3 grade bearings generate less heat, but at the same time they are susceptible to external factors, such as vibration, impact, etc. The C4 level bearing has large internal clearance and has better heat dissipation when running at high speed, but it is also stable and is suitable for use in equipment such as vibrating screens.
Conclusion
When selecting vibrating screen bearings, it is necessary to comprehensively consider factors such as specific equipment size, load, and working environment to select the appropriate bearing model. At the same time, attention needs to be paid to the size, clearance, and load-bearing capacity of the bearing to ensure that it can meet the working needs of the equipment. In addition, attention needs to be paid to the installation and maintenance of bearings so that they can operate properly and extend their service life. During installation, it is necessary to ensure the matching dimensional accuracy of the bearing and the bearing seat to avoid causing rotational imbalance; during use, regular inspection and lubrication maintenance are also required to ensure the normal operation of the bearing and equipment.