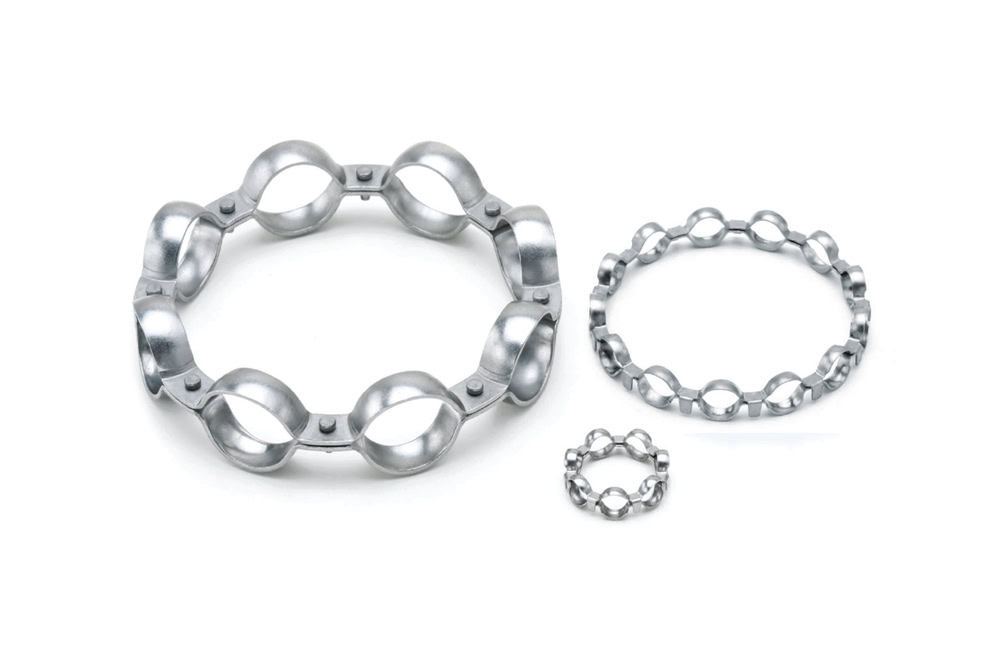
Bearing Manufacturer & Supplier
Specialize in ball bearings, roller bearings, thrust bearings, thin section bearings etc.
Guide to Bearing Cages
The main function of bearing cages is to isolate and guide the rolling elements in the raceways. Bearing cages can ensure the proper distance between rolling elements, prevent them from contacting each other to achieve the purpose of reducing friction; can evenly distribute the load force; guide and improve the rolling conditions of the bearing rolling elements to prevent damaging sliding. The design and material of the cage determine its performance and bearing reliability; it enables it to withstand stress caused by friction, strain and inertia force and chemical corrosion caused by lubrication or aging substances, solvents, etc. This blog aims to provide you with constructive suggestions for choosing the right bearing cage by introducing the types of cages, breakage and prevention measures.
Table of Contents
ToggleTypes of Bearing Cages
The materials used to make cages are usually required to have high strength, good thermal conductivity and wear resistance, small friction factor and density, strong impact toughness, etc.; and its expansion coefficient should be close to that of the rolling elements. For stamped cages, the manufacturing material should also have certain processing properties. According to the manufacturing materials, the types of cages usually include: low carbon steel cage/stainless steel cage, bakelite cage/nylon cage, brass cage/bronze cage/aluminum alloy cage, etc.
Stamped steel cage
Stamped steel cages are mostly made of continuous hot-rolled low carbon thin steel plates or X5CrNi18-10 stainless steel; they are a light cage with high strength and can reduce friction and wear through further surface treatment.
Machined steel cages
Machine-cut steel cages are usually made of S355GT (St 52) steel; they are mostly used in large bearings or applications where there is a risk of chemical reaction with copper cages; they can operate at temperatures up to 300°C and their performance is generally not affected by minerals or lubricants and organic solvents used to clean bearings, but sometimes they need surface treatment to improve their performance in terms of anti-sliding and wear resistance.
Stamped brass cages
Stamped brass cages are mainly used for small and medium-sized bearings; however, for similar applications such as refrigeration compressors using ammonia, stamped copper cages are prone to cracking.
Machined brass cages
Most brass cages are made of CW612N cast brass or forged brass, and their performance is generally not affected by bearing lubricants such as synthetic oils and greases, and organic solvents used for cleaning. However, the operating temperature of brass cages should be below 250°C.
Nylon cages
The polyamide (nylon 66) solid cage made by injection molding has high material elasticity and light weight, which can ensure that the bearing cage has good sliding and self-lubricating properties. It can be used in working environments with vibration shock, high speed change or inclination of the inner and outer rings of the bearing; the operating temperature range is relatively wide, between -40°C and 120°C. However, the use of polyamide nylon cages needs to consider the influence of corrosive components in the lubricant; and the material will dehydrate and become brittle in a vacuum.
Bearing cage code
Code | Description |
A or B after retainer code indicates the retainer is guided by the outer ring (A) or inner ring (B). | |
F | Steel solid retainer, guided by the rolling elements. |
FA | Steel solid retainer, guided by the outer ring. |
FAS | Steel solid retainer, guided by the outer ring, with lubrication groove. |
FB | Steel solid retainer, guided by the inner ring. |
FBS | Steel solid retainer, guided by the inner ring, with lubrication groove. |
FN | Steel solid retainer, guided by the rolling elements. |
E, H1 | Phenolic resin retainer. |
FP | Steel solid pin type retainer, guided by the outer ring. |
FPA | Steel solid pin type retainer, guided by the outer ring. |
FPB | Steel solid pin type retainer, guided by the inner ring. |
FV, FVI | Steel solid retainer with centrifugal cast, vibration proof, quality adjustment. |
LA | Light alloy solid retainer, guided by the outer ring. |
LAS | Light alloy solid retainer, guided by the outer ring, with lubrication groove. |
LAB | Light alloy solid retainer, guided by the inner ring. |
LBS | Light alloy solid retainer, guided by the inner ring, with lubrication groove. |
LP | Light alloy solid pin type retainer, guided by the outer ring. |
LPA | Light alloy solid pin type retainer, guided by the outer ring. |
LPB | Light alloy solid pin type retainer, guided by the inner ring (thrust ball bearing guided by the shaft). |
M | Brass solid retainer, guided by the rolling elements. |
MA | Brass solid retainer, guided by the outer ring. |
MAS | Brass solid retainer, guided by the outer ring, with lubrication groove. |
MB | Brass solid retainer, guided by the inner ring. |
MBS | Brass solid retainer, guided by the inner ring, with lubrication groove. |
MR | Brass solid retainer, guided by the rolling elements. |
MPA | Brass solid pin type retainer, guided by the outer ring. |
MPB | Brass solid pin type retainer, guided by the inner ring (thrust ball bearing guided by the shaft). |
T | Polyamide resin press-formed solid retainer, guided by the outer ring. |
TA | Polyamide resin press-formed solid retainer, guided by the rolling elements. |
T1 | Polyamide resin press-formed solid retainer, guided by the rolling elements. |
THB | Polyamide resin press-formed pin type retainer, guided by the inner ring. |
TP | Polyamide resin press-formed pin type retainer, guided by the outer ring. |
TPA | Polyamide resin press-formed pin type retainer, guided by the outer ring. |
TPB | Polyamide resin press-formed pin type retainer, guided by the inner ring. |
TN | Polyamide resin press-formed retainer, guided by the rolling elements, use material code indicated by numbers. |
TNH | Polyamide resin press-formed retainer, guided by the rolling elements. |
TVH | Glass fiber reinforced polyamide resin press-formed retainer, guided by the rolling elements. |
TV1 | Glass fiber reinforced polyamide resin press-formed pin type retainer, guided by the steel balls. |
TVP | Glass fiber reinforced polyamide resin press-formed retainer, guided by the rolling elements. |
TVP2 | Glass fiber reinforced polyamide resin press-formed retainer, guided by the balls. |
TVPB | Glass fiber reinforced polyamide resin press-formed pin type retainer, guided by the inner ring (thrust ball bearing guided by the shaft). |
J | Steel stamped retainer. |
During the operation of rolling bearings, heating and wear will occur due to sliding friction, especially in high temperature or high speed applications, which may cause the cage to burn or break directly. Improper assembly or use will cause deformation of the cage, increase friction between it and the rolling element, and may cause the rolling element to get stuck, or cause friction between the cage and the ring, loosening or breaking of rivets, etc., resulting in cage rupture. If used continuously, abnormal working conditions such as vibration, noise and heating will be aggravated, leading to bearing damage. There are usually several reasons for the damage of bearing cages:
1) Excessive torque load
2) Too high speed or too frequent speed changes
3) Poor or insufficient lubrication
4) Foreign matter stuck or impurities intruded
5) Large vibration working environment
6) Improper installation
7) Abnormal temperature rise
1) Select the appropriate bearing model according to the use conditions
2) Check the lubrication conditions and use the appropriate lubrication method and lubricant
3) Correct selection of cage materials and types
4) Pay attention to the installation and use of bearings
5) Select bearings that meet the rigidity requirements of the bearing box
Conclusion
Under the working conditions of complex loads and high-speed rotation, the centrifugal force, impact and vibration that the rolling bearing cage needs to withstand will be relatively large, and the sliding friction between the cage and the rolling element will also generate a lot of heat. Leading to cage failure, even burns and fractures. Therefore, the cage material must have a certain strength, good thermal conductivity, wear resistance, impact toughness, small friction, density, and its linear expansion coefficient is close to that of the rolling element. In addition, in order to cope with complex stamping deformation, the cage material must also have good processing performance.
The selection of cage materials also needs to consider the effects of chemical media such as lubricants, lubricant additives, organic solvents and coolants, and special uses and working conditions such as high temperature resistance, corrosion resistance, self-lubrication (used in vacuum) or non-magnetic.