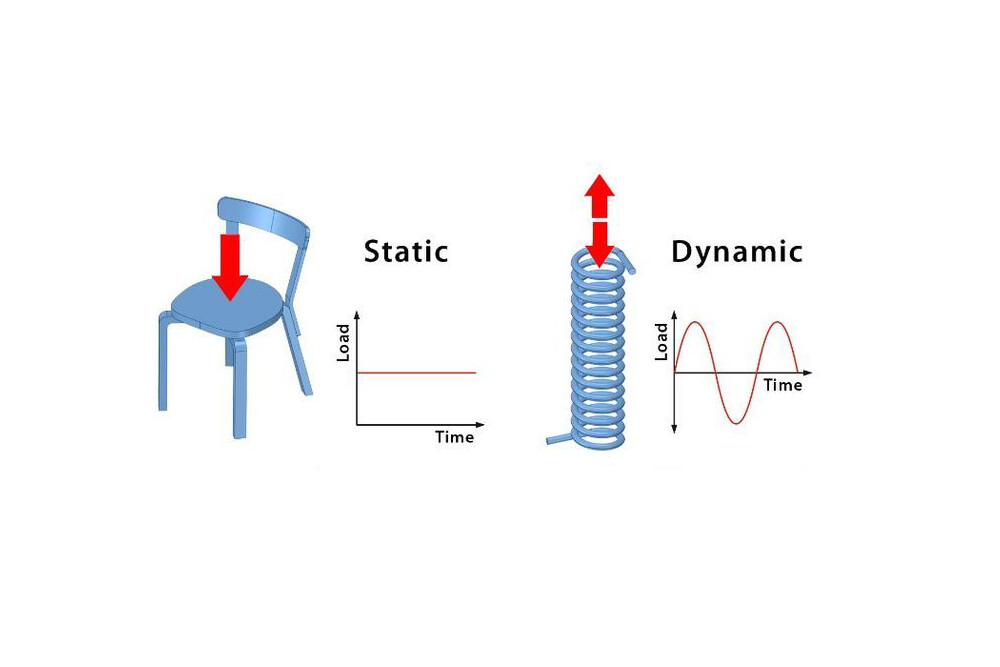
Bearing Manufacturer & Supplier
Specialize in ball bearings, roller bearings, thrust bearings, thin section bearings etc.
Guidance on Bearings Static Loading
Static load and dynamic load are crucial to the normal operation of the bearing and are important indicators of the bearing’s load capacity. Static load refers to the bearing’s ability to withstand load in a static state. In this blog, Aubearing will delve into the importance of static loading in selecting the right bearing.
Table of Contents
ToggleWhat is bearing static load?
Following the ISO 14728-2 definition, static load C 0 is the amount of load a bearing can withstand before the sum of ball and raceway deformations equals 0.01% (0.0001 times) of the ball diameter. However, the standard has been updated to specify load levels that can produce 480,000 pounds per square inch (psi) [3,310 megapascals (Mpa)] Hz contact stress in the raceway. However defined, the static load capacity of a bearing is almost always higher than the dynamic load capacity. The plastic deformation of the ball and raceway materials that occurs when a load is applied to a bearing in a static (not moving) or slowly moving state. If this deformation is exceeded, the running characteristics of the bearing will decrease, resulting in increased vibration, noise and friction.

Although static load capacity is not a parameter used in calculating bearing life, it is an important parameter in measuring bearing performance. Some examples of static loads include pressure, impact loads, and holding forces. For example, when the bearing is stopped rotating and the drill bit is operating, the bearing will be subject to static load. Similarly, when a bearing is subjected to a momentary impact when it first starts rotating, it is subject to a static load. Shock and vibration, on the other hand, are often caused by conditions that are random, unpredictable, and/or difficult to quantify. Needless to say, exceeding the static load capacity will definitely impair bearing performance.
Calculate bearing static load
The static load of a bearing refers to the maximum load it can bear without permanent deformation. Calculating static load carrying capacity is critical to ensuring a bearing is suitable for a specific application. Next, Aubearing will discuss the formulas and methods for calculating the static load carrying capacity of bearings. Calculating static bearing loads involves several factors, including bearing geometry, materials and manufacturing processes. The general calculation formula for bearing static load is as follows:
C0 = (P0 / F0) x C
C0 is the static load carrying capacity
P0 is the static load exerted on the bearing
F0 is the appropriate load factor
C is the basic dynamic load rating of the bearing
The load factor F0 takes into account bearing type, load direction, lubrication conditions, and other factors that may affect bearing performance. It is usually provided by the bearing manufacturer and can also be found in bearing catalogs. Determine the static load P0 applied to the bearing in Newtons (N) or pounds (lbs). This can be calculated based on the weight of the equipment or machinery the bearing supports.
Determine the load factor F0 based on the bearing type and other relevant factors. This factor can be obtained from the bearing manufacturer or from a bearing catalog.
Determine the basic dynamic load rating C of the bearing, which is the value provided by the bearing manufacturer. It indicates that the bearing can operate a load of one million revolutions without failure.
Bearing static safety factor
Static loading is usually an unexpected and difficult to quantify impact on the bearing. Therefore, bearing manufacturers recommend that a static safety factor be calculated based on the type of application and operating conditions. The static safety factor is the ratio between the basic static load rating and the maximum combined static load applied to the bearing. This can range from 2 for smooth operating conditions where the risk of vibration is low, to 5 or 6 for applications that may be subject to severe shock loading.
S 0 = static load safety factor
C 0 = static load capacity
F 0max = maximum combined static load
When forces and moments exist simultaneously, the resultant static load (also called the equivalent static load) should be calculated and used to determine the static load safety factor. Additionally, in general, if the applied load is less than 2.8 times the bearing preload, the preload must be taken into account in the resulting static load calculation.
Factors affecting static load
It is worth noting that there are many factors that affect the static load capacity of bearings, including:
Materials and heat treatment processes
Factors such as bearing design, quality, materials, and technology will all affect the rated static load of the bearing; the material and heat treatment process determine performance parameters such as hardness, toughness, and fatigue limit, which have a key impact on the service life of the bearing. Therefore, in bearing design and manufacturing, attention should be paid to the selection and control of materials and heat treatment.
Bearing geometry
The geometric structure of a bearing is one of the important factors influencing its load-bearing capacity and service life. Reasonable bearing geometry can effectively reduce bearing wear and fatigue damage and increase bearing service life.
Temperature
Due to the principle of “thermal expansion and contraction”, the static load-bearing capacity of the bearing is affected by temperature. When the temperature increases, the molecular structure inside the bearing will “expand” and its load-bearing capacity will decrease. High temperatures can cause bearing materials to soften or lose strength.
Time
The static load carrying capacity of a bearing is based on short-term loads, usually only a few seconds. If a bearing is subjected to static load for a long period of time, it will cause fatigue of the bearing material and reduce its static load capacity.
Vibration and shock
The static load carrying capacity of the bearings is not suitable for applications with vibration or shock loads. Even if the load is within the static load carrying capacity, vibration and shock loads can cause bearing deformation or failure.
lubricating
The static load carrying capacity of a bearing assumes that the bearing is adequately lubricated. Even if the load is within the static load carrying capacity, insufficient lubrication can cause bearing failure.
Alignment
The static load carrying capacity of a bearing assumes perfect bearing alignment. Even if the load is within the static load capacity, misalignment can cause bearing failure.
Importance of static load capacity in bearing selection
The static load capacity of a bearing is related to many factors, such as material composition, design and manufacturing process. Bearings with higher static load capacities are usually made of stronger materials and can handle heavy loads. In contrast, bearings with lower static load capacities are usually made of softer materials and are suitable for lighter loads.
When the load exceeds its static load capacity, it may cause permanent deformation or damage to the bearing, affecting its performance and life. For example, if a bearing is subjected to a heavy load that cannot be supported, plastic deformation may occur, leading to increased friction, vibration, noise, reduced efficiency, etc. In extreme cases, bearings can fail completely, leading to costly downtime and potential risks.
To ensure that a bearing has adequate static load carrying capacity, it is crucial to consider several factors during the selection process. These factors include expected loads, operating conditions, and required reliability and performance levels. The type of bearing, such as ball bearings, angular contact bearings, tapered roller bearings, cylindrical roller bearings or plain bearings, must also be considered, as each type has its own unique static load carrying capacity characteristics. Aubearing’s online store displays than 40,000 types of bearings, all of which are marked with static and dynamic load capacities.
Conclusion
Static load carrying capacity is important when selecting bearings for any application. Bearings with a higher static load carrying capacity can provide better performance, reliability and service life, while bearings with a lower static load carrying capacity can lead to premature failure and safety risks. By considering the expected loading and operating conditions as well as the required reliability and performance levels, engineers can select the most suitable bearing with the appropriate static load carrying capacity for the application. If you have any questions about the static load of bearings, please contact Aubearing’s online engineers in time and we will answer your questions at any time.