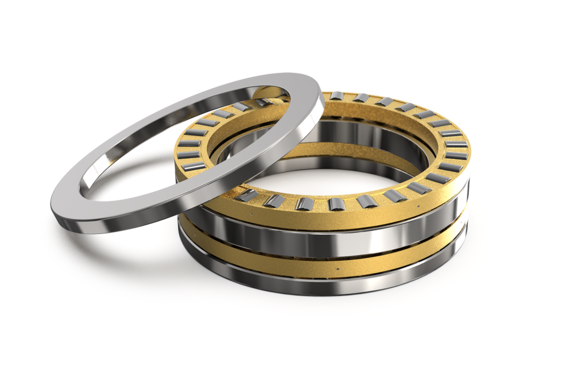
Bearing Manufacturer & Supplier
Specialize in ball bearings, roller bearings, thrust bearings, thin section bearings etc.
Everything You Should Know About Thrust Bearings
A thrust bearing is a rotary bearing that rotates between parts to reduce friction and is designed to support axial loads (mainly for low speed applications). It is an axial bearing that allows rotation between components. Thrust bearings are used when axial forces are too high to be transmitted using radial ball bearings or when rigid guidance is required.
As a global leader in the bearing manufacturing industry, AUB provides custom thrust bearing solutions to lead your industry. We find solutions to get the bearings you need and shorten your lead times. Whether modifying, manufacturing or repairing bearings to your specifications, we are here to help. In this article, we discuss thrust bearings, from design to applications and .
Table of Contents
ToggleThrust Bearing Type
Thrust bearings bear forces in the same direction as the shaft. They can be divided into two categories: thrust ball bearings and thrust roller bearings. Thrust ball bearings are used to provide high performance, while thrust roller bearings are often used in applications requiring high load carrying capacity.
Thrust ball bearing
Thrust ball bearings use balls as rolling elements and are designed to bear axial loads. Ball rolling elements enable them to withstand higher rotational speeds, but they cannot withstand high axial loads compared to cylindrical rolling elements. Their different design types are as follows:
Single direction thrust ball bearings
A single direction thrust ball bearing can handle axial loads only in one direction and can locate a shaft only in the axial direction. However, they are not suitable for radial loads.
Single direction thrust ball bearings have a shaft and housing washer with a raceway, and a ball and cage assembly, as seen in Figure 2. Housing washers come with flat or sphered seating surfaces. A bearing with a sphered washer can compensate for initial misalignment if it is used with a washer with sphered seat. These bearings are separable and the components can be mounted individually, making assembling the bearings simple.
Double direction thrust ball bearings can handle axial loads in both directions. However, they are not suitable for radial loads. The components of a double direction thrust ball bearing are a shaft washer with raceway on each face, two assemblies with ball and cage, and two housing washers with raceways. The housing washers can either be flat or spherical, depending on the application. Bearings with spherical housing washers can compensate for initial misalignment if used with seating washers that have a correspondingly spherical surface.
Full Complement Thrust Ball Bearings
Full complement thrust ball bearings carry axial loads but not radial loads. They consist of a shaft ring with an inner diameter slightly smaller than the race, a race with an outer diameter slightly larger than the race, and a complete set of balls. A full complement bearing means that the ball elements are not contained in the cage. This allows the maximum number of balls to be placed between the raceways. This allows for higher load carrying capacity, but disadvantages include lower maximum speed and greater rotational torque from ball to ball friction.
ANGULAR CONTACT THRUST BALL BEARINGS
As opposed to single direction thrust ball bearings with grooved raceways the raceways for Angular contact thrust ball bearings are designed so that under certain contact angles the forces are transferred from one ball path to the other. Because of the contact angle, one shoulder on the shaft washer and one shoulder on the housing washer is raised up. The bearing contact angle ensures rigid guidance of the balls of the axially preloaded bearing. For high speed machine tool spindles where rigid guidance is required the single and double acting angular contact thrust ball bearings are ideal.
Thrust roller bearings
Thrust roller bearings have cylinders as their rolling element and are designed to handle axial loads. The cylindrical rolling element allows them to handle a higher load than thrust ball bearings, but at lower speeds. The varying design types of them are below:
Single direction cylindrical roller thrust bearings carry axial loads in one direction, and are not suitable for radial loads. They consist of a shaft washer with an inside diameter smaller than the housing washer, and the housing washer has an outside diameter which is bigger than the shaft washer. The final parts are the rollers and cage.
Double direction or two-way cylindrical roller thrust bearings handle axial loads in either direction but are not suited for radial loads. They consist of a shaft washer with an inside diameter smaller than the housing washer, two housing washers with an outside diameter larger than the shaft washer, as well as two assemblies with rollers and cages.
For applications that space is critical, thrust needle bearings are a good solution while also providing a high degree of stiffness. These bearings can accommodate very high speeds, but only for axial forces. Needle bearings often have either just one raceway or none, instead, adjacent machine parts act as raceways, such as in gear assemblies. Consequently, the bearing occupies no space than a washer. Due to the small deviation in diameter of the rollers within one assembly, these bearings are capable of handling heavy axial and peak loads. A slight relief is typically provided at the roller ends to modify the contact area between the raceway and rollers in order to prevent stress peaks.
Tapered roller thrust bearings can be either single or double direction. They have a high carrying capacity for their small cross section, long service life, and can handle medium and heavy combined radial and axial loads. These qualities make them suitable for a wide range of industrial and automotive applications. As a result of the rollers’ tapered shape, the load is evenly distributed between the rollers. In addition, the rollers’ shape and design reduce friction and heat generation.
Thrust bearings with spherical rollers are widely used in applications involving heavy axial and simultaneous radial loads. They are self-aligning and can accommodate misalignment. Due to their low coefficient of friction, spherical roller thrust bearings require less maintenance. Due to the cage design and conformity between rollers and washers, these bearings can operate at relatively high speeds.
Spherical roller thrust bearings have separable washers, making it possible to mount and dismount the housing washer independently from the shaft washer and roller and cage assembly. It also makes it much easier to perform routine inspections, allowing for a constant lubrication level at all times.
Thrust Bearing Specifications
Bearing geometry, identified in metric or imperial units, must equate to the application’s housing allocation.
Shaft washer diameter is the measurement across the bore hole, which is the interface for a shaft. This equates to the inner diameter of a non-thrust bearing.
Housing washer diameter is the straight-line measurement between antipodal points on this component, which is engraved with a raceway for rolling elements.
Width is the measurement across the bearing side which is parallel to the shaft axis; this can also been viewed as the “height” of the bearing.
Minimum load
To stably operate at high speeds, the bearing must have a minimum load applied to rolling elements and raceways. This prevents damage to internal components from excessive friction. The following table provides formulas to determine this for each of the basic thrust bearing-types.
Dynamic and static thrust load
Dynamic load represents the mechanical burden on the bearing while in operation, while static loading is the burden experienced by the bearing while at rest. In most instances, the applied thrust load is equal to both the dynamic and static load. Both specifications are important to thrust bearing selection, and also help determine the expected bearing lifespan.
Lifespan
After determining some of the above dynamic load values, the lifespan of the bearing becomes calculable.
Operating temperatures
The acceptable operating temperature is determined by the equipment requirements, potential lubrication and service limitations of the bearing, the bearing materials, and the service life expected. A bearing’s equilibrium temperature is the temperature under which heat is created in the bearing at the same rate it is exhausted. However, this is an ideal and not practical for many applications. Heat is accumulated by friction in the bearing, ambient environmental temperatures, and other heat-producing machinery. Heat is dissipated by lubricants, the materials and masses of the bearing, the surface area of the bearing, and the exchange of air within bearing components.
Precision tools will be highly affected by thermal expansion, but most industrial equipment is less sensitive. Transient conditions will peak temperatures before stabilizing, due to uneven heating across bearing components. New bearings will also produce very high temperatures before “breaking in.”
Most standard bearing steels cannot sustain temperatures above 275° F, but manufacturers will temper steel for suitable applications, raising the steel’s temperature threshold to 800° F. Above this temperature, cobalt alloys express resistance to thermal changes and oxidation.
BENEFITS/IMPORTANCE OF THRUST BEARINGS
Thrust ball bearings offer many benefits that make them an important component in a wide range of applications. Their benefits include:
High reliability
High load capacity
Withstands harsh environments
Easy mounting and dismounting
Various types to suit different needs
High availability
Lowest friction of all rotary bearings
Runs cool at high speeds
THRUST BEARING APPLICATIONS/INDUSTRIES
A variety of applications and industries rely on thrust bearings, such as centrifuges and various medical equipment. Other common applications include:
Automotive. Thrust bearings are used in vehicles to support axial forces caused by helical gears in modern vehicle gearboxes. They are also ideal for higher speed automotive applications that require oil lubrication.
Transportation. Thrust bearings are very important for the transportation industry as they allow for powerful and improved engines and propellers.
Generators and water turbines. Certain types of thrust bearings are capable of reducing friction and drag, making them ideal for generators and water turbines.
Heavy-Duty Machinery. Thrust bearings with high load ratings are suitable for heavy-duty machinery, such as drills and cranes.
Industrial Machinery. Several types of industrial machinery have a need for rotating shafts, making thrust bearings a crucial component.
Mining & Construction. Thrust bearings are typically made using corrosion-resistant materials, allowing them to support axial loads in equipment used in demanding mining and construction environments.
Causes of Thrust Bearing Failure and How to Avoid It
When a bearing does fail, it is critical to determine the exact cause so adjustments can be made. The three most common causes of thrust bearing failure are contamination, misalignment and overloading.
1. Contaminants – Contaminants are one of the main causes of bearing failure. Airborne dust, dirt, sand and water are what you will most often encounter, but chemicals and caustics can also damage bearings.
Things to watch out for: Watch out for dents in rolling elements and raceways that can cause vibration.
Filter lubricants and clean work areas, tools, fixtures and hands to reduce the risk of contamination.
2. Misalignment – Misalignment can cause excessive vibration and loads.
The most common causes of misalignment include: bent shaft, dirt or burrs on the shaft or housing shoulder, shaft threads not at right angles to the shaft seat, and locknut faces not at right angles to the threaded shaft.
To prevent misalignment, there are a few best practices you can keep in mind. Make sure to check the shaft and housing regularly, use precision-grade locknuts, and shim the housing as needed.
3. Overloading – Applying excessive loads to bearings is another common cause of failure.
This may seem like normal fatigue. You may see undulating rolling element wear paths, signs of overheating and extensive areas of fatigue. Reduce load or consider redesign with larger capacity bearings. When bearings fail, it can negatively impact your facility, reputation and bottom line. Regular preventive measures can keep your bearings performing at their best for as long as possible, saving your business time and money.
There are a few precautions you can take to extend the life of your bearings and prevent undue wear of your bearings.
Thrust ball bearings support axial loads and reduce friction in a wide range of applications, including automotive, heavy machinery, and . Various types of thrust bearings are available depending on your specific needs. At AUB we are a leading manufacturer of precision bearings, including thrust bearings. Our thrust ball bearings are available with or without raceways and are available in various sizes and load ratings to meet the needs of different applications. To learn about our thrust series bearings, contact us today or request a quote to get started.