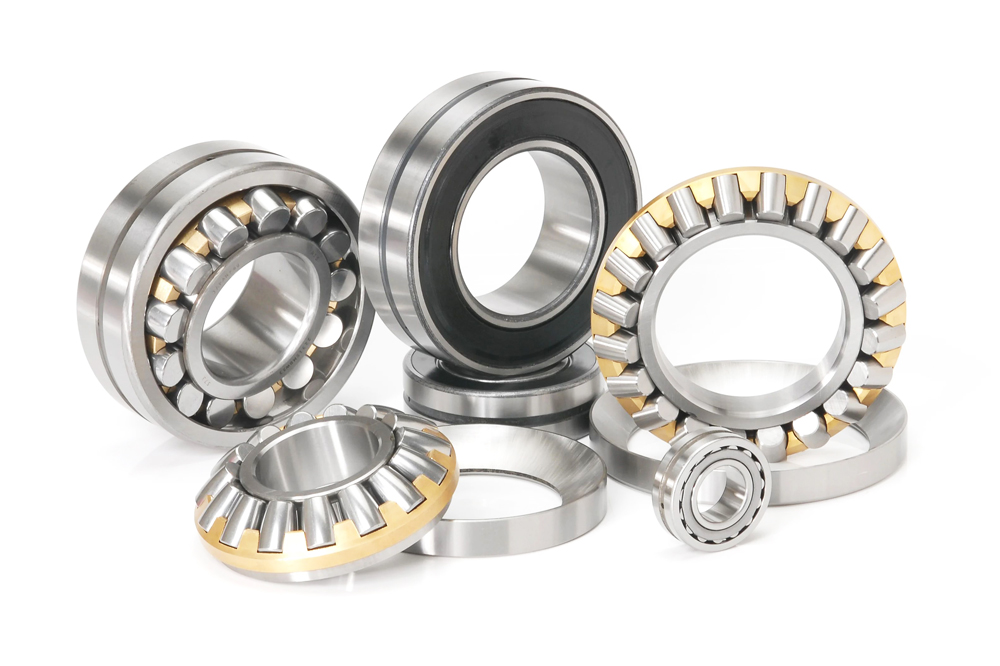
Bearing Manufacturer & Supplier
Specialize in ball bearings, roller bearings, thrust bearings, thin section bearings etc.
Everything You Should Know About Bearing Materials
Bearings are vital to manufacturing and are used in many different types of equipment and machinery. From basic industrial equipment to complex machinery, bearings reduce friction and enable them to handle different types of loads. Therefore, the use of quality and reliable materials is crucial to the bearing manufacturing process.
Different materials are used to produce various types of high-quality bearings and their many components. These materials are subjected to a specific process to obtain the desired properties that increase the life and performance of the bearing. Teams at AUB can discuss the different materials used in bearing manufacturing and how each affects the bearing’s use, integrity and function.
The performance of any bearing depends on the properties of the chosen alloy and its heat treatment. Selecting a material with the correct hardness, corrosion resistance and fatigue life ensures that the bearing will perform reliably within the operating and environmental parameters of the application. AUB uses different materials to produce various bearing components. These materials are processed to obtain ideal characteristics to maximize bearing performance and service life. The materials described here are the most commonly used. The bearing material is heat treated in-house for optimum hardness and dimensional stability.
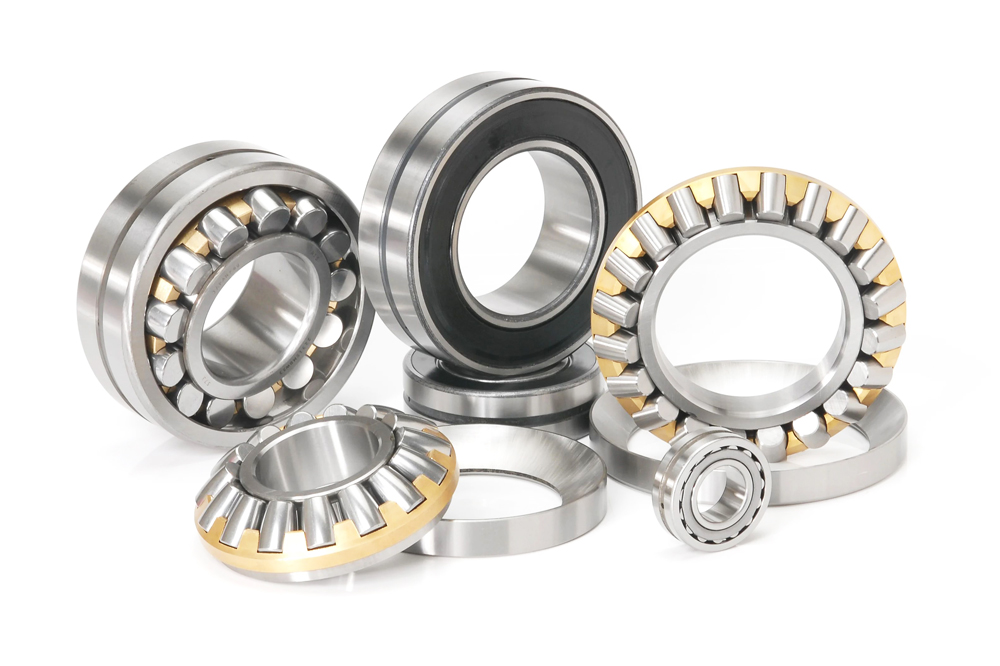
Table of Contents
ToggleChrome Steel Bearings – 52100
The most common material used for the production of load-carrying components in precision ball bearings, roller bearings and tapered roller bearings is 52100 chrome steel. These components refer to bearing inner and outer rings, balls and rollers. The chemical composition of this steel is high in carbon and contains about 1.5% chromium. Using controlled machining and heat treatment methods, the finished bearing components have high strength to resist cracking and hard surfaces to resist subsurface rolling contact fatigue. Typical surface hardnesses for bearing components made from this material range from 60-64 on the Rockwell C scale (Rc).
It has an acceptable cost, high hardness level and quieter running noise. Therefore, the benefits of using chrome steel bearings are high hardness, high load capacity, low decibel and wide accessibility. However, it needs to stay lubricated and is not resistant to corrosion or chemicals. Users are advised to protect chrome steel bearings with an oil or anti-rust coating to prevent corrosion.
Ultra clean 52100 chrome steel
The raw steel used to produce high-precision bearings is treated with an additional melting step, resulting in a steel with a very uniform structure of fine-grained material – ultra-clean 52100 chrome steel. The bearing contact surfaces can be super-finished very smooth, so the bearings run very quietly.
The most common heat treatment method for chrome steels is to quench the steel in a controlled atmosphere furnace. Bearings made of chrome steel can operate at continuous temperatures up to 120°C. Where higher temperatures are encountered, the bearing assembly can be thermally stabilized. By varying the heat treatment process, it is possible to produce bearings capable of operating at 220°C or higher. For these applications, bearing components must be tempered at higher temperatures corresponding to the operating temperatures. This increased tempering has an adverse effect on the hardness of the material and the load carrying capacity of the bearing is reduced.
As can be seen from the table below, the standard chemical composition of chrome steels varies from country to country.
Another common material used to make bearings is stainless steel. Stainless steel is a popular material choice for bearings because of its high chromium and carbon content, which is resistant to surface corrosion than chrome steel. There are than 60 grades of stainless steel, each of which varies according to its composition and physical properties. In general, the composition of stainless steel includes varying amounts of chromium, carbon, phosphorus, nickel, manganese, and molybdenum. In addition, grades help describe the properties of stainless steel alloys, including corrosion and temperature resistance, magnetic response, toughness, ductility, weldability, and work hardening.
In addition to containing at least 18% chromium, stainless steel also contains nickel. The chromium in the stainless steel reacts chemically when exposed to oxygen, forming a layer of chromium oxide on the surface of the bearing components. This passivating chemical film provides additional protection for the bearing. However, stainless steel bearings are less hard due to their carbon content. As a result, they have a 20% lower load carrying capacity than 52100 chrome steel bearings.
There are two common types of stainless steel bearings: martensitic and austenitic. Martensitic stainless steel bearings (SV30) often undergo deterioration during processing of the original steel, resulting in reduced carbon content and increased nitrogen content in the material. The result is a steel with high strength, hardness and enhanced corrosion resistance. Austenitic stainless steel bearings (AISI316), on the other hand, are non-magnetic and highly corrosion resistant due to their low carbon content. However, they can only be used for low load and low speed applications.
The carbon content in 400 series stainless steel is high enough that it can be hardened to Rc58 using standard heat treatment methods. Bearings made of this material have a 20% lower load carrying capacity than 52100 chrome steel bearings due to the lower hardness. The level of carbon content means that the component is magnetic. Corrosion resistance is “Good” when 440C material is exposed to fresh water and mild chemicals. This material is widely popular among American bearing manufacturers.
Bearings made from conventional 440C stainless steel will be slightly noisy because carbides, which usually concentrate at grain boundaries, are exposed during raceway finishing. Bearings with larger bores are not affected by this condition. Bearings made of 400 series stainless steel can operate at higher temperatures than chrome steel, up to 250°C continuously. Bearings made of this material are usually expensive than chrome steel bearings.
AISI 440 Stainless Steel – Excellent toughness and hardness with good corrosion resistance. This material is widely used in bearing applications where precise tolerances and surface finishes are required. Ordinary heat treatment may be performed in accordance with MIL-H-6875. Stainless steel bearings are available in a variety of stainless steel material grades and compositions. Benefits of stainless steel bearings include: Withstands harsh corrosive conditions resulting in longer life, reduced maintenance costs and equipment downtime. Seawater exposure is one of the harshest applications in the bearing world. Special grades of stainless steel are available for seawater applications.
Martensitic Stainless Steel Bearings – ACD34 / KS440 / X65Cr13
Many bearing manufacturers use stainless steel with slightly lower carbon and chromium content than AISI 440C, known by various names such as ACD34, KS440 and X65Cr13, for their rings and balls. When heat treated, this material has smaller carbides so the bearing will have excellent low noise characteristics while providing the same corrosion resistance as 440C. Some manufacturers publish the same load ratings as chrome steel for bearings produced from this material. This is due to the use of a tightly controlled heat treatment with a hardness of up to Rc 60. Although this is one of the most widely used stainless steels for ball bearings, this material does not have an AISI designation.
Martensitic Stainless Steel Bearings – SV30
Martensitic stainless steels can be modified during raw steel processing by reducing the carbon content and introducing nitrogen as an alloying element. Nitrogen increases the saturation of chromium, which turns into chromium nitride instead of chromium carbide. The result is a high-strength, high-hardness steel with an excellent microstructure that can increase fatigue life by up to 100% (double) in some applications. This material also has enhanced corrosion resistance, even 5 times better than 440C and ACD34. Bearings made of this material can be 20 – 40% expensive, but this is usually offset by the benefits of superior performance.
Austenitic stainless steel
300 series austenitic stainless steels are used for non-load bearing parts. Bearing components made of 300 series stainless steel material are resistant to corrosion and are non-magnetic due to their low carbon content. However, the trade-off is that this material cannot be hardened, so the bearings can only operate at low loads and speeds. The chemical reaction of the bearing surface with oxygen is called the passivation process; the passivation film formed on the surface protects the bearing from corrosion. Corrosion resistance is best when the bearing is not completely submerged in the liquid, such as in underwater applications. Bearings made of this material are usually special order items that require a minimum quantity; in addition, they are expensive.
Typically 300 series stainless steel bearings have a grade 304 housing and a grade 302 bearing retainer. Grade 304 is very resistant to fracture (high ductility) and has very high corrosion resistance. 302 has a slightly higher carbon content – increasing hardness – making it suitable for components in the bearing itself. A complete bearing made of 300 series stainless steel has approximately half the load carrying capacity of a bearing made of 52100 bearing steel.
AUB manufactures bearings using 316 Stainless Steel, which offers superior corrosion resistance compared to conventional steel and 440 Stainless Steel bearings. 316 stainless steel is resistant to atmospheric and general corrosive conditions than any other standard stainless steel. 316 stainless steel is widely used in food and medical industries. Bearings made of this steel can run in liquids or dry at low speeds. 316 stainless steel is a molybdenum-containing stainless steel. Molybdenum gives 316 better overall corrosion resistance than 304 grade, especially higher resistance to pitting and crevice corrosion in chloride environments.
Salient features:
Molybdenum content increases resistance to marine environments.
High creep strength and good heat resistance at high temperature.
Biocompatible.
Manufacturing characteristics are similar to Types 302 and 304.
Applications: Food and pharmaceutical processing equipment, marine environments, surgical medical equipment, and industrial equipment handling aggressive chemicals used in the production of inks, rayon, photographic chemicals, paper, textiles, bleach, and rubber.
Corrosion resistance: Corrosion resistance is better than 440c, 302, 304 stainless steel. Resistant to sodium and calcium salt solutions, hypochlorite solutions, phosphoric acid, sulfite solutions and sulfurous acid commonly used in the pulp industry.
316 stainless steel material composition
Other 300 Series Stainless Steel Bearings
Bearing shields, sealing washers and ball cages are sometimes manufactured in AISI303 or AISI304 stainless steel as they have moderate corrosion resistance and are suitable for forming into various shapes.
Carbon Alloy Steel Bearings
Carbon steel materials are used to produce various components of bearings, and there are two basic types, medium carbon alloy steel and low carbon alloy steel.
Medium Carbon Alloy Steel Bearings
Bearings made of medium carbon or low carbon alloy steel materials are often referred to as “semi-precision” or “commercial grade” bearings. Typical materials are AISI8620 or AISI4320. The inner and outer rings are case hardened in a heat treatment process called case hardening or carburizing. Bearings made of these materials cannot withstand high loads or high speeds and are not corrosion resistant. Bearings made from these materials are generally low cost.
Low Carbon Alloy Steel Bearings
Mild steel is used to produce bearing cages, metal shields and metal washers around which rubber is molded for use as seals. Commonly used materials are AISI C1008 and C1010. Oil/grease coating (cage) or plating (shield) is required to protect the material from corrosion. For information on retainers and closures, see the respective technical bulletins.
Heat treatment of bearing steel
When bearing steel is in its soft (unhardened) state, metallurgists refer to its structure as the pearlitic state. In order to harden steel, it must be heated to very high temperatures and then cooled very rapidly. When heated to 1,750°F in a heat-treating furnace, the structure changes from pearlite to what is known as austenite. After quenching (rapid cooling), the structure changes from austenite to martensite. Once transformed into martensite, the steel becomes very hard. However, it is not considered “thermally stable” at this time. This is because not all of the austenite is transformed into martensite during the quenching process. This phenomenon is called “retained austenite”.
If the steel is not thermally stable, the retained austenite will transform to martensite over an extended period of time (possibly years). This transformation is accompanied by an increase in volume and is called metallurgical growth (not to be confused with thermal growth). Metallurgical growth can cause changes in the size and shape of any steel component, such as a bearing, even at room temperature.
While not a problem in low precision commodity type bearings, this lack of dimensional stability can cause problems in high precision (ABEC 5P, 7P, 9P) miniature bearings. To eliminate this unwanted metallurgical growth, the steel must be thermally stabilized. This is accomplished by repeated cooling and tempering at -120 F to transform most of the retained austenite to martensite.