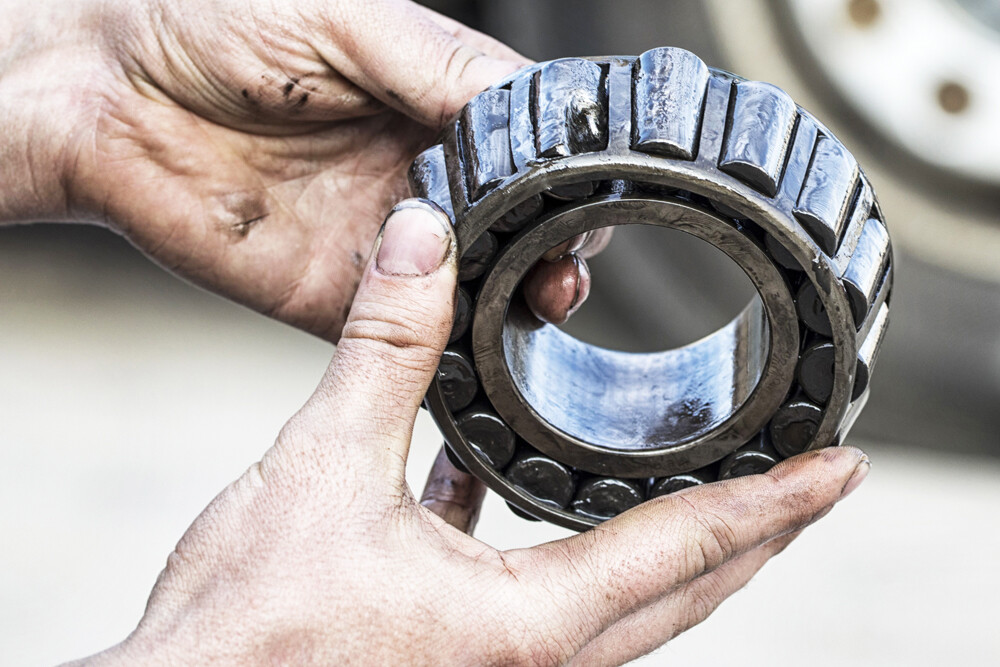
Bearing Manufacturer & Supplier
Specialize in ball bearings, roller bearings, thrust bearings, thin section bearings etc.
Everything You Should Know About Bearing Failure Causes and Preventive Measures
Bearing failure occurs when a bearing fails to meet its expected life or performance levels, resulting in failure of the machine shaft or even damage to parts adjacent to the bearing. The consequences of bearing failure can have far-reaching consequences for your facility. Potential scenarios include, but are not limited to, increased downtime, high maintenance costs, delayed deliveries, lost revenue and, in some extreme cases, potentially life-threatening conditions for workers. When bearings fail, it can negatively impact your facility, reputation and bottom line. That said, there are some precautions you can take to extend the life of your bearings and prevent improper bearing wear.
We know how frustrating it can be for a bearing failure in your plant to cause costly downtime and often force you out of the normal supply chain. At AUB, we are committed to providing high quality over 8000 types of bearings, including deep groove ball bearings, thin section bearings, angular contact bearings, thrust bearings, tapered roller bearings, cylindrical roller bearings, spherical roller bearings, etc. , helping you better serve your customers with reduced turnaround times.

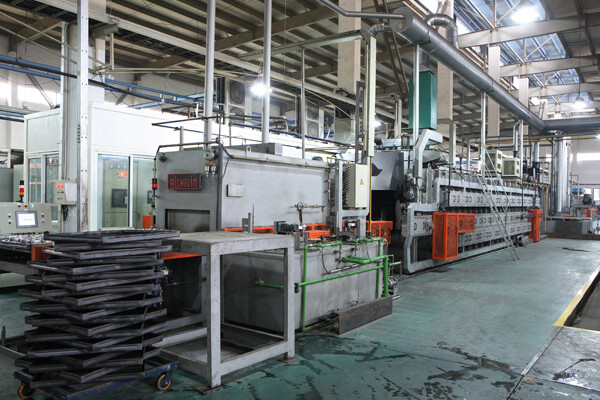
Table of Contents
ToggleWhat is a bearing failure and its impact on a facility?
Simply put, anytime a bearing fails to live up to its expected life or performance level, it can be called a bearing failure. Bearing failures are complex than you might think, and even with careful planning and proper maintenance, they can still fail unexpectedly or prematurely in their application. According to incomplete statistics, less than 30% of bearings will reach their determined fatigue limit and “wear” in their application. Based on years of bearing manufacturing experience, AUB summarizes several common causes of bearing failure:
Insufficient or improper lubrication
Pollution
Improper handling and installation
Overload
Other reasons
What should I do if the bearing fails?
Bearings are critical to the proper functioning of your machine, so when you hear a horrible noise in operation, you need to act quickly. This is likely to be a hint of bearing failure. Bearing failures require immediate attention, as they can cause all kinds of frustrating problems in your facility, such as:
Unplanned downtime
Increased downtime
Loss of productivity
Reduced operating efficiency
Missed delivery times
Increased operating costs
According to incomplete statistics, when a $50 bearing stops running in a multi-million dollar machine, the loss can be as high as $25,000 to $50,000 per hour. Next, AUB goes on to discuss the four stages of bearing failure and its common manifestations across the spectrum.
What You Need to Know About Bearing Failure Stages
As we discussed earlier, bearings don’t keep turning forever. If proper precautions are not taken, bearings can be damaged and have a shortened service life. So, how do we know if a bearing is about to fail? First, we need to understand that there are four distinct stages of bearing failure.
Stage 1
In the first stage, we will see small dimples starting to appear in the bearing races, and the ultrasonic frequency of the rolling element in the spectrum is not in the normal range. But it is likely that at this stage, the bearing is operating normally, for example when we test the frequency spectrum of the bearing at around 20,000-60,000 Hz, although this is not a reason to replace the bearing, it may indicate a lack of lubrication between the raceways and rolling elements.
Stage 2
Once you reach the second stage of failure, you will usually find that the bearing defect starts to ring at its natural frequency, ranging from 500 to 2,000 Hz. Often these frequencies are actually resonances of the bearing components (such as races or rolling elements) or the bearing support structure. It is worth noting that maintenance facilities should be included in the schedule at this stage.
Stage 3
During this stage, bearing defect frequency levels become pronounced and harmonics appear on the frequency spectrum. Determining the rate of degradation is key if you are troubleshooting a problem where you can clearly see defects in the raceway. Additionally, bearings (in both critical and non-critical machinery) that have reached this stage of failure should be promptly replaced.
Stage 4
Bearings reach this stage at the end of their useful life and you will notice an increase in machine noise at all levels, which in turn produces a random broadband spectrum. “The high-frequency noise floor and the amplitude of the HFE may actually decrease, but this is a sign that the bearing is about to fail. In short, the goal is to prevent the bearing from reaching this stage, but if it does, it must be replaced immediately. Using this The four stages and identifying which stage a bearing is in is critical as it will not only help you create an accurate predictive maintenance schedule, but it will also help you keep your machines running efficiently and prevent costly unplanned downtime.
Common causes of bearing failure
When a bearing fails, it means that the machine can fail and therefore the machine itself can be damaged and malfunction. Whether or not your facility has experienced bearing failures recently, bearings wear out every minute of operation and that’s normal. You can probably summarize a number of causes for bearing failure, some common than others. According to incomplete statistics, than 70% of bearing failures are caused by improper installation, poor lubrication or contamination. Here is a chart of bearing failures summarized by AUB to better show the statistics behind the common causes of bearing failures. Let’s take a closer look at the 13 common causes of bearing failure as they relate to your manufacturing process and ultimately your bottom line.
1. Lubrication failure
According to a recent study, up to 80% of bearing failures are caused by lubrication failure. This includes insufficient lubrication, use of the wrong lubricant, or excessive temperatures that degrade the lubricant. This should be one of the first reasons to consider when inspecting a failed bearing. To ensure proper lubrication, there must be sufficient viscosity at the operating temperature. When troubleshooting, look for highly polished or discolored bearing raceways to determine if the running surfaces lack sufficient viscosity at operating temperatures.
Overlubrication is just as harmful as underlubrication. “Insufficient lubrication causes metal-to-metal contact, and overlubrication causes heat buildup and friction as the rolling elements constantly try to push excess grease away.
2. Cage damage
There are many reasons for cage damage. Some of the common problems include vibration, overload, excessive speed, wear or clogging.
3. Pollution and Corrosion
Contaminants such as dirt, sand and water can cause bearing damage during bearing operation, and of course, chemicals and corrosive products can have a negative impact on bearings. These pollutants will reduce the life of the lubricating grease, destroy the oil film, cause corrosion of the bearing surface and generate abrasive particles in the raceway. Therefore, it is important to keep the work area, tools, and fixtures clean, as this can prevent bearing failures and contamination.
4. Arc
Also known as “arc corrosion,” this failure occurs when an electrical current passes through the bearing and breaks the contact surfaces between the races and rolling elements, creating high temperatures at localized points. This creates dimples in the raceways and rolling elements, which can damage the bearing.
5. Improper installation
Mounting the correct bearing on a dimensionally accurate shaft is critical. If not, it can cause two problems:
1. If the shaft is oversized or swollen, it will cause a tight fit, reducing the internal clearance of the bearing.
2. If the shaft is undersized or the fit is too loose, the bearing will creep on the shaft and wear and generate heat, eventually causing vibration and runout problems.
6. Fatigue
Fatigue failure refers to the breakdown of the surface of the bearing during operation, causing tiny, detached particles to fall off, causing bearing failure. Bearing fatigue is progressive, and once it occurs, it will continue to spread as the bearing operates. This generally occurs at the end of the bearing’s expected life, but bearing fatigue due to excessive loads is not excluded.
7. Brinell indentation
When the load exceeds the elastic limit of the bearing ring material, permanent indentations are created in the raceways, which leads to increased vibration. There are two types of Brinell indentation:
True Brinell indentation: caused by loads exceeding the elastic limit of the bearing material.
False Brinell indentation: Caused by vibration or wobbling between rolling elements and raceways.
8. Dislocation
Misalignment can cause excessive vibration and loads on the bearing, and not all bearings are self-aligning. AUB concludes that the most common causes of misalignment include: shaft bending, dirt or burrs on the shaft or housing shoulders, shaft threads not at right angles to the shaft seat, and locknut faces not at right angles to the shaft seat on the threaded shaft. To prevent misalignment, AUB reminds you of some best practices: Make sure the shaft and housing are inspected regularly, use precision-grade locknuts, and shim the housing as needed.
9. Path mode
To better understand the operating conditions of a bearing, it is best to examine the wear path pattern of a disassembled bearing that has already been put into service. Through failure analysis testing and understanding normal/abnormal wear paths, it is possible to properly assess whether a bearing is operating under ideal conditions.
10. Seal selection and maintenance
Fully sealed bearings prevent contamination and ensure lubrication is not compromised. AUB provides some guidelines for selecting and maintaining seals:
Use seals capable of withstanding the selected environmental/operating conditions of the facility.
If possible, install an external shield to prevent debris from accumulating on and around the seal.
Always schedule routine inspections of radial lip seals for flexibility, hardening, cracking, and shaft contact.
Check for leaks and replace damaged seals promptly.
Avoid removing excess grease from lip seals. This can cause them to lose their potency, and in some severe cases, they may fall out of their casings.
Proceed with caution if you use water, steam or compressed air spray when cleaning. It is easy to accidentally damage the seal and force contaminants into the otherwise clean interior of the bearing.
If you are taking apart large machinery, avoid lifting with chains, wire ropes, or dirty slings that can scratch sealing surfaces. If the seal contact faces are worn, be sure to resurface and grind them to their original finish and diameter specifications.
11. Overload
Applying excessive loads to bearings is a common cause of failure. You can resolve overloading by reducing the load on the bearing or by considering a higher capacity bearing.
12. Improper handling and storage
In short, improper storage of bearings can lead to problems later on as they are exposed to external elements such as moisture, dust and changing temperatures. Handling becomes an issue when the box is opened or the packing material tears prematurely, as this exposes the bearings to dirt and corrosive elements. AUB says to be sure to watch out for humidity and temperature, which can cause rust or exposed bearings in storage areas.
13. Insufficient internal clearance
Last but not least, such failures affect the friction, load zone size and fatigue life of the bearing. If the bearing clearance is insufficient, excessive heat will build up. As we have already discussed, high temperatures are not good for bearings and can cause lubrication and internal friction among other problems already listed. We have summarized the most common types of bearing failures, so how to prevent bearing failures? Read on to learn how to implement top preventative measures in your plant!
Preventive measures for bearing failure
Bearings have a reasonably long life under normal operating conditions, but since they do have a fixed life, it is eventually inevitable that bearings will fail. In fact, according to incomplete statistics, less than 1% (specifically 0.35%) of rolling bearings did not reach the expected life. The key to preventing facility downtime and lost productivity is preventing premature bearing failure, which results from bearing damage. Doing this will not only help you prevent premature failure, but it will also help you keep your manufacturing process running smoothly.
Most of the bearing failures we discussed above can be traced back to a small set of causes that are not only interrelated but also repairable.
These causes are installation/alignment, lubrication, overloading, environmental influences and incorrect storage.
Why Proper Mounting and Alignment of Bearings Is Important
During the installation of bearings, suitable tools, ovens and induction heaters must be used. Consider avoiding misalignment or shaft deflection, as this is important when mounting bearings with separate components. If the components are not properly aligned, the bearings will eventually wear abnormally. After installation according to the manufacturer’s instructions, the best practice to remember is to thoroughly flush and clean the bearing with lubricant. Also, be sure to apply a final amount of lubricant before using the machine.
Lubricate according to manufacturer's guidelines
Lubrication is used in bearings to completely cover rolling and sliding surfaces with a thin film of oil to prevent metal-to-metal contact. Grease is commonly used because it is easier to handle, while oil lubrication is often used in high temperature or high speed applications. Common lubrication failures are due to:
Using the wrong type of lubricant
Too little grease/oil or too much grease/oil
Mixed grease/oil
Grease/oil contaminated by objects or water
Use appropriate bearing operating stress
Operating stresses on bearings can affect bearing life.
If the load on the bearing is too low, it will cause the rolling elements to slip and be improperly loaded.
If the load is too high, it may cause overload and early fatigue.
Usually, the first sign of such problems are unusual noises and/or increased temperatures. The ideal bearing temperature is below 100 degrees Celsius. It is important to note that the bearing temperature usually increases with start-up and levels off at a temperature slightly lower than start-up (range 10 to 40 degrees Celsius above room temperature). This is why it is critical to ensure that vibrations are isolated in the associated equipment, as if they are not isolated, they can cause abnormal noise and uneven operation.
Consider environmental impact
If not considered, there are many operating environments in which even the best bearings can become damaged and lead to failure.
Dust and dirt can contaminate bearings extremely quickly. Be sure to use proper sealing techniques to prevent this type of contamination.
Aggressive media or water – this is another example where proper sealing is critical.
External Heat – Ambient operating temperature requirements have multiple options in terms of radial internal clearance, high temperature lubricants, intermittent or continuous operation, and other factors that affect bearing life.
Current Passage or Electrolytic Corrosion – If current is allowed to flow through a bearing’s rolling elements, the sparks can create pitting or grooves in the bearing surfaces. You can fix this by using insulating material on or in the bearing or by creating a bypass circuit for the electrical current.
Store Your Bearings Actively
Present-day, a majority of facilities keep the number of spares they have in stores a minimum.
Thanks to preventative maintenance (like the other measures we’ve mentioned above), facilities can detect potential failures earlier.
This means facilities can order and replace the damaged bearings before an entire machine breaks down, making the need for spare bearings to sit on shelves practically obsolete.
When you need to have bearings being stored in your facility and sitting on shelves, be sure to store them actively. This can be accomplished by rotating or spinning them frequently.
Conclusion
Bearings are generally very reliable and have a long service life under normal operating conditions, even under the most severe conditions. When a bearing does fail prematurely, it is usually due to avoidable causes. For this reason, it is crucial to be able to identify root causes to prevent future failures through preventive actions and consequent problems. Accurately diagnosing and troubleshooting bearing failures to address issues early will help prevent repeat failures and other pain points your facility may experience, such as reduced operational efficiency, increased downtime and lost revenue. As a top bearing manufacturer in China, AUB is committed to providing high quality, authentic bearings to meet customer expectations. If you are looking for a trustworthy bearing manufacturer, you can try to establish a cooperative relationship with AUB.