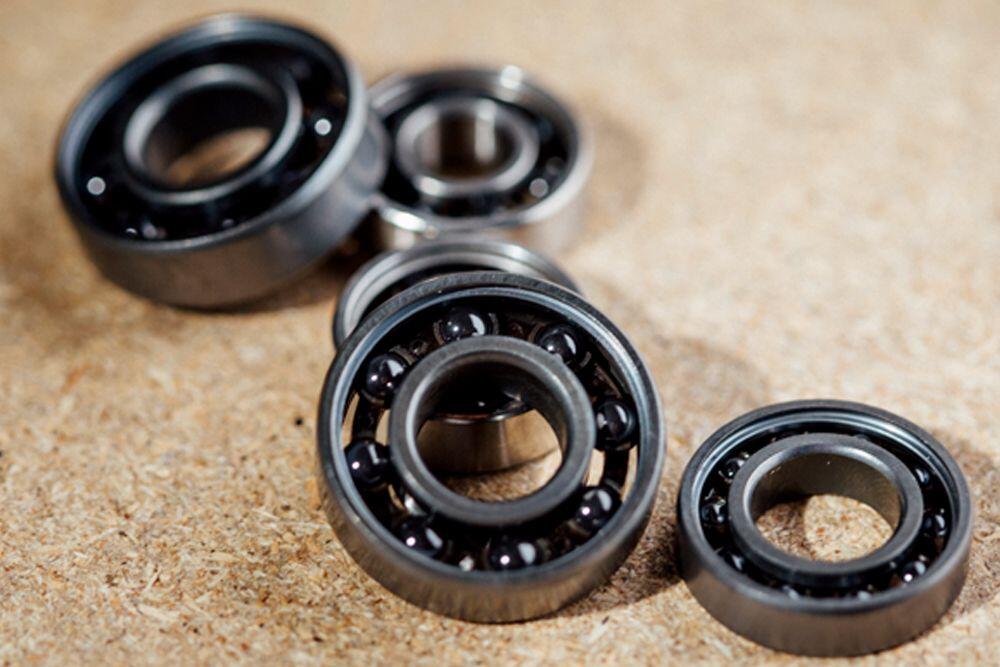
Bearing Manufacturer & Supplier
Specialize in ball bearings, roller bearings, thrust bearings, thin section bearings etc.
Common Ceramic Bearings Characteristics and Applications
When many people think of bearings, they often imagine them as being made of metal. However, with technological advancements and increasing societal demands, bearing materials have diversified. Graphite bearings, ceramic bearings, air bearings, and plastic bearings have emerged and found widespread applications. Each material has its unique advantages and specific uses. Let’s take a detailed look at three types of ceramic bearings, their characteristics, advantages, and suitable applications, to help you better choose the right bearing material for your needs.
Table of Contents
ToggleDo Ceramic Bearings Break?
When first encountering ceramic bearings, many people might wonder, “Do ceramic bearings break? Do they need to be handled as carefully as household ceramics?” To answer this question, let’s look at the materials used to make ceramic bearings—silicon nitride (Si3N4), zirconia (ZrO2), alumina (Al2O3), or silicon carbide (SiC) (the most common being zirconia (ZrO2) and silicon nitride (Si3N4) ceramic bearings). These ceramic materials have low density, moderate elastic modulus, low thermal expansion coefficient, high hardness, high temperature resistance, corrosion resistance, and non-magnetic properties. These advantages make ceramic bearings stand out in various high-precision, high-speed machine tools, automobiles, racing cars, subways, motors, aerospace engines, petrochemical machinery, and metallurgical machinery.
Ceramic bearings are very strong and durable, with high technical requirements in their production, so they do not need to be handled with extreme care. However, due to the low thermal expansion coefficients of ceramics, especially silicon nitride, silicon carbide, and alumina, compared to steel, improper handling might cause full-ceramic bearings to break when paired with steel shafts.
Advantages of Ceramic Bearings
Ceramic bearings are crucial mechanical components used in various industrial fields. What are their advantages?
Corrosion Resistance
Ceramic bearings have high corrosion resistance, making them suitable for working in harsh environments filled with corrosive media.
Stable Physical Properties
Ceramic bearings are less affected by thermal expansion and contraction, allowing them to work in environments with significant temperature changes.
Deformation Resistance
Ceramic bearings, having a high elastic modulus, are less prone to deformation under force. This helps improve working speed and achieve high precision.
Lightweight
Ceramic bearings are much lighter due to the low density of ceramic rolling elements. This reduces the centrifugal force on the outer ring during rotation, significantly extending the bearing’s service life.
Disadvantages of Ceramic Bearings
Despite their numerous advantages, ceramic bearings are not perfect and have their drawbacks:
Manufacturing Difficulty
Ceramic bearings have lower load capacity and are sensitive to thermal shocks compared to metal materials. Therefore, the manufacturing process is complex and involves many considerations, making them difficult to produce.
High Cost
Ceramic bearings are made from non-metal, non-plastic materials, which are excellent non-magnetic insulators. Their material cost is relatively high. Additionally, the manufacturing and grinding costs are complex, resulting in high production costs.
Zirconia ceramic bearings are known for their high toughness, high bending strength, and high wear resistance. Their thermal expansion coefficient is close to that of metals, allowing seamless integration with metals. They also have good insulation properties, maintaining stable performance in high-temperature, high-load environments. Additionally, zirconia ceramics have excellent corrosion resistance against acidic, alkaline, and other corrosive media.
Corrosion Resistance
Suitable for equipment exposed to corrosive media like electroplating equipment, electronic equipment, chemical machinery, shipbuilding, and medical devices.
High Temperature
Withstands high temperatures without thermal expansion issues, suitable for furnaces, plastic production, and steel making.
Self-Lubricating
Low friction coefficient and smooth surface provide good self-lubrication, overcoming lubrication challenges in ultra-high vacuum environments.
Non-Magnetic
Non-magnetic properties prevent dust absorption, reducing early peeling and noise.
Electrical Insulation
High resistance prevents electric arc damage, suitable for insulated power equipment.
High Hardness and Strength
Hardness close to Mohs 9.5, higher than most metals and traditional ceramics, excellent wear resistance, and high load-bearing capacity.
Thermal Stability
Low thermal conductivity and expansion ensure stability at high temperatures.
Biocompatibility
Suitable for medical applications like dental implants, bones, joints, and valves.
Suitable Scenarios: High temperature, high load, corrosive environments in machinery like petrochemical, metallurgy, and power industries.
Silicon nitride ceramic bearings are favored for their high hardness, high wear resistance and low friction coefficient. Silicon nitride ceramic bearings have a variety of excellent properties that make them perform well in various applications. The following are the main characteristics of silicon nitride ceramic bearings:
High Hardness and Strength
Withstands high loads and impacts, resists friction and wear, prolonging equipment life.
Low Starting Torque
Lower density and higher elastic modulus reduce starting inertia and rolling friction.
Long Lifespan
Higher rolling ratio and lower sliding reduce temperature rise, extending bearing life.
High Rigidity
Higher elastic modulus enhances system rigidity, suitable for high-precision transmission mechanisms.
Wear and High-Temperature Resistance
Performs well in high-speed operations and high-temperature environments.
Corrosion Resistance
Effective against most chemicals, preventing corrosion and ensuring precision and lifespan.
Non-Magnetic
Suitable for applications avoiding magnetic interference.
Low Heat Generation and Expansion
Small thermal expansion coefficient minimizes size changes and thermal preload, ideal for environments with temperature variations.
Suitable Scenarios: Aerospace, automotive manufacturing, precision machine tools, and high-speed, high-precision, high-reliability machinery.
Silicon carbide ceramic bearings stand out for their ultra-high temperature resistance and excellent chemical stability. Key characteristics include:
High Hardness and Wear Resistance
Superior to most metals, ensuring durability under high-speed and high-load conditions.
High-Temperature Resistance
Material withstands temperatures up to 1400℃, with normal operating temperatures between 180℃-260℃, and full-ball bearings up to 1000-1200℃, suitable for furnaces, plastic production, and steel making.
Corrosion Resistance
Resists most acids and bases, making them suitable for harsh environments.
Low Friction Coefficient
Reduces wear and energy consumption, improving operational efficiency.
Non-Magnetic:
Non-magnetic properties prevent dust absorption, reducing peeling and noise.
Conductivity
The only conductive ceramic material, suitable for devices requiring conductivity.
However, silicon carbide ceramic bearings have drawbacks like brittleness and low toughness. They are susceptible to extreme loads and impacts, which can cause cracks or breaks, especially under harsh conditions. They also have lower load-bearing capacity compared to metal bearings, making them prone to cracking at bending points.
Suitable Scenarios: Ultra-high temperature, highly corrosive environments in machinery like furnaces, plastic production, steel making, and electroplating equipment.
Conclusion
Zirconia, silicon nitride, and silicon carbide ceramic bearings each have their unique advantages and suitable applications. When choosing bearing materials, one should evaluate the specific application environment and needs. For example, in high temperature, high load, and highly corrosive environments, zirconia or silicon carbide ceramic bearings are suitable; for high-speed, high-precision, and high-reliability machinery, silicon nitride ceramic bearings may be appropriate. By choosing the right material, one can ensure efficient and stable operation of machinery, improving production efficiency and product quality.