
Bearing Manufacturer & Supplier
Specialize in ball bearings, roller bearings, thrust bearings, thin section bearings etc.
Ceramic Bearings Are Prone to Breakage?
Ceramic bearings are essential components in ensuring the efficient and stable operation of mechanical equipment. With advancements in materials science, ceramics such as zirconia, silicon nitride, and aluminum oxide have gained widespread use in bearing manufacturing due to their unique physical and chemical properties. Ceramic bearings play a crucial role in modern industry, owing to their exceptional material characteristics. One commonly discussed issue is whether ceramic bearings are prone to breakage.
Table of Contents
ToggleMaterial Characteristics of Ceramic Bearings
Ceramic bearings are primarily made from high-performance ceramics like zirconia, silicon nitride, and aluminum oxide. These materials exhibit high hardness, excellent wear resistance, low friction coefficients, and good chemical stability. Compared to traditional metal bearings, ceramic bearings offer higher speeds, lower friction and wear, and superior insulation properties.
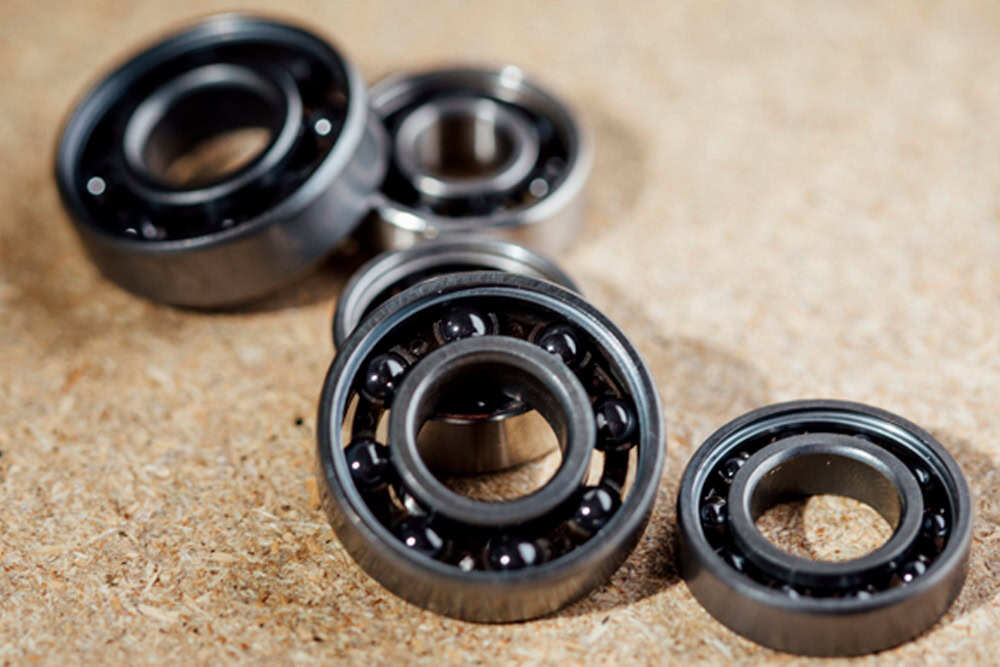
Brittle Nature of Ceramic Bearings
Despite their numerous advantages, the brittleness of ceramics is a significant concern. Due to the strong atomic bonding between ceramic materials, they tend to fracture rather than deform plastically under external forces. Therefore, ceramic bearings are indeed susceptible to fracturing under conditions of excessive impact loads or improper installation.
Overloading: While ceramic bearings have higher compressive strength compared to traditional bearings, their fatigue life is relatively shorter, making them unable to withstand excessive loads.
Improper Installation: During installation, it’s crucial to avoid using inappropriate tools that could damage the bearing surfaces. Attention should also be paid to rotation direction and fitting orientation to ensure proper functionality.
Inadequate Maintenance: Proper maintenance involves keeping bearings clean to prevent contaminants from entering the internals. Timely replacement of lubricants is necessary to maintain proper lubrication conditions.
However, it’s important to note that the risk of fracturing does not imply that ceramic bearings are inherently fragile in practical applications. In fact, with proper structural design, precise manufacturing processes, and correct usage and maintenance, the risk of fracture can be effectively controlled.
Crush Load Test of Ceramic Bearings
Generally, ceramic bearings are not easily broken, regardless of the angle from which they fall. This typically does not result in any damage to the bearing’s appearance. However, full ceramic bearings paired with steel shafts are at risk of cracking due to the difference in thermal expansion coefficients between the materials.
Comparison of Basic Properties Between Ceramic and Steel Materials | |||||||
Item | Unit | Bearing Steel | Stainless Steel | Si3N4 | ZrO2 | SiC | Al2O3 |
Density | g/cm³ | 7.85 | 7.90 | 3.20 – 3.30 | 6.00 | 3.10 | 3.95 |
Thermal Expansion Coefficient | 10^-6/K | 10 | 11.0 | 3.2 | 10.5 | 4.5 | 8.5 |
Elastic Modulus | GPa | 208 | 200 | 300 – 320 | 210 | ≥ 350 | 380 |
Thermal Conductivity | W/m·K | 30-40 | 15 | 35 | 2-3 | 150 | 30 |
Specific Resistance | Ω·mm²/m | 0.1 – 1 | 0.75 | 10^8 – 10^18 | 10^5 – 10^15 | 10^-1 – 10^3 | 10^8 – 10^18 |
Non-lubricated Sliding Wear |
| Large | Large | Small | Small | Small | Small |
Operational Torque |
| Large | Large | Small | Medium | Small | Medium |
Fatigue Life Test Results for Three Types of Bearings | ||||||
Test Bearing Type | Load (N) | Max Contact Stress (GPa) | Speed (r/min) | L10L_{10}L10 Life (h) | L50L_{50}L50 Life (h) | Weibull Slope (β\betaβ) |
All-steel Bearing | 5880 | 3.3 | 8000 | 46.2 | 269.5 | 1.06 |
Hybrid Ceramic Bearing | 5880 | 3.9 | 8000 | 68.2 | 589.2 | 0.95 |
All-ceramic Bearing | 5880 | 3.9 | 8000 | 49.4 | 294.6 | 0.96 |
In simple crush load comparison tests, the minimum crush load for ceramic balls is approximately 1/2 to 1/3 that of steel balls. This is because the contact surface area increases due to plastic deformation of the steel balls, resulting in a higher crush load. Based on the crush load values of ceramic balls, the maximum contact stress at failure can be calculated to be about 6 to 7 times the value specified in the ISO-TC4 standard. This not only proves that ceramic balls are safe for use in rolling bearings but also indicates that they can withstand greater static loads than steel bearings.
Mitigating Fracture Risk in Ceramic Bearings
Selecting Appropriate Bearing Types and Specifications: Choose ceramic bearings that match the specific application requirements, ensuring they can handle the operational loads and speeds.
Proper Installation and Usage: Adhere to manufacturer guidelines during installation and operation to prevent excessive impact loads and other installation-related issues.
Regular Inspection and Maintenance: Regularly inspect and maintain ceramic bearings to promptly identify and address potential issues, ensuring they remain in good working condition.
While ceramic bearings do exhibit some brittleness, effective control measures through proper selection, usage, and maintenance have made them highly effective in applications such as high-speed motors, precision instruments, and aerospace sectors. Looking forward, continual advancements in materials and manufacturing technologies are expected to further enhance the performance and reliability of ceramic bearings, expanding their applications in diverse industrial fields.