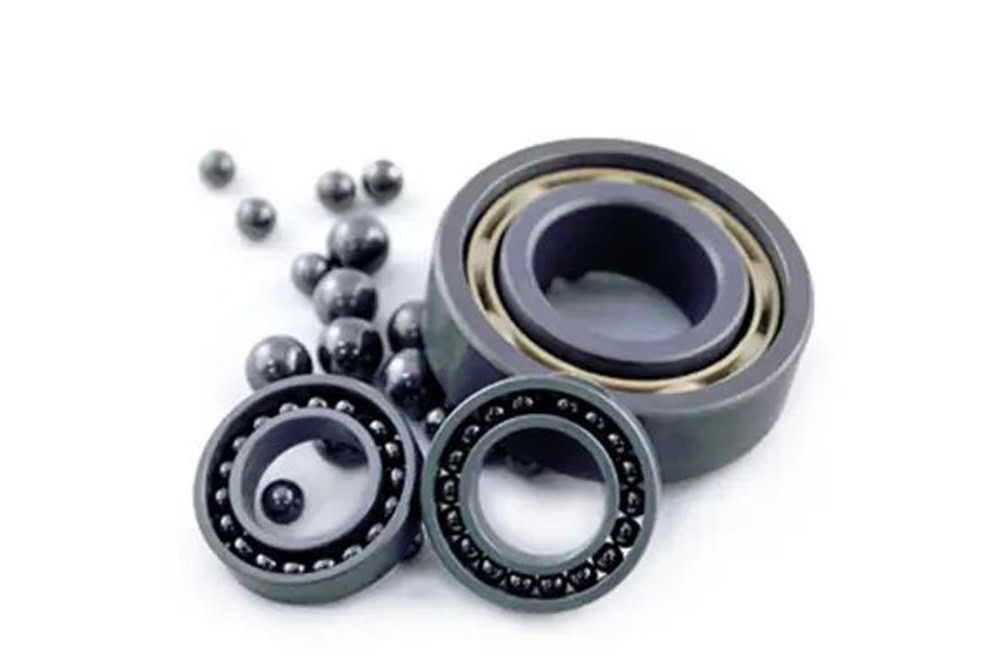
Bearing Manufacturer & Supplier
Specialize in ball bearings, roller bearings, thrust bearings, thin section bearings etc.
Are Full Ceramic Bearings Worth Investing in?
Full ceramic bearings are wear-resistant, corrosion-resistant, and have high speed. They are also non-magnetic, have low friction coefficients, are anti-electric, corrosion-resistant, lighter, smoother, and harder. They have been widely used in extremely harsh environments or special working conditions, such as aerospace, petrochemicals, and electronic equipment. Full ceramic bearings are a type of bearing whose rings and rolling elements are made of ceramic materials such as zirconium oxide (ZrO2), silicon nitride (Si3N4), and silicon carbide (Sic); there are many types of retainers, and common manufacturing materials include polytetrafluoroethylene, nylon 66, polyetherimide, zirconium oxide, silicon nitride, stainless steel, or special aviation aluminum. This blog will introduce the advantages, types, and comparisons with steel bearings of Full ceramic bearings in detail, as well as a comprehensive exploration of whether Full ceramic bearings are worth investing in.
Table of Contents
ToggleAdvantages of Full Ceramic Bearings
Full ceramic bearings have many advantages over traditional metal bearings, including high-speed performance, low friction, corrosion resistance and durability. They are widely used in harsh environments ranging from high-speed machinery to chemical processing equipment and high-temperature furnaces.
①. Prevent current corrosion
When the motor is running, the potential difference between the two ends of the shaft or between the shafts is called shaft voltage, and the resulting shaft current may cause damage to the raceway and rolling elements and aging of the lubricant. Full ceramic bearings can prevent the passage of current and have a durable insulation ability than ceramic-coated bearings. In generator applications of wind turbines, full ceramic bearings are often specified.
②. High speed
The density of silicon nitride rolling elements is 60% lower than that of bearing steel rolling elements of the same size. Lighter weight and inertia result in higher speed performance, which makes the bearing’s ability to start and stop quickly outstanding. In addition, full ceramic bearings have oil-free self-lubricating properties and a low friction coefficient, so ceramic ball bearings have a very high speed.
③. Long life
The heat generated by friction in full ceramic bearings is low, especially at high speeds, which helps to extend the service life of the bearings and extend the relubrication interval, which can greatly reduce the downtime losses and maintenance costs caused by bearing maintenance.
④. High hardness and high toughness
Ceramic rolling elements have higher hardness and excellent toughness. The combination of these two characteristics can obtain better surface roughness, and can prevent damage from external hard particles and impacts, and have strong wear resistance.
⑤. Higher stiffness
The stiffness of the bearing refers to the degree of elastic deformation of the bearing under load. Stiffness affects various aspects of bearing vibration, noise, life and rotation accuracy, and is an important performance parameter in bearing analysis. The hardness of full ceramic bearings is 1 times higher than that of bearing steel, and the elastic modulus is about 1/3 higher.
⑥. High temperature resistance
Ceramic rolling elements have a lower thermal expansion coefficient. A small thermal expansion coefficient helps to reduce sensitivity to temperature changes, thereby preventing jamming. In high temperature environments, full ceramic bearings can work reliably at 800-1000°C without expansion caused by temperature differences.
Full Ceramic Bearing Types
ZrO2 full ceramic bearings have excellent resistance to high and low temperatures, high pressure, corrosion, magnetic insulation, and self-lubrication. They can operate in special environments. Zirconia (ZrO2) ceramic bearings without a retainer can be used in environments up to 400℃.
Si3N4 full ceramic bearings possess all the properties of ZrO2 full ceramic bearings, plus additional benefits such as being lightweight, highly wear-resistant, and having high hardness. Compared to ZrO2 full ceramic bearings, Si3N4 full ceramic bearings are suitable for high-speed and high-load applications and can withstand higher temperatures. They offer good high-temperature strength, mechanical oxidation resistance, high-temperature load capacity, and resistance to corrosive gases. Si3N4 ceramic bearings without a retainer can operate in environments up to 1100℃.
Silicon carbide (SiC) full ceramic bearings offer higher chemical corrosion resistance, better strength, higher hardness, and greater wear resistance compared to other ceramic materials. They also have low friction properties and are suitable for the highest temperatures. SiC ceramic bearings without a retainer can be used in environments up to 1400℃.
Al2O3 Ceramic Bearings
Alumina (Al2O3) ceramic bearings use alumina ceramic with a 99% alumina content. The rolling elements are also made from alumina ceramic. Al2O3 ceramic bearings without a retainer can operate in environments up to 1400℃.
Full Complement Ball Full Ceramic Bearings
Full complement ball full ceramic bearings have a notch on one side, allowing for ceramic balls to be loaded than standard structures due to the absence of a cage. This increases their load capacity and avoids the limitations of cage materials, achieving the corrosion resistance and temperature endurance of ceramic cage full ceramic bearings. These bearings are not suitable for high speeds, and during installation, the notch should be positioned on the side that does not bear axial load.
Challenges of Full Ceramic Bearings
The production process of ceramic bearings involves multiple processes, including raw material preparation, molding, sintering, and finishing, and each process has an important impact on the performance of the final product. The complexity of the production process not only increases the production cost, but also puts higher requirements on the control of the production process.
High cost.
The production cost of ceramic materials is relatively high, which is mainly due to the expensive raw materials of ceramic materials and the complex production process. The preparation process of high-performance ceramic materials such as zirconium oxide (ZrO2), silicon nitride (Si3N4) and silicon carbide (SiC) requires high-temperature sintering and precision machining, which are not only time-consuming and energy-consuming, but also require expensive equipment and technical support. Therefore, the high cost of ceramic bearings has become a major obstacle to their promotion and application.
Difficult to manufacture
Ceramic materials have high hardness and low toughness, which makes them difficult to process. Traditional metal processing technology often does not work in the processing of ceramic materials, which is prone to material damage or processing errors. In addition, the brittleness of ceramic materials makes it easy to crack and fragment during processing, increasing the complexity and risk of processing.
Due to brittle fracture
Although ceramic bearings have excellent high temperature resistance, corrosion resistance and low friction properties, the brittleness and impact resistance of ceramic materials are poor in some extreme environments, which limits their application range. For example, in high impact and high vibration environments, ceramic bearings may fail due to brittle fracture.
Full ceramic bearings have become an indispensable key component in modern industry with their excellent performance and wide application prospects. Although their initial investment is high, their long service life and low maintenance cost make them economical in long-term use. Especially in harsh environments such as high temperature, high pressure, and corrosiveness, the advantages of full ceramic bearings are obvious.
Excellent performance
Taking silicon nitride Full ceramic bearings as an example, silicon nitride ceramics are a structural ceramic with excellent comprehensive performance and many unique properties, which make them widely used in modern technology. Silicon nitride ceramics have extremely high mechanical strength and hardness, comparable to corundum, and are self-lubricating and wear-resistant. At room temperature, its bending strength can even be as high as 980MPa, which is comparable to alloy steel. importantly, its strength will not decrease even at a high temperature of 1200℃. Silicon nitride ceramics have excellent thermal stability, small thermal expansion coefficient, and excellent thermal conductivity, so they have good thermal shock resistance. Even thermal shock from room temperature to 1000℃ will not cause it to crack.
Typical Properties | Al2O3 | ZrO2 | Si3N4 | SiC | Bearing Steel |
---|---|---|---|---|---|
Density (kg/m^3) | 3250 | 3100 | 3900 | 3200 | 7800 |
Elastic Modulus (GPa) | 310 | 210 | 320 | 420 | 210 |
Compressive Strength (MPa) | >3500 | 2000-2500 | 2000-2700 | 2000 | — |
Flexural Strength (MPa) | 700-1000 | 500-900 | 500-900 | 300-600 | 1000 |
Fracture Toughness (MPa·m^1/2) | 3-5 | 8-12 | 6-10 | 3-5 | 16-20 |
Hardness (GPa) | 14-18 | 10-13 | 18-20 | 24-28 | 8 |
Thermal Expansion Coefficient (10^-6/K) | 4-8 | 10-12 | 2-4 | 3-5 | 12 |
Thermal Conductivity (W·m^-1·K^-1) | 20 | 2 | 30 | 100 | 30 |
Specific Heat (J·kg^-1·K^-1) | 800 | 500-700 | 800 | 880 | 450 |
Maximum Operating Temperature (℃) | 1050 | 500-800 | 1250 | 1250 | 400-600 |
Oxidation Resistance | High | Medium | High | Very High | Very High |
Failure Mode | Brittle Fracture | Brittle Fracture | Brittle Fracture | Brittle Fracture | Ductile Fracture |
This table provides a comparative overview of the key properties of industrial ceramics (Al2O3, ZrO2, Si3N4, SiC) and bearing steel, highlighting their differences in density, mechanical strength, thermal properties, and failure modes.
Silicon nitride ceramics have excellent chemical stability and can resist corrosion from almost all inorganic acids (except hydrofluoric acid) and caustic soda solutions with a concentration below 30%. At the same time, they also have good tolerance to corrosion from many organic substances. importantly, they are non-wetting to a variety of non-ferrous metal solutions, especially aluminum liquid, and can withstand strong radiation. Silicon nitride ceramics have low density and low specific gravity, only 2/5 of steel, and have good electrical insulation.
Self-lubricating
Full ceramic bearings can work properly without the use of lubricants, so the application in cryogenic pumps allows researchers to avoid the influence of lubricant viscosity changes on the normal operation of bearings. Cryogenic bearings are mainly used in various types of liquid pumps, such as liquefied natural gas pumps, liquid nitrogen (hydrogen, oxygen) pumps, butane pumps, etc. These devices need to maintain stable performance and long life in low temperature environments, and ceramic bearings have become an indispensable part of these devices due to their excellent performance and adaptability. Ceramic bearings have also been widely used in equipment such as liquid pumps for rockets and missiles and spacecraft. These devices need to operate in extremely harsh environments, and ceramic bearings have excellent corrosion resistance and the ability to adapt to high and low temperature environments, making them an ideal choice for these devices.
Application Case - MRI
Magnetic resonance imaging (MRI) is an imaging technology widely used in medical and scientific research. It is often associated with MRI scanners in hospitals, which use strong magnetic fields to generate two-dimensional and three-dimensional images of the human body or other living objects. In MRI scanners, all equipment used must be non-magnetic to prevent interference with the image. Therefore, traditional steel bearings are not suitable in this scenario because their magnetism may affect the quality of the image. Non-magnetic ceramic bearings are very suitable for use inside MRI scanners. The advantage of ceramic bearings is that they are highly non-magnetic and therefore do not cause any interference with MRI scans. In addition, ceramic bearings also have excellent corrosion resistance and high hardness, which can maintain stable performance in harsh environments.
Application Case - Cleanroom
A cleanroom is an environment that is extremely close to dust-free, providing researchers with pollution-free conditions for preparing and measuring small instruments, equipment or materials. However, the ability to maintain this dust-free environment is often challenged, especially because the lubricant in standard steel bearings is gradually released into the environment. This phenomenon can undermine the cleanliness control of the cleanroom. Full ceramic bearings provide a solution. Because they can operate without lubricants, ceramic bearings produce almost no friction during operation, and the surface can be made very smooth, thus achieving lubricant-free operation. In addition, unlike stainless steel bearings, full ceramic bearings do not generate heat accumulation inside the bearing, so lubrication is not required to help dissipate heat.
The use of lubricant-free ceramic bearings can completely eliminate the outgassing problem caused by steel bearings, thereby maintaining the cleanliness control of the cleanroom. Full ceramic bearings not only run smoothly, but also provide stable and reliable performance in cleanrooms. Therefore, ceramic bearings play an important role in maintaining the cleanliness and control capabilities of cleanrooms.
Conclusion
Full ceramic bearings have advantages such as high temperature resistance, corrosion resistance, and electrical insulation, but they also face the challenges of much higher costs than steel bearings and relatively low load-bearing capacity. For special applications, such as high temperature, high pressure, corrosion, precision, clean and other working environments, Full Ceramic Bearings are worth investing in.