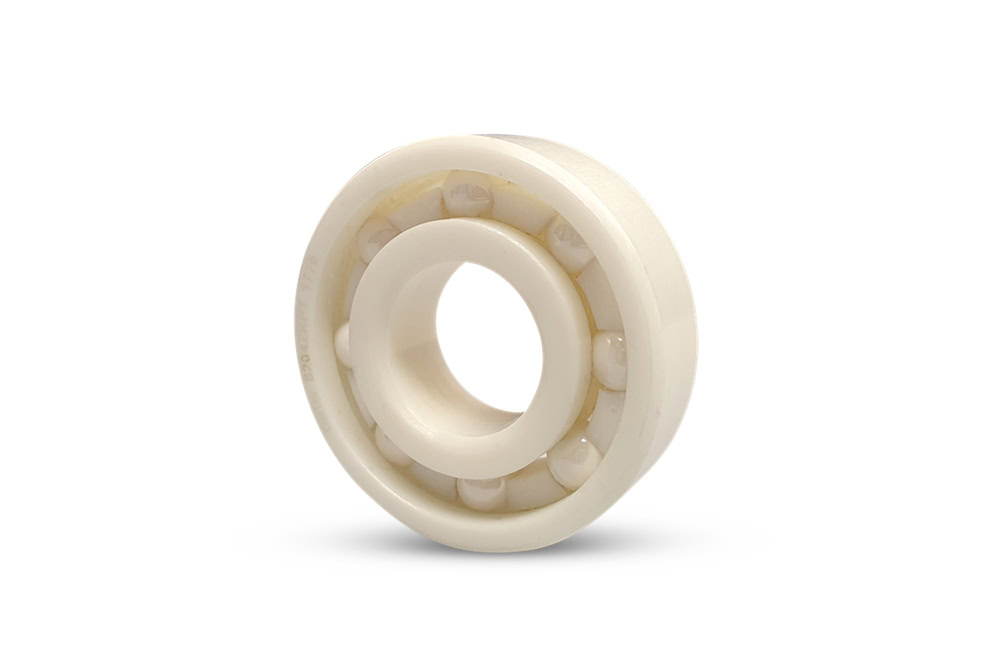
Bearing Manufacturer & Supplier
Specialize in ball bearings, roller bearings, thrust bearings, thin section bearings etc.
A Guide to Alumina Ceramic Bearings
Alumina ceramic bearings have significant advantages in hardness, wear resistance, corrosion resistance and insulation properties, and are widely used in various fields. Through fine manufacturing processes and special material formulas, alumina ceramic shafts can meet various harsh working environment requirements. Alumina ceramic is a ceramic material based on aluminum oxide (Al2O3). It is a widely used ceramic bearing and is indispensable in modern industrial environments.
Table of Contents
ToggleAdvantages of alumina ceramic bearings
Alumina ceramic bearings have become increasingly popular due to their exceptional performance and versatility. Whether in manufacturing, aerospace, electronics or any other industry, the decision to use alumina ceramic bearings can significantly impact the efficiency and quality of your product. Here are ten reasons why choosing alumina ceramics is a smart investment:
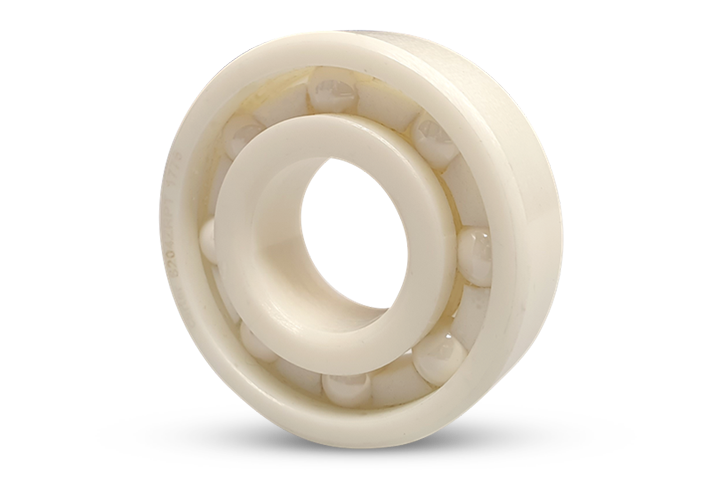
1. Extremely high hardness: Alumina ceramic has extraordinary hardness, making it highly wear-resistant. It has been measured that the Rockwell hardness of alumina ceramic bearings is HRA80-90, which is second only to diamond in hardness and far exceeds the wear resistance of wear-resistant steel and stainless steel. This property ensures extended machinery life and reduced maintenance requirements, resulting in cost savings over time.
2. Excellent wear resistance: its wear resistance is equivalent to 266 times that of manganese steel and 171.5 times that of high chromium cast iron. According to our customer tracking surveys over than ten years, under the same working conditions, the service life of the equipment can be extended by at least ten times.
3. Chemically Inert: Alumina ceramics are chemically inert, which means they are corrosion-resistant and unaffected by many harsh chemicals. This resistance makes them suitable for use in environments with frequent contact with corrosive substances.
4. Electrical insulation: Due to its insulation properties, alumina ceramic bearings are widely used in electrical and electronic equipment. Their excellent dielectric strength and stability ensure reliable performance in demanding electrical applications.
5. Light weight: Its density is 3.8g/cm, which is only half that of steel, which can greatly reduce the equipment load.
5. Low friction coefficient: Alumina ceramics have a low friction coefficient, which can reduce friction and wear in mechanical systems. This property is advantageous in applications such as bearings, seals and sliding components.
7. Biocompatibility: In biomedical applications, alumina ceramics are favored for their biocompatibility and inertness in the human body. They are used in dental implants, joint replacements and a variety of medical devices with minimal risk of adverse reactions.
8. High dielectric strength: Alumina ceramics have high dielectric strength, allowing them to withstand high voltages without electrical breakdown. This property is critical for insulation applications where reliability and safety are critical.
9. Environmental Sustainability: Alumina ceramics are environmentally friendly materials as they are inert and non-toxic. Their durability and longevity help reduce the need for frequent replacement, thereby minimizing waste generation.
10. Wide range of applications: Alumina ceramics are used in various industries, from automotive and aerospace to electronics and medical equipment. Their versatility and superior performance make them the first choice for critical components in a variety of manufacturing processes.
Alumina performance parameters
High-purity alumina ceramics are ceramic materials with an Al2O3 content of than 99.9%. Due to its sintering temperature of up to 1650-1990℃ and a transmission wavelength of 1~6μm, it is generally made into molten glass to replace platinum crucibles; it is used as sodium lamps due to its light transmittance and resistance to alkali metal corrosion; it can be used as integrated circuit substrates and high-frequency insulation materials in the electronics industry. Ordinary alumina ceramics are divided into 99 porcelain, 95 porcelain, 90 porcelain, 85 porcelain and other varieties according to the Al2O3 content. Sometimes those with an Al2O3 content of 80% or 75% are also classified as ordinary alumina ceramics. Among them, 99 alumina ceramic materials are used to make high-temperature crucibles, refractory furnace tubes and special wear-resistant materials, such as ceramic bearings, ceramic seals and water valve plates.
Mechanical properties
Item | Unit | 95% Alumina | 99% Alumina | 99.5% Alumina |
Color | – | White | Yellow | Yellow |
Density | g/cm³ | 3.7 | 3.85 | 3.9 |
Hardness | GPa | 13.7 | 15.2 | 15.7 |
Compressive Strength | MPa | 2000 | 2160 | 2350 |
Flexural Strength | MPa | 280 | 310 | 350 |
Fracture Toughness | MPa·m^1/2 | 3-4 | 3-4 | 4.5 |
Young’s Modulus | GPa | 320 | 360 | 370 |
Poisson’s Ratio | – | 0.23 | 0.23 | 0.23 |
Thermal properties
Item | Unit | 95% Alumina | 99% Alumina | 99.5% Alumina |
Maximum Operating Temperature | °C (without mechanical load) | 1650 | 1650 | 1650 |
Thermal Conductivity @ 20°C | W/(m·K) | 24 | 29 | 32 |
Linear Thermal Expansion Coefficient | 40-400°C = 10^-6/°C | 7-8 | 7-8 | 7-8 |
Specific Heat | J/(kg·K) | 780 | 790 | 780 |
Thermal Shock Resistance | °C (placed in water) | 200 | 200 | 200 |
Electrical properties
Item | Unit | 95% Alumina | 99% Alumina | 99.5% Alumina |
Dielectric Constant | 1 MHz | 9.4 | 9.9 | 9.9 |
Dielectric Strength | V/m | 15 x 10^6 | 15 x 10^6 | 15 x 10^6 |
Dielectric Loss | 1 MHz | 4 x 10^-4 | 2 x 10^-4 | 1 x 10^-4 |
Volume Resistivity @ 20°C | Ω·cm | >10^14 | >10^14 | >10^14 |
Volume Resistivity @ 500°C | Ω·cm | >10^8 | >10^8 | >10^10 |
Conclusion
As a high-quality ceramic product, alumina ceramic bearings have significant advantages in hardness, wear resistance, corrosion resistance and insulation properties, and are widely used in various fields. Through fine manufacturing processes and special material formulas, alumina ceramic shafts can meet various harsh working environment requirements and provide stable and reliable solutions for various industries.