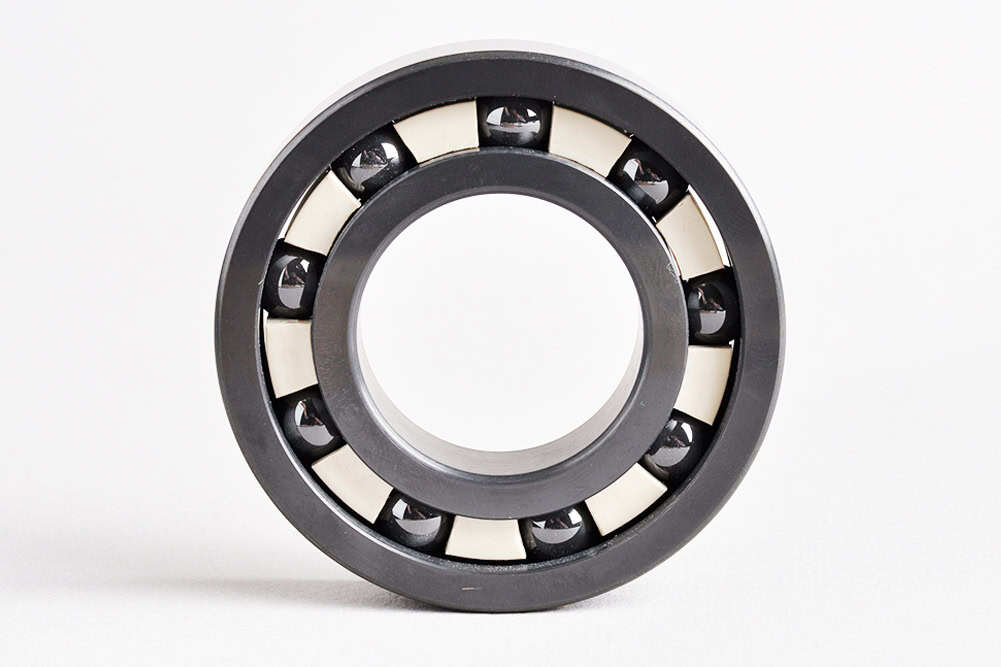
Bearing Manufacturer & Supplier
Specialize in ball bearings, roller bearings, thrust bearings, thin section bearings etc.
Are Ceramic Bearings Worth Investing In?
As a high-performance component in the field of mechanical engineering, ceramic bearings have attracted increasing attention due to their excellent performance under specific conditions and wide application prospects. According to statistics, the full ceramic bearing market will grow at a CAGR of about 11% from 2017 to 2023, mainly due to the growth in demand for laboratory equipment. This article aims to explore the materials, performance and structural characteristics of ceramic bearings, analyze their advantages and disadvantages, discuss their application scenarios, and provide suggestions for selection, installation, matching and disassembly to help potential investors fully understand the value and market prospects of ceramic bearings.
Table of Contents
ToggleMaterial of ceramic bearings
The choice of ceramic bearing materials directly determines its performance and application scenarios. Common ceramic bearing materials mainly include silicon nitride (Si3N4), zirconium oxide (ZrO2), aluminum oxide (Al2O3) and silicon carbide (SiC).
Silicon nitride (Si3N4)
Silicon nitride is a material widely used in high-performance ceramic bearings. It has high hardness, low density, excellent heat resistance and outstanding mechanical strength. Silicon nitride ceramic bearings perform particularly well in high-speed rotation and high-temperature environments. Its low coefficient of friction and high wear resistance make it suitable for aerospace, high-performance racing cars, and industrial equipment that requires high-speed operation. In addition, the oxidation resistance and chemical stability of silicon nitride materials enable it to maintain excellent performance in harsh environments.
Zirconia (ZrO2)
Zirconia is an ideal material for manufacturing ceramic bearings due to its high mechanical strength and toughness, as well as excellent corrosion resistance. Zirconia ceramic bearings can be used for a long time in highly corrosive environments, such as chemical equipment and medical devices. Its high strength and impact resistance enable it to withstand high mechanical stress, while its excellent oxidation resistance and chemical stability also increase the service life of the bearing.
Alumina (Al2O3)
Alumina is a cost-effective ceramic material with good wear resistance and insulation properties. Alumina ceramic bearings are often used in electronic equipment and applications that require insulation. Although its mechanical strength is not as good as silicon nitride and zirconium oxide, its cost is lower and it is suitable for less demanding industrial applications. The insulating properties of alumina make it widely used in electrical and electronic equipment.
Silicon carbide (SiC)
Silicon carbide is known for its extremely high thermal conductivity and high temperature resistance. Silicon carbide ceramic bearings are suitable for extremely high temperature environments and applications requiring high thermal conductivity, such as industrial furnaces, chemical equipment, and high-temperature processing equipment. The high hardness and low density of silicon carbide materials also make it an excellent bearing material that can maintain stable performance in harsh environments.
Advantages of ceramic bearings
Ceramic bearings exhibit many advantages over traditional steel bearings in terms of performance and structure due to their material properties. Understanding these performance and structural characteristics will help in the correct selection and application of ceramic bearings.
High hardness and wear resistance: The hardness of ceramic materials is much higher than traditional metal materials. This makes ceramic bearings extremely wear-resistant and able to maintain stable performance over long periods of operation. The high hardness also makes ceramic bearings less likely to deform during high-speed operation, ensuring the accuracy and stability of the bearings.
Low friction coefficient: The friction coefficient of ceramic materials is very low. The friction coefficient of traditional bearings is between 0. 08-0. 12, while the friction coefficient of ceramic bearings is only 0. 001-0. 005. This enables ceramic bearings to significantly reduce friction losses and improve transmission efficiency during operation. Low friction coefficient can not only reduce energy consumption, but also reduce operating temperature and extend the service life of bearings and related mechanical equipment.
High temperature resistance: Ceramic materials can still maintain excellent mechanical properties in high temperature environments. The strength and hardness of ceramic materials such as silicon nitride and silicon carbide are almost unaffected at high temperatures, making them suitable for high-temperature operating environments such as aerospace, industrial furnaces and high-temperature processing equipment.
Non-magnetic and insulating: Ceramic materials are non-magnetic and have insulating properties. They are suitable for applications that have special requirements for magnetism and conductivity, such as magnetic resonance imaging equipment, electronic equipment, etc. Non-magnetic and insulating properties make ceramic bearings widely used in electronic and electrical equipment.
Lightweight: The density of ceramic materials is low, which can effectively reduce the total weight of the equipment and improve the energy efficiency of the equipment. Lightweighting not only helps reduce energy consumption, but also improves the dynamic response performance of mechanical equipment, making it suitable for high-speed operation applications.
Corrosion resistance: Ceramic materials have extremely strong corrosion resistance in acid and alkali environments and are suitable for highly corrosive environments such as chemical industry, marine and food processing. Zirconia and silicon carbide ceramic bearings can maintain stable performance in chemically corrosive media and extend the service life of the bearing.
Although ceramic bearings offer many performance advantages, their high cost and brittleness also present usage challenges. Therefore, in practical applications, it is necessary to select the appropriate ceramic material and bearing type according to the specific situation to ensure that it can perform optimally in a specific environment.
Disadvantages of Ceramic Bearings
Although ceramic bearings excel in many aspects, their disadvantages cannot be ignored. These disadvantages may limit their use in certain applications and need to be considered during design and selection.
High cost: The manufacturing cost of ceramic bearings is much higher than that of traditional metal bearings. The high price of ceramic materials and the complex processing technology lead to a large initial investment in ceramic bearings. In some cost-sensitive applications, the high cost of ceramic bearings may become the main factor limiting their use.
High brittleness: Ceramic materials are highly brittle and easy to break. In high-impact and vibration environments, ceramic bearings are prone to cracking, which affects their service life. Therefore, ceramic bearings should be used with caution in high-impact and vibration applications, and appropriate protective measures should be taken.
Size restrictions: Ceramic materials are difficult to process, and the process of manufacturing large-size ceramic bearings is complex and costly. This makes ceramic bearings limited in some applications that require large-size bearings. In these applications, it may be necessary to select other types of bearings or reduce the bearing size through design optimization.
High sensitivity: Ceramic bearings are highly sensitive to foreign matter. During operation, foreign matter entering the bearing may cause greater vibration and noise, affect work efficiency and may cause early damage. Therefore, in equipment using ceramic bearings, effective protective measures need to be taken to prevent foreign matter from entering the bearing.
High installation and maintenance requirements: Ceramic bearings have high requirements for installation and maintenance, requiring professional technology and equipment. Ceramic bearings require precise fit and uniform pressure during installation to avoid damage caused by improper installation. At the same time, ceramic bearings also have high requirements for the selection and maintenance of lubricants during use, and regular inspection and maintenance are required to ensure their normal operation.
Although ceramic bearings have many advantages in performance, these disadvantages may limit their use in certain applications. When selecting ceramic bearings, it is necessary to comprehensively consider their advantages and disadvantages, weigh the pros and cons, and ensure that they can perform at their best under specific conditions.
Application of Ceramic Bearings
Due to their unique properties, ceramic bearings have been widely used in many high-demand and special application scenarios. These application scenarios include but are not limited to the following fields:
Aerospace
Aerospace: Ceramic bearings are widely used in key parts of the aerospace field, such as engines and turbines, due to their high temperature stability and lightweight advantages. The high strength and wear resistance of ceramic materials enable bearings to operate stably and for a long time under extreme temperature and high load conditions. In addition, the lightweight characteristics of ceramic bearings help reduce the overall weight of aircraft and spacecraft, improve fuel efficiency and flight performance.
Medical Equipment
Medical Equipment: In the medical field, ceramic bearings are often used in magnetic resonance imaging (MRI) equipment due to their non-magnetic and corrosion resistance. MRI equipment needs to operate in a strong magnetic field environment. Traditional metal bearings may fail due to the influence of the magnetic field, while ceramic bearings are non-magnetic and can ensure the stable operation of the equipment. In addition, the corrosion resistance of ceramic materials allows bearings to be used in medical equipment for a long time without being corroded by disinfectants and other chemicals.
Chemical and Petroleum
Chemical and Petroleum: The corrosion resistance of ceramic bearings makes them an ideal choice for chemical equipment and oil drilling equipment. Chemical equipment and oil drilling equipment usually need to handle highly corrosive chemicals. Traditional metal bearings are prone to corrosion failure in these environments, while ceramic bearings can operate stably for a long time in corrosive media, extending the service life of the equipment.
Electronic equipment
Electronic equipment: In the field of electronics, ceramic bearings are used in equipment with high precision and high insulation requirements due to their high precision and insulation properties. For example, ceramic bearings are often used in precision instruments, optical equipment, and semiconductor manufacturing equipment to improve the stability and precision of the equipment. The low friction coefficient and high hardness of ceramic materials make the bearings perform well in precision operation.
Clean room
Clean room: Ceramic bearings are widely used in clean rooms because they do not require lubricants, can avoid pollution and maintain a clean environment. Clean rooms usually require extremely high cleanliness. Lubricants in traditional bearings may produce volatile organic compounds (VOCs) and pollute the environment, while ceramic bearings can operate stably without lubricants, ensuring a dust-free environment in the clean room.
Automotive industry
Automotive industry: In the automotive industry, ceramic bearings are used in key parts of high-performance cars and racing cars due to their high temperature resistance, wear resistance, and low friction coefficient. For example, ceramic bearings are often used in engines, turbochargers, and suspension systems to improve the power performance and handling stability of vehicles.
These application scenarios demonstrate the wide application and excellent performance of ceramic bearings in various fields. However, different application scenarios have different requirements for ceramic bearings. When selecting and using ceramic bearings, it is necessary to fully understand their performance characteristics and applicable scope to ensure optimal performance under specific conditions.
Factors for choosing ceramic bearings
When choosing ceramic bearings, you need to consider a variety of factors to ensure that they can perform at their best in actual applications. The following are several factors that need to be considered when choosing ceramic bearings:
Material type: Ceramic bearings of different materials are suitable for different application scenarios. Silicon nitride, zirconium oxide, aluminum oxide and silicon carbide are common ceramic bearing materials. Silicon nitride is suitable for high-speed and high-temperature environments, zirconium oxide is suitable for environments with high corrosion resistance requirements, aluminum oxide is suitable for electronic equipment with high insulation requirements, and silicon carbide is suitable for high-temperature and highly corrosive environments.
Size and precision: The size and precision of ceramic bearings directly affect their performance and service life. Choosing the right size and precision grade to ensure the matching degree between the bearing and the mechanical device is the key to ensuring the stable operation of the bearing. High-precision ceramic bearings can reduce friction loss, improve transmission efficiency and the overall performance of the equipment.
Speed: Select suitable ceramic bearings according to the speed in the actual application to ensure good stability and low friction coefficient at high speeds. Equipment running at high speeds needs to use low-friction, high-precision ceramic bearings to reduce energy loss and improve work efficiency.
Load and load capacity: Choose the right ceramic bearing according to the load and load capacity in the application to ensure that it can withstand sufficient load while maintaining good operating performance. Heavy load and high impact load applications require high-strength and high-toughness ceramic bearings to ensure their stability and durability.
Environmental factors: Consider the use environment of the bearing, such as temperature, humidity and corrosiveness, and select ceramic bearing materials and seal types suitable for the specific environment. High temperature and highly corrosive environments require high temperature and corrosion resistant ceramic bearings to ensure long-term stable operation under harsh conditions.
Cost: Ceramic bearings are expensive, and the relationship between performance and cost must be weighed when selecting to ensure economic rationality. In some applications, it may be necessary to consider performance and cost comprehensively and select ceramic bearing materials and models with high cost performance.
By comprehensively considering the above factors, you can choose the ceramic bearing that best suits the specific application requirements, so as to give full play to its excellent performance and improve the working efficiency and service life of mechanical equipment.
Installation of ceramic bearings
The installation of ceramic bearings requires care and patience to ensure correct installation and avoid damage. The following are several key points to note during the installation of ceramic bearings:
Temperature control: During the installation process, proper temperature control can help the bearings to be installed smoothly. For tight-fitting bearings, the bearings can be heated to a suitable temperature (such as 80-100°C) to expand the inner ring of the bearing for easy installation. During the heating process, care should be taken to avoid excessive temperatures to avoid damaging the bearing material.
Installation environment: The environment in which ceramic bearings are installed should be kept clean to prevent dust and foreign matter from entering the bearing. Foreign matter entering the bearing may cause unstable operation, increase friction loss, and even cause bearing damage. Therefore, the installation environment should be thoroughly cleaned before installation to ensure that it is dust-free and free of impurities.
Uniform pressure: During the installation process, pressure should be evenly applied on the circumference of the bearing end face to ensure the correct installation direction and position. Avoid using heavy objects such as axes and hammers to hit the bearings to avoid damage to the end faces. Uniform pressure can be applied using special installation tools, such as hydraulic presses or screw presses, to ensure that the pressure is evenly distributed and does not cause damage to the bearings.
Inspection and adjustment: After installation, the bearings should be inspected and adjusted to ensure that they are in the correct position and direction. Check whether the bearing runs smoothly, whether there are abnormal sounds and vibrations, and make appropriate adjustments as needed. If necessary, a trial run can be carried out to ensure the stability and reliability of the bearing under actual working conditions.
Lubricant selection: Ceramic bearings should choose a suitable lubricant before installation to reduce friction and wear during installation. For ceramic bearings operating under unlubricated conditions, cleanliness and pollution-free during installation should be ensured to avoid affecting bearing performance.
Specification selection: Choose the correct specification of ceramic bearings according to the needs of the installation location, rather than judging by the naked eye. Correct specification selection can make installation easier and stable. Wrong specification selection will not only increase the difficulty of installation, but may also cause the bearing to fail during use.
Ceramic bearing fit
The fit selection of ceramic bearings needs to be based on the load direction and load nature. The following are several key factors to consider in the ceramic bearing fit process:
Load type: Select the appropriate fit method according to the load type borne by the ring. Load types include rotating load, static load and non-directional load. Rotating load and non-directional load should adopt interference fit to ensure a tight fit between the ring and the shaft or housing to prevent the bearing from sliding or loosening during operation. For static load, transition fit or clearance fit can be selected for easy installation and removal.
Fit tolerance: Select the appropriate fit tolerance to ensure a tight fit between the bearing and the shaft or housing. The selection of fit tolerance should be optimized according to the load, speed and use environment of the bearing. Too large fit tolerance may cause the bearing to loosen during operation, affecting its stability and service life; while too small fit tolerance may increase the difficulty of installation and even cause bearing damage.
Lubrication and sealing: During the fitting process, appropriate lubrication and sealing methods should be selected to ensure lubrication and protection of the bearing during operation. The selection of lubricants should be optimized according to the working environment and working conditions of the bearing to reduce friction and wear and extend the service life of the bearing. The sealing device should be able to effectively prevent dust, impurities and moisture from entering the bearing and keep the bearing clean and lubricated.
Fitting method: Select the appropriate fitting method according to the type of bearing and the use environment. Common fitting methods include cold fitting, hot fitting and hydraulic fitting. Cold fitting is suitable for clearance fitting and light load applications; hot fitting is suitable for interference fitting and high load applications, by heating the inner ring of the bearing or cooling the outer ring of the bearing to expand or contract it for easy installation; hydraulic fitting is suitable for large-size bearings and heavy-load applications, and the bearing is tightly fitted through hydraulic pressure.
Surface roughness: The surface roughness of the shaft and housing has an important influence on the fit quality of the bearing. Excessive surface roughness will increase friction and wear, affecting the operating performance and service life of the bearing. When designing the fit, the surface finish of the shaft and housing should be ensured to meet the requirements to reduce friction loss and ensure the smooth operation of the bearing.
Through the above matching design and selection, the stability and reliability of ceramic bearings in practical applications can be ensured, and their excellent performance can be fully utilized.
Conclusion
Ceramic bearings have become an ideal choice for many high-demand applications due to their excellent performance and wide application prospects. This article discusses the materials, performance and structural characteristics of ceramic bearings in detail, analyzes their advantages and disadvantages, discusses their application scenarios in various fields, and provides suggestions for selection, installation, matching and disassembly. Taking into account the advantages and disadvantages of ceramic bearings, it can be concluded that under specific conditions and application scenarios, ceramic bearings have obvious advantages and are high-performance mechanical parts worthy of investment.
FAQ
What applications are suitable for ceramic bearings?
Ceramic bearings are suitable for high-demand and special applications such as aerospace, medical equipment, chemical and petroleum, electronic equipment, clean rooms and automotive industries.
What are the main advantages of ceramic bearings?
Ceramic bearings have advantages such as high hardness, wear resistance, corrosion resistance, high temperature performance, low friction coefficient, lightweight, non-magnetic and insulating properties.
What are the main disadvantages of ceramic bearings?
The main disadvantages of ceramic bearings include high cost, high brittleness, high installation and maintenance requirements, size restrictions and high sensitivity to foreign matter.
How to choose suitable ceramic bearings?
When selecting ceramic bearings, factors such as material type, size and accuracy, speed, load and load capacity, environmental factors and cost need to be considered comprehensively.
What should be paid attention to when installing ceramic bearings?
The installation of ceramic bearings requires attention to specification selection, installation environment, uniform pressure, temperature control, lubricant selection and inspection and adjustment after installation.
What should be paid attention to when removing ceramic bearings?
The removal of ceramic bearings requires preparation, selection of appropriate removal tools, avoidance of rough operation, detailed inspection and safety measures.