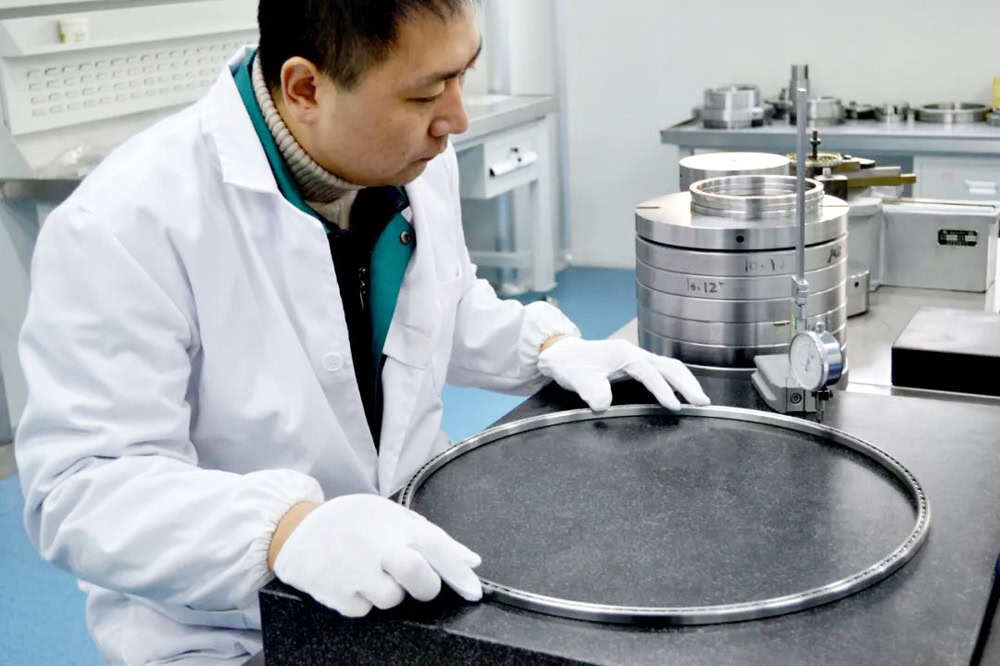
Bearing Manufacturer & Supplier
Specialize in ball bearings, roller bearings, thrust bearings, thin section bearings etc.
Manufacturing And Maintenance of Thin-Section Bearings
Thin-section bearings are widely used in high-end products such as industrial robots, aerospace vehicles, and medical equipment due to their light weight, compact structure, and small moment of inertia. With the increase in market demand, the production technology and quality requirements of thin-section bearings are also increasing. Due to their small radial wall thickness and poor rigidity, they are very prone to large radial deformation, so they face many challenges in the manufacturing process. This article will discuss in detail the manufacturing difficulties, cage fracture analysis, and maintenance methods of thin-section bearings to help readers better understand and apply thin-section bearings.
Table of Contents
ToggleManufacturing difficulties of thin-section bearings
Forging process
The forging process is the first step in the manufacture of thin-section bearings. For thin-section bearing rings with large sizes and small aspect ratios, the combined forging method is usually used. Combined forging is to combine two or blanks together for forging, and then use wire cutting to separate the rings after the rough grinding process. This method can not only reduce the processing difficulty of the forging process, reduce the deformation of the rings and the end surface machining allowance, but also save raw materials and improve production efficiency.
Turning process
In the turning process, the clamping and positioning of thin-section bearings, excessive cutting force, unreasonable fixture design, cutting thermal deformation and vibration during cutting will affect the processing accuracy. In order to reduce the deformation caused by excessive turning stress, a steel soft claw clamping ring with a large enveloping circle contact area and unquenched is usually used for rough turning. For example, a multi-point clamping chuck (12-point clamp or 24-point clamp) can be used, the positioning clamping scheme can be changed (change radial clamping to end face positioning clamping method), and the process parameters can be adjusted (high-speed cutting, small back cutting amount, larger main deflection angle of the tool, smaller tool tip arc radius, reasonable selection of cutting fluid, etc.). After rough turning, an additional tempering is required to eliminate stress. After that, the end face is soft-ground, and then the ring is fine-turned.
During the heat treatment process, the internal structure of the ring undergoes phase change, mainly from austenite to martensite, the density decreases, the volume expands, and the structure stress is generated; in addition, the ring is rapidly quenched and cooled from the expansion state of high temperature (thin-walled products are generally 830-845℃), generating thermal stress. When these two internal stresses exceed the yield limit of the material, the material will undergo plastic deformation. Usually, die quenching is used to control deformation. When there is no condition for die quenching, and the outer diameter deformation of the ring after quenching is too large to exceed the process requirements, the method of comprehensive shaping and then tempering is used to correct it so that it is controlled within the range of process requirements.
Grinding process
In the grinding process, the main difficulty lies in selecting appropriate grinding equipment, processing methods and grinding process parameters. For example, the method with a reinforcing ring can be used for processing with a “one-to-two” structure; the outer diameter surface can be ground by multiple fine adjustments of the machine tool; tempering stabilization treatment is added during the process to ensure that the grinding quality of the ring meets the process requirements.
Cage Fracture Analysis
The cage in the rolling bearing plays the role of isolating the rolling elements at equal distances and preventing the rolling elements from falling, guiding and driving the rolling elements to rotate. Generally speaking, the cage of thin-section bearings will not be damaged under reasonable working conditions, but incorrect operations in daily production will reduce the service life of the bearing cage. Common cage failure phenomena include: cage damage, loose or broken rivets, cage fracture, and scattered rolling elements. So, what are the causes of thin-section bearing cage fracture?
Poor lubrication
If the bearing is not lubricated adequately during operation, it will affect normal operation. Insufficient lubricating oil will cause the bearing to be in an oil-poor state, which is prone to bite wear, thereby deteriorating the working surface condition. The tearing of bite wear will enter the cage, generating abnormal loads, which may cause the cage to break.
Excessive load
When there is a problem with the cage during installation, such as improper installation, tilting or excessive interference, the clearance will be reduced, friction and heat will be aggravated during use, the surface will soften, and abnormal peeling will occur prematurely. The peeled foreign matter enters the cage pocket, causing the cage to block operation and generate additional loads, aggravating the wear of the cage, and eventually causing the cage to break.
Creep
The creep phenomenon refers to the sliding phenomenon of the ring. When the interference of the mating surface is insufficient, the load point moves in the surrounding direction due to sliding, resulting in the ring relative to the shaft or housing. The position deviation in the circumferential direction. Creep will significantly wear the mating surface, and wear powder may enter the bearing, causing abnormal wear, raceway spalling, cage wear and additional load, and eventually lead to cage breakage.
Foreign matter intrusion
Foreign matter entering the cage is the intuitive cause of cage breakage. Hard foreign matter will aggravate the wear of the cage, generate abnormal additional loads, and thus cause the cage to break.
Poor cage quality
The quality of the cage is also an important factor affecting its service life. If the cage is of poor quality, especially if there are defects such as cracks, large pieces of foreign metal inclusions, shrinkage holes, bubbles, or riveting defects (such as missing nails, pad nails or gaps between the two halves of the cage, severe riveting damage, etc.), it is easy to break during use.
Thin-section bearings require regular maintenance to extend their service life and ensure the normal operation of the equipment. The following are the main maintenance methods for thin-section bearings.
Cleaning
Cleaning is the first step in maintaining thin-section bearings. Bearings will be contaminated by external dust and impurities during use. Regular cleaning can effectively extend the service life of bearings. Cleaning is divided into two steps: rough cleaning and fine cleaning.
Rough cleaning: remove the bearing, put it in the cleaning oil, use a metal mesh as a bottom, and use a brush to remove grease and dust on the surface. Be careful not to damage the rolling surface of the bearing.
Fine cleaning: put the bearing in the cleaning oil, rotate the bearing slowly, and clean it carefully. The cleaning oil should be kept clean.
Rust prevention
After cleaning, the bearing needs to be treated with rust prevention. After wiping the surface of the bearing clean, soak it in rust prevention oil so that the rust prevention oil covers the surface of the bearing to form a protective film. Rust prevention can prevent rust on the surface of the bearing and extend its service life.
Lubrication
Lubrication is one of the important steps in maintaining thin-section bearings. After the rust prevention treatment is completed, apply lubricating oil or grease evenly to the surface of the bearing, including the inner and outer rings, steel balls and cages. When applying lubricating oil, apply it while rotating the bearing to ensure that the lubricating oil fully enters the bearing to achieve a good lubrication effect.
Storage
When storing thin-section bearings, try to store them in an environment with a humidity of less than 65% and a temperature of about 20 degrees, place them on a shelf higher than 30cm, and avoid direct sunlight and cold walls. The correct storage method can prevent the bearings from getting damp and rusting.
Conclusion
Thin-section bearings play an important role in modern industry, and their manufacturing and maintenance processes are complex and delicate. Through reasonable manufacturing processes and strict quality control, high-quality thin-section bearings can be produced to meet the needs of various high-end applications. At the same time, regular maintenance can effectively extend the service life of bearings and ensure the stable operation of equipment.
Frequently Asked Questions (FAQ)
1. What is the service life of thin-section bearings?
The service life of thin-section bearings depends on operating conditions, maintenance methods and load capacity. Generally, reasonable lubrication and regular maintenance can significantly extend their service life.
2. How to prevent the thin-section bearing cage from breaking?
The key to preventing cage breakage is to ensure adequate lubrication, avoid excessive loads, prevent foreign matter from entering, prevent creep, and select high-quality cages.
3. What are the main application areas of thin-section bearings?
Thin-section bearings are widely used in high-end product fields such as industrial robots, aerospace vehicles, and medical equipment, and are particularly suitable for applications with limited space and strict weight requirements.
4. How to clean thin-section bearings?
Cleaning is divided into two steps: rough cleaning and fine cleaning. When rough cleaning, use a metal mesh as a base and use a brush to remove grease and dust on the surface. When fine cleaning, put the bearing in the cleaning oil and rotate it slowly for cleaning.
5. What should be paid attention to when storing thin-section bearings?
Thin-section bearings should be stored in an environment with a humidity of less than 65% and a temperature of about 20 degrees, placed on a shelf higher than 30cm, and avoid direct sunlight and cold walls.