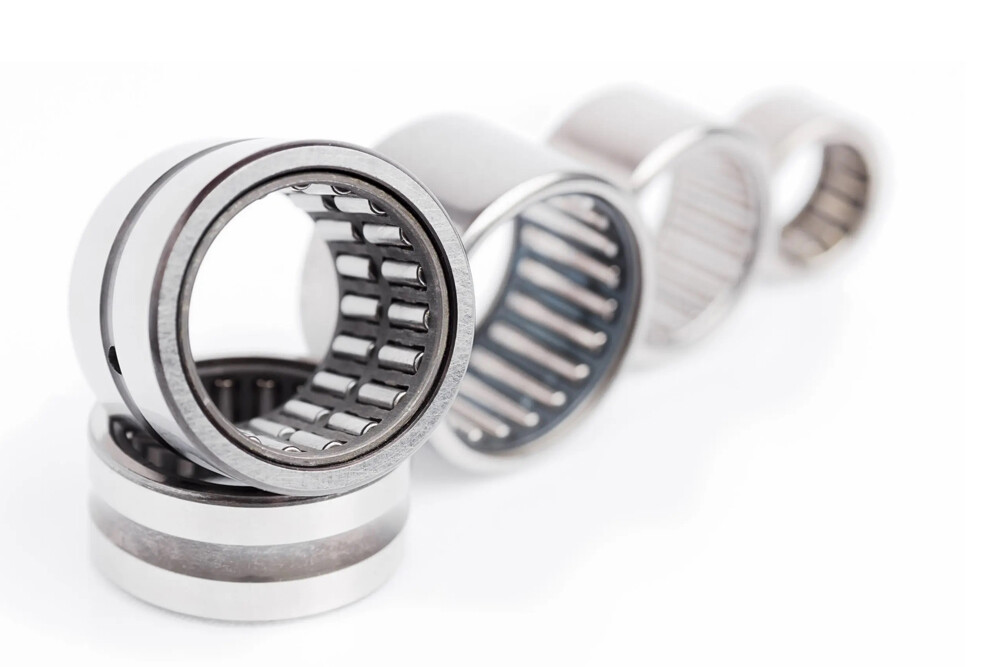
Bearing Manufacturer & Supplier
Specialize in ball bearings, roller bearings, thrust bearings, thin section bearings etc.
Ultimate Guide to Ball Bearings vs Needle Roller Bearings
Explore the key differences between ball bearings vs needle roller bearings. Read our blog to find out which type of bearing is best for your application. From high-speed turbochargers in automobiles to precision machinery in industrial applications, needle roller bearings and ball bearings are the two most common bearing types used for support and rotation. But which one is better? This article will compare ball bearings vs needle roller bearings to help you determine which one is the best choice for your specific application. Learn about the key differences, uses and common applications of ball bearings vs needle roller bearings. Save time and increase efficiency with analysis from our bearing experts.
Table of Contents
ToggleBall Bearings vs Needle Roller Bearings
Ball bearings vs needle roller bearings are both rolling bearings. Rolling bearings consist of orbital rings (inner and outer rings), rolling elements (balls or rollers) and cages. Several rolling elements are arranged between two opposing track rings of a rolling bearing, and a cage is used to prevent the rolling elements from contacting each other and maintain a certain interval for operation. The geometric shape of the rolling elements and the inner and outer ring raceway surfaces is point (ball) or line (roller) contact. Theoretically, the rolling elements roll and rotate between the inner and outer rings.
The main function of bearings is to help mechanical equipment reduce friction. Bearings reduce friction by causing two surfaces to roll against each other, thereby reducing the amount of friction produced. The contact surface (point) between the rolling elements and the raceway ring supports the load on the bearing with its raceway surface. The bearing cage does not directly bear the bearing load. In addition to maintaining the correct position of the rolling elements at equal intervals, the bearing cage also prevents the rolling elements from falling off when the bearing is installed.
The loads carried by bearings include radial loads and thrust loads. Rolling bearings are mainly divided into two categories: ball bearings and roller bearings according to the shape of the rolling elements. Compared with roller bearings with the same main dimensions, ball bearings are suitable for high-speed, high-precision, low-torque, and low-noise applications. – Suitable for vibration applications due to low friction resistance and shaft runout during rotation. Since there are many forms and types of rolling bearings, each has its own inherent characteristics. Rolling bearings have the following common advantages:
(1) The friction coefficient is small
(2) There are internationally unified standards and specifications, and brands are easily interchangeable.
(3) Low lubricating oil consumption.
(4) The bearing can bear both radial load and axial load.
(5) It is also easier to use at high or low temperatures.
(6) Applying preload can improve bearing rigidity.
What are ball bearings?
Ball bearings are designed to reduce rotational friction and support radial and axial loads. The basic design of a ball bearing contains at least two races that contain balls and transmit loads through the balls. One of the races is usually fixed, while the other race is connected to a rotating component, such as a wheel hub or axle. As the bearing rotates, the balls roll between the races, reducing friction and wear on the bearing. One of the main advantages of ball bearings is that they have a lower coefficient of friction than other types of bearings. This allows them to operate with less heat and wear, extending the life of the bearings. They also have high-speed capabilities, which makes them suitable for high-speed applications.There are many types of ball bearings:
Among ball bearings, deep groove ball bearings are the most commonly used bearings. Both the inner and outer ring tracks are arc-shaped deep grooves, which can bear radial load, bidirectional axial load or combined load, and are also suitable for high-speed rotation. One race of a ball bearing is connected to a rotating component (such as a shaft or hub), while the other race is fixed. When the seat ring rotates, the ball also rotates. Due to the rotation of the ball, the friction coefficient is less than that of two flat surfaces rubbing against each other. The contact area between the retainer’s race and the ball is very small. Therefore, ball bearings tend to have lower load-carrying capacities than other types of bearings. However, these controllers may tolerate some misalignment between the outer and inner rings. However, one of the disadvantages of deep groove ball bearings is that the balls “flatten” over time and may eventually fail if the outer ring wears. Therefore, parameters such as the load rating of ball bearings must be checked regularly.
What is a needle roller bearing?
Needle roller bearings are a special type of roller bearing that use slender cylindrical rollers that resemble needle rollers. The main difference between needle roller bearings and other types of roller bearings is the diameter to length ratio of the rollers. The diameter to length ratio is between 0.1 and 0.4. One of the main advantages of needle roller bearings is the larger surface area in contact with the outer surface of the bearing, resulting in a higher load-carrying capacity than ball bearings. This makes them ideal for applications with high loads and limited space. The typical structure of a needle roller bearing consists of a needle roller cage that orients and houses the needle rollers, the needle rollers themselves, and the outer ring.
The needle roller cage is usually made from a material like stamped steel or plastic and helps to hold the needle roller in place, while the outer ring is usually made from a complex material like steel or brass. Needle roller bearings are available in many different designs, including radial, thrust and combined loads. Radial needle roller bearings are designed to support radial loads, while thrust needle roller bearings are designed to support axial loads. Combined radial and thrust needle roller bearings are designed to support radial and axial loads. In terms of maintenance, needle roller bearings have relatively low maintenance requirements. They are usually lubricated with grease or oil, and the lubricant should be checked and replenished as needed. Additionally, they should be kept clean and free of clutter to ensure proper functioning. Overall, needle roller bearings are versatile and durable roller bearings that are ideal for a variety of applications. They feature high load carrying capacity and minimal space requirements, and are available in a variety of designs to suit different application needs.
Compared with ordinary rolling bearings, needle roller bearings have a smaller cross-sectional height and space, stronger load-bearing capacity and significantly improved rigidity. Needle roller bearings are capable of carrying 2 to 8 times load than ball bearings or equivalent to cylindrical roller bearings of the same shaft diameter. At the same time, needle roller bearings are suitable for rocking motion due to the small inertial force caused by rotation. Suitable for lightweight, small machine design, and can also be used to replace sliding bearings. Needle roller and cage assembly is the main type of needle roller bearing, which includes a needle roller and a mechanical cage that supports it. In the miniaturized design that requires space, it is often used in reciprocating compressors and small engine connecting rod bearings. In particular, the design of the cage can be used in environments with large speed changes, acceleration and deceleration, high temperatures, and poor lubrication conditions.
Advantages of ball bearings
The advantages of ball bearings are relative stability, small starting and running torque, low power loss, and high efficiency. However, their disadvantage is the smaller load capacity for their size. Applications include small power motors, automotive and tractor transmissions, machine tool transmissions, general machinery and tools.
Strong carrying capacity
A ball bearing is a bearing that can withstand axial and radial loads. It supports the load by rolling spherical balls between the inner and outer rings. Compared with other bearings, ball bearings have a stronger load-bearing capacity and can withstand larger loads, making mechanical movement stable.
Flexible operation
Because ball bearings are supported by rolling balls, their operation flexibility is higher. In mechanical movement, it can withstand a certain angle of deviation, allowing mechanical parts to move in different directions, thereby improving the operability of mechanical movement.
Easy to install
The structure of ball bearings is relatively simple and easy to install. Simply place the ball bearing in the equipment bearing seat and secure it with a fastening nut or threaded retainer. Compared with other installation methods with complex bearing structures, the installation of ball bearings is simpler and convenient.
Durable
The inner and outer ring surfaces of the ball bearing are made of high-quality steel, so it is very wear-resistant. It can still maintain good performance during long-term operation in mechanical movements and is not easily damaged, which increases the service life of ball bearings.
Save Space
Ball bearings take up less space than other bearings. For bearings of the same specifications, the outer diameter of the ball bearing is smaller, which can save space. In the design of mechanical equipment, ball bearings can provide possibilities for the compact structure of the equipment.
Advantages of needle roller bearings
Needle roller bearings have the advantages of small friction resistance, low power consumption, and high mechanical efficiency. However, they have the disadvantage of being relatively expensive and producing noise than other bearings. Applications include compressors, transmissions, pumps, torque converters and suspension systems. Needle roller bearings are durable, compact, and lightweight and are often preferred over ball bearings when space is limited.
Low maintenance cost
Most needle bearings require no daily, weekly or even monthly maintenance. However, they do need to be kept well lubricated. This means choosing the right lubricant type and ensuring that the right amount of lubricant covers the bearing’s rolling elements (needle rollers). Proper lubrication is also critical to keeping dirt and debris out and protecting bearings from corrosion. It’s also important to know when to lubricate and how much lubricant to use. The best solutions usually involve installing an automatic lubrication system so that the bearings receive the right amount of lubricant at the right time.
Excellent axial and radial load capacity
Industrial needle roller bearings can also withstand high axial and radial loads. This is different from ball bearings, which are typically used in applications that do not require high axial and radial load requirements. Axial loads, sometimes called thrust loads, are forces applied parallel to the axis, whereas radial loads are applied perpendicular to the axis. Needle roller bearings bear high loads on the mounting surface (axial direction) and in the radial direction, and therefore have excellent axial and radial load capabilities.
Excellent rigidity
Stiffness refers to the ability of a material to maintain its shape without deforming, bending, or breaking when high external forces are applied. Industrial needle roller bearings have excellent rigidity, and even a small amount of elastic deformation on the needle roller bearing usually does not affect its operation. The use of rigid bearings in tight-fit applications with high axial and radial loads helps protect mating surfaces and adjacent parts from friction and excessive wear. Rigidity will vary depending on the size of the bearing and the type of needle bearing used. Factors including the physical space the bearing must occupy and the axial and radial loads the bearing must withstand should always be considered. Increasing the number of needle rollers used will increase rigidity.
Ideal for high speed applications
Ball bearings generate less centrifugal force in high-speed applications. This increases friction, causing the ball bearing to overheat and eventually break. In contrast, needle roller bearings produce higher centrifugal forces at high rotational speeds because the needles are longer and heavier than the balls in ball bearings. Needle roller bearings also produce high rotation and do not overheat at high speeds, making them ideal for high temperature applications.
Low coefficient of friction
Friction occurs when a given material or surface encounters resistance when sliding, moving, or rubbing against another material or surface. The coefficient of friction is the ratio of the friction between two materials to the normal force holding them together. A low coefficient of friction means low resistance between two surfaces. Needle roller bearings have a low coefficient of friction during operation. This means friction is very low, so the bearings don’t overheat. This also means that the bearings do not require much lubrication to control friction between mating surfaces.
Excellent mechanical properties
Finally, mechanical properties vary depending on the material the bearing is made of. However, in most cases, bearing manufacturers heat treat needle roller bearings to improve their mechanical properties. Heat treatment can improve the strength, durability, hardness, ductility, elasticity and wear resistance of bearings. Since the bearing will be in contact with other metals, increasing its hardness, tensile strength, ductility and wear resistance through heat treatment can help extend the service life of the bearing while protecting any mating surfaces. This makes the bearings stronger and durable, last longer and require fewer replacements.
Disadvantages of ball bearings
The main disadvantage of ball bearings is that they tend to wear out over time. The rolling elements of a ball bearing will eventually wear out, and when the parts begin to wear out, it can cause the bearing to make noise. Additionally, if a ball bearing is exposed to extreme heat or cold, it can become brittle, causing the bearing to crack and break, causing it to fail. Ball bearings are also susceptible to contamination, which can cause the bearings to become clogged and unable to rotate smoothly. If the bearings are not lubricated regularly, they will make noise and begin to vibrate, causing premature bearing failure. Finally, ball bearings can be expensive to replace and maintain. They can be difficult to install and require special tools and skills to install, which can increase the cost of replacing them. Additionally, they require regular maintenance such as lubrication and cleaning, which increases the total cost of ownership.
Disadvantages of needle roller bearings
Needle roller bearings can be very expensive. If lubrication is not properly maintained, it can be easily damaged. If a needle bearing is used in an application without adequate support, it may wear prematurely. In addition, needle roller bearings are susceptible to impact loads and can be easily damaged if they are subjected to excessive force. Needle roller bearings require precise alignment to function properly, but this can be difficult to achieve in some applications.
Ball bearing applications
Ball bearings reduce rotational friction and support radial and axial loads in different applications. Ball bearings are commonly found in robots, electric motors, pumps, fans, compressors and other rotating machinery to support rotating shafts and reduce friction between the shaft and its components. They are also used in conveyor systems and automotive components. Additionally, ball bearings are used in skateboards, inline skates, and other recreational products. Ball bearings are also found in many consumer products, such as handheld appliances, toys and tools. Ball bearings are also used in high-performance medical and dental equipment, such as dental drills and medical imaging equipment. Ball bearings are also used in many industrial machines, such as machine tools, pumps, compressors and conveyor systems.
Applications of needle roller bearings
Needle roller bearings are commonly used in automotive, aerospace and industrial applications. These bearings are designed to provide support for rotating and oscillating shafts and are used in a variety of applications. In automotive applications, needle roller bearings are used in transmissions, clutches, differentials, power steering systems and other driveline components. In gearboxes, needle bearings are used to reduce friction and wear on components and reduce the power required to drive the gearbox. In clutches, needle roller bearings are used to reduce wear and friction on the clutch plates, making them last longer and provide smoother operation. In aerospace applications, needle roller bearings are used in aircraft engines, landing gear and control surfaces. In engines, needle roller bearings are used to reduce friction and wear on crankshafts and other rotating parts, which helps improve engine efficiency and performance. In landing gear, needle bearings are used to reduce friction and wear on suspension components and provide a smoother ride. On control surfaces, needle bearings are used to reduce friction and wear on the actuators, allowing for better control of the aircraft.
If you have questions about ball bearings vs needle roller bearings or need help selecting the best needle roller bearing for your application, please contact Aubearings. Established over twenty years ago, we are an ISO 9001 and IATF 16949 certified bearing manufacturer specializing in all types of bearings. Contact us today to learn about our capabilities and bearing designs or to request a quote.