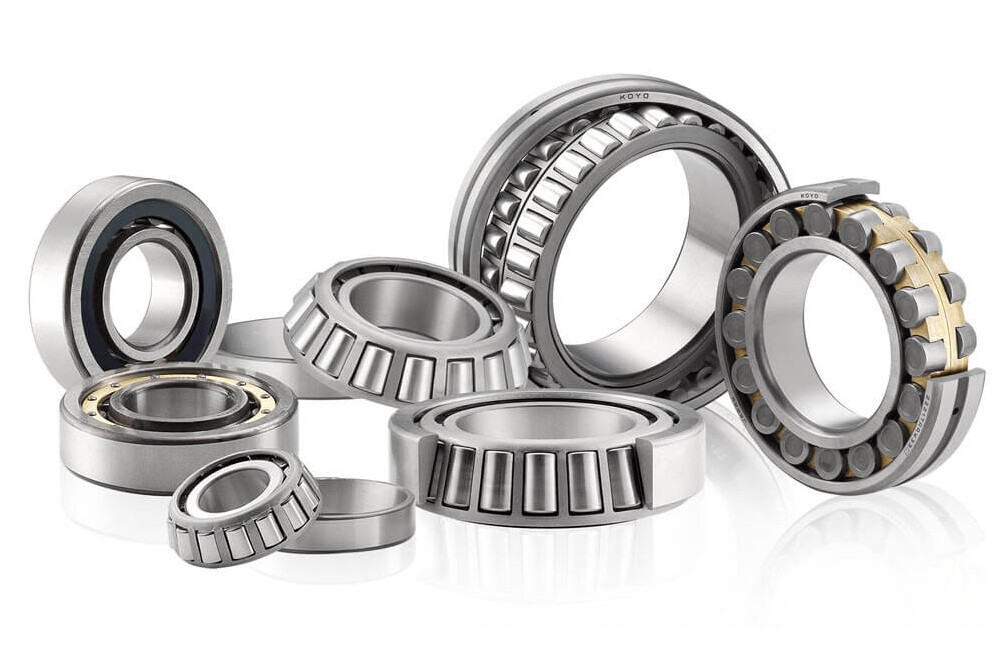
Bearing Manufacturer & Supplier
Specialize in ball bearings, roller bearings, thrust bearings, thin section bearings etc.
The Ultimate Guide to Rolling Bearings
A roller bearing is a type of bearing that uses rolling elements to support loads and reduce friction. Roller bearings are similar to ball bearings and are designed to carry loads while minimizing friction. In contrast to ball bearings, roller bearings consist of barrel or tapered rolling elements instead of balls. Roller bearings use cylindrical rolling elements rather than balls to transfer load. Roller bearings can handle heavier loads than similarly sized ball bearings, but they cannot operate at the same high speeds as ball bearings. Advances in technology have produced precision roller bearings that offer an excellent balance between cost, size, load capacity, accuracy, life and weight. In this blog we will take a closer look at the different types of roller bearings.
Table of Contents
ToggleWhat is a roller bearing?
Roller bearings consist of an inner ring, an outer ring and a set of rollers fixed between the two rings. Rollers are usually cylindrical but can also be tapered or needle-shaped. The inner and outer rings are usually made of steel, while the rollers are made of steel or a harder material such as ceramic or tungsten carbide. Roller bearings work on the same principle as ball bearings and have one main function: to carry loads with minimal friction. The difference between ball bearings and roller bearings is the shape and structure. The former uses balls and the latter uses cylindrical rolling elements. Roller bearings can contain single or multiple rows of rolling elements; multiple rows significantly increase radial load carrying capacity. Additionally, using differently shaped rollers can further reduce friction and support radial and axial loads. Although roller bearings can handle higher loads than traditional ball bearings, their applications are usually limited to low-speed operation. Many types of roller bearings are self-aligning and can easily overcome misalignment and installation issues – reducing maintenance, repairs and labor requirements. Roller bearings come in many shapes and sizes and can be customized for special situations. In addition, higher performance can be achieved using flanges, cages and multi-row bearings to meet specific application needs.
Single row rollers have one row of rolling elements. They have a simple, non-detachable design and can only withstand loads in one direction. The main advantage of single row bearings is that they are an excellent choice for high speed applications. The rolling element load action line and the radial load action line are usually not on the same radial plane. Therefore, single row rollers must be installed in pairs when subjected to pure radial loads.
Double row roller bearings, on the other hand, have two rows of rolling elements. They can withstand radial and axial loads in both directions. However, they can limit the axial displacement of the shaft and housing to the axial clearance of the bearings. Double-row bearings have higher rigidity than single-row bearings, allowing them to withstand overturning moments or tilting effects. In addition to increased rigidity, other advantages of double-row bearings include high load capacity and compactness.
Why use roller bearings?
The main reason for using roller bearings is to reduce friction for easy application. As a result, they generate less heat during operation and reduce the need for relubrication. Other advantages of using roller bearings include:
Reduce maintenance and repair costs
Separate design, easy to install and disassemble
Interchangeable program – user can easily replace the inner ring
Bearings can easily change direction without technical modifications
Allowed axial displacement
Different types of roller bearings
There are thousands of different types of roller bearings available to meet specific application requirements. Aubearing offers a wide selection of roller bearings, including the following popular types:
Cylindrical Roller Bearings
Cylindrical roller bearings have high radial load capacity and moderate thrust load. They contain cylindrical rollers but are not true cylinders. Instead, these rollers feature convex surfaces or end relief to reduce stress concentrations. This geometry achieves low friction and allows high-speed applications. The rollers are guided by the ribs of the inner or outer ring. The inner ring and outer ring can be separated for easy assembly, and the two can fit tightly. Cylindrical roller bearings are similar in design to needle roller bearings, but the diameter and roller length dimensions are closer. Cylindrical roller bearings have rollers that are longer than their diameter and can handle higher loads than ball bearings. Aubearing’s cylindrical roller bearings can withstand heavy radial loads and can be used in high-speed applications. Cylindrical roller bearings are divided into two categories. Next we introduce single row cylindrical roller bearings and double row roller bearings.
Single row cylindrical roller bearings
Single row roller bearings are removable, the ring with guide flange is together with the cage with rollers, and the second ring can be assembled separately. They are made in several series in the basic designs NU, N, NJ and NUP. Single row cylindrical roller bearings have the characteristics of high rigidity, low friction, the ability to transmit high radial loads and are suitable for high speeds. Single row cylindrical roller bearings are suitable for special equipment applications and are available with low or high radial clearance. For higher accuracy or higher rotational speeds, use bearings with higher operating accuracy.
Double row cylindrical roller bearings
Cylindrical roller bearings are designed for increased strength to withstand radial loads. Double row cylindrical roller bearings are interchangeable so that the dimensions and diameter below the rollers (type NNU) and the diameter above the rollers (type NN) comply with ISO/DIN standards. Interchangeability is designed for rings without rollers so that they can be interchanged with competitor inner rings. Double row cylindrical roller bearings are used in printing cylinders, rolling mill rollers, machine tool spindles and other places where thin-walled bearings are needed in printing machinery.
Spherical roller bearing
Spherical roller bearings consist of an inner ring with two raceways inclined at an angle to the bearing axis, an outer ring with a common spherical raceway, spherical rolling elements, a cage and, in some designs, an inner center ring. Their construction enables them to carry heavy axial and radial loads at high speeds in any direction, even in the presence of bearing misalignment or shaft deflection. Spherical roller bearings are versatile and available with cylindrical or tapered bores from 20 mm to 900 mm, allowing the user to install them with or without a sleeve adapter. Spherical roller bearings can carry heavy loads even when dealing with misalignment and shaft deflection. Spherical roller bearings are available with a variety of internal clearance and cage options to withstand axial loads in either direction as well as heavy shock loads. Spherical roller bearings have an inner spherical outer ring. The roller is thicker in the middle and thinner at both ends. Therefore, spherical roller bearings can accommodate both static and dynamic misalignment. However, spherical rollers are difficult to produce and therefore expensive, and because there is a certain amount of slippage between the rolling elements and rings, the bearings have higher friction than ideal cylindrical or tapered roller bearings.
Tapered Roller Bearings
Tapered roller bearings are designed on the principle that cones can roll against each other without slipping. They consist of inner and outer rings and rows of inseparable cone assemblies. Tapered roller bearings run on tapered raceways that correspond to the size of the bearing. Tapered design. Due to their large contact surface area, tapered rollers can withstand heavy radial, axial and thrust loads, typically in medium speed applications. They are very similar to cylindrical bearings, but if you decide which one to buy, the main difference is this: Cylindrical roller bearings can only handle a limited thrust load. At the same time, its tapered counterpart can withstand huge thrust loads. Tapered roller bearings generally come in imperial and metric sizes. Tapered roller bearings use tapered rollers running on a tapered race and can generally handle higher loads than ball bearings due to their larger contact area. For example, tapered roller bearings are used as wheel bearings in most wheeled land vehicles. The disadvantages of this type of bearing are that due to the complexity of manufacturing, tapered roller bearings are generally expensive than ball bearings; under heavy loads, the tapered roller acts like a wedge, and the bearing load will tend to try to eject the roller; compared to ball bearings , the force from the collar that holds the rollers in the bearing increases bearing friction.
Single row tapered roller bearings
Single row tapered roller bearings are the most basic and widely used bearings and consist of a tapered component and an outer ring. Single row tapered roller bearings are designed to carry combined loads, i.e. radial and axial loads acting simultaneously. The projected lines of the raceways intersect at a common point on the bearing axis to provide true rolling action and thus low friction torque during operation.
Double row tapered roller bearings
Double row tapered roller bearing designs come in many variations and have different characteristics. By design, these bearings can handle heavy radial loads, axial loads in both directions, and have high stiffness. Double row tapered roller bearings are commonly used in gearboxes, lifting equipment, rolling mills and machines in the mining industry, for example. Tunnel boring machine.
Needle roller bearings
Needle roller bearings are a variation of cylindrical bearings. The cup design of needle roller bearings enables them to withstand high radial load capabilities in applications requiring high-speed rotational accuracy. The main advantage of needle rollers is the ability to use the mating surface as an inner raceway or an outer raceway, or both. Needle roller bearings maintain a simple cross-sectional design. Needle roller bearings are thinner than traditional roller bearings and can be designed with or without an inner ring. Needle roller bearings are ideal for handling radial space constraints in heavy-load, high-speed applications. Needle roller bearings enable high load capacities while still offering a slim cross-section design. These bearings are available with imperial or metric seals. Needle roller bearings are used extensively in automotive components such as rocker arm pivots, pumps, compressors and transmissions. Driveshafts on rear-wheel drive vehicles usually have at least eight needle bearings (four per U-joint), often if they are particularly long or run on steep slopes.
Thrust roller bearing
Thrust bearings are special rotating bearings used to handle high loads in harsh environments. Thrust bearings are designed for pure thrust loads and can carry little or no radial loads. Roller thrust bearings use similar rollers to other types of roller bearings. Thrust roller bearings can be equipped with cylindrical rollers or spherical rollers. Thrust bearings only bear axial load, but have high axial rigidity and are suitable for heavy loads. They contain convex rollers, are self-aligning, and are not affected by shaft deflection or installation errors.
Global manufacturers launch approximately 10 billion bearings every year. Ninety percent of these last longer than the machine on which they are installed. Only 0.5% or 50,000,000 units are replaced due to failure or damage. Roller bearings become damaged or fail for a variety of reasons, including:
fatigue
Poor lubrication scheme or practice
Poor sealing causes contamination
Improper handling, installation and maintenance
Suitable for heavier loads or loads different from those specified
The frequency and extent of damage vary by industry and application. For example, roller bearings in the pulp and paper industry fail due to contamination and poor lubrication rather than fatigue. These events often leave damaging imprints within the bearing raceway, known as path pattern damage. Inspecting components enables users to determine the root cause of damage. Therefore, they can use a bearing puller to remove the bearing from the shaft, inspect it, and take corrective action to ensure the problem does not occur. Take, for example, contamination due to seal failure. Particles are lodged in the bearing recesses along the raceway. Continuous excessive rolling can cause sharp dents in the track. When normal function puts stress on the dented area, it can cause surface fatigue. The metal casing begins to pull away from the raceways, a process called spalling. If the user does not address the damage, the spalling will continue until the bearing becomes unusable.
Customers can use the formula for bearing dynamic capacity C to calculate roller bearing life. It refers to the standard static radial load that a rolling bearing can withstand for one million cycle life. Industrialists use bearing dynamic capacity to predict rating life at specific loads and rolling speeds. Manufacturers recommend that roller bearings be subjected to a maximum operating load of half the load carrying capacity. The International Organization for Standardization (ISO) and the American Bearing Manufacturers Association (ABMA) define calculation methods, usually considering raceways. Internal dimensions and rolling elements. “Rated Life” is the bearing durability calculated at 90% reliability. It is defined as the amount of time a set of identical rollers completes before fatigue spalling occurs. The basic calculation formula to determine the rated life of the bearing (L10) is as follows:
Selection of rolling bearings
Bearing selection is the process of matching specific bearings to application requirements, including load, misalignment, speed and torque. Rolling element bearings support loads through the contact that exists between rolling elements and raceways. During rotation, one raceway moves relative to the other. Rolling bearings come in many different forms, each with a unique set of functions. The suitability of a rolling bearing for a specific application depends on the match between these characteristics and the application requirements. In this case, certain factors must be considered when choosing the most suitable bearing type. According to the SKF (leading rolling bearing manufacturer) catalog, the following are the key factors for optimal bearing selection:
Available space
Loading conditions (size and orientation)
dislocation
speed
Operating temperature
Accuracy requirements
rigidity
Vibration level
pollution level
Lubrication conditions
In addition to these factors, it is important to consider not only the bearing itself, but also the entire assembly, such as the shaft and housing. Therefore, in order to choose the best bearing, the following factors must also be considered:
Proper design of other components
Proper clearance and preload
Proper sealing
Type and quantity of lubricant
Proper installation and removal methods
Although roller bearings are standardized components, selection criteria for the correct bearing can only be established to a limited extent, usually based on application requirements. Still, buyers must consider one of the main dimensions of the bearing, usually the bore diameter, in light of the overall design and construction. Today, computerization of the design process allows manufacturers to create bearings with optimal dimensions. The technology can also help consumers pick the right parts for use in various machines. When looking for the right bearing for a specific application, project managers and designers should focus on the following factors:
Load type and capacity
Installation requirements – installation space and lubrication methods
Bearing functional life
Bearing operating parameters (speed and thermal conditions)
Accuracy requirements
Maintenance and care
Environmental conditions (vibration, dirt, etc.)
Assembly and disassembly requirements
Applications of rolling bearings
Because different types of roller bearings offer different combinations of properties, such as performance, speed, reliability, load capacity, durability, and precision, they are used in a wide variety of equipment and in several different industries. Examples of widely used rolling bearings include:
air cargo system
Heavy rotating equipment and machinery
Automobile industry
medical equipment
Hydroelectric power plant turbine generates electricity
Solar panels
agricultural industry
Pulp and paper
refining
Rolling bearings have properties that make them suitable for certain applications. For example, cylindrical roller bearings are popular in rolling mills, machine tool spindles, and medium- and heavy-duty electric motors. High radial load carrying capacity, precision, high support stiffness, high speed capabilities etc. make it suitable for such applications. Ball bearings are used in electric vehicle motors where the load is usually a combination load or radial load and is relatively low, while the speed range is wide and reaches a fairly high level. These bearings are also used in light-duty gearboxes, conveyor rollers and small vehicles. Important aspects of selection include light load, dual load capacity and low cost.
When looking for bearings to support combined axial and radial loads as well as high loads, tapered roller bearings are the better choice. Therefore, they are used in wheels for off-road vehicles, passenger cars, gearboxes for marine drives, landing gear for aircraft, printing presses, other transmission systems and machine tool spindles. Special factors such as heavy load capacity and adjustability for accuracy and stiffness should be considered during the selection process. Spherical roller bearings are used in windmills, rolling mills, paper mills, large industrial gearboxes, etc. They have efficient misalignment capabilities and heavy radial load carrying capacity. Finally, needle roller bearings are used in automotive transmissions due to their compactness and economy.
Roller bearings are subject to standards indicating their accuracy and efficiency. Bearing quality is rated by RBEC (Roller Bearing Engineering Council). These grades classify different accuracy and tolerance ranges of roller bearings. The higher the RBEC number, the tighter the bearing tolerances. Ultra-high-speed applications will benefit most from precise bearings. Manufacturers do not have to follow these industry guidelines. North American roller bearings adhere to RBEC grades, while other ball bearings adhere to ISO or its regional equivalent (DIN, KS, etc.). There are five acceptable levels of RBEC rating, and the levels are independent of bearing size. For ball bearings, these tolerance classes are ABEC 1, ABEC 3, ABEC 5, ABEC 7 and ABEC 9. Similarly, the accuracy classes of roller bearings (cylindrical and spherical) are RBEC 1, RBEC 3, RBEC 5, RBEC 7, and RBEC 9. The values of ABEC and RBEC classes are the same: for both, the higher the class number, the better the bearing The smaller the tolerance – and therefore the better the bearing’s accuracy, efficiency and speed capabilities.
Roller Bearings VS Ball Bearings
The main difference between roller bearings and ball bearings is the type of rolling elements used. Roller bearings use cylindrical rollers, while ball bearings use balls. Therefore, roller bearings can handle heavier loads and are suitable for applications with heavy radial or thrust loads. Roller bearings have a larger contact area than ball bearings and are suitable for heavy-duty applications. The load is assumed to be evenly distributed over multiple axes. In this case, roller bearings are usually less expensive to manufacture and maintain over their lifetime because there is less friction between the rings.
Additionally, roller bearings typically have higher load carrying capacities and lower speed ratings than ball bearings. Ball bearings, on the other hand, are better suited for high speeds and low to moderate load applications. One of the most significant differences between roller bearings and ball bearings is that roller bearings are generally expensive than ball bearings. However, they offer several advantages, including higher load-bearing capacity and greater accuracy.
Bearing size is an important aspect of roller bearings, and there are several factors that determine roller bearing size. These factors include the diameter of the mounting shaft, the bore diameter of the bearing, the outer diameter and the width of the bearing. Bore diameter is the inside diameter of a roller bearing, usually measured in millimeters (mm). The width of a bearing is the distance between the outer rings of the bearing, also measured in millimeters. In order to determine the correct size of a roller bearing with a shaft as the rotating element and a transition fit in the outer ring, it is necessary to know the diameter of the shaft on which it will be installed. The diameter of the shaft must be larger than the bore diameter of the bearing because the bearing must fit snugly on the shaft. A tight fit is required to prevent the bearing from rotating on the shaft, which can cause damage to the bearing and shorten its service life. On the other hand, if the outer ring rotates, the diameter of the housing must be smaller than the outer ring, and the shaft will have a transition fit.
When selecting the appropriate size, in addition to the bore diameter and width, the load capacity of the bearing must also be considered. The load capacity of a roller bearing is determined by the bearing type, size and material. For example, larger bearings can generally handle higher loads than smaller bearings. It is also important to consider operating conditions such as speed and temperature, as these conditions can affect the size and load capacity of the bearing. For example, in high-speed applications, bearings with low coefficients of friction and high load capacities may be required. To ensure proper operation and service life of roller bearings, it is critical to select the appropriate size based on specific application requirements. It is also important to choose the correct lubrication for the specific situation.
Roller bearing manufacturing process
1. The manufacturing process of cylindrical roller bearings: blank forming → deburring or ring belt → soft grinding of raceway surface → soft grinding of double end faces → heat treatment → rough grinding of front rolling surface → rough grinding of double end faces → rough grinding of rear rolling surface → final grinding Double-end face → fine and final grinding rolling surface → super-finishing rolling surface → cleaning and drying → final inspection of appearance and size grouping → oiled packaging.
2. The manufacturing process of tapered roller bearings: blank forming → deburring or ring belt → soft grinding of raceway surface → soft grinding of double end surfaces → heat treatment → rough grinding of rolling surface → fine grinding of rolling surface → ball base surface grinding → final grinding of rolling surface →Super finishing rolling surface→Cleaning and drying→Final inspection of appearance and size grouping→Oil coating and packaging. The above two kinds of rollers can be made into convex busbar rolling surfaces. If the convexity is less than 0.005mm, it can generally be carried out directly in the super-finishing rolling surface process; if the convexity is greater than 0.005mm, it can generally be rolled in the last final grinding process. The convexity is ground out in the surface process and then super-finished.
3. The manufacturing process of needle roller bearings: blank forming → deburring → heat treatment → coarse, fine and final grinding of the rolling surface → super-finishing of the rolling surface or sawdust polishing. For flat-head and tapered-head needle rollers, if it is difficult to ensure length and dimensional tolerances during blank molding, the double-end grinding process can be added to the grinding and rolling process. If a convex busbar rolling surface is required, it can be directly processed in the super-finishing rolling surface or channeling process.
4. The manufacturing process of spherical roller bearings: blank forming → deburring or ring belt → soft grinding of raceway surface → soft grinding of double end faces → heat treatment → grinding of non-spherical end faces → grinding of ball end faces → coarse, fine and final grinding of rolling surfaces → Polishing → cleaning, drying → final appearance inspection, size grouping → oiling and packaging. The process of symmetrical spherical rollers is: blank forming → deburring or ring belt → soft grinding of raceway surface → soft grinding of double end faces → heat treatment → rough grinding of rolling surface → rough and final grinding of double end faces → fine and final grinding of rolling surfaces → polishing →Cleaning and drying→Final inspection of appearance and size grouping→Oil packaging. If the final grinding rolling surface process can meet the surface roughness requirements, polishing does not need to be performed.
Bearing suffix code
The suffix code of the bearing is placed behind the basic code. When there are multiple sets of suffix codes, they should be arranged from left to right in the order of the suffix codes listed in the bearing code table. Some postcodes are separated from the basic codename by a small dot.
Suffix code - internal structure
(1), A, B, C, D, E—— Internal structure changes.
Example: Cylindrical roller, spherical roller and thrust spherical roller bearings N309E, 21309 E, 29412E – enhanced design, improved bearing load capacity.
(2), VH – full-roller cylindrical roller bearing with self-locking rollers (the compound circle diameter of the rollers is different from that of standard bearings of the same model).
Example: NJ2312VH.
Post code - bearing dimensions and external structure
(1), DA – separable double row angular contact ball bearing with double half inner ring. Example: 3306DA.
(2), DZ——Roller bearing with cylindrical outer diameter. Example: ST017DZ.
(3), K—— tapered bore bearing, taper 1:12. Example: 2308K.
(4), K30- tapered bore bearing, taper 1:30. Example: 24040 K30.
(5), 2LS – double row cylindrical roller bearing with double inner ring and dust cover on both sides. Example: NNF5026VC.2LS.V—— Internal structure change, double inner ring, dust cover on both sides, full roller double row cylindrical roller bearing.
(6), N—— Bearings with stop grooves on the outer ring. Example: 6207N.
(7), NR—— Bearings with stop grooves and stop rings on the outer ring. Example: 6207 NR.
(8), N2-—— four-point contact ball bearing with two stop grooves on the outer ring. Example: QJ315N2.
(9), S—— Bearing with lubricating oil groove and three lubricating oil holes in the outer ring. Example: 23040S. Spherical roller bearings with bearing outer diameter D ≥ 320mm are not marked with S.
(10), X—— Overall dimensions comply with international standards. Example: 32036X
(11), Z.——Technical conditions for special structures. Starting from Z11 and working downwards. Example: Z15——Stainless steel bearing (W-N01.3541).
(12), ZZ——The roller bearing has two retaining rings that guide the outer ring.
Post code - sealing and shielding
(1), RSR—— The bearing has a sealing ring on one side. Example: 6207 RSR
(2), 2RSR—— The bearing has sealing rings on both sides. Example: 6207.2RSR.
(3), ZR—— The bearing has a dust cover on one side. Example: 6207 ZR
(4), 2ZR bearings are equipped with dust covers on both sides. Example: 6207.2ZR
(5), ZRN—— The bearing has a dust cover on one side and a stop groove on the outer ring on the other side. Example: 6207 ZRN.
6), 2ZRN—— The bearing has dust covers on both sides and a stop groove on the outer ring. Example: 6207.2ZRN.
Post code - cage and its materials-solid cage.
A or B is placed after the cage code. A means that the cage is guided by the outer ring, and B means that the cage is guided by the inner ring.
1), F—— Steel solid cage, rolling element guide.
2), FA – steel solid cage, outer ring guide.
3), FAS – steel solid cage, outer ring guide, with lubrication groove.
4), FB—— Steel solid cage, inner ring guide.
5), FBS – steel solid cage, inner ring guide, with lubrication groove.
6), FH—— Steel solid cage, carburized and quenched.
7), H, H1——carburizing and quenching cage.
8), FP——steel solid window cage.
9), FPA – steel solid window cage, outer ring guide.
10), FPB – steel solid window cage, inner ring guide.
11), FV, FV1——Steel solid window cage, aged, quenched and tempered.
12), L—— Light metal solid cage, rolling element guide.
13), LA – light metal solid cage, outer ring guide.
14), LAS – light metal solid cage, outer ring guide, with lubrication groove.
15), LB——Light metal solid cage, inner ring guide.
16), LBS——Light metal solid cage, inner ring guide, with lubrication groove.
17), LP – light metal solid window cage.
18), LPA – light metal solid window cage, outer ring guide.
19), LPB – light metal solid window cage, inner ring guide (thrust roller bearing is shaft guide).
20), M, M1——brass solid cage.
21), MA – brass solid cage, outer ring guide.
22), MAS——brass solid cage, outer ring guide, with lubrication groove.
23), MB——brass solid cage, inner ring guide (thrust spherical roller bearing is shaft ring guide).
24), MBS——brass solid cage, inner ring guide, with lubrication groove.
25), MP—— Brass solid straight pocket cage.
26), MPA – brass solid straight pocket and cage, outer ring guide.
27), MPB – brass solid straight pocket cage, inner ring guide.
28), T—— Phenolic laminated pipe solid cage, rolling element guide.
28), TA – phenolic laminated pipe solid cage, outer ring guide.
30), TB – phenolic laminated pipe solid cage, inner ring guide.
31), THB – phenolic laminated cloth tube pocket type cage, inner ring guide.
32), TP—— Phenolic layer cloth tube straight pocket cage.
33), TPA – phenolic laminated cloth tube with straight pocket cage and outer ring guide.
34), TPB – phenolic laminated cloth pipe with straight pocket cage and inner ring guide.
35), TN – engineering plastic molded cage, rolling element guide, with additional numbers indicating different materials.
36), TNH—— Engineering plastic self-locking pocket cage.
37), TV – glass fiber reinforced polyamide solid cage, steel ball guided.
38), TVH – glass fiber reinforced polyamide self-locking pocket-type solid cage, guided by steel balls.
39), TVP – glass fiber reinforced polyamide window type solid cage, steel ball guided.
40), TVP2 – glass fiber reinforced polyamide solid cage, roller guide.
41), TVPB – glass fiber reinforced polyamide solid cage, inner ring guide (thrust roller bearing is shaft guide).
42), TVPB1 – glass fiber reinforced polyamide solid window cage, shaft guide (thrust roller bearing).
Post code - cage and its material - stamped cage
1), J—— Steel plate stamping cage.
2), JN—— deep groove ball bearing riveted cage.
The number added after the cage code, or inserted in the middle of the cage code, indicates that the cage structure has been changed. These numbers are only for transitional periods, for example: NU 1008M 1.
Post code - bearing without cage
(1), V – full complement rolling element bearing. Example: NU 207V.
(2), VT – full complement rolling element bearing with isolation ball or roller. Example: 51120VT.
Post code - tolerance level
(1), P0 – the tolerance level complies with the level 0 specified by the international standard ISO, and is omitted in the code and does not indicate it.
(2), P6 – the tolerance level complies with level 6 specified by the international standard ISO.
(3), P6X – Grade 6 tapered roller bearings whose tolerance level complies with the international standard ISO.
(4), P5 – the tolerance level complies with level 5 specified by the international standard ISO.
(5), P4 – the tolerance level complies with level 4 specified by the international standard ISO.
(6), P2 – the tolerance level complies with level 2 specified by the international standard ISO (excluding tapered roller bearings).
(7), SP – dimensional accuracy is equivalent to level 5, and rotation accuracy is equivalent to level 4 (double row cylindrical roller bearings).
(8), UP——The dimensional accuracy is equivalent to level 4, and the rotation accuracy is higher than level 4 (double row cylindrical roller bearing).
(9), HG——The dimensional accuracy is equivalent to level 4, and the rotation accuracy is higher than level 4 and lower than level 2 (spindle bearing).
Post code - clearance
(1), C1——The clearance complies with group 1 specified in the standard and is less than group 2.
(2), C2——The clearance complies with Group 2 specified in the standard and is less than Group 0.
(3), C0 – the clearance complies with group 0 specified in the standard, and is omitted in the code and not represented.
(4), C3——The clearance complies with the 3 groups specified in the standard and is greater than the 0 group.
(5), C4——The clearance complies with the 4 groups specified in the standard and is greater than the 3 groups.
(6), C5——The clearance complies with the 5 groups specified in the standard and is greater than the 4 groups.
Example: 6210.R10.20——6210 bearing, radial clearance 10 μm to 20 μm.
6212.A120.160——6212 bearing, axial clearance 120 μ m to 160 μ m.
Post code - bearings tested for noise
(1), F3 – low noise bearing. Mainly refers to cylindrical roller bearings and deep groove ball bearings with an inner diameter d > 60mm. Example: 6213.F3.
(2), G—— low noise bearing. Mainly refers to deep groove ball bearings with inner diameter d ≤ 60mm. Example: 6207.
Post code - heat treatment
(1), S0——The bearing ring has been tempered at high temperature, and the working temperature can reach 150 ℃.
(2), S1——The bearing ring has been tempered at high temperature, and the working temperature can reach 200 ℃.
(3), S2—— The bearing ring has been tempered at high temperature, and the working temperature can reach 250 ℃.
(4), S3——The bearing ring has been treated with high temperature tempering, and the working temperature can reach 300 ℃.
(5), S4——The bearing ring has been tempered at high temperature, and the working temperature can reach 350 ℃.
Conclusion
Thousands of different types of roller bearings are available to meet specific application requirements. Aubearing offers a wide selection of roller bearings. As an industry leader in the distribution of quality ball and roller bearings, Aubearing is proud to be a trusted partner to leading brands including SKF, FAG, INA, IKO, NACHI, NSK, NTN. Our experts are on hand to guide customers in selecting the best bearing type for their unique needs, and we’ll work closely with your team to ensure you choose the best option. To learn , contact us today.