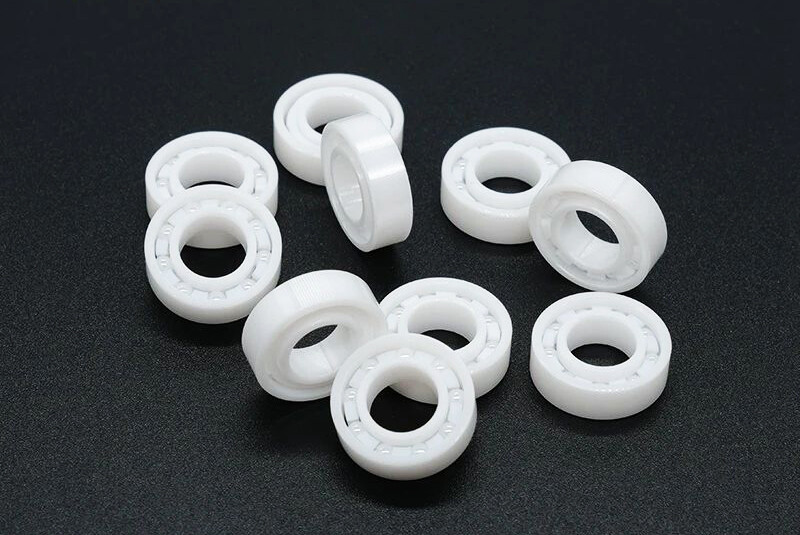
Bearing Manufacturer & Supplier
Specialize in ball bearings, roller bearings, thrust bearings, thin section bearings etc.
The Ultimate Guide to Ceramic Bearings
Ceramic bearings are developed for heavy loads, low temperatures, and no lubrication in harsh industrial environments. They are a perfect combination of new materials, new processes, and new structures. Ceramic bearings can completely cover all applications of current precision, medium-speed and above metal (bearing steel, stainless steel) bearings. The inner diameter, outer diameter and other dimensions of ceramic ball bearings can follow the standard dimensions of P4, P5 and P6 grades of steel bearings. Due to the low thermal expansion coefficient, small heat transfer performance, and small elasticity of ceramic materials, attention must be paid to installation and coordination.
Table of Contents
ToggleCharacteristics of ceramic bearings
The service life of ceramic bearings is than three times that of traditional steel bearings, which can save a lot of downtime and maintenance time, reduce the scrap rate, and reduce the inventory of bearing spare parts. Compared with the performance of bearing steel, the density of ceramic bearings is 30%-40% of bearing steel, which can reduce the increase in moving body load and slippage caused by centrifugal force. Due to its high wear resistance, the rotation speed of ceramic bearings is 1.3-1.5 times that of bearing steel, which can reduce groove surface damage caused by high-speed rotation. The elastic modulus is 1.5 times higher than bearing steel. The force elasticity is small, which can reduce the deformation caused by high load. The hardness is 1 times that of bearing steel, which can reduce wear. The compression resistance is 5-7 times that of bearing steel. The thermal expansion coefficient is 20% less than bearing steel. The friction coefficient is 30% less than that of bearing steel, which can reduce the heat generated by friction and reduce premature peeling failure of bearings caused by high temperature. The tensile strength and bending resistance are the same as those of metal.

Ceramic bearing classification
High speed bearings
It has the advantages of cold resistance, low stress elasticity, high pressure resistance, poor thermal conductivity, light weight, and small friction coefficient. It can be used in high-speed spindles of 12,000 rpm-75,000 rpm and other high-precision equipment;
High temperature resistant bearings
The ceramic material itself has a high temperature resistance of 1200°C and is self-lubricating. It will not expand due to temperature differences when used at temperatures between 100°C and 800°C. Can be used in furnaces, plastic making, steel making and other high temperature equipment;

Corrosion-resistant bearings
Ceramic materials themselves are corrosion-resistant and can be used in fields such as strong acids, strong alkali, inorganic, organic salts, seawater, etc., such as: electroplating equipment, electronic equipment, chemical machinery, shipbuilding, medical equipment, etc.
Antimagnetic bearings
Because it is non-magnetic and does not absorb dust, it can reduce premature peeling of bearings and loud noise. It can be used in demagnetization equipment, precision instruments and other fields.
Electrically insulated bearings
Because the resistance is very high, arc damage to the bearings can be avoided. Ceramic bearings can be used in various power equipment that require insulation.
Vacuum bearings
Due to the unique oil-free self-lubricating properties of ceramic materials, it can overcome the problem of ordinary bearings being unable to achieve lubrication in ultra-high vacuum environments.
Note: For the above five types of bearings, the same set of bearings can be applied to high temperature, high speed, acid and alkali, magnetic field, and non-insulation. However, due to different material properties, customers are asked to choose products based on their application scenarios. Choose the most suitable ceramic bearing.
Classification by material
All-ceramic bearings have the characteristics of anti-magnetic and electrical insulation, wear resistance and corrosion resistance, oil-free self-lubrication, high temperature resistance and high cold resistance, and can be used in extremely harsh environments and special working conditions. The ferrules and rolling elements are made of zirconium oxide (ZrO2) ceramic material, and the cage uses polytetrafluoroethylene (PTFE) as standard configuration. Generally, glass fiber reinforced nylon 66 (RPA66-25), special engineering plastics (PEEK, PI), stainless steel (AISISUS316), brass (Cu), etc.

Silicon nitride full ceramic bearings
Silicon nitride full ceramic bearing rings and rolling elements are made of silicon nitride (Si3N4) ceramic material, and the cage is made of polytetrafluoroethylene (PTFE) as standard configuration. Generally, RPA66-25, PEEK, PI, and phenolic clips can also be used. Cloth glue wood pipe, etc. Compared with ZrO2 materials, full ceramic bearings made of SiN4 are suitable for higher speeds and load capacities, as well as higher ambient temperatures. At the same time, we can provide precision ceramic bearings for high-speed, high-precision and high-rigidity spindles, with the highest manufacturing accuracy reaching P4 to UP levels.

Full complement ceramic bearings
Full complement ball type all-ceramic bearings have a gap for adding balls on one side. Due to the cageless structure design, ceramic balls can be installed than standard structure bearings, thereby increasing their load capacity. In addition, they can also avoid limitations due to cage materials. , which can achieve corrosion resistance and temperature resistance of ceramic cage type all-ceramic bearings. This series of bearings are not suitable for higher speeds. When installing, attention should be paid to installing the notch surface on the end that does not bear axial load.

Ceramic cage bearings
Ceramic cages have the advantages of wear resistance, high strength, corrosion resistance and self-lubrication. All-ceramic bearings made of ceramic cages can be used in harsh environments such as extreme corrosion, ultra-high and low temperatures, and high vacuum. Commonly used ceramic materials are ZrO2, Si3N4 or SiC.

Hybrid Ceramic Ball Bearings
Ceramic balls, especially silicon nitride balls, have the characteristics of low density, high hardness, low friction coefficient, wear resistance, self-lubrication and good rigidity. They are especially suitable for rolling elements (inner and outer rings) of high-speed, high-precision and long-life hybrid ceramic ball bearings. for metal). Generally, the inner and outer rings are made of bearing steel (GCr15) or stainless steel (AISI440C), and the ceramic balls can be made of ZrO2, Si3N4, or SiC materials.

Classified by category
Deep groove ball ceramic bearings
Deep groove ball ceramic bearings are the most representative rolling bearings. They are widely used and can withstand radial loads and bidirectional axial loads. It is suitable for high-speed rotation and applications requiring low noise and low vibration, or in areas such as high temperature, high cold, corrosion, magnetic field, and non-insulation where steel bearings cannot be used.

Aligning ball ceramic bearings
The outer ring raceway of the self-aligning ball ceramic bearing is spherical and self-aligning, which can compensate for errors caused by non-concentricity and shaft deflection. It is used to produce misalignment between the shaft and the shell or the deflection of the shaft, as well as the alignment parts that require high temperature, low cold, corrosion, non-insulation of the magnetic field, etc. Note: The inclination cannot exceed 3 degrees.

Single row angular contact ball ceramic bearings
Single row angular contact ball ceramic bearings are suitable for high-speed and high-precision rotation. They do not affect their accuracy in high temperatures, magnetic fields, water, etc., and can withstand synthetic loads. The standard contact angles are 15°, 30° and 40°. The larger the contact angle, the greater the axial load capacity. The smaller the contact angle, the bearing can withstand radial load and unidirectional axial load. Generally installed in pairs. Please pay attention when purchasing.

Ceramic thrust ball bearings
Ceramic thrust ball bearings are composed of a washer-shaped ferrule with a ball rolling raceway and a cage assembled with balls. Can bear axial load, but cannot bear radial load.

Ceramic bearing manufacturing process
The ceramic bearing manufacturing process includes raw material preparation, molding, sintering, finishing and other links. The following is a detailed introduction to the manufacturing process of ceramic bearings.
Ceramic raw material preparation
The materials of ceramic bearings are mainly alumina and silicon nitride. The powders of these two materials need to be strictly screened and measured to ensure that their particle size and proportion meet the requirements. At the same time, the raw materials need to be dried and ball-milled so that they can be better formed during molding. flow and filling.
Mixed ceramic powder
Ceramic powders are mixed with other additives to improve the performance and processability of ceramic materials. And through grinding, mixing and other processes to ensure uniform particle size and stable composition.
Sintering
The formed ceramic body is sintered in a high-temperature environment to combine the particles and form a dense structure, improving strength and hardness.

Precision machining
The sintered ceramic material has high surface hardness and good wear resistance, but is prone to cracking. Therefore, precision machining is required, including turning, grinding, etc. This process requires multiple inspections and polishing and other subsequent treatments to ensure the bearing’s appearance smoothness and internal quality.
Assemble
Precision machined ceramic bearings are ready for assembly. This process is to assemble the inner ring, outer ring, balls and other parts together. Professional equipment is required during assembly and the quality is thoroughly checked to ensure that all indicators of the product meet standards.
Quality Control
Ceramic materials have the characteristics of high strength, high temperature, high wear resistance, and high chemical stability, but they also have a certain degree of brittleness. Strict quality control is required during the manufacturing process to ensure that the quality and performance of the product are up to standard. Commonly used quality inspection methods include X-ray inspection, metallographic microscope inspection, etc.

Ceramic bearings are high-tech products that require strict manufacturing processes and quality control. Through the manufacturing process introduced above, I believe that readers have a certain understanding of the production of ceramic bearings. In the future, ceramic materials will be widely used and bring greater development to industrial production.
Load capacity of ceramic bearings
The load capacity of ceramic bearings has certain limitations. Therefore, the maximum load qualification test of ceramic balls needs to be carried out. The deep groove ball bearing 6307E is used to install ceramic balls in the B30/60 test machine to conduct large load qualification tests.
According to experimental data, the load-bearing capacity of ceramic bearings is approximately 2-3 times that of steel bearings of the same size. However, in actual applications, bearings of different materials need to be selected according to specific conditions to achieve the best use effect. For example, ceramic bearings are used in high-speed machine tools. The elasticity of ceramics is 1.5 times higher than that of steel bearings, and the stress elasticity is relatively small. This can reduce deformation caused by excessive load, so it is very beneficial to increase the working speed, and can Achieve relatively high accuracy.

Although ceramic materials have high hardness and strength, due to their brittleness, they are prone to breakage when subjected to large instantaneous impact forces and heavy loads. When the operating temperature increases, the load-bearing capacity of ceramic bearings decreases accordingly. Due to the brittleness of ceramics, all-ceramic bearings cannot withstand large impact loads. The outer ring or inner ring may crack or even break suddenly under a certain impact load. over, ceramic bearings have poor thermal conductivity and are prone to cracks due to excessive temperature under overload and high temperature. Therefore, the bearing capacity of ceramic bearings has its limitations in the application range and cannot bear too much weight.
Regarding the load-bearing capacity limitations of ceramic bearings, product manufacturers usually clearly indicate their load-bearing capacity range in the product description. Therefore, the selection of appropriate ceramic bearings should be comprehensively considered based on various factors such as the use environment, working conditions, and load-bearing requirements. When purchasing ceramic bearings, you must carefully check the product’s technical parameters, especially the load-bearing capacity parameters, on the product specifications. During use, you must strictly follow the usage and maintenance methods provided in the instruction manual. If an abnormality occurs, the machine should be shut down for maintenance in time to avoid other problems.
Ceramic bearings have a high load-bearing capacity and can withstand larger loads. The load-bearing capacity of ceramic bearings is stronger than bearings made of other materials, but it also has certain limitations. In actual use, it is still necessary to select bearings of different materials according to actual conditions. Pay attention to the impact of use conditions on the bearing capacity to ensure its service life and working effect.
Are ceramic bearings fragile?
Ceramic bearings are not easily broken, no matter what angle they slip from? Basically, it will not cause damage to the appearance of the bearing, but when the full ceramic bearing is matched with the steel shaft, it is likely to cause fragmentation due to the different expansion coefficient of the material; through a simple comparison of crushing load experiments, the minimum crushing of ceramic balls The load is about 1/2-1/3 of the steel ball. This is because the contact surface caused by the plastic deformation of the steel ball increases, resulting in a larger crushing load. According to the crushing load value of the ceramic ball, it can be calculated that the maximum contact stress when it breaks is about 6-7 times that specified in the ISO-TC4 standard. This not only proves that the ceramic ball is safe for rolling bearings, but also shows that it is It can bear greater static load than steel bearings.
Hybrid ceramic bearings VS full ceramic bearings
Hybrid ceramic bearings refer to bearings that use semi-ceramic materials to make inner and outer rings or rolling elements. All-ceramic bearings refer to bearings whose inner and outer rings and rolling elements are made of ceramic materials. The main advantages are low friction coefficient, high rigidity, and good corrosion resistance. The manufacturing process of hybrid ceramic bearings is simpler than that of all-ceramic bearings, and the cost is relatively lower. So, what is the difference between hybrid ceramic bearings and full ceramic bearings?
Different materials
In hybrid ceramic bearings, only the inner and outer rings or rolling elements are made of ceramic materials, and the rest are made of metal materials. The inner and outer rings and rolling elements of all-ceramic bearings are made of ceramic materials, which are resistant to high temperatures and corrosion.

Different performance
Hybrid ceramic bearings have higher strength and reliability than all-ceramic bearings, but the hardness of ceramic balls is higher than that of steel bearings, which will cause certain wear and tear on other parts during operation. Full ceramic bearings have better wear resistance, corrosion resistance, high temperature performance and corrosion resistance, and can maintain good stable performance in harsh working environments.
Applicable to different environments
The applicable environmental range of hybrid ceramic bearings is relatively narrow and is usually only suitable for general industrial environments. Full ceramic bearings have the characteristics of good corrosion resistance and high temperature resistance, so they are suitable for use in harsh environments such as high temperature and corrosion. Although hybrid ceramic bearings and all-ceramic bearings are both made of ceramic materials, they have differences in materials, applicable environments, and functions. According to actual needs, selecting suitable bearings can better utilize its characteristics and improve the use effect of mechanical equipment.
White ceramic bearings VS black ceramic bearings
Although white ceramic bearings and black ceramic bearings are both ceramic bearings, they themselves are different.
Material properties
White ceramics are mainly made of alumina, which is a new material with high hardness, high strength, high wear resistance and good corrosion resistance. Due to its high hardness, white ceramics can significantly improve the wear resistance of the bearing. It can also reduce the heat generated when the bearing is in contact with the friction material, thereby increasing the service life of the bearing. Black ceramics are mainly composed of zirconium oxide + yttrium oxide. Compared with white ceramics, they have slightly lower hardness, but have better toughness and wear resistance, and have a longer service life.
Appearance
Black ceramic bearings are usually black, while white ceramic bearings are white or off-white.
Price
Due to the high material cost and difficulty in processing of black ceramic bearings, they are generally expensive, while white ceramic bearings are relatively cheaper.

Hardness
White ceramic bearings have a lower hardness, generally at 85-90 HRA, while black ceramic bearings have a higher hardness, usually reaching 94-98 HRA.
Application
White ceramic bearings are widely used in machinery, building materials, chemical industry, food, medical and other fields, while black ceramic bearings are mainly used in high-speed, high-temperature, high-risk environments, such as aviation, aerospace, optoelectronics and other fields.
White ceramic bearings and black ceramic bearings are both high-end bearing materials, each with its own advantages, disadvantages and applicable scenarios. When selecting bearings, it is necessary to reasonably select appropriate bearing materials based on the requirements of the actual use occasion.
Ceramic Bearings VS Stainless Steel Bearings
Bearings can provide support and reduce friction between two rotating parts. Bearings play an important role in industrial machinery and equipment and various transportation vehicles. At present, stainless steel bearings are one of the most widely used bearing types. However, with the continuous development of ceramic technology, ceramic bearings are increasingly used in various fields. So, what are the advantages of ceramic bearings and stainless steel shafts?
First, let’s review the advantages of ceramic bearings. Advantage one: high speed. Ceramic bearings have the advantages of cold resistance, low stress elasticity, high pressure resistance, poor thermal conductivity, light weight, and small friction coefficient. They can be used in high-speed spindles and other high-precision equipment between 12,000 rpm and 75,000 rpm; Advantage two: high temperature resistance. The ceramic bearing material itself has a high temperature resistance of 1200°C and is self-lubricating. It does not cause expansion due to temperature differences when the operating temperature is between 100°C and 800°C. It can be used in high-temperature equipment such as furnaces, plastic making, and steel making; advantage three: corrosion resistance. The zirconia ceramic and alumina ceramic materials used in ceramic bearings are inherently corrosion-resistant and can be used in fields such as strong acid, strong alkali, inorganic, organic salt, seawater, etc., such as: electroplating equipment, electronic equipment, chemical machinery, shipbuilding, Medical equipment, etc.
Let’s take a look at the advantages of stainless steel bearings. Advantage 1: Excellent corrosion resistance. Stainless steel bearings are not easy to rust and have strong corrosion resistance. Advantage two: washable. Stainless steel bearings can be washed down without having to be re-lubricated to prevent rust. Advantage 3: Can run in liquid. Due to the materials used, we can run bearings and housings in liquids. Therefore, stainless steel bearings are mainly used for medical equipment, cryogenic engineering, optical instruments, high-speed machine tools, high-speed motors, printing machinery, and food processing machinery.

Based on the above comparison of advantages, we can conclude that different machines need to be analyzed in detail and choose the bearing type that suits them to achieve the best results.
Applications of ceramic bearings
Ceramic bearings are a new type of bearing material, which have the characteristics of high temperature resistance, cold resistance, wear resistance, corrosion resistance, oil-free self-lubrication, high speed, etc., and are widely used in many fields. Ceramic bearings can be used in extremely harsh environments and special working conditions, and can be widely used in aviation, aerospace, navigation, petroleum, chemical industry, automobiles, electronic equipment, metallurgy, electric power, textiles, pumps, medical equipment, scientific research and national defense and military fields. , is a high-tech product for the application of new materials. The rings and rolling elements of ceramic bearings are made of all-ceramic materials, including zirconium oxide (ZrO2), silicon nitride (SisN4), and silicon carbide (Sic). The retainer is made of polytetrafluoroethylene, nylon 66, polyetherimide, zirconium oxide, silicon nitride, stainless steel or special aviation aluminum, thereby expanding the application surface of ceramic bearings. Application areas: medical equipment, cryogenic engineering, optical instruments, high-speed machine tools, high-speed motors, printing machinery, food processing machinery.
Aerospace
Lorem ipsum dolor sit amet, consectetur adipiscing elit. Ut elit tellus, luctus nec ullamcorper mattis, pulvinar dapibus leo.
Ceramic bearings are widely used in the aerospace field. The most important use is in high-speed rotating parts such as turbines, engines, servos, propellers and other spacecrafts such as aircraft, rockets and satellites. Research data shows that it will not be damaged after 50 launches. over, compared with traditional metal bearings, ceramic bearings have higher strength and better wear resistance, can withstand higher speeds and larger loads, and are corrosion-resistant. Due to its lightweight and high performance, it can improve aircraft fuel efficiency and reduce environmental impact. Therefore, ceramic bearings are increasingly used in the aerospace field.
Chemical industry
Most equipment in the chemical industry needs to withstand the erosion of corrosive gases or liquids, and traditional metal bearings are difficult to meet their requirements. However, ceramic bearings have excellent corrosion resistance and can operate stably in harsh environments such as strong acid, strong alkali, and salt water. Therefore, ceramic bearings are widely used in chemical equipment, such as pickling machines, chemical pumps and other equipment.
Machinery
Ceramic bearings are also widely used in the field of machinery manufacturing. Such as motors, water pumps, centrifuges, high-speed hydraulic pumps, machine tools, etc., ceramic bearings can effectively reduce noise, increase speed and life, not only maintain stability in high-speed and high-temperature environments, but also reduce equipment maintenance costs. In addition, in some special mechanical equipment, such as high-temperature furnaces, vacuum furnaces, high-purity condensation furnaces, etc., ceramic bearings have stronger corrosion resistance and better high-temperature resistance, which can ensure the normal operation of machinery and equipment.
Medical
Ceramic bearings are used in various medical equipment, such as operating room equipment, dialysis machines, etc. Ceramic bearings not only ensure the accuracy and reliability of the equipment, but also reduce the time and cost of maintenance and upkeep.
Electronic
In the electronic field, ceramic bearings are also widely used. For example, in electronic equipment such as high-speed fans, high-speed hard disk motors, and precision motors, ceramic bearings can reduce friction losses, increase rotation speed and life, making the equipment stable and reliable. Their stability and sealing make ceramic bearings widely used.
In short, the multiple uses of ceramic bearings have made them widely used in various industrial equipment, and their excellent performance and reliability have been recognized by the majority of users.